Expert CNC Machining for High-Precision Global Clients
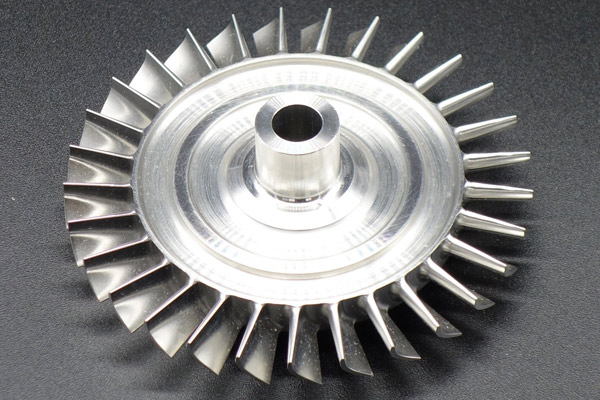
# Expert CNC Machining for High-Precision Global Clients
In today’s interconnected world, industries like aerospace, medical devices, automotive, and electronics demand components that meet the highest standards of precision and reliability. CNC machining has become the backbone of manufacturing these complex parts, especially when customized solutions are critical. China-based CNC manufacturers are increasingly recognized for their expertise in delivering high-precision, tailored machining services to international clients. This article explores how expert CNC machining, with its focus on customization, material versatility, and extensive experience, is revolutionizing global manufacturing and overcoming industry challenges with innovative solutions.
## Expert CNC Machining: Delivering Precision for Global Industries
CNC (Computer Numerical Control) machining stands at the forefront of precision manufacturing, serving diverse industries worldwide. Expert CNC machining providers leverage advanced technology and skilled craftsmanship to produce parts with tight tolerances, intricate geometries, and consistent quality. By integrating state-of-the-art equipment and rigorous quality control, these manufacturers ensure that each component adheres to exact specifications. For global clients, this means reliable delivery of high-precision parts for critical applications, from aerospace to medical devices, where failure is not an option. Such expertise hinges on a deep understanding of machining processes and the ability to adapt to complex design requirements.
Beyond precision, these manufacturers excel in scaling production efficiently, managing intricate projects, and maintaining competitive lead times. Their proficiency enables them to handle a wide variety of materials—metals, plastics, composites—each with unique machining challenges. The result is a comprehensive service that emphasizes quality and consistency, essential for international markets where specifications are often stringent and inspection standards rigorous.
Furthermore, expert CNC machining providers offer comprehensive solutions beyond just manufacturing. They assist clients in design optimization, reducing costs while ensuring manufacturability. This collaborative approach enhances product performance and simplifies the supply chain, building long-term partnerships based on trust and technical excellence. As global industries evolve, the role of expert CNC machining becomes increasingly vital in delivering innovative, high-precision components that meet diverse and demanding specifications.
## Custom CNC Solutions Tailored to Client Specifications Worldwide
Every client’s project is unique, requiring highly customized CNC machining solutions. Leading manufacturers understand the importance of tailoring processes to meet specific design, material, and functional requirements. This involves detailed consultations, precise interpretation of technical drawings, and often, iterative prototyping to refine the final product. Customization starts with comprehensive analysis—identifying critical dimensions, tolerances, surface finishes, and functional features essential for the application.
Chinese CNC manufacturers, in particular, excel in producing complex, high-precision parts according to international standards. They employ advanced CAD/CAM systems to translate client designs into precise machine instructions, ensuring accuracy from the first part to the last. The ability to process high-difficulty components, such as micro-sized parts or those with intricate internal geometries, sets these providers apart. They also adapt to various standards—ISO, ASME, DIN—catering to a global client base with diverse requirements.
Material selection is another key aspect of customization. Different applications demand different properties; aerospace parts require lightweight, high-strength alloys, while medical implants need biocompatible materials. Custom CNC solutions incorporate appropriate tooling, fixturing, and process parameters to optimize machining for each material. This flexibility ensures clients receive parts that not only meet design specifications but also enhance overall product performance and durability.
Moreover, these manufacturers often offer value-added services such as surface treatment, heat treatment, and assembly, providing a complete turnkey solution. This integrated approach minimizes the need for multiple suppliers, reduces lead times, and guarantees that the final product aligns perfectly with client expectations. Custom CNC machining thus becomes a strategic tool for global companies seeking precision, reliability, and innovation in their manufacturing processes.
## High-Precision CNC Processing for Complex and Intricate Parts
Processing complex and intricate parts demands exceptional skill, advanced equipment, and meticulous attention to detail. Expert CNC machining services are well-equipped to handle high-precision tasks involving micro-machining, multi-axis operations, and fine finishing. These capabilities are crucial in industries such as aerospace and medical, where components often feature intricate geometries, tight tolerances, and surface quality requirements.
Multi-axis CNC machines, such as 5-axis or even 7-axis systems, enable the production of complex geometries that would be impossible with traditional machining. These machines allow for continuous tool movement, reducing the need for multiple setups and increasing accuracy. As a result, manufacturers can achieve intricate features like internal channels, curved surfaces, and complex cut-outs with high precision.
High-precision CNC processing also involves sophisticated measurement and control systems, such as laser scanners and coordinate measuring machines (CMM), to verify dimensions during and after production. This ensures that each part conforms to strict tolerances, often within micrometer ranges. Achieving such accuracy reduces the risk of failure in critical applications, where even minor deviations can lead to significant issues.
Furthermore, processing complex parts often requires specialized tooling and fixturing to securely hold delicate components during machining. Experienced CNC providers develop custom fixtures and employ advanced cutting strategies to minimize deformation and maximize surface quality. The combination of technology and expertise allows for the production of intricate components with high repeatability and minimal errors, satisfying the demanding needs of global high-precision markets.
## Utilizing Advanced Materials for Superior Machining Outcomes
Material choice plays a pivotal role in delivering high-performance CNC machined components. Expert manufacturers are proficient in working with a broad spectrum of advanced materials—such as titanium alloys, stainless steels, aluminum composites, and medical-grade polymers—each presenting unique machining challenges.
Titanium, for example, is widely used in aerospace due to its high strength-to-weight ratio and corrosion resistance. Machining titanium requires specialized tools and controlled cutting conditions to prevent issues like work hardening and tool wear. Chinese CNC experts have developed extensive experience in handling such materials, optimizing parameters to achieve precise, clean cuts while extending tool life.
Similarly, superalloys like inconel are favored in high-temperature aerospace applications. These materials demand high cutting forces and generate significant heat, necessitating advanced cooling and lubrication techniques. Manufacturers with deep knowledge of material behavior can implement these techniques to produce complex parts reliably.
Medical-grade polymers and biocompatible materials also require precise processing to meet strict hygiene, safety, and functional standards. CNC machining of these materials often involves low-temperature, high-precision operations to prevent surface contamination or deformation.
Handling diverse materials effectively requires not only advanced machinery but also a thorough understanding of material properties and failure modes. Expert CNC providers continually update their knowledge and tooling options to meet evolving material demands, ensuring superior outcomes regardless of material complexity.
## The Critical Role of Extensive Experience in CNC Manufacturing
Experience is a cornerstone for achieving high-precision, complex manufacturing outcomes. Established CNC machining firms have accumulated years of hands-on expertise, enabling them to anticipate and resolve potential issues before they impact quality or delivery.
Seasoned manufacturers understand the nuances of different materials, cutting tools, and machine capabilities. They recognize subtle signs indicating possible deviations, allowing for proactive adjustments. This knowledge minimizes errors, reduces waste, and ensures consistent quality across large production runs.
Moreover, vast experience informs process optimization—identifying the most efficient sequence of operations, tooling combinations, and fixture designs. This results in shorter lead times and cost savings for clients, especially when dealing with high-difficulty parts. It also enhances their ability to undertake complex projects that require multi-stage processing or custom solutions.
Experience also fosters innovation. Veteran CNC providers develop proprietary techniques and process improvements that push the boundaries of precision and complexity. They stay ahead of technological trends, integrating new tools and methods that increase efficiency and quality for clients worldwide.
Additionally, an experienced manufacturer understands international standards and quality protocols, ensuring compliance with client specifications and certification requirements. This reliability is vital for global clients who depend on consistent, high-precision outputs for mission-critical applications.
## Overcoming Global Challenges in High-Precision CNC Machining
Global manufacturing presents numerous challenges—different standards, supply chain complexities, and logistical hurdles—that expert CNC machining providers must navigate. Overcoming these obstacles requires robust processes, adaptive strategies, and a customer-centric approach.
Language and cultural differences can complicate communication, potentially leading to misunderstandings of specifications. Experienced manufacturers mitigate this through clear documentation, regular updates, and multilingual support, ensuring that client requirements are accurately interpreted and executed.
Supply chain disruptions, especially in sourcing advanced materials or specialized tooling, pose risks to timely delivery. To counter this, reputable CNC providers establish diversified sourcing channels and maintain strategic inventories, minimizing delays and maintaining project momentum.
Logistical hurdles, including international shipping and customs clearance, are addressed through comprehensive planning and collaboration with reliable logistics partners. This ensures that high-precision components reach clients on schedule, regardless of location.
Furthermore, quality assurance across borders demands stringent inspection and documentation. Leading manufacturers implement rigorous internal testing and provide comprehensive reports—such as CMM data and material certificates—to guarantee that each part meets global standards.
Adapting to international regulatory requirements and certifications is also essential. Experienced CNC providers stay informed about evolving standards and incorporate necessary adjustments into their processes, ensuring that exported parts are fully compliant and ready for deployment worldwide.
## Case Studies of Complex CNC Machining Difficulties and Solutions
Real-world examples highlight the expertise required for high-precision CNC machining. One such case involved manufacturing aerospace turbine blades with complex internal cooling channels. These features demanded multi-axis machining, meticulous fixturing, and advanced cooling techniques. The solution involved custom jigs, high-speed spindle operations, and in-process inspection, resulting in blades that met strict aerodynamic and thermal specifications.
Another example centered on medical implants requiring biocompatible titanium with micro-level surface finishes. The challenge lay in machining delicate features without deformation or contamination. The manufacturer employed specialized low-force tools, ultra-fine polishing, and cleanroom conditions, achieving parts that fulfilled both functional and regulatory standards.
A third case involved high-strength stainless steel components for automotive applications subjected to high stress conditions. Machining these parts was complicated by work hardening and tool wear. The solution included optimized cutting speeds, high-performance coolant systems, and high-quality carbide tooling, significantly improving process stability and tool longevity.
These examples demonstrate the importance of tailored solutions, technological innovation, and experience-driven process control. They also underscore the value of collaboration and continuous improvement in tackling complex challenges in CNC manufacturing.
## How Customization Ensures Perfect Fit and Functionality
Customization in CNC machining is not just about producing parts to print; it’s about ensuring that each component integrates seamlessly into the final product with optimal functionality. Precise customization involves adjusting tooling, process parameters, and finishing techniques to suit specific design features and operational requirements.
For example, tight tolerances—often within micrometers—are critical in aerospace and medical applications. Custom fixture design and process calibration guarantee that each part meets these exacting standards. Surface finish requirements, such as mirror polishing or textured surfaces, are achieved through bespoke machining strategies and post-processing treatments.
Moreover, customization extends to incorporating features like threaded holes, complex contours, or internal channels that enhance the part's usability and assembly. These features require specialized tooling and multi-stage processes, which experienced CNC providers can execute efficiently.
By tailoring machining strategies to material characteristics and functional demands, manufacturers ensure durability, performance, and ease of assembly. This guarantees that the final product not only fits perfectly but also functions reliably under operational stresses.
In essence, customized CNC solutions bridge the gap between design intent and real-world performance, delivering parts that are precisely crafted to meet the specific needs of global clients and their end-users.
## Precision Engineering for Aerospace and Medical Applications
Aerospace and medical sectors exemplify high-precision engineering demands. Components used in these industries must adhere to the highest standards of accuracy, safety, and reliability. CNC machining provides the capability to produce such critical parts through meticulous process control and advanced technology.
In aerospace, high-strength alloys and lightweight materials are machined into turbine blades, structural brackets, and other vital components. The emphasis is on achieving complex geometries with exacting tolerances to ensure aerodynamic efficiency, thermal stability, and structural integrity. The parts often undergo rigorous inspection, including CMM testing and non-destructive evaluation, to validate precision.
Medical applications require biocompatible, corrosion-resistant materials like titanium, stainless steel, or medical-grade polymers. Machining these materials involves fine surface finishes, micro-machining, and strict contamination control. The goal is to produce implants, surgical instruments, and diagnostic components that meet strict regulatory standards and function flawlessly within the human body.
Expert CNC providers incorporate a comprehensive quality management system, adhering to standards such as ISO 13485 for medical devices or AS9100 for aerospace. They also leverage traceability, documentation, and validation processes to certify that each component meets or exceeds industry requirements.
This level of precision engineering ensures safety, performance, and longevity of critical components, ultimately saving lives and supporting technological advancements in these specialized fields.
## Managing Material Diversity in High-Precision CNC Projects
Handling diverse materials in high-precision CNC projects demands adaptability, specialized tooling, and process expertise. Different materials—metals, plastics, composites—present unique machining challenges, including varying hardness levels, thermal properties, and chip formation behaviors.
Steel and titanium alloys require robust cutting tools and cooling strategies to prevent work hardening and excessive tool wear. Aluminum and plastics, on the other hand, benefit from high-speed machining and optimized feed rates to achieve smooth finishes without deformation. Composites demand careful tool selection to prevent delamination and fiber pull-out.
Expert providers develop tailored machining protocols for each material, considering their specific characteristics. They may utilize carbide or ceramic tools, high-pressure coolant systems, and vibration damping fixtures to optimize outcomes. Additionally, they leverage software simulations and in-process inspections to predict and control potential issues.
Material management also involves sourcing quality raw materials with consistent properties, especially when dealing with specialized alloys. This ensures parts meet the required specifications without costly rework or delays.
By mastering material diversity, experienced CNC manufacturers can deliver a wide range of high-precision components, expanding their service scope to meet the evolving needs of global industries.
## Ensuring Quality and Accuracy in International CNC Orders
For international clients, quality assurance and accuracy are paramount. Expert CNC machining providers implement rigorous inspection regimes, including 3D measurement, surface roughness analysis, and compliance testing, to ensure each order meets precise specifications.
They utilize advanced measurement equipment like coordinate measuring machines (CMM) and optical scanners to verify dimensions at multiple stages. Documentation such as process reports, certificates of conformity, and inspection records accompany each shipment, providing transparency and traceability.
Adherence to international standards—ISO 9001, ISO 13485, AS9100—ensures consistent quality regardless of geographic location. Moreover, these manufacturers often establish dedicated quality teams that perform final audits and coordinate with logistics to prevent damage and loss during transit.
Technology integration, such as real-time monitoring and digital twins, helps maintain process control and predict potential deviations before they impact the final product. This proactive approach enhances reliability and customer confidence in global supply chains.
Ultimately, meticulous attention to quality and accuracy ensures that international clients receive parts that meet their demanding standards, supporting their compliance, safety, and performance objectives.
## Future Trends in CNC Machining for Global High-Precision Markets
The landscape of CNC machining is constantly evolving with technological innovations. Future trends include the integration of artificial intelligence (AI) and machine learning to optimize processes, predictive maintenance, and real-time quality control. These advancements will lead to even higher precision, efficiency, and flexibility.
Additive manufacturing (3D printing) is increasingly complementing traditional CNC processes, enabling rapid prototyping and complex geometries that are difficult to machine conventionally. Hybrid manufacturing solutions will become more prevalent, offering tailored, high-value components.
Furthermore, Industry 4.0 concepts—IoT connectivity, big data analytics, and automation—will enhance transparency, traceability, and responsiveness in CNC operations. This will facilitate smarter supply chains and customized manufacturing at scale.
The adoption of new materials, such as composites and high-performance alloys, will expand, demanding continuous innovation in tooling and process control. Sustainability efforts will also drive the development of eco-friendly machining fluids, waste reduction techniques, and energy-efficient equipment.
As global industries pursue higher safety, quality, and innovation standards, CNC machining will evolve towards more integrated, intelligent, and sustainable manufacturing ecosystems—keeping China and other global leaders at the forefront of high-precision manufacturing excellence.
---
## OUTRO:
Expert CNC machining, especially from experienced Chinese manufacturers, is transforming global high-precision industries. Their capabilities in customization, complex processing, and material handling, combined with a deep understanding of industry standards, empower clients worldwide to achieve manufacturing excellence. As technological innovations continue to shape the future, these manufacturers will remain vital partners in delivering precise, reliable, and innovative components for the most demanding applications.