Expert CNC Machining Services for High-Precision Global Clients
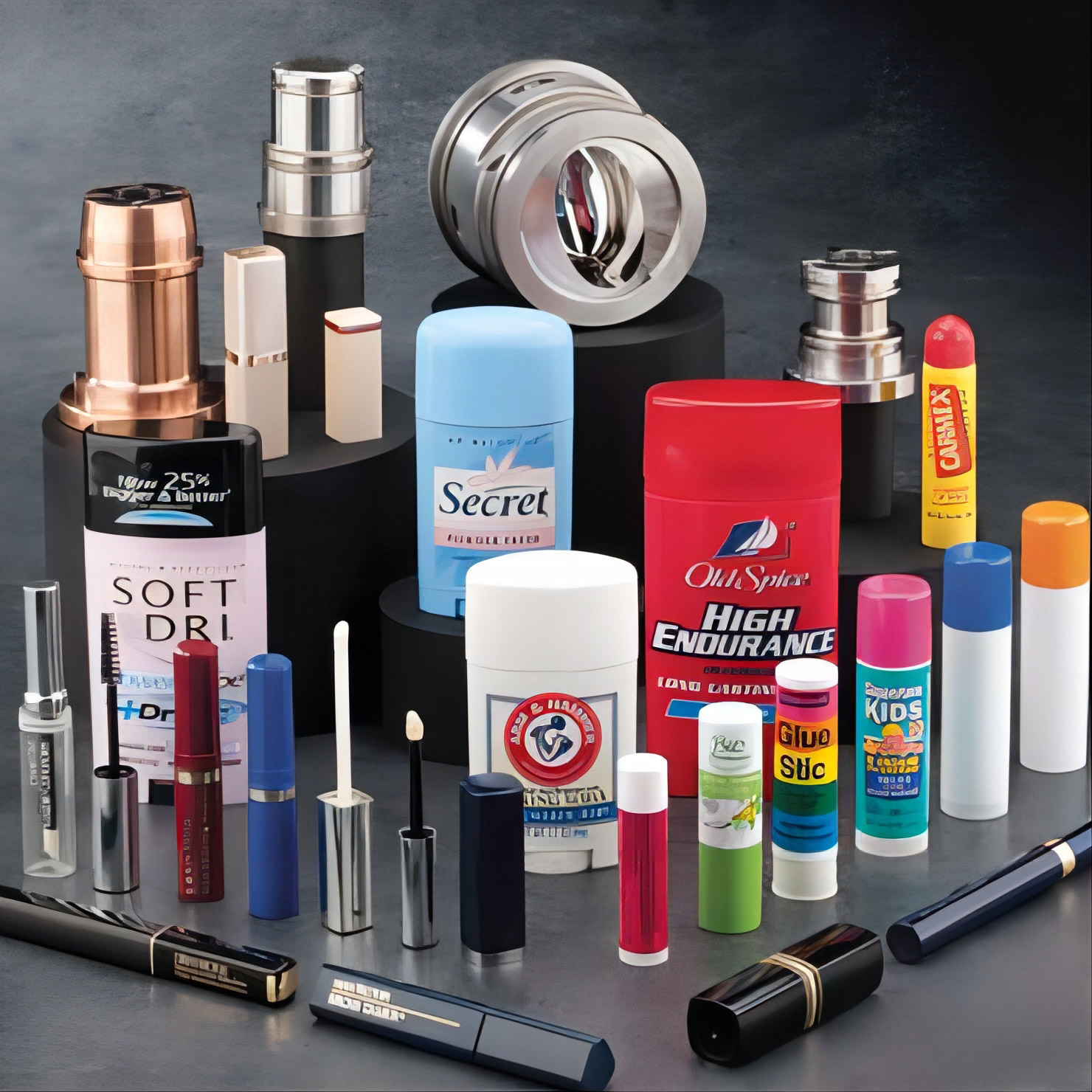
In today’s fast-paced manufacturing world, high-precision CNC machining plays a pivotal role in delivering complex components for global clients. Especially for international industries such as aerospace, medical devices, automotive, and advanced electronics, the demand for exacting standards and intricate designs is higher than ever. Chinese CNC machining manufacturers are increasingly recognized for their capability to provide bespoke solutions, tackling difficult materials and complex geometries with remarkable accuracy. This article explores the depth of expertise, advanced techniques, and innovative solutions that define professional CNC machining services tailored for worldwide clients seeking excellence in precision manufacturing.
---
## Custom CNC Machining Solutions Tailored to Client Specifications
Custom CNC machining is at the core of delivering precise, client-specific parts, especially when dealing with complex or unconventional designs. Chinese CNC manufacturers excel in interpreting detailed drawings and specifications, transforming them into real-world components with tight tolerances. They offer comprehensive services that include 3D modeling, prototype development, and small-batch or mass production runs, ensuring flexibility to meet diverse project demands.
Understanding each client’s unique needs, these providers utilize advanced CAD/CAM systems to optimize tool paths and machining strategies, reducing waste and improving efficiency. Custom solutions often involve multi-axis machining, enabling the creation of intricate features and geometries that conventional methods cannot achieve. Whether a client requires high-precision aerospace components or delicate medical implants, these manufacturers adapt their processes to fulfill exact specifications.
Collaboration is key in custom CNC projects. Manufacturers frequently work closely with clients to refine designs for manufacturability, preventing potential issues early in the process. This proactive approach minimizes errors, shortens production cycles, and ensures the final product meets or exceeds quality expectations. The ability to deliver tailored, high-precision solutions positions Chinese CNC machining firms as essential partners in global supply chains.
Furthermore, customization extends beyond just design adaptation. Surface finishes, coatings, and treatments are tailored to client needs, enhancing durability, corrosion resistance, or aesthetic appeal. This holistic approach to customization ensures that each part is optimized for its specific application, providing value-added solutions that stand out in competitive markets.
In a global landscape where precision and reliability are paramount, custom CNC machining services ensure that clients receive parts precisely aligned with their technical and functional requirements. This commitment to bespoke solutions underscores the strategic importance of experienced, capable manufacturing partners in achieving project success.
---
## High-Precision CNC Services for Complex Mechanical Components
The production of complex mechanical components demands not only advanced machinery but also extensive experience and meticulous process control. Chinese CNC machining factories are renowned for their ability to produce high-precision parts that meet stringent international standards, often surpassing client expectations.
These services encompass multi-axis machining, which allows for the creation of intricate features such as internal channels, thin walls, and complex geometries. High-precision CNC centers equipped with sophisticated tools and measurement systems guarantee that each feature adheres to the tightest tolerances, often within ±0.01mm or better.
Complex components frequently involve tight mating fits and critical dimensional requirements, especially in aerospace and medical applications. Manufacturers utilize high-precision measurement equipment like CMMs (Coordinate Measuring Machines) to verify dimensions throughout production, ensuring consistency and accuracy. This rigorous quality control process is essential for parts that require flawless functionality, safety, and longevity.
Moreover, the machining of complex mechanical parts often includes multiple operations—milling, turning, drilling, and finishing—integrated seamlessly via advanced machining centers. This integrated approach reduces handling errors, enhances precision, and improves turnaround times. Skilled technicians with deep process knowledge optimize machining parameters, select appropriate cutting tools, and implement real-time adjustments for optimal results.
In addition, these manufacturers are adept at handling tight deadlines without compromising quality. Their extensive experience with complex parts means they understand how to troubleshoot issues like deformation, tool wear, or thermal effects that could jeopardize precision. As a result, clients receive reliable, high-quality components that perform flawlessly in demanding environments.
The ability to produce complex mechanical components with high precision directly impacts the performance, safety, and reliability of end products. Chinese CNC service providers excel in this niche, offering expert solutions that meet the most challenging specifications on a global scale.
---
## Advanced Material Applications in CNC Machining Processes
Material selection is a critical factor influencing the success of CNC machining projects. Chinese manufacturers are proficient in working with a broad spectrum of advanced materials, including titanium alloys, stainless steels, Inconel, ceramics, and composites. Their expertise ensures that each material is machined efficiently while maintaining structural integrity and surface quality.
Titanium and Inconel are commonly used in aerospace and medical implants due to their strength, corrosion resistance, and biocompatibility. Machining these materials requires specialized cutting tools, high spindle power, and precise control to avoid issues like work hardening or thermal deformation. Chinese manufacturers have invested in high-performance equipment and tools designed specifically for such challenging materials.
Ceramics and composites, known for their hardness and lightweight properties, are increasingly used in electronic and aerospace applications. Machining ceramics demands exceptional skill and specialized tools to prevent cracking or chipping. The experience of Chinese CNC providers in grinding, polishing, and precision cutting ensures these delicate materials are handled with care, achieving the desired tolerances and surface finishes.
Surface treatments and coatings, such as anodizing, PVD, or DLC, are often applied post-machining to enhance performance. Manufacturers coordinate these secondary processes seamlessly within the workflow, ensuring that the quality of the material properties is preserved.
The ability to work with advanced materials expands the scope of applications, enabling the production of high-performance parts that can withstand extreme environments. It also demonstrates the technical prowess and versatility of Chinese CNC machining companies, which can adapt their processes to the unique demands of each material type.
Overall, advanced material applications in CNC machining not only improve product performance but also open new avenues for innovation and high-value manufacturing, cementing the role of experienced Chinese manufacturers in the global high-precision market.
---
## Overcoming Global Challenges in Precision Manufacturing
Global manufacturing faces numerous challenges, including strict quality standards, tight delivery schedules, diverse material requirements, and the need for seamless communication across borders. Chinese CNC machining firms have risen to these challenges by establishing robust quality systems, investing in cutting-edge technology, and fostering international cooperation.
One of the primary hurdles is maintaining consistent quality across large production runs. Chinese manufacturers implement rigorous quality control protocols, utilize advanced measurement systems, and adhere to international standards such as ISO 9001 and AS9100 for aerospace. These measures ensure reliability, traceability, and compliance with client specifications.
Supply chain disruptions and logistical complexities are other challenges faced by global clients. To mitigate these issues, many Chinese CNC firms develop flexible manufacturing schedules and maintain strategic inventory levels. They also work with a global network of logistics providers to ensure timely delivery, regardless of geographic location.
Cultural and language barriers are addressed through dedicated project management teams fluent in multiple languages and experienced in international communication. This approach ensures clear understanding of technical requirements and reduces misunderstandings that could impact product quality or delivery.
Adapting to different regulatory environments, safety standards, and quality expectations requires extensive experience and local knowledge. Chinese CNC manufacturers often partner with local regulatory bodies or obtain relevant certifications to streamline compliance processes for overseas clients.
Technological innovation is also critical in overcoming manufacturing hurdles. Many Chinese firms adopt Industry 4.0 principles, including automation, IoT integration, and data analytics, to enhance process stability and traceability. This technological edge helps them deliver precision components consistently and efficiently on a global scale.
In essence, overcoming global manufacturing challenges demands a combination of technical expertise, adaptable processes, and strategic planning—areas in which Chinese CNC machining companies have demonstrated significant strength and reliability.
---
## Expertise in Machining Difficult Materials for Unique Projects
Machining difficult materials such as titanium, tungsten, ceramics, and high-temperature alloys requires not only advanced equipment but also deep expertise and experience. Chinese CNC machining providers have developed specialized skills and processes to handle these challenging materials effectively.
For instance, titanium and its alloys are popular in aerospace and medical devices but are known for their difficult machinability. Precision tools, high spindle speeds, and optimized cutting parameters are essential to prevent issues like work hardening or excessive tool wear. Experts at Chinese firms leverage their extensive experience to develop tailored machining strategies, ensuring high precision and surface quality.
Ceramics, being extremely hard and brittle, demand precise control during grinding and polishing. Specialized tools, slow feed rates, and post-processing techniques like ultrasonic machining are employed to achieve the required tolerances and finish quality. Skilled technicians understand the material behavior and can troubleshoot problems such as chipping or cracking.
High-temperature alloys like Inconel are resistant to corrosion and deformation but require high-performance cutting tools and coolant systems to manage heat. Experienced operators adjust machining parameters dynamically, balancing speed and precision to prevent excessive tool wear.
The mastery of machining difficult materials enables the creation of components that perform reliably under extreme conditions, such as aerospace engine parts, medical implants, or electronic components in harsh environments. These capabilities position Chinese CNC service providers as leaders in niche markets demanding specialized expertise.
Moreover, ongoing research and development efforts are continuously expanding the range of materials and techniques. The integration of new tooling, cooling methods, and process automation further enhances their capacity to tackle unique projects with confidence and precision.
In summary, expertise in machining difficult materials is a cornerstone of high-precision manufacturing, ensuring that clients receive functional, durable components tailored to their demanding applications.
---
## Case Studies: Solving Global Precision Manufacturing Challenges
Real-world case studies exemplify the capability of Chinese CNC machining firms to solve complex, high-stakes manufacturing challenges. These examples highlight the application of advanced techniques, problem-solving skills, and collaborative approaches to meet global client demands.
One notable case involved the production of aerospace engine components requiring ultra-high precision and complex geometries. The Chinese manufacturer employed five-axis machining combined with specialized tooling to achieve the tight tolerances. By integrating real-time measurement and adaptive control, they minimized errors and delivered the components ahead of schedule, meeting all safety and performance standards.
Another example centers on medical implants made from titanium alloy. The challenge was machining intricate shapes with high surface quality. The solution involved customized fixture design, optimized cutting parameters, and post-machining surface treatments. The result was implants that met biocompatibility standards and passed rigorous sterilization tests, gaining approval in international markets.
A different case focused on high-performance electronic components using ceramic materials. The manufacturer utilized ultrasonic-assisted grinding and polishing to achieve precise features without cracking. This enabled the client to develop advanced electronic devices with enhanced durability and performance.
These case studies showcase how deep technical expertise, innovative process integration, and proactive communication can overcome seemingly insurmountable manufacturing hurdles. They reinforce the importance of experienced partners who understand material behaviors, complex geometries, and international standards.
The successful resolution of such challenges not only benefits immediate project goals but also strengthens long-term client relationships and trust. Chinese CNC companies’ ability to adapt and innovate underpins their reputation as reliable global partners for high-precision manufacturing.
---
## The Importance of Experienced CNC Machining Teams Worldwide
Behind every successful high-precision CNC project is a team of experienced professionals—engineers, technicians, and quality control specialists—whose expertise ensures flawless execution. Chinese manufacturers emphasize building skilled teams with international experience, fostering a culture of continuous learning and innovation.
Experienced CNC teams possess a deep understanding of various materials, machining techniques, and industry standards. They can quickly troubleshoot issues such as tool wear, dimensional deviations, or surface defects, minimizing downtime and ensuring consistent quality.
Training and certifications are integral to maintaining high standards. Many Chinese firms invest heavily in workforce development, sending technicians for international certifications or engaging in knowledge exchange programs. This global perspective enhances their ability to meet diverse client requirements across different industries.
Communication skills are crucial, especially when collaborating with international clients. Multilingual teams facilitate clear technical discussions, reduce misunderstandings, and streamline project management. This cultural competence improves responsiveness and fosters long-term partnerships.
Moreover, experienced teams are adept at process optimization, leveraging data analytics and Industry 4.0 technologies. They can implement smart manufacturing practices that improve efficiency, traceability, and flexibility—vital for handling complex or small-batch projects.
The importance of such expertise cannot be overstated. It directly impacts the quality, delivery, and innovation capacity of CNC machining services. Chinese companies recognize that investing in talent development is key to maintaining their competitive edge in the global high-precision manufacturing arena.
In conclusion, highly skilled, globally aware CNC teams serve as the backbone of successful projects, ensuring clients worldwide receive parts that meet their exacting standards.
---
## Custom Fabrication of High-Complexity Parts for Various Industries
High-precision CNC machining enables the fabrication of complex parts required in diverse industries, each with unique specifications and operational environments. Chinese manufacturers have established a reputation for delivering high-quality, custom-fabricated components that push the boundaries of design and functionality.
In aerospace, parts like turbine blades, structural brackets, and engine components demand extreme precision, lightweight structures, and durability. Chinese firms utilize multi-axis machining, lightweight materials, and specialized surface treatments to meet these stringent requirements.
Medical industry components, including implants, surgical tools, and diagnostic devices, require biocompatibility, sterilizability, and complex geometries. Precise CNC machining ensures these parts fit perfectly and function reliably within the human body or medical systems.
Automotive applications benefit from high-precision parts such as transmission components, engine parts, and custom prototypes. These often involve working with high-strength steels and light alloys, requiring advanced tooling and process control.
Electronics and semiconductor industries rely on high-precision parts with micro-scale features. Chinese manufacturers employ micro-machining, laser integration, and cleanroom facilities to meet these demanding standards.
The versatility of Chinese CNC machining services allows for rapid prototyping, small-batch production, and full-scale manufacturing of high-complexity parts. This flexibility is vital for innovation-driven industries where design iterations and tight delivery timelines are common.
Overall, the ability to customize and reliably produce high-complexity parts across industries underscores Chinese manufacturers' strategic role in global high-precision manufacturing ecosystems.
---
## Ensuring Quality and Accuracy in Precision CNC Machining
Quality assurance is paramount in high-precision CNC machining, where deviations even by micrometers can compromise function or safety. Chinese CNC providers employ comprehensive quality management systems, advanced measurement techniques, and continuous process improvement to guarantee accuracy.
Calibration of machines and tooling is performed regularly to ensure consistent performance. State-of-the-art measurement equipment, including CMMs, laser scanners, and surface profilometers, verify dimensional accuracy throughout production.
Process control methodologies, such as Statistical Process Control (SPC), monitor critical parameters in real-time. Any deviations trigger immediate adjustments, preventing defective parts from progressing further in the production cycle.
Documentation and traceability are maintained meticulously, enabling clients to verify compliance with quality standards and facilitate audits. This transparency builds trust and meets international certification requirements.
Surface finish quality is achieved through optimized machining parameters and finishing processes like polishing, anodizing, or coating. These steps are carefully integrated into the workflow to meet functional and aesthetic criteria.
Training and certification programs ensure that technicians and quality inspectors stay updated on the latest standards and techniques. Continuous improvement practices, including feedback loops and root cause analysis, further enhance process stability.
In sum, robust quality assurance processes are embedded within Chinese CNC machining operations, delivering parts with consistent accuracy, durability, and reliability for demanding global clients.
---
## Innovative Techniques for Machining Difficult and Specialized Materials
To address the challenges of machining difficult and specialized materials, Chinese CNC companies adopt innovative techniques that push the boundaries of traditional manufacturing. These include ultrasonic-assisted machining, laser machining, and cryogenic processing.
Ultrasonic-assisted machining introduces high-frequency vibrations to cutting tools, reducing force and heat generation. This technique is particularly effective for brittle materials like ceramics or glass, enabling high-precision cuts without cracking.
Laser machining offers contactless, highly precise cutting, engraving, or drilling of difficult materials. It allows for complex geometries with minimal thermal distortion, suitable for delicate or heat-sensitive components.
Cryogenic machining involves cooling cutting tools and workpieces with liquid nitrogen, reducing thermal stress and tool wear. This method enhances machinability for materials like titanium or Inconel, extending tool life and improving surface integrity.
Furthermore, the integration of automation, robotics, and real-time monitoring systems enhances process stability and repeatability. These innovations enable the production of high-precision parts with complex features and strict quality requirements.
Research and development efforts continuously lead to new tooling materials and coatings that improve wear resistance and cutting performance. This commitment to technological innovation keeps Chinese CNC machining firms at the forefront of handling difficult and specialized materials.
Through these advanced techniques, Chinese manufacturers can fulfill projects requiring exceptional precision, surface finish, and material integrity, satisfying the most demanding global clients.
---
## Collaborating with International Clients for Customized Machining Projects
Effective collaboration with international clients requires more than just technical expertise; it involves understanding cultural nuances, communication clarity, and flexibility. Chinese CNC machining firms prioritize building transparent, cooperative relationships to ensure project success.
From initial consultation, they carefully interpret client drawings, specifications, and functional requirements. Multilingual teams facilitate seamless communication, reducing misunderstandings and ensuring alignment throughout the project lifecycle.
Project management systems are employed to provide real-time updates, track progress, and manage feedback. This transparency fosters trust and allows clients to make informed decisions or adjustments promptly.
Flexibility in accommodating design revisions, varying batch sizes, and delivery schedules is a hallmark of Chinese manufacturers. They adapt their processes to meet evolving project demands without compromising quality.
Quality control results, inspection reports, and certification documentation are shared with clients, reinforcing confidence in the final product. Post-delivery support and after-sales service further enhance long-term partnerships.
Cultural sensitivity, professionalism, and technical competence form the foundation of successful international collaborations. Chinese CNC machining firms understand the importance of aligning their expertise with client goals, ensuring that each customized project achieves its intended performance and quality standards.
---
## Future Trends in High-Precision CNC Machining Technologies
Looking ahead, the landscape of high-precision CNC machining is poised for transformative growth driven by technological advancements. Industry 4.0, smart manufacturing, and artificial intelligence will increasingly integrate into CNC processes, enhancing automation and predictive maintenance.
Additive manufacturing combined with subtractive CNC machining—hybrid processes—will enable the production of even more complex, lightweight, and high-performance parts. This integrated approach will accelerate innovation in aerospace, medical, and electronics sectors.
Machine learning algorithms will optimize machining parameters in real time, minimizing errors and defects, and enabling autonomous quality control. These intelligent systems will adapt to material behaviors and process variations dynamically.
Advanced materials, including composites, meta-materials, and nanomaterials, will become more prevalent, necessitating further innovation in tooling, cutting techniques, and surface treatments. Researchers are exploring laser-assisted, cryogenic, and ultrasonic methods to expand capabilities.
Digital twins and virtual simulation will allow manufacturers to test and validate machining processes before production, reducing trial-and-error and accelerating development cycles.
Sustainability considerations will influence future trends, with a focus on minimizing waste, energy consumption, and environmental impact. Eco-friendly coatings, recycled materials, and energy-efficient machinery will become standard.
In sum, the future of high-precision CNC machining will be characterized by smarter, faster, and more sustainable manufacturing methods, driven by continuous innovation and global collaboration—areas where Chinese manufacturers are actively investing and leading.
---
High-precision CNC machining is a vital component of advanced manufacturing, especially in a global context where quality, customization, and innovation are non-negotiable. Chinese CNC service providers have demonstrated exceptional expertise in tackling complex geometries, difficult materials, and stringent standards, making them valuable partners for international clients. Through continuous technological innovation, a skilled workforce, and a customer-centric approach, they are shaping the future of high-precision manufacturing. As industry demands evolve, these manufacturers will remain at the forefront, delivering solutions that meet the highest standards of accuracy, durability, and complexity—driving progress across industries worldwide.