Expert CNC Machining for High-Precision Overseas Clients
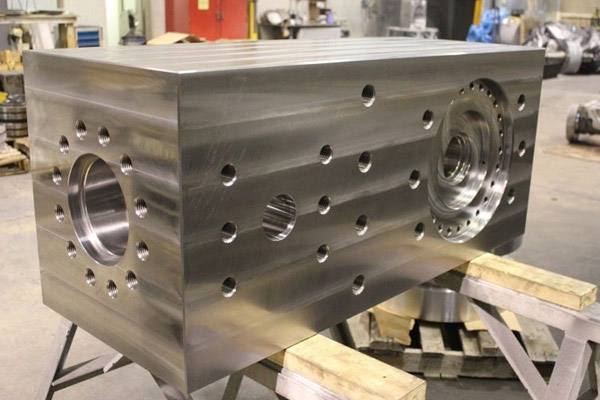
===INTRO:===
In today’s interconnected world, the demand for high-precision CNC machining services from overseas clients has surged significantly. Manufacturers across the globe seek reliable partners capable of delivering complex, custom-made components with impeccable accuracy. Chinese CNC machining factories have stepped up to meet this challenge, leveraging advanced technology, extensive experience, and a commitment to quality. This article explores the key aspects of expert CNC machining tailored for international clients, emphasizing the importance of customization, material selection, technological innovation, and problem-solving expertise. Whether it’s intricate high-precision parts or difficult material applications, China’s CNC manufacturers are proving to be invaluable partners in global manufacturing supply chains. Let’s delve deeper into how these factories excel in meeting the rigorous standards of worldwide industries.
Understanding the Importance of Custom CNC Machining for Overseas Clients
Custom CNC machining plays a pivotal role in fulfilling the unique requirements of overseas clients across various industries such as aerospace, medical devices, automotive, and electronics. Unlike mass-produced parts, custom machining ensures every component adheres precisely to detailed specifications, often involving complex geometries and tight tolerances. For international clients, this means peace of mind that their prototypes or production runs will meet their exact design needs without compromise.
Chinese CNC manufacturers excel in providing tailored solutions, from initial design consultation to final delivery. They invest in sophisticated software and machinery that can interpret detailed CAD files, ensuring that custom specifications are accurately translated into physical components. This flexibility is crucial for clients who require prototype development or small batch production with high precision.
Moreover, custom CNC services enable clients to innovate by experimenting with complex shapes and specialized materials that traditional manufacturing processes cannot handle efficiently. The ability to turn intricate digital designs into high-quality physical parts underscores the importance of customized CNC machining in today’s competitive global market.
International clients benefit not only from precision but also from the cost-effectiveness and rapid turnaround times that Chinese CNC factories offer. These advantages allow overseas companies to stay agile and responsive to market demands while maintaining high standards of quality and precision.
High-Precision CNC Machining: Meeting Global Industry Standards
Achieving high precision in CNC machining is vital for industries where safety, performance, and reliability are non-negotiable. Chinese CNC manufacturers have adopted rigorous standards to ensure their products meet or exceed global benchmarks such as ISO, ASME, and industry-specific certifications. These standards guarantee consistency, safety, and performance in high-precision components supplied internationally.
State-of-the-art equipment, such as multi-axis CNC machines, laser measuring systems, and coordinate measuring machines (CMM), are employed to monitor and control tolerances down to micrometers. Such precision is essential in sectors like aerospace, where even minute deviations can compromise safety, or in medical devices where accuracy directly impacts patient outcomes.
Compliance with international standards also involves establishing comprehensive quality management systems. Many Chinese CNC factories have obtained certifications such as ISO 9001, ISO 13485, and IATF 16949, underpinning their commitment to quality. These certifications demonstrate adherence to strict quality control protocols and continuous improvement practices, giving overseas clients confidence in their supply chain.
Furthermore, Chinese manufacturers often collaborate closely with clients during the development phase, providing feedback and adjustments to ensure that the final product aligns perfectly with industry standards and application-specific requirements. This proactive approach helps prevent costly errors and ensures the final parts are fit for purpose.
The capacity to produce high-precision parts consistently and reliably has elevated Chinese CNC machining as a trusted choice for international industries demanding exacting specifications. This reputation continues to grow as technological investments and quality practices advance.
Tailored CNC Solutions for Complex and High-Precision Parts
Many international industries demand components with intricate geometries, micro-features, or tight tolerances that challenge conventional manufacturing techniques. Chinese CNC machining factories excel in delivering customized solutions tailored to these complex requirements, leveraging their extensive experience and advanced equipment.
From multi-axis turning and milling to micro-machining, these factories can handle elaborate designs that involve deep cavities, fine threads, or complex surface finishes. For high-precision parts, the machining process often involves multiple steps, including drilling, tapping, grinding, and polishing, all coordinated seamlessly to achieve the desired outcome.
The ability to customize machining parameters, such as cutting speed, feed rate, and tool paths, allows factories to optimize each project for maximum precision and surface quality. Such flexibility is critical when producing parts with tight tolerances, complex features, or difficult geometries that standard processes cannot manage effectively.
Chinese manufacturers also provide comprehensive design support, working with clients to optimize CAD models for manufacturability. This proactive collaboration helps identify potential issues early, reduce lead times, and improve overall quality.
In addition, the capacity for small batch and prototype production enables clients to test and refine their designs before moving to large-scale manufacturing. This tailored approach ensures that each high-precision component meets the specific needs of the application, whether for aerospace, medical, or high-end electronics.
Selecting the Right Materials for Superior CNC Machining Results
Material selection is a fundamental factor influencing the success of high-precision CNC machining. Different materials have unique properties such as hardness, machinability, thermal stability, and corrosion resistance, all of which impact machining difficulty and final component performance.
Chinese CNC factories offer an extensive range of materials, including metals like aluminum, titanium, stainless steel, and alloy steels, as well as non-metals like plastics, ceramics, and composites. Material expertise is crucial when machining high-end components for demanding applications.
For instance, aerospace and medical parts often require titanium or specialized alloys, which offer strength-to-weight ratio and biocompatibility but pose challenges in machining due to their hardness and reactivity. Experienced Chinese manufacturers understand these nuances and utilize appropriate cutting tools, coolant systems, and machining parameters to optimize results.
Choosing the right material also involves considering factors such as cost, availability, and environmental factors. For example, plastics like PEEK or PTFE are preferred for medical devices due to their inert properties, while certain ceramics are used for high-temperature or wear-resistant applications.
In some cases, material properties dictate the selection of specialized machining techniques, such as high-speed cutting, cryogenic machining, or laser-assisted processes. Chinese CNC factories stay updated with material innovations and possess the expertise to handle the most challenging materials, ensuring durability and performance of the final parts.
Material expertise combined with advanced machining capabilities enables Chinese manufacturers to produce high-precision components that satisfy stringent international standards and client specifications.
The Role of Experienced Machining Experts in Achieving Accuracy
Behind every successful high-precision CNC component is a team of skilled and experienced machining experts. These professionals possess not only technical knowledge but also a deep understanding of the nuances involved in turning complex digital designs into flawless physical parts.
Chinese CNC factories prioritize training and skill development, ensuring their technicians are proficient in interpreting CAD/CAM files, selecting appropriate tools, and fine-tuning machine parameters for optimal results. Their expertise is especially critical when dealing with difficult-to-machine materials or complex geometries.
Experienced operators can anticipate potential issues such as tool wear, thermal expansion, or vibration, and adjust machining strategies accordingly. This proactive approach minimizes errors and reduces scrap rates, leading to better quality and cost savings.
Quality assurance also relies heavily on these experts conducting in-process inspections, making real-time adjustments, and performing final measurements using advanced metrology equipment. Their keen eye for detail ensures that each part meets the high-precision tolerances required by global clients.
Furthermore, seasoned technicians contribute to continuous improvement by analyzing machining data, implementing best practices, and exploring innovative techniques. This culture of expertise and innovation enhances the factory’s capability to deliver complex, high-precision parts reliably.
Chinese CNC manufacturers recognize that skilled human resources are as vital as cutting-edge machinery, and they invest heavily in developing their workforce to uphold international standards of accuracy and quality.
Overcoming Challenging Machining Tasks with Advanced Techniques
Some CNC machining projects involve formidable challenges, such as processing extremely hard materials, achieving ultra-fine tolerances, or replicating complex micro-geometries. Overcoming these hurdles requires advanced techniques, cutting-edge equipment, and innovative problem-solving strategies.
Chinese CNC factories are equipped with multi-axis machining centers, high-speed spindles, and specialized tooling designed to tackle tough materials like titanium, Inconel, ceramics, or composites. These tools are essential for reducing machining time and improving surface finishes on difficult materials.
Laser-assisted machining and cryogenic cooling are among the advanced techniques employed to enhance cutting performance and tool life. For instance, laser pre-heating can soften tough materials, making them easier to machine, while cryogenic cooling reduces thermal distortion and improves precision.
Additive manufacturing combined with CNC subtractive processes is increasingly used to produce complex parts that traditional methods cannot easily achieve. This hybrid approach enables the fabrication of intricate internal channels or micro-structures with high accuracy.
Specialized fixturing and vibration-damping systems are also implemented to maintain stability during machining, especially for long or delicate components. Such innovations help prevent deflections and ensure consistent quality.
Chinese manufacturers continually invest in research and development to stay ahead of machining challenges, exploring new materials, tools, and techniques. Their ability to adapt and innovate is key to overcoming complex and high-precision machining tasks.
Case Studies: Solving Global CNC Machining Difficulties
Real-world case studies highlight the expertise of Chinese CNC manufacturers in resolving complex manufacturing challenges. For example, one aerospace client required ultra-precise titanium components with micro-holes and intricate surface finishes. Through meticulous process planning, specialized tooling, and real-time monitoring, the factory successfully delivered parts within tight tolerances.
In another instance, a medical device company needed high-precision, biocompatible PEEK parts with micro-structural features. The manufacturer employed micro-milling and laser polishing to achieve the required specifications, demonstrating their capability to handle delicate and challenging materials.
A high-end electronics client sought complex aluminum heat sinks with integrated micro-channels for improved cooling. The Chinese factory utilized multi-axis CNC machining and custom fixturing to produce the micro-structures accurately, reducing assembly time and enhancing device performance.
In a more demanding project, a defense contractor required components made from Inconel, a difficult-to-machine superalloy. By adopting cryogenic machining and high-pressure coolant systems, the manufacturer managed to extend tool life and meet the stringent quality standards.
These case studies exemplify the problem-solving capacity and technological versatility of Chinese CNC manufacturers. Their ability to analyze, customize, and execute complex projects makes them invaluable partners for global clients facing difficult manufacturing tasks.
Ensuring Quality Control in High-Precision CNC Manufacturing
Quality control is the backbone of high-precision CNC machining, especially when serving international clients with rigorous standards. Chinese manufacturers implement comprehensive quality management systems, including detailed inspection protocols at every stage of production.
Advanced measurement tools such as CMM, laser scanners, and surface profilometers are employed for precise dimensional verification and surface quality assessments. These inspections ensure each part adheres to the specified tolerances, often within micrometer ranges.
In-line monitoring systems and automated process control software help detect deviations early, allowing immediate corrections and reducing scrap rates. This proactive approach maintains consistency and minimizes rework, which is vital for complex high-precision parts.
Traceability is also emphasized, with detailed records of raw materials, machining parameters, and inspection results maintained for each batch. Such documentation is critical for compliance with international standards and client audits.
Chinese CNC factories often participate in external quality audits and continuously improve their processes based on feedback and testing results. This dedication to quality assurance ensures that clients receive reliable, high-precision components every time.
Furthermore, staff training and certification programs foster a culture of quality awareness among operators and inspectors. This human factor complements technological measures, creating a robust quality control environment essential for high-stakes applications.
Collaborating Effectively with International Clients for Customized Projects
Successful international collaboration requires clear communication, understanding of client expectations, and flexibility from the manufacturer’s side. Chinese CNC manufacturers prioritize building strong relationships with overseas clients through transparent project management and regular updates.
Understanding client drawings, specifications, and functional requirements is the first step. Many factories employ bilingual staff and utilize advanced communication tools to facilitate seamless exchanges. This ensures that design intent is accurately interpreted and maintained throughout production.
Flexibility in production processes allows manufacturers to accommodate changes or adjustments requested by overseas clients, whether in design, materials, or delivery schedules. This adaptability fosters trust and long-term partnerships.
Quality assurance and timely delivery are core to effective collaboration. Regular reporting, inspection reports, and open channels for feedback help build confidence and facilitate continuous improvement.
Cultural understanding and proactive service also play vital roles. Chinese manufacturers often go the extra mile in providing technical support, troubleshooting, and post-production services, which enhance customer satisfaction.
Ultimately, successful international projects are rooted in mutual respect, clear communication, and a shared commitment to excellence. Chinese CNC factories have demonstrated their capability to serve high-precision global clients effectively through these collaborative practices.
Innovations in CNC Technology for Enhanced Precision and Efficiency
The landscape of CNC machining is constantly evolving, driven by technological innovations that improve accuracy, speed, and cost-efficiency. Chinese manufacturers are at the forefront of adopting and developing such innovations to meet the demanding needs of high-precision overseas clients.
Automation plays a significant role, with robotic loading/unloading systems, AI-driven process optimization, and real-time data analytics enhancing productivity and consistency. These advancements reduce human error and enable 24/7 manufacturing cycles.
Precision enhancement technologies, such as ultra-high-speed spindles, high-precision linear guides, and vibration-damping systems, allow for finer surface finishes and tighter tolerances. Laser and electron beam machining are also integrated for micro and nano-scale features.
Material innovations, including new alloys and composites, expand the design possibilities for clients. Correspondingly, CNC equipment is upgraded to handle these advanced materials effectively.
Software innovations, such as adaptive CAM programs and simulation tools, enable manufacturers to plan and optimize complex machining paths, reducing trial-and-error and waste. This digital integration accelerates development cycles and improves precision.
Research institutions and industry leaders in China continually push the boundaries of CNC technology, ensuring that factories remain competitive and capable of delivering cutting-edge solutions. These innovations translate into tangible benefits for global clients seeking high-precision, efficient, and reliable manufacturing services.
Common Challenges in High-Precision CNC Machining and How to Address Them
Despite technological advancements, high-precision CNC machining continues to face challenges such as thermal distortion, tool wear, material variability, and vibration. Effective strategies and expertise are necessary to overcome these issues.
Thermal distortion, caused by heat generated during cutting, can lead to dimensional inaccuracies. Using high-precision cooling systems, temperature-controlled environments, and optimized cutting parameters helps mitigate this problem.
Tool wear impacts surface quality and tolerances. Implementing high-quality, durable tooling and monitoring tool life allows timely replacements, maintaining machining accuracy.
Material variability, especially with exotic or composite materials, can cause inconsistencies. Understanding material behavior and adjusting machining parameters accordingly are critical for maintaining quality.
Vibration and deflection, particularly with large or delicate parts, can compromise precision. Advanced fixturing, damping techniques, and machine calibration are employed to minimize these effects.
Continuous staff training, process documentation, and adoption of predictive maintenance practices help manufacturers anticipate and address these challenges proactively. Emphasizing quality control and process optimization ensures that high-precision standards are consistently met, even in demanding scenarios.
Future Trends in CNC Machining for the Global Market
The future of CNC machining is poised to be shaped by Industry 4.0, automation, and digitalization. Chinese manufacturers are actively integrating these trends to enhance their offerings for international clients.
Smart factories leveraging IoT sensors, AI algorithms, and cloud-based data analytics will enable real-time monitoring and predictive maintenance, reducing downtime and increasing throughput. This technological leap will translate into faster turnaround times and higher precision.
Additive manufacturing combined with traditional CNC processes will open new horizons for complex, lightweight, and customized components. Hybrid manufacturing approaches will become more prevalent, offering unparalleled design freedom.
Material science innovations will continue to expand the selection of high-performance materials, demanding equally advanced machining techniques. The development of new tooling and cutting strategies will keep pace with these materials.
Sustainability will gain importance, with a focus on reducing waste, energy consumption, and carbon footprint. Chinese CNC factories are exploring environmentally friendly coolant systems and recycling practices to align with global eco-conscious standards.
Lastly, industry standards and certifications will evolve to demand even higher precision, traceability, and quality assurance, prompting continuous technological and process improvements. The future of CNC machining is bright, with Chinese manufacturers at the forefront, ready to meet the evolving needs of the global market.
OUTRO:
Chinese CNC machining factories have established themselves as reliable, innovative, and highly capable partners for overseas clients requiring high-precision, custom components. Their mastery of complex projects, advanced technology, material expertise, and commitment to quality control uniquely position them to solve some of the most challenging manufacturing problems worldwide. As industry standards continue to rise and technology advances, these manufacturers are poised to lead the way into a future of even greater precision, efficiency, and collaboration. For international industries seeking dependable partners in high-precision manufacturing, China’s CNC industry offers a compelling combination of experience, innovation, and global competitiveness.