Precision Machining for Fluid Control Components in Harsh Environments
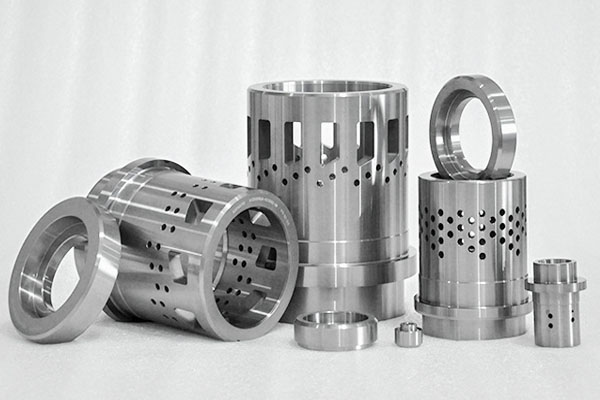
Design and manufacture high-performance fluid control parts engineered to operate in severe conditions. Whether handling erosive media, abrasive slurries, high temperatures, or corrosive fluids, these components are crafted for longevity, precision sealing, and dependable performance.
Primary Capabilities & Materials
Tungsten Carbide Component Production
Complete workflow from sintering to rough and finish machining of tungsten carbide parts. Custom components include valve seals, plunger sleeves, liners, spools, nozzles, and pistons—suitable for applications such as regulating valves, blackwater valves, slag isolation valves, slurry control systems, and high-pressure metering machinery SPPGY.
Industrial Ceramic & Gemstone Fabrication
Advanced processing of tough ceramic and gemstone materials (zirconia, alumina, silicon carbide, boron nitride, ruby, sapphire) for wear‑resistant, chemically stable components such as valve seats, stem guides, metering valves, and high‑purity flow control parts .
Multi-Axis CNC & Specialty Machining
State‑of‑the‑art CNC processes including turning, milling, grinding, EDM (spark and wire-cut), deep-hole drilling, and micro‑feature cutting—able to machine complex and ultra-hard parts from carbide, ceramics, and quartz glass as needed for fluid control applications .
Coating & Wear-Enhancement Treatments
Material coatings such as PVD titanium, ceramic coatings, and hardened-carbide overlays significantly increase durability and lifespan in abrasive environments. Assembly and component integration services are also available for pump and valve assemblies .
Fluid Control Applications & Component Scope
- Valve Seals & Precision Spools
Components for regulating valves, pressure-reducing valves, cleaning valves, one-way valves, and hydraulic metering valves—including carbide valve stems, sleeves, seats, and plunger assemblies. - Metering Pumps & Dosing Systems
Ceramic piston chambers, high-pressure ceramic or carbide valve cores, and hard-wearing plugs/nozzles for controlled fluid dosing in pharmaceutical, chemical, food & beverage, and laboratory equipment. - Slurry & Abrasive Flow Control
Durable tungsten carbide nozzles, guide sleeves, and liners designed to resist erosion in slurry pipelines, mining operations, or petroleum muddy water systems. - Sealing & Guiding for High-Load Media
Hard seal rings, sapphire or ceramic valve balls, ceramic seat inserts, and carbide cages used in throttling valves, slag isolation valves, and blackwater control valves.
Key Benefits & Engineering Value
- Exceptional Wear Resistance
Use of ultra-hard carbide and ceramics ensures excellent lifecycle performance in abrasive, erosive, and corrosive fluid environments. - Extreme Precision
Tight machining tolerances and mirror-finish grinding are suitable for critical sealing and flow control tasks. - Versatile Material Expertise
Support for tungsten carbide, technical ceramics, industrial gemstones, and quartz glass—matched to chemical resistance, mechanical strength, or purity needs. - Integrated Manufacturing
One-stop services from material shaping to assembly-ready valve blocks and instruments reduce handling, lead times, and quality risk.
SEO-Focused Keywords
Use these optimized terms in page content, headings, metadata, and image alt texts to elevate search visibility:
- Tungsten carbide fluid control parts
- Ceramic valve seats machining
- Sapphire metering valve components
- Precision tungsten carbide valve stems
- Industrial gemstone fluid parts
- Hard-material fluid control machining
- Wear-resistant metering pump components
- High-precision valve spool machining
- Ceramic flow-control valve manufacturing
- Carbide sealing ring and guide sleeve parts
Request a Tailored Quote for Fluid Control Parts
Whether you require ultra-wear-resistant valve spools, ceramic metering components, or sapphire-sealed guide parts, supply your drawings and specifications to receive a customized machining proposal. We’ll recommend optimal materials, manufacturing approaches, and finishing techniques to match your fluid control system’s performance and durability demands.