Experts Discuss Precision CNC Machining for Complex International Projects
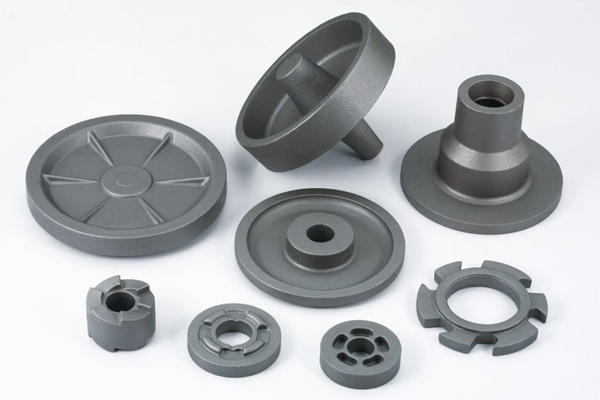
===INTRO:
In today's highly interconnected global economy, precision CNC machining has become an essential pillar supporting complex international projects across various industries. From aerospace to medical devices, the demand for customized, high-precision components continues to grow. Chinese CNC machining manufacturers have gained recognition for their ability to deliver tailored solutions that meet stringent quality standards for overseas clients. This article explores how experts emphasize the importance of customized precision CNC machining, tackle high-precision challenges, highlight key material applications, analyze notable case studies, and underline the critical role of experienced teams in achieving project success worldwide.
Experts Highlight the Importance of Custom Precision CNC Machining for Complex Projects
Precision CNC machining tailored to specific project requirements is vital for successful international collaborations. Experts agree that "customization" is not just about meeting dimensions but also involves understanding the nuanced demands of each application, including material properties, tolerance levels, and functional performance. High-precision machining enables manufacturers to produce components that fit seamlessly into complex assemblies, ensuring reliability and longevity.
In complex projects such as aerospace or medical implants, even minor deviations can lead to significant issues. Therefore, customized CNC solutions, often based on detailed drawings and client specifications, are essential. Chinese CNC manufacturers like those highlighted on SPPGY leverage their extensive experience to interpret design intent accurately, translating it into precise, high-quality components. This level of customization enhances overall project efficiency and reduces the need for costly rework or modifications downstream.
Furthermore, experts point out that advanced CNC technology combined with skilled craftsmanship allows for the production of intricate geometries that would be impossible with traditional methods. This capability is crucial for complex international projects requiring innovative designs and tight tolerances. The ability to deliver such specialized components makes Chinese CNC machining a preferred choice for overseas clients looking for reliable and high-precision manufacturing partners.
Another aspect emphasized by industry leaders is the importance of communication and collaboration in customizing solutions. Understanding the end-use conditions, environmental factors, and application specifics enables manufacturers to choose the appropriate materials and machining strategies. This collaborative approach ensures the final product meets or exceeds client expectations, fostering long-term partnerships across borders.
Customization also involves flexibility in handling different materials, sizes, and complexity levels. Chinese CNC manufacturers have invested in versatile equipment and rigorous quality control systems to accommodate such diversity. Their experience with complex, high-precision projects has cultivated a deep understanding of the trade-offs and best practices necessary to optimize manufacturing processes for each unique application.
In the context of international projects, cultural and language barriers can pose challenges. Experts highlight the importance of clear communication channels and technical expertise to bridge these gaps. Transparent project management and detailed documentation ensure that all specifications are met precisely, reinforcing the importance of experienced teams familiar with global standards and client expectations.
Overall, experts agree that the cornerstone of success in complex international projects lies in the ability to deliver highly customized, precision-engineered components. The combination of technological prowess, skilled personnel, and a customer-centric mindset positions Chinese CNC manufacturers as reliable partners capable of tackling the most demanding requirements.
Overcoming High-Precision Challenges in International CNC Manufacturing
High-precision CNC machining for international projects presents numerous technical challenges that require advanced solutions and expert knowledge. One of the primary difficulties is maintaining ultra-tight tolerances across complex geometries, which demands sophisticated machine tools and meticulous process control. Chinese CNC manufacturers have responded by investing in high-precision equipment and continuous staff training to ensure consistent quality.
Material variability is another challenge when working with diverse international clients. Different applications necessitate specific materials like aerospace-grade aluminum, medical-grade stainless steel, or exotic alloys, each with unique machining characteristics. Experts emphasize the importance of understanding these materials’ behaviors, including cutting forces, thermal expansion, and surface finish requirements, to optimize machining parameters accordingly.
Temperature control during machining is critical to prevent dimensional inaccuracies. In high-precision projects, even slight thermal fluctuations can lead to deviations. Advanced CNC centers equipped with thermal compensation systems help stabilize machining conditions, ensuring the components meet the strictest standards. Chinese manufacturers leverage such technology to deliver reliable results consistently.
Tool wear and vibration are additional issues that impact machining precision. Using high-quality, specially coated cutting tools and implementing advanced vibration damping techniques significantly extend tool life and improve surface quality. Experts note that managing these factors is crucial for producing complex parts with intricate features and tight tolerances.
The integration of CAD/CAM software with CNC systems has been transformative in overcoming challenges. These tools enable detailed simulation and optimization before actual machining, reducing errors and material waste. Chinese manufacturers utilize cutting-edge software to plan complex machining paths, ensuring precision and efficiency even for the most complicated parts.
Quality control is paramount in high-precision manufacturing. Experts highlight the importance of employing advanced measurement systems such as coordinate measuring machines (CMM), laser scanners, and optical comparators. Real-time feedback during machining allows for immediate adjustments, guaranteeing that each component adheres to exact specifications.
Handling large and heavy components introduces additional logistical and technical hurdles, especially in international projects where transportation and assembly are involved. Chinese CNC manufacturers have developed specialized fixtures and clamping solutions to ensure stability during machining, facilitating the production of large, complex parts without compromising accuracy.
Finally, cultural differences and communication gaps can hinder the resolution of technical issues. Experts stress the importance of experienced project managers and technical teams who understand international standards and can effectively liaise with overseas clients. Clear documentation and detailed process reports foster transparency and help resolve precision challenges swiftly.
In summary, overcoming high-precision challenges in international CNC manufacturing requires a combination of technological advancements, material expertise, and skilled personnel. Chinese CNC manufacturers’ comprehensive approach ensures the delivery of complex, precision-engineered components worldwide.
Key Material Applications in Advanced CNC Machining for Global Clients
Material selection plays a pivotal role in the success of high-precision CNC machining for international projects. Different applications demand materials with specific properties such as strength, corrosion resistance, or biocompatibility. Chinese manufacturers have extensive experience working with a variety of materials, tailoring their machining processes to meet precise requirements.
Aluminum alloys, particularly aerospace-grade 7075 and 6061, are among the most common materials due to their excellent strength-to-weight ratio and machinability. Chinese CNC factories excel in producing lightweight, durable components for aviation and automotive industries, applying optimized cutting strategies to achieve high surface quality and tight tolerances.
Stainless steel, including 304, 316, and medical-grade variants, is extensively used in medical devices, food processing equipment, and marine applications. Machining these materials requires careful parameter control to prevent work hardening and achieve smooth finishes. Experts highlight that Chinese manufacturers’ experience in handling stainless steel ensures components meet strict hygiene and durability standards.
Exotic alloys such as titanium, Inconel, and zirconium are critical in high-performance sectors like aerospace and nuclear energy. These materials are difficult to machine due to their hardness and low thermal conductivity. Advanced CNC machinery equipped with specialized tools and cooling systems enables Chinese manufacturers to produce complex parts from these challenging materials reliably.
Ceramics and composite materials are increasingly being incorporated into high-tech projects, including electronics and aerospace components. Precision CNC machining of such materials requires controlled environments and expert handling to prevent cracking or delamination. Chinese companies have developed expertise in these advanced applications, expanding their capabilities to meet diverse international demands.
Plastic materials like PEEK, PTFE, and UHMWPE are used in medical implants, electrical insulation, and lightweight structural components. CNC machining plastics demands different tooling and parameter settings compared to metals. Chinese manufacturers are adept at optimizing these processes to produce high-precision plastic parts with smooth finishes and complex geometries.
In addition to material properties, surface treatment and finishing processes such as anodizing, plating, and coating are vital for enhancing corrosion resistance and aesthetic appeal. Chinese CNC manufacturers often integrate these secondary processes into their workflows, providing comprehensive solutions that meet international standards.
Experts stress that understanding the mechanical and thermal behaviors of each material allows for precise control during machining, minimizing defects and ensuring the longevity of the components. This deep material knowledge is critical for fulfilling the rigorous demands of global clients in complex projects.
Finally, material sourcing and quality assurance are crucial components of successful international CNC projects. Chinese manufacturers establish trusted supply chains and enforce strict inspection protocols to guarantee that raw materials meet all specifications before machining begins. This approach ensures consistency and reliability across diverse applications and regions.
In essence, mastery over a wide range of materials empowers Chinese CNC machining providers to serve the needs of global industries with precision, versatility, and confidence.
Case Studies: Solving Tough CNC Machining Problems Worldwide
Real-world case studies exemplify the innovative solutions Chinese CNC manufacturers have provided to overcome complex machining challenges for international clients. One notable example involved aerospace components requiring extremely tight tolerances and complex geometries. The Chinese team utilized advanced multi-axis machining centers, combined with thermal compensation technology, to produce parts that met the exacting standards of global aerospace firms.
Another case involved medical implants from titanium alloys, which are notoriously difficult to machine due to their low thermal conductivity and high strength. The manufacturer implemented specialized coolant management and vibration damping techniques, allowing for precise, smooth finishes on intricate medical devices. This solution ensured compliance with international health and safety standards.
A challenging project involved large, high-precision mechanical parts for the energy sector. The parts were made from exotic alloys and exceeded 1 meter in length. To address the issues of stability and accuracy, the Chinese manufacturer developed bespoke fixtures and employed real-time measurement systems, enabling the production of parts with minimal deviations despite their size and material complexity.
In the automotive industry, a client required high-precision, lightweight components made from aluminum alloys with complex internal channels. The Chinese team adopted optimized tool paths and multi-step machining strategies, reducing cycle times and improving surface quality. The result was a successful delivery that met all performance and safety requirements.
For electronics and aerospace applications, a manufacturer faced the challenge of machining ceramics for high-frequency components. These materials are brittle and prone to cracking. The solution involved low-force machining, controlled environment conditions, and specialized tools, resulting in high-precision ceramic parts with excellent surface finishes.
A particularly notable case involved the production of custom mold components with micro-scale features for the semiconductor industry. Achieving such intricate details required ultra-fine cutting tools and precise process control, which Chinese manufacturers mastered through rigorous training and technological investment, ensuring the components’ functionality and durability.
These case studies demonstrate how Chinese CNC manufacturers leverage their technical expertise, advanced equipment, and innovative problem-solving approaches to tackle diverse and tough machining challenges worldwide. Their ability to adapt and optimize processes underpins their reputation as reliable partners for complex international projects.
Experts conclude that these real-world examples highlight the importance of experience, technological sophistication, and a proactive approach to problem-solving in achieving success in high-precision CNC manufacturing for global clients.
The Role of Experienced Machining Teams in Achieving Complex Project Success
At the heart of successful international CNC projects lies a team of highly skilled and experienced professionals. These experts possess not only technical knowledge but also a deep understanding of international standards, quality requirements, and client-specific expectations. Their role is pivotal in translating complex designs into precise, functional components.
Experienced machining teams excel in interpreting detailed drawings and specifications, ensuring that every aspect of the product meets the intended design. They are adept at identifying potential issues early in the process and devising effective solutions, which is crucial for high-precision projects with minimal margin for error.
Training and continuous education are integral to maintaining a top-tier team. Chinese CNC manufacturers invest heavily in personnel development, equipping their operators and engineers with up-to-date skills in the latest CNC technology, software, and quality control methods. This commitment ensures that the teams can handle complex tasks efficiently and accurately.
Effective communication within the team and with overseas clients is another critical factor. Multilingual staff and project managers who understand cultural nuances facilitate smoother exchanges of technical information, reducing misunderstandings and errors. This clarity is vital when working on high-stakes projects across different regions.
Quality assurance is driven by experienced personnel who oversee every step of the manufacturing process, from raw material inspection to final measurement. Their keen attention to detail and rigorous standards guarantee that each component adheres to strict international specifications, minimizing rework and delays.
Problem-solving skills are a hallmark of seasoned teams. When faced with unexpected machining difficulties or material issues, these professionals leverage their expertise to troubleshoot promptly, applying innovative techniques or adjusting processes to maintain project timelines and quality.
Collaboration and teamwork also contribute significantly to project success. Skilled teams coordinate seamlessly, sharing knowledge and supporting each other to optimize machining workflows. This synergy enhances productivity and ensures that complex components are produced efficiently.
Finally, the experience of the team fosters a culture of continuous improvement. Lessons learned from past projects are integrated into new processes, leading to incremental enhancements in precision, efficiency, and reliability. This proactive approach is essential for meeting the ever-increasing demands of international clients.
In conclusion, the role of experienced machining teams cannot be overstated. Their technical prowess, problem-solving capabilities, and commitment to quality are fundamental in delivering complex, high-precision components that meet the exacting standards of global industries.
As global industries continue to push the boundaries of innovation, the importance of precision CNC machining—especially when tailored to complex international projects—becomes increasingly evident. Chinese CNC manufacturers, with their rich experience, technological advancements, and skilled teams, are well-positioned to meet these demands. By emphasizing customization, overcoming high-precision challenges, applying diverse materials expertly, solving tough problems through real-world case studies, and relying on seasoned professionals, they are shaping the future of high-precision manufacturing on the world stage. Their commitment to excellence ensures that complex international projects are not only possible but also successful, fostering continued growth and collaboration across borders.