Expert CNC Machining for High-Precision Custom Parts Worldwide
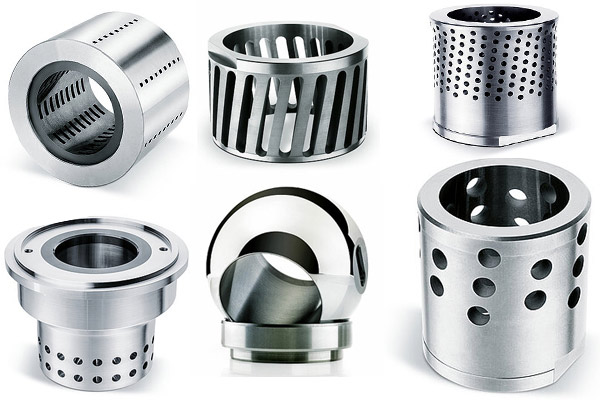
===INTRO:===
In the rapidly evolving world of manufacturing, the demand for high-precision, custom-engineered parts has surged across industries worldwide. Advanced CNC (Computer Numerical Control) machining has become the backbone of this trend, offering unparalleled accuracy and versatility. Especially for overseas clients seeking reliable, high-quality solutions, expert CNC machining providers in China have emerged as strategic partners. With extensive experience in turning complex designs into tangible products, these manufacturers excel at overcoming the most challenging machining tasks. This article explores the vital role of expert CNC machining in creating high-precision components, emphasizing material mastery, technological innovation, and global collaboration. Whether it’s aerospace, medical devices, or precision instrumentation, the significance of exact manufacturing cannot be overstated in today’s competitive landscape.
---
## Introduction to Expert CNC Machining for Custom High-Precision Parts
CNC machining has revolutionized manufacturing by enabling the production of intricate, high-precision parts with remarkable consistency. Expert providers leverage state-of-the-art equipment and skilled craftsmanship to realize complex designs that meet stringent specifications. Customization is at the core of these services, allowing clients worldwide to transform their ideas into reality. From prototyping to large-scale production, experienced CNC shops excel at handling a diverse array of materials and geometries. Their expertise ensures that each component conforms to exact dimensions, tolerances, and surface finishes, vital for high-performance applications. Such precision not only enhances product functionality but also reduces waste and downstream assembly issues, making expert CNC machining an indispensable part of modern manufacturing ecosystems.
---
## The Importance of Precise Manufacturing in Global Industries
Precision manufacturing is critical across numerous global industries, including aerospace, medical, automotive, and electronics. In aerospace, even minor deviations can compromise safety and performance, demanding absolute accuracy. Medical devices require meticulous attention to detail to ensure patient safety and regulatory compliance. Automotive components benefit from high precision for improved durability and fuel efficiency. Electronics rely on tiny, complex parts with tight tolerances for proper functioning. As industries become more interconnected and technology-driven, the need for consistent, high-quality parts has grown exponentially. Manufacturers worldwide recognize that investing in expert CNC machining capabilities translates into better product reliability, longer lifespan, and enhanced competitive advantage. The ability to produce parts that meet exact specifications is no longer optional but essential for success.
---
## Custom CNC Machining: Turning Designs into Realities Worldwide
Transforming a digital design into a physical component is the core function of custom CNC machining. Advanced software tools translate CAD files directly into machine instructions, enabling precise control over complex geometries. Expert CNC providers in China and other regions have honed their skills over years, mastering the nuances of various materials and finishing techniques. They work closely with clients to understand design intent, suggest improvements, and optimize manufacturing processes—all while maintaining the integrity of original concepts. This collaborative approach ensures that even the most intricate and high-difficulty parts are fabricated accurately and efficiently. The global reach of these services empowers companies worldwide to access high-quality, custom components without the need for extensive local facilities.
---
## Key Materials Used in High-Precision CNC Manufacturing
Material selection is fundamental to achieving the desired performance and durability of high-precision parts. Common materials include metals like aluminum, titanium, stainless steel, and superalloys, each offering unique characteristics suited for specific applications. Specialized plastics and composites also find use in lightweight or non-conductive components. Experts in CNC machining are well-versed in handling these diverse materials, understanding their properties, machining behaviors, and post-processing requirements. For example, titanium’s strength and corrosion resistance make it ideal for aerospace but present machining challenges that require experienced operators. Proper material choice ensures parts meet performance specifications, environmental resistance, and regulatory standards. This comprehensive material expertise is crucial for delivering reliable, high-quality components on a global scale.
---
## Challenges of Processing Complex and High-Difficulty Parts
High-precision machining of complex, high-difficulty parts presents numerous technical challenges. These include tight tolerances, intricate internal features, difficult-to-machine materials, and the need for multiple finishing processes. Such components often require multi-axis machining, advanced tooling, and strict process controls. For instance, micro-machining of tiny aerospace components or medical implants demands exceptional skill and equipment stability. The risk of tool wear, deformation, or dimensional inaccuracies increases with complexity. Overcoming these hurdles requires a combination of technological innovation, precise process planning, and experienced craftsmanship. Chinese CNC providers with rich experience have successfully tackled these issues, setting benchmarks in the industry by consistently delivering high-precision, complex parts worldwide.
---
## How Experienced CNC Machining Providers Ensure Quality and Precision
Achieving consistent quality and precision is the hallmark of seasoned CNC machining providers. They employ rigorous quality control measures, including coordinate measuring machines (CMM), laser scanning, and non-destructive testing. Their staff undergo continuous training to stay ahead of technological advancements and industry standards. Process validation, regular calibration of equipment, and detailed inspection protocols are standard practices. Additionally, they maintain open communication channels with clients to ensure specifications are met at every stage. Many top providers leverage automation and real-time monitoring to enhance accuracy and reduce errors. The culmination of these efforts results in parts that meet or exceed international standards, establishing trust and long-term partnerships with global clients.
---
## Case Studies: Overcoming Global CNC Machining Difficulties
Numerous case studies highlight the expertise of Chinese CNC manufacturers in overcoming global machining challenges. For example, one aerospace client required titanium components with complex internal channels and tight tolerances. Through innovative fixturing, multi-axis machining, and precise process control, the provider successfully delivered parts that passed stringent testing standards. Another case involved medical implants needing micro-machining on biocompatible materials, which posed significant challenges due to material fragility. By employing advanced micro-machining techniques and surface treatments, the manufacturer achieved the desired quality. These examples underscore the importance of experience, technological investment, and problem-solving skills in tackling the toughest manufacturing hurdles worldwide.
---
## The Role of Advanced Equipment in Achieving Exact Tolerances
High-precision CNC machining relies heavily on cutting-edge equipment capable of delivering exact tolerances. Multi-axis CNC centers, high-speed spindles, and specialized tooling enable complex geometries and fine finishes. Automation and intelligent control systems provide repeatability and stability, ensuring minimal deviations. For instance, Chinese manufacturers have invested in European and Japanese CNC machines, integrating them seamlessly to maximize productivity and accuracy. Additionally, innovations like adaptive machining and real-time feedback systems help compensate for material anisotropy or tool wear. The strategic use of advanced equipment directly correlates with the ability to produce high-precision parts consistently, meeting even the most demanding international standards.
---
## Behind the Scenes: The Process of Custom CNC Fabrication
The journey from concept to finished product involves multiple meticulous steps. Initially, detailed CAD models are created and reviewed with clients to confirm design intent. Next, CAM software generates optimized tool paths, considering material properties and machining constraints. Skilled operators then set up the CNC machines, ensuring proper tooling and fixture alignment. During production, real-time monitoring detects issues early, reducing waste and rework. Post-machining processes such as polishing, surface treatment, and quality inspection finalize the parts. Throughout, communication between manufacturer and client ensures transparency and adherence to specifications. This behind-the-scenes effort exemplifies the dedication and precision required to produce high-quality, custom CNC parts at a global level.
---
## Collaboration with Overseas Clients for Tailored High-Precision Parts
Global clients benefit from close collaboration with experienced Chinese CNC providers through clear communication, flexible logistics, and tailored solutions. Understanding client specifications, industry standards, and application environments enables manufacturers to tailor processes accordingly. Many companies offer comprehensive services, including design optimization, prototyping, and after-sales support, ensuring seamless project execution. Language barriers are often bridged via multilingual teams and digital communication tools, fostering transparency. By integrating client feedback at every stage, manufacturers deliver parts that precisely match expectations. This collaborative approach underscores the importance of trust, technical expertise, and cultural understanding in achieving successful international partnerships.
---
## Ensuring Material Integrity and Performance in Every Project
Maintaining material integrity throughout manufacturing processes is vital for the performance of high-precision components. Expert CNC providers adhere to strict handling protocols, especially for sensitive or high-performance materials like titanium or superalloys. Proper storage, post-processing heat treatments, and surface finishing techniques help preserve material properties. Inspection methods verify that parts meet not only dimensional tolerances but also structural and surface quality standards. For critical applications, additional testing such as non-destructive evaluation (NDE) ensures reliability and safety. These practices guarantee that every part withstands real-world conditions, delivering consistent performance across industries and geographies.
---
## Future Trends in CNC Machining for High-Precision Manufacturing
Looking ahead, the future of CNC machining is set to become even more advanced with the integration of AI, automation, and data-driven quality control. Smart machines with self-learning capabilities will optimize processes in real-time, reducing errors and enhancing efficiency. The adoption of additive manufacturing techniques alongside traditional CNC processes promises more complex, lightweight, and customizable parts. Material science innovations will enable the use of new composites and alloys tailored for specific performance needs. Furthermore, increased emphasis on sustainability will drive eco-friendly manufacturing practices. As Chinese manufacturers continue to innovate and invest in cutting-edge technology, their role in global high-precision manufacturing will become even more pivotal.
---
===OUTRO:===
Expert CNC machining, especially from experienced Chinese providers, plays a crucial role in meeting the escalating global demand for high-precision, custom-designed parts. Their mastery over complex geometries, diverse materials, and advanced equipment ensures that clients worldwide receive reliable, top-quality components. As technology continues to evolve, these manufacturers will push the boundaries of what’s possible, contributing to innovations across industries. By harnessing experience, meticulous process control, and collaborative partnerships, they are shaping the future of high-precision manufacturing—delivering precision, performance, and excellence worldwide.