Expert CNC Machining for High-Precision Global Clients
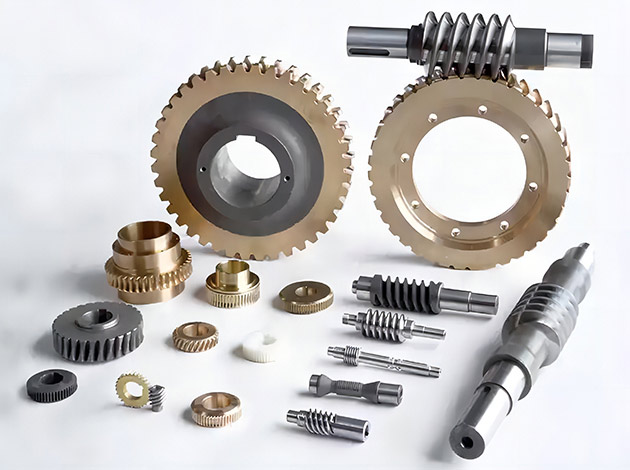
# Expert CNC Machining for High-Precision Global Clients
---
### ===INTRO:
In the rapidly evolving landscape of manufacturing, high-precision CNC machining has become a cornerstone for delivering intricate and demanding components to clients worldwide. As industries such as aerospace, medical, electronics, and automotive push the boundaries of technology, the need for reliable, accurate, and customized machining solutions grows exponentially. Chinese CNC machining manufacturers, renowned for their advanced capabilities and cost-effective solutions, now serve a global clientele with a focus on high-end, precise parts. This article explores how expert CNC machining services are tailored to meet the complex needs of international clients, emphasizing custom solutions, material expertise, and overcoming machining challenges with innovative approaches.
---
## Precision CNC Machining: Tailored Solutions for Global High-End Clients
High-precision CNC machining is not merely about cutting metal; it’s about delivering tailor-made solutions that meet exact specifications. For international clients demanding the utmost accuracy, Chinese CNC manufacturers offer comprehensive customization based on detailed technical drawings, ensuring each component aligns perfectly with project requirements. These tailored solutions incorporate advanced programming, meticulous setup, and tight tolerances, often within micrometer ranges, to ensure parts perform flawlessly in their application. Whether it’s aerospace components with complex geometries or medical implants requiring flawless surface finishes, the ability to customize every detail is essential for satisfying high-end global markets.
Manufacturers invest heavily in sophisticated CNC equipment—multi-axis machines, high-speed spindles, and specialized tooling—to address unique client specifications. The integration of CAD/CAM software allows precise translation of digital designs into manufacturable programs, enabling seamless production of complex parts. Moreover, customization extends beyond machining; it involves selecting appropriate surface treatments, coatings, and finishing processes tailored to the end-use environment. This holistic approach ensures the final product not only meets but exceeds client expectations.
Furthermore, global clients benefit from flexible production runs and rapid prototyping, helping them iterate designs quickly. This agility in customization supports innovation and reduces time-to-market, a critical factor in competitive industries. Trusted Chinese CNC manufacturers combine technological expertise with a customer-centric mindset, providing detailed consultation and ongoing communication to refine specifications and achieve perfect results.
In essence, precision CNC machining for global high-end clients hinges on the ability to provide bespoke solutions that harmonize technological prowess with attentive service. This customized approach guarantees that complex, high-value components are delivered with superior quality, tight tolerances, and reliable consistency, reinforcing trust and long-term partnerships across industries.
---
## Custom CNC Manufacturing Based on Detailed Technical Drawings
At the core of high-precision CNC machining lies the meticulous interpretation and implementation of detailed technical drawings. For overseas clients, these blueprints are the foundation for manufacturing complex parts with exacting standards. Chinese CNC service providers excel at translating intricate design details into precise manufacturing processes, ensuring every dimension, hole, and surface finish adheres strictly to specifications.
The process begins with thorough review and verification of client drawings, often involving close communication to clarify tolerances, material requirements, and surface treatments. Advanced CAD/CAM systems generate highly accurate tool paths, minimizing errors and optimizing machining efficiency. Skilled engineers analyze the drawings to identify potential challenges, such as tight tolerances, micro-features, or complex geometries, and develop strategies to address them effectively.
Once the manufacturing plan is established, the production phase emphasizes quality control. High-precision measurement tools, like coordinate measuring machines (CMM), are employed to verify parts against the original drawings at multiple stages. This rigorous validation ensures conformity and allows for immediate correction if deviations are detected. Such strict adherence to technical drawings guarantees that every component fulfills critical performance criteria, particularly in demanding sectors like aerospace or medical devices.
Custom CNC manufacturing based on detailed drawings also involves choosing appropriate machining parameters—cutting speeds, feeds, tooling—to optimize precision while preventing deformation or damage. Furthermore, manufacturers often incorporate finishing processes like polishing, anodizing, or coating to enhance surface quality and durability, all aligned with client specifications.
Overall, the ability to faithfully reproduce complex designs from detailed drawings showcases the expertise of Chinese CNC machining providers. This meticulous approach ensures clients worldwide receive parts that meet the highest standards of accuracy, functionality, and aesthetic quality.
---
## Overcoming High-Difficulty Machining Challenges with Expert Skills
Manufacturing high-precision parts often involves tackling formidable machining challenges, such as machining ultra-hard materials, micro-features, or parts with tight tolerances. Chinese CNC experts excel in overcoming these difficulties through years of experience and innovative techniques. Their proficiency enables them to push the limits of what is technically achievable, ensuring clients’ complex requirements are met without compromise.
One common challenge is machining difficult materials like titanium, stainless steel, or ceramic composites. These materials demand specialized cutting tools, precise control of cutting parameters, and advanced cooling techniques to prevent tool wear and deformation. Expert operators know how to select the right tooling and optimize machining conditions to achieve clean, accurate cuts on tough substrates. They also utilize high-speed spindle technology and rigid fixturing to minimize vibrations that could jeopardize accuracy.
Another significant hurdle is manufacturing micro-scale features or intricate geometries, which require exceptional stability and precision. Expert CNC machinists employ multi-axis machines, high-precision collets, and laser measurement systems to maintain tight tolerances during complex operations. They often develop custom fixtures or jigs to securely hold parts, preventing movement or distortion during machining.
High-difficulty machining also involves managing thermal expansion and residual stresses that can distort parts. Skilled engineers implement strategies such as controlled cooling, slow feed rates, and process monitoring to mitigate these effects. By combining technological innovation with their deep understanding of material behaviors, Chinese CNC manufacturers consistently deliver high-quality, high-precision components even in the most challenging scenarios.
Additionally, addressing geometric complexities like sharp internal corners or delicate micro-holes requires specialized end mills and advanced toolpaths. Overcoming these challenges depends heavily on the expertise of the machinists and engineers to select appropriate techniques, ensuring the final parts meet the exacting standards demanded by global clients.
In summary, expert CNC skills in overcoming high-difficulty machining challenges are fundamental to delivering complex, high-precision components. Their ability to innovate and adapt ensures that even the most demanding specifications are successfully realized, solidifying their role as trusted partners for international high-end markets.
---
## Material Selection Expertise for Complex CNC Machining Projects
Material selection is a critical factor influencing the success of high-precision CNC machining projects. Chinese manufacturers with extensive experience understand the unique properties of various materials, allowing them to choose the best options for each application. From metals like titanium, aluminum, and stainless steel to advanced composites and ceramics, material expertise ensures optimal machinability, performance, and longevity.
For high-end applications, material properties such as hardness, thermal stability, corrosion resistance, and biocompatibility must align with project requirements. Expert manufacturers analyze these factors in relation to machining processes to recommend suitable materials that balance performance with manufacturability. For instance, titanium—known for its strength-to-weight ratio and corrosion resistance—is frequently used in aerospace and medical implants but requires specialized machining techniques due to its low thermal conductivity and tendency to work-harden.
Advanced composites, like carbon fiber reinforced plastics, offer lightweight and high-strength options but pose unique challenges such as fiber pull-out and delamination during machining. Skilled CNC providers develop tailored strategies, including specific cutting tools and parameters, to handle these materials effectively without compromising structural integrity.
Ceramic materials, with their high hardness and temperature resistance, demand ultra-precise tool selection and slow, controlled machining processes. Expert material knowledge allows for the development of specialized tooling and process adjustments, ensuring high-quality finishes and dimensional accuracy.
Furthermore, material compatibility with surface treatments and coatings is considered during planning. For example, certain metals respond better to anodizing or PVD coatings, enhancing corrosion resistance or aesthetic appeal. The right material selection ultimately impacts the performance, cost, and manufacturability of the final component.
In conclusion, material expertise is fundamental for achieving high precision and success in complex CNC projects. Chinese manufacturers leverage their deep understanding of material behaviors to deliver parts that meet strict industry standards and client expectations, even under challenging conditions.

Manufacturer of customized worm gears and worm shafts according to drawings
## The Importance of Extensive Machining Experience in High-Precision Tasks
Experience is a vital component in high-precision CNC machining, particularly when dealing with complex geometries, tight tolerances, and demanding materials. Chinese CNC manufacturing companies pride themselves on decades of accumulated expertise, which translates into better problem-solving capabilities and refined processes. This extensive experience is what allows them to consistently deliver high-quality, precise components for global clients.
Veteran CNC machinists possess a deep understanding of machine capabilities, tooling behavior, and material responses. They can anticipate potential issues such as tool wear, thermal distortion, or defect formation and implement preventative measures proactively. Their familiarity with various machining strategies enables them to optimize processes for efficiency and accuracy, reducing waste and cycle times.
Furthermore, experienced operators are adept at interpreting complex technical drawings, identifying challenging features, and devising innovative fixturing or machining techniques to address them. They understand how small deviations can cascade into larger defects and are skilled at implementing quality control measures to catch issues early. This proactive approach minimizes errors and ensures compliance with strict tolerances.
In high-precision manufacturing, the ability to troubleshoot and adapt on the fly is invaluable. Seasoned professionals can adjust machining parameters in real-time to accommodate unexpected phenomena, ensuring consistent output even in complex or unconventional projects. Their expertise also extends to selecting the right tools, coatings, and finishing techniques suited to each specific task.
The cumulative knowledge gained from numerous projects provides a rich repository of solutions for common and uncommon machining challenges. This experience-driven approach fosters continuous improvement, innovation, and confidence among clients who rely on the manufacturer’s capability to handle their most sensitive and complex components.
Ultimately, extensive machining experience underpins the reliability, accuracy, and repeatability essential in high-precision industries. Chinese manufacturers leverage this wealth of expertise to establish themselves as trusted partners for clients worldwide seeking top-tier CNC machining services.
---
## Case Study: Solving Complex Geometries in Global CNC Projects
One of the most compelling demonstrations of high-precision CNC expertise involves tackling complex geometries that challenge conventional manufacturing methods. For instance, a global aerospace client required a turbine blade component with intricate cooling channels, micro-holes, and ultra-tight tolerances. The Chinese CNC manufacturer employed a multifaceted approach to succeed where standard processes might have failed.
First, they conducted an in-depth analysis of the design, identifying features that could cause issues such as tool deflection or surface imperfections. Custom fixtures were designed to securely hold the workpiece, minimizing vibrations during high-precision milling. Multi-axis CNC machines, including 5-axis and 6-axis configurations, enabled complex toolpaths that accessed difficult angles and internal features without compromising precision.
Advanced micro-drilling techniques were utilized to create micro-holes with consistent diameter and smooth finishes, essential for cooling performance. The use of high-precision measurement equipment like CMMs ensured that each feature adhered to exact dimensions, with real-time feedback guiding process adjustments.
Throughout the process, engineers carefully selected cutting tools and optimized parameters to prevent material work-hardening and thermal distortion. Surface finishing was achieved through specialized polishing and coating techniques that improved performance while maintaining the complex geometry.
Post-production inspection revealed parts that met or exceeded all specifications, including a micron-level tolerance on critical features. The success of this project underscored how extensive experience, technological sophistication, and innovative problem-solving coalesce to overcome challenging geometries in high-precision manufacturing.
Such case studies serve as testament to the capability of Chinese CNC manufacturers to deliver tailored solutions for the most demanding global clients, reinforcing their reputation as industry leaders.
---
## Advanced Techniques for Machining Tough and Specialized Materials
Machining tough or specialized materials requires advanced techniques beyond conventional methods. Chinese CNC manufacturers employ innovative approaches such as cryogenic machining, ultrasonic-assisted machining, and laser-assisted processes to handle materials like titanium alloys, Inconel, ceramics, and composites efficiently.
Cryogenic machining involves cooling the cutting zone with liquid nitrogen, reducing heat generation and preventing tool wear on difficult-to-machine metals. Ultrasonic-assisted machining leverages high-frequency vibrations to facilitate chip removal and reduce cutting forces, enabling precise processing of brittle materials like ceramics or hardened steels.
Laser-assisted machining introduces a laser pre-heating step to soften tough materials before cutting, reducing tool wear and improving surface finish. These techniques extend the machinability of challenging materials, enabling complex geometries and tight tolerances that would be impossible with traditional methods.
Furthermore, the integration of high-speed spindles, specialized tool coatings, and advanced coolant delivery systems enhances machining performance. The use of high-precision, multi-axis CNC systems allows for complex, multi-faceted operations on tough materials without sacrificing accuracy.
The expertise gained through years of applying these advanced techniques ensures that high-value parts are produced efficiently, with minimal defects, and in accordance with stringent industry standards. Chinese manufacturers continually innovate and adopt new technologies to maintain their competitive edge in serving global clients with specialized material requirements.
---
## Ensuring Quality and Accuracy in High-Precision CNC Parts Production
Quality assurance in high-precision CNC machining is paramount, especially when manufacturing components for critical applications. Chinese CNC companies prioritize rigorous quality control protocols, employing a combination of in-process inspections, final testing, and advanced measurement technologies.
During production, parts undergo multiple checks using coordinate measuring machines (CMMs), laser scanners, and optical comparators to verify dimensions, surface integrity, and geometric tolerances. Statistical process control (SPC) methods are implemented to monitor and optimize machining parameters continuously, reducing variability and ensuring consistency across batches.
Surface quality and finish are critical in many high-precision parts, necessitating meticulous polishing, coating, and non-destructive testing processes. These steps confirm that parts meet not only dimensional requirements but also functional and aesthetic standards.
Furthermore, compliance with international certifications such as ISO 9001, AS9100, and TS16949 underscores a manufacturer’s commitment to maintaining high quality standards. Traceability of raw materials, process documentation, and thorough inspection records provide transparency and confidence to global clients.
The implementation of quality management systems, coupled with investment in advanced metrology equipment, ensures that every part leaving the production line conforms to strict tolerances. This unwavering focus on quality and accuracy is what makes Chinese CNC machining a trusted partner for clients demanding high-end, reliable components.
---
## How Experienced CNC Machining Engineers Tackle Difficult Tolerance Requirements
Meeting tight tolerances is one of the most challenging aspects of high-precision CNC machining. Experienced engineers in Chinese manufacturing firms approach this by combining meticulous planning, precise tool control, and continuous monitoring. Their goal is to consistently achieve tolerances within micrometers, even on complex geometries.
Engineers start by selecting appropriate cutting tools with high stability and minimal deflection. They optimize machining parameters such as feed rate, spindle speed, and cutting depth to minimize dimensional deviations. The use of high-precision fixtures and environmental controls further stabilizes the process, reducing thermal expansion or vibrations that could compromise accuracy.
Real-time measurement systems, including inline laser scanners and touch probes, are employed during machining to detect deviations early. Adjustments are made proactively to correct any drift, ensuring parts stay within specified tolerances. For ultra-tight requirements, multi-stage machining processes are used—roughing followed by fine finishing—to incrementally refine dimensions.
In addition, extensive experience allows engineers to anticipate potential issues such as tool wear, material deformation, or residual stresses, and implement strategies like slow feed rates or cooling solutions. This proactive approach minimizes the risk of rework or scrap, saving time and costs.
Through their expertise, these engineers uphold the highest standards of precision, enabling the production of components that meet the most demanding tolerance specifications across industries worldwide.
---
## Addressing Common Global CNC Machining Challenges with Innovative Solutions
Global clients often face challenges such as material limitations, complex geometries, and strict tolerances. Chinese CNC manufacturers respond with innovative solutions tailored to these issues. For instance, they develop custom tooling and fixtures for micro-machining or delicate features, overcoming geometrical constraints.
They also leverage multi-axis machining and advanced CAM programming to access hard-to-reach areas, reducing the need for multiple setups and improving accuracy. For tough materials, adopting specialized cutting tools and cooling methods extends tool life and enhances surface quality.
In terms of communication, manufacturers employ digital collaboration platforms, virtual prototyping, and 3D simulations to ensure clear understanding of complex designs. This reduces errors and accelerates project timelines. When facing tight tolerances, they implement rigorous process control and continuous feedback loops to maintain precision.
Furthermore, they invest in cutting-edge inspection technology and quality management systems to detect defects early, preventing costly rework. Their ability to innovate and adapt ensures that common industry challenges are effectively addressed, fostering confidence among international clients.
By continuously refining processes and embracing technological advancements, Chinese CNC machining companies turn challenges into opportunities, delivering reliable, high-quality components on time and within budget.
---
## Custom CNC Processes for Unique Client Specifications Worldwide
Every client has unique requirements that demand custom CNC processes. Chinese manufacturers excel at developing tailored solutions, from specialized machining sequences to unique surface treatments. This flexibility allows them to meet diverse industry standards and functional needs.
For example, clients in aerospace may require parts with ultra-smooth finishes, specific coatings, and strict weight tolerances, while medical device manufacturers need biocompatible materials and micro-machined features. The ability to customize the entire process—from material selection to post-processing—ensures comprehensive satisfaction.
Manufacturers often create custom tooling, fixtures, and process parameters to optimize production for each project. They also incorporate advanced finishing techniques like PVD coatings, anodizing, or laser marking, aligning with client branding and performance requirements.
Moreover, they adapt their logistics and packaging solutions to ensure safe, timely delivery across borders. Their global experience enables them to understand and navigate various regulatory standards, quality expectations, and environmental considerations.
This commitment to customization fosters long-term partnerships, as clients can rely on manufacturers to deliver complex, high-precision parts tailored precisely to their specifications. Ultimately, bespoke CNC processes are the backbone of serving a diverse international clientele with unique project demands.
---
## Building Trust Through Proven Expertise in High-Precision CNC Manufacturing
Trust is the foundation of successful international business relationships. Chinese CNC manufacturers build this trust through a proven track record of delivering high-precision, complex components consistently and reliably. Their extensive experience, technological investment, and commitment to quality set them apart.
Clients worldwide recognize the importance of transparency, communication, and adherence to deadlines. Manufacturers achieve this by providing detailed process documentation, certificates of conformity, and comprehensive after-sales support. They also foster long-term collaborations by continuously improving their capabilities and incorporating client feedback.
Case studies demonstrating successful handling of challenging projects—such as complex geometries, tight tolerances, or difficult materials—serve as testament to their expertise. Certifications like ISO 9001 and industry-specific standards further reinforce credibility.
Moreover, they prioritize confidentiality and intellectual property protection, ensuring clients’ designs and innovations remain secure. This integrity, combined with competitive pricing and flexible service options, consolidates trust and encourages ongoing partnerships.
In essence, Chinese CNC machining companies leverage their expertise, technological prowess, and customer-centric approach to establish themselves as trusted global suppliers. Their reputation for high-quality, reliable manufacturing drives confidence among international clients seeking precision components for critical applications.
---
###
High-precision CNC machining has become an indispensable part of modern manufacturing, especially for global clients demanding the highest standards. Chinese CNC manufacturers, with their extensive experience, advanced technology, and a deep understanding of materials and complex geometries, stand out as trusted partners. Their ability to customize processes, tackle difficult challenges, and ensure consistent quality makes them integral to industries such as aerospace, medical, and electronics worldwide. As the industry continues to evolve, these expert manufacturers will remain at the forefront, delivering innovative, precise, and reliable solutions that meet the demanding needs of clients around the globe.