High-Precision CNC Machining for Global Clients Custom Parts and Challenges
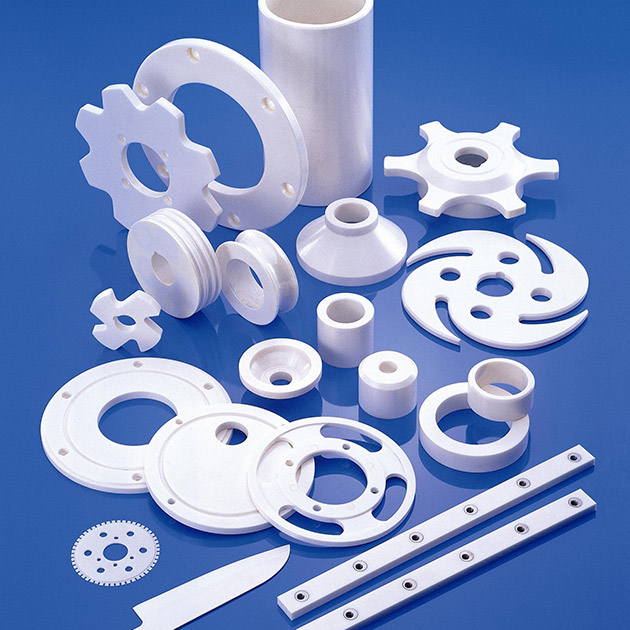
# High-Precision CNC Machining for Global Clients: Custom Parts and Challenges
===INTRO:===
In today’s globalized manufacturing landscape, high-precision CNC machining has become an essential service for industries demanding intricate, reliable, and custom-engineered parts. From aerospace to medical devices, the need for precision, material versatility, and sophisticated processing techniques has driven manufacturers worldwide to push the boundaries of CNC technology. Chinese CNC machining companies, known for their expertise in custom part production with complex geometries and tough materials, are increasingly vital players on the international stage. Their ability to interpret detailed drawings, handle high-difficulty components, and meet strict tolerances underscores their importance in global supply chains. This article explores the core aspects of high-precision CNC machining for international clients, addressing the challenges, solutions, and future trends shaping this dynamic industry.
---
## Understanding the Importance of Custom Parts in High-Precision CNC Machining
Custom parts are the backbone of modern engineering, enabling tailored solutions that meet specific application requirements. In high-precision CNC machining, custom parts are not simply off-the-shelf components; they are meticulously designed and manufactured to exact specifications. This level of customization allows for enhanced performance, weight reduction, and integration of complex functionalities that standard parts cannot offer. For global clients, especially those in high-tech industries, the ability to produce custom parts ensures their products stay competitive and innovative.
Precision in custom CNC machining also minimizes assembly issues, reduces the need for modifications, and enhances overall product reliability. The process begins with detailed CAD models and technical drawings, which are then interpreted meticulously by experienced machinists and advanced CNC equipment. The significance of customizing parts lies in its contribution to product differentiation, enabling companies worldwide to develop unique solutions that align precisely with their design intents. Moreover, custom parts often require tight tolerances — sometimes within microns — highlighting the need for advanced machining capabilities and skilled craftsmanship.
Custom CNC machining also offers scalability and flexibility. As clients’ needs evolve, so too can the manufacturing processes, allowing for rapid prototyping, small batch production, or large-volume manufacturing without compromising quality. This adaptability is critical for industries like aerospace, medical implants, and electronics, where innovation cycles are rapid. In essence, custom parts manufactured via high-precision CNC machining serve as the foundation for technological advancements, fostering innovation across the globe.
Furthermore, the importance of custom parts extends to reducing overall project costs in the long run. Although initial setup and machining might be complex and costly, the precise fit and function of custom parts reduce assembly errors, warranty issues, and the need for rework. This is particularly vital when manufacturing high-stakes components that demand unwavering quality standards. For international clients, partnering with experienced CNC machinists capable of interpreting complex designs and delivering precision parts is a strategic move toward achieving competitive advantages in their respective markets.
The significance also lies in the ability to incorporate advanced materials into custom parts. As industries push for lighter, stronger, and more durable components, CNC machining offers the versatility needed to work with a broad array of materials such as titanium, aluminum, stainless steel, ceramics, and composites. Precision machining ensures that even the most challenging materials are processed accurately, maintaining their integrity and functionality. Overall, custom CNC parts are central to advancing technological innovation and operational excellence on a global scale.
Lastly, high-precision customized parts enable the integration of complex geometries and intricate internal structures that would be impossible with traditional manufacturing methods. This capability opens new frontiers for design creativity and functional performance, giving industries the tools to develop smarter, more efficient products. As global markets demand increasingly sophisticated solutions, the role of custom parts in high-precision CNC machining becomes ever more critical. It empowers manufacturers to meet demanding specifications while maintaining cost-effectiveness and efficiency.
---
## Key Materials Used in Advanced CNC Processing for Diverse Industries
The selection of materials is fundamental to the success of high-precision CNC machining, especially when manufacturing complex custom parts for diverse industries. Each industry’s specific requirements dictate the choice of materials, balancing factors such as strength, weight, corrosion resistance, thermal stability, and machinability. Chinese CNC manufacturers leverage a comprehensive range of materials to meet these varied needs, ensuring precision and durability in every component.
Aluminum alloys are among the most popular materials due to their excellent machinability, lightweight properties, and versatility. They are widely used in aerospace, automotive, and consumer electronics, where reducing weight without sacrificing strength is vital. For example, aerospace components made from high-grade aluminum alloys undergo meticulous CNC processing to achieve tight tolerances and complex geometries. Their ease of machining allows for efficient production of customized parts with intricate features.
Stainless steel is another critical material owing to its corrosion resistance, strength, and hygienic properties. Industries such as medical devices, food processing, and marine applications depend on stainless steel for their durability and biocompatibility. High-precision CNC machining ensures that stainless steel components meet strict standards for surface finish, dimensional accuracy, and internal features, which are essential in high-performance and safety-critical applications.
Titanium and its alloys have gained prominence in aerospace, medical implants, and high-performance engineering due to their exceptional strength-to-weight ratio, corrosion resistance, and biocompatibility. Machining titanium is challenging because of its hardness and tendency to work-harden, but advanced CNC techniques and skilled operators enable the production of precise, complex parts that meet stringent specifications.
Ceramics and composite materials are also increasingly used for specialized applications requiring high thermal stability and wear resistance. These materials are difficult to machine but are critical in electronics, aerospace, and cutting-edge medical applications. CNC processing of such materials demands not only sophisticated tools but also deep material knowledge to avoid cracking or deformation.
Polymer materials, including PEEK, acetal, and other engineering plastics, are essential in industries requiring lightweight, chemical-resistant, and electrically insulating components. CNC machining of plastics offers rapid turnaround and high precision, making them suitable for prototypes and small batch productions.
In terms of process, the choice of cutting tools, cooling methods, and machining parameters varies depending on the material. For example, hardened steels require different tooling and cooling techniques compared to softer aluminum alloys. Chinese CNC manufacturers adept at working with diverse materials adapt their technology and processes accordingly to maximize precision and surface quality.
Material quality and consistency are critical for achieving tight tolerances and ensuring long-term performance of high-precision parts. Suppliers often provide certified materials with specific mechanical properties, assuring clients of the reliability of their components. This rigorous material selection and processing capability are vital for meeting the exacting standards of industries such as aerospace and medical devices.
Overall, the ability to process a wide range of advanced materials enables Chinese CNC manufacturers to serve international clients across multiple sectors, delivering custom parts that meet precise specifications, withstand demanding environments, and push technological boundaries.
---
## Challenges in Machining High-Complexity Parts: Common Difficulties Explored
Manufacturing high-complexity parts through CNC machining presents numerous technical challenges that require expertise, advanced technology, and meticulous planning. These challenges are amplified when the parts involve intricate geometries, tight tolerances, and difficult-to-machine materials. Understanding these difficulties is crucial for both manufacturers and clients to achieve successful outcomes.
One common challenge is achieving the required precision and tight tolerances. Complex parts often have multiple features, internal channels, and minute details that must align perfectly. Variations in machining, tool wear, or thermal expansion can compromise the accuracy, necessitating careful control of machining parameters and continual calibration of equipment.
Another significant difficulty is handling difficult-to-machine materials like titanium, hardened steels, ceramics, or composites. These materials tend to work-harden, cause excessive tool wear, or are prone to cracking and deformation. CNC operators and engineers must select appropriate tooling, cutting speeds, and cooling techniques to mitigate these issues while maintaining surface quality.
Internal features such as deep cavities, blind holes, or complex internal channels pose additional challenges. Accessing these areas without damaging surrounding features requires specialized tools, multi-axis machining, or advanced fixturing methods. Ensuring consistent quality in internal geometries often involves the use of precise simulation software and meticulous process planning.
Surface finish quality is also a critical challenge, especially for functional or aesthetic parts. Achieving a smooth, defect-free surface on complex geometries may require multiple finishing passes, specialized abrasives, or post-processing techniques. Maintaining surface integrity without compromising dimensional accuracy demands experienced craftsmanship and process control.
Managing residual stresses and deformation during machining is a common concern, particularly in thin-walled or delicate components. Excessive cutting forces or thermal effects can cause warping or distortion, which must be countered through optimized machining strategies and clamping methods.
The complexity of fixturing and part setup can also significantly impact manufacturing efficiency and quality. Securing intricate parts without damaging sensitive features requires customized fixtures, precise alignment, and careful handling, often increasing setup times and costs.
Furthermore, software limitations and programming errors can lead to machining inaccuracies or tool collisions, especially with complex geometries. This underscores the importance of sophisticated CAD/CAM systems and thorough simulation to anticipate and resolve potential issues beforehand.
Lastly, the balance between processing time and quality becomes a challenge with complex parts. Longer machining cycles, increased tool changes, and additional finishing steps are often necessary to meet specifications, demanding careful scheduling and resource management.
Overcoming these challenges requires a combination of advanced technology, skilled personnel, rigorous quality control, and innovative problem-solving. Chinese CNC manufacturers with extensive experience and cutting-edge equipment are well-positioned to address these difficulties, ensuring that even the most complex parts meet international standards.
---
## How Experienced CNC Manufacturers Tackle Precision and Material Challenges
Experience in high-precision CNC machining plays a pivotal role in overcoming the inherent challenges of producing complex, custom parts. Manufacturers with extensive track records and a deep understanding of machining intricacies develop effective strategies to ensure accuracy, surface quality, and material integrity across diverse projects.
One key approach is meticulous process planning. Experienced manufacturers conduct comprehensive analyses of the CAD drawings, material properties, and functional requirements before machining begins. They optimize tool paths, cutting parameters, and fixture designs to minimize errors, reduce machining time, and extend tool life. This proactive planning is crucial when working with difficult materials like titanium or ceramics, which require specific procedures to prevent damage.
Skilled operators and engineers are indispensable in high-precision CNC machining. Their expertise allows for real-time adjustments based on tool wear, temperature fluctuations, and unexpected issues. They can recognize early signs of problems, such as vibration or overheating, and adapt machining strategies accordingly, maintaining tight tolerances and surface finishes.
Advanced equipment is another cornerstone of successful high-precision machining. Manufacturers invest in multi-axis CNC machines, high-precision spindles, and automated tool changers. These capabilities enable complex geometries, internal features, and tight tolerances to be achieved consistently. Moreover, integrated measurement systems and inline inspection tools facilitate real-time quality control, catching deviations early and reducing waste.
Material handling and preparation also benefit from experienced knowledge. For instance, understanding how to work with specific alloys or ceramics—considering their thermal and mechanical behaviors—allows for selecting appropriate tooling, cooling methods, and cutting speeds. Proper fixturing techniques are employed to prevent deformation and ensure stability throughout the process.
Quality assurance is embedded at every stage in seasoned CNC manufacturing facilities. They implement rigorous inspection protocols, including coordinate measuring machines (CMM), optical comparators, and surface analyzers. These tools verify dimensions, tolerances, and surface finishes, ensuring that every part meets customer specifications.
Furthermore, experienced manufacturers foster continuous improvement through feedback loops. Data collected during machining, such as tool wear patterns and process deviations, inform maintenance schedules and process adjustments. This iterative learning enhances process stability, repeatability, and overall quality.
Training and workforce development are also integral. Skilled machinists and programmers deeply understand the nuances of high-precision work, enabling them to troubleshoot complex issues quickly. They stay abreast of technological advancements, integrating new tools, materials, and methodologies into their workflows.
Finally, collaboration with clients is emphasized to clarify design intent, material expectations, and application conditions. This transparency helps in preemptively addressing potential challenges, ensuring that the final product aligns perfectly with the intended specifications. Through these comprehensive measures, experienced CNC manufacturers effectively tackle the challenges of high-precision machining and deliver reliable, high-quality custom components.
---
## Case Studies: Solving Global CNC Machining Difficulties with Innovative Solutions
Real-world examples underscore the importance of technical ingenuity, experience, and advanced technology in overcoming complex CNC machining challenges. Chinese manufacturers, with their extensive expertise, have successfully delivered solutions for some of the most demanding projects globally, setting benchmarks in high-precision manufacturing.
One notable case involved the production of titanium aerospace components requiring intricate internal channels and tight tolerances. The challenge lay in machining a hard material prone to work-hardening and deformation. The solution employed multi-axis CNC machines with specialized ceramic tools and cryogenic cooling. This approach minimized thermal effects and prolongs tool life, enabling the production of parts that met strict aerospace standards with high surface quality and dimensional accuracy.
Another example focused on medical implants made from stainless steel. The parts featured complex geometries, internal cavities, and precision surface finishes. To address internal accessibility issues, the manufacturer adopted advanced 5-axis machining combined with custom fixturing that securely held delicate components without deformation. Post-machining surface treatments further enhanced biocompatibility and surface smoothness, ensuring compliance with international medical standards.
A different challenge involved processing ceramic components used in electronics. Ceramics are brittle and prone to cracking during machining. The solution involved the use of diamond-coated tools and optimized cutting parameters to reduce stresses. Additionally, ultrasonic vibration-assisted machining was introduced to facilitate material removal without inducing fractures, resulting in high-precision parts with excellent surface properties.
In a high-precision optical device application, the requirement was for ultra-fine features on aluminum alloys. The manufacturing team integrated laser micromachining with CNC milling, achieving features with micron-level accuracy. This hybrid approach demonstrated how combining technologies can resolve complex geometrical demands that are difficult for traditional CNC alone.
For small batch production of customized prototypes, a manufacturer used rapid tooling and flexible CNC setups to minimize lead times and costs. They employed modular fixturing systems and real-time inspection to ensure each part adhered to tight tolerances, exemplifying adaptability in the face of diverse client needs.
Some projects tackled material limitations by developing specialized coating and cooling techniques to extend tool life and reduce thermal distortion. For instance, using cryogenic cooling with nitrogen gas significantly improved machining performance with titanium, ensuring consistent quality over multiple production runs.
These case studies highlight that innovative approaches—whether through advanced tooling, process integration, or material handling—are vital to solving global CNC machining difficulties. They demonstrate how experienced manufacturers leverage technology and expertise to turn challenging projects into successful, high-quality outcomes, reinforcing the critical role of continuous innovation in precision manufacturing.
---
## The Role of Accurate Design Interpretation in Custom CNC Manufacturing
Precise interpretation of design data is fundamental to achieving the desired quality and functionality in high-precision CNC machining. For global clients providing detailed drawings and specifications, accurately translating these into workable manufacturing instructions is essential. Any misinterpretation can lead to errors, increased costs, and delays—issues that are detrimental in high-stakes industries.
First, comprehensive review of CAD models and technical drawings is crucial. Experienced CNC manufacturers analyze every detail, including dimensions, tolerances, surface finishes, and material specifications. They identify potential ambiguities or conflicts in the design, seeking clarification from clients when necessary. This proactive approach helps prevent misunderstandings and ensures alignment between design intent and manufacturing reality.
Advanced software tools play a vital role in this process. CAM (Computer-Aided Manufacturing) systems generate precise tool paths based on the digital models, but require careful input and calibration. Skilled programmers review and validate these programs to ensure they accurately reflect the design, accounting for factors like tool behavior, machine capabilities, and material properties.
Material considerations also influence design interpretation. Certain features may need adjustments or specific machining strategies depending on the chosen material’s machinability and physical characteristics. For example, thin walls or fragile internal features in ceramics or titanium require modifications in approach to prevent damage during processing.
Communication with clients is integral to accurate design translation. Manufacturers often collaborate closely with designers or engineers to understand functional requirements, tolerances, and critical features. This dialogue facilitates a mutual understanding, reducing the risk of errors and enabling tailored machining solutions that meet or exceed expectations.
Quality control measures are implemented at every stage to verify that the manufactured parts align with the original design. Coordinate measuring machines (CMMs), optical inspections, and surface analyzers are used to detect deviations early. If discrepancies are found, feedback loops enable prompt adjustments, maintaining high precision standards.
Training and expertise are paramount in interpreting complex designs. Skilled engineers and technicians possess deep knowledge of manufacturing processes, materials, and tolerance stack-up. Their experience allows them to foresee manufacturing challenges and devise pragmatic solutions that uphold design integrity.
Lastly, documentation and traceability ensure that every step from design to production is well-recorded. This practice not only facilitates quality assurance but also aids in future troubleshooting or modifications. Accurate design interpretation remains a cornerstone of successful high-precision CNC manufacturing, especially when serving demanding international clients with complex specifications.
---
## Overcoming Material Limitations in High-Precision CNC Components
Working with challenging materials like titanium, ceramics, or hardened steels requires specialized techniques and expertise to overcome inherent limitations. These materials often pose difficulties such as brittleness, work-hardening, or thermal sensitivity, which can hinder achieving desired tolerances and surface finishes in high-precision CNC machining.
One effective strategy involves selecting appropriate tooling and cutting parameters. For example, using diamond-coated or ceramic tools can facilitate machining of ceramics and hardened steels, reducing tool wear and preventing cracking. Adjusting cutting speeds, feeds, and cooling methods helps mitigate thermal stresses and deformation, ensuring stable machining conditions.
Advanced cooling techniques, such as cryogenic or Minimum Quantity Lubrication (MQL), are also employed to manage heat generation during machining. Cryogenic cooling, typically with liquid nitrogen, significantly lowers temperatures at the cutting zone, preventing work-hardening and reducing residual stresses—crucial factors when working with difficult materials like titanium or ceramics.
Material pre-treatment and conditioning can further improve machinability. For instance, heat treatments or alloy modifications can alter material properties to favor machining. For ceramics, pre-sintering or grinding processes may enhance toughness or reduce brittleness before final CNC processing.
Multi-stage machining processes are often adopted to address material limitations. Initial roughing removes bulk material with aggressive parameters, followed by finishing passes with delicate tooling and slower speeds. This approach minimizes stress and deformation, resulting in high-precision components with superior surface quality.
Finite Element Analysis (FEA) and simulation software help predict potential issues such as deformation or cracking before actual machining. These insights enable engineers to optimize tool paths, machining strategies, and fixture designs, reducing trial-and-error and improving success rates.
Post-processing treatments, like polishing, surface coatings, and heat treatments, are applied to enhance the surface integrity and performance of parts made from challenging materials. These processes can improve wear resistance, corrosion protection, and dimensional stability, extending the lifespan of high-precision components.
Collaboration with material suppliers ensures consistent raw material quality and provides insights into specific processing nuances. Certified materials with defined mechanical and thermal properties enable predictable machining outcomes and compliance with international standards.
Finally, continuous research and technological innovation keep manufacturers at the forefront of overcoming material limitations. Incorporating robotic automation, ultrasonic machining, or laser assistance allows for more precise and efficient processing of difficult materials. By mastering material challenges, Chinese CNC manufacturers can reliably produce high-precision parts that meet the demanding standards of global industries.
---

Supplier of customized ceramic parts according to drawings
## Critical Factors in Ensuring Quality and Tolerance in Complex Parts
Maintaining high quality and strict tolerances in complex CNC machined parts hinges on several critical factors. Each element, from initial design to final inspection, must be meticulously managed to ensure the finished component performs as intended in demanding applications.
First, precise design interpretation is fundamental. Clear, detailed drawings and CAD models—paired with thorough review and communication—set the foundation for accurate manufacturing. Understanding the critical dimensions, functional features, and allowable tolerances guides every machining step.
Advanced machine capability and stability are equally important. High-precision multi-axis CNC machines equipped with linear scales and environmental controls ensure consistent, repeatable results. Regular calibration and maintenance prevent drift and inaccuracies, especially when producing parts with tight tolerances.
Tool selection and management greatly influence quality. Using high-quality, sharp cutting tools suited for specific materials reduces defects and surface imperfections. Proper tool life management, including timely replacements and toolpath optimization, minimizes errors due to tool wear.
Process control and parameter optimization are vital. Carefully selecting cutting speeds, feeds, and cooling methods reduces residual stresses, deformation, and surface roughness. Monitoring machining conditions in real-time allows for adjustments that uphold tight tolerances throughout production.
Inspection and measurement are integral to quality assurance. Employing CMMs, laser scanners, and optical comparators verifies dimensional accuracy and surface quality post-machining. Establishing control plans with defined inspection points ensures compliance with specifications before shipping.
Environmental controls within manufacturing facilities—such as temperature, humidity, and vibration damping—help maintain machine stability and part accuracy. For sensitive components, such controls prevent material expansion or contraction that could compromise tolerances.
Operator expertise and training are crucial. Skilled technicians interpret inspection data, troubleshoot issues, and make real-time adjustments. Their experience ensures that complex geometries are machined correctly and consistently.
Documentation and traceability support continuous quality improvement. Recording process parameters, inspection results, and corrective actions creates a feedback loop that enhances future production runs and maintains standards.
Finally, fostering a quality-centric culture and continuous improvement mindset ensures that every team member prioritizes precision, accuracy, and reliability. Combining advanced technology, skilled personnel, and rigorous procedures enables Chinese CNC manufacturers to consistently deliver complex parts with impeccable quality and tight tolerances.
---
## Strategies for Managing Tight Tolerances in Custom CNC Machining Projects
Successfully managing tight tolerances in custom CNC machining requires strategic planning, sophisticated technology, and rigorous quality control. These strategies help ensure that complex parts meet exact specifications, critical for high-performance applications across industries.
The first step is comprehensive design analysis. Collaborating closely with clients to understand functional requirements and tolerances allows manufacturers to identify potential manufacturing challenges early. Optimization of the design, including features that facilitate easier machining, can reduce complexity and improve tolerances.
Employing multi-axis machining centers enhances flexibility and precision. 5-axis or higher machines enable access to difficult geometries, reduce setup times, and improve positional accuracy, all of which are essential for tight tolerance control.
Choosing appropriate tooling is crucial. High-quality, precision-ground tools with consistent geometry reduce the risk of deviation. Additionally, implementing tool wear monitoring and proactive replacements prevent dimensional inaccuracies caused by dull or damaged tools.
Process parameter optimization involves selecting cutting speeds, feeds, and coolant strategies tailored to each material and feature. Variable parameters can be adjusted dynamically based on real-time feedback, ensuring consistent precision throughout the production cycle.
Environmental control within manufacturing facilities maintains ambient conditions such as temperature and humidity, minimizing thermal expansion or contraction that could impact dimensions. Vibration damping and isolation techniques further stabilize machine performance.
In-process measurement and monitoring are vital. Integrating CNC machines with probing systems or inline inspection devices allows for immediate detection of deviations. Automated feedback mechanisms facilitate real-time adjustments, preserving tight tolerances during long or complex runs.
Implementing rigorous inspection protocols post-machining, including coordinate measuring machines (CMM) and optical comparators, verifies conformity to specifications. Statistical process control (SPC) methods help identify variations and enable corrective actions before parts are shipped.
Training and experience of operators and programmers are invaluable. Skilled personnel can interpret complex data, troubleshoot issues promptly, and adjust processes as needed to maintain accuracy.
Finally, maintaining open communication with clients ensures that tolerances are clearly understood, and any potential issues are addressed proactively. This collaborative approach, combined with continuous process improvement, lays the foundation for consistently managing tight tolerances in high-precision CNC projects.
By integrating these strategies, Chinese manufacturers can deliver complex, custom parts that meet the most demanding standards of quality and precision required by global clients.
---
## The Impact of Advanced Technology on Global CNC Machining Capabilities
Technological innovations are transforming CNC machining, expanding the possibilities for high-precision, complex, and custom parts on a global scale. Advanced equipment and digital tools enable manufacturers to meet stringent standards, reduce lead times, and tackle previously insurmountable challenges.
Multi-axis CNC machines, such as 5-axis or even 7-axis systems, provide unparalleled flexibility. They allow complex geometries, internal features, and tight tolerances to be achieved in fewer setups, improving accuracy and efficiency. These machines also reduce the risk of errors associated with repositioning parts between operations.
Automation and robotics are increasingly integrated into CNC workflows. Automated tool changers, material handling, and inspection systems minimize human error, enhance repeatability, and enable continuous production, vital for high-volume, high-precision manufacturing.
The adoption of Industry 4.0 principles—such as IoT connectivity, real-time data analytics, and machine learning—further elevates CNC capabilities. These technologies facilitate predictive maintenance, process optimization, and quality assurance, ensuring consistent output and reducing downtime.
Advanced CAD/CAM software, incorporating simulation and verification features, helps preempt machining issues like tool collisions or deviations from tolerances. Virtual prototyping allows for optimization before physical production, saving time and reducing costly errors.
Surface finishing technologies such as laser polishing, ultrasonic cleaning, and electrochemical machining complement traditional milling and turning. These methods achieve superior surface quality, critical for optical, medical, or aerospace components.
Additive manufacturing (3D printing) is increasingly integrated with CNC machining, providing hybrid manufacturing solutions. Combining subtractive and additive processes enables the production of complex, lightweight, and high-precision parts with internal geometries that are impossible solely through traditional machining.
Digital twins and process monitoring tools enable manufacturers to simulate, monitor, and adjust machining processes dynamically. These technologies improve accuracy, reduce waste, and shorten development cycles, facilitating faster time-to-market.
Furthermore, the development of specialized cutting tools and coatings extends the capability to machine hard or sensitive materials effectively. Innovations in tooling materials, such as polycrystalline diamond (PCD) or cubic boron nitride (CBN), enhance durability and precision.
Overall, advanced technology drives global CNC machining capabilities forward, empowering manufacturers—particularly those in China—to deliver high-quality, complex, and customized parts efficiently. These innovations continue to open new horizons for industries demanding ever-higher standards of precision and performance.
---
## Collaborating with International Clients: Communication and Specification Challenges
Effective collaboration with international clients is essential in high-precision CNC machining, especially when dealing with complex custom parts. Clear communication and precise specification management help prevent misunderstandings, ensure quality, and foster long-term partnerships.
Language barriers and cultural differences can pose challenges, potentially leading to misinterpretation of technical requirements. Employing bilingual teams, detailed documentation, and visual aids such as 3D CAD files or annotated drawings can bridge communication gaps.
Time zone differences necessitate flexible scheduling and proactive communication. Regular updates, virtual meetings, and real-time project tracking tools facilitate transparency and keep all stakeholders aligned throughout the manufacturing process.
Accurately interpreting and verifying client specifications is critical. This involves thorough review of drawings, tolerances, and functional requirements, as well as seeking clarifications when necessary. Misunderstandings at this stage can result in costly rework or non-compliance with standards.
Providing detailed process documentation, inspection reports, and certifications enhances trust and demonstrates compliance with international quality standards such as ISO, ASME, or aerospace-specific certifications. This transparency is vital for clients in regulated industries.
Managing changes or design modifications during production requires clear communication channels. Agile response systems, change management procedures, and version control ensure that updates are correctly implemented without affecting quality or delivery timelines.
Cultural sensitivity and customer service excellence build trust and facilitate smoother collaboration. Understanding clients’ expectations, preferences, and feedback loops helps tailor manufacturing processes to specific needs.
Implementing robust quality management systems and adhering to international standards demonstrate commitment to excellence. This reassures clients and aligns the manufacturing process with global best practices.
Finally, post-delivery support, including technical assistance, warranty services, and ongoing communication, fosters long-term relationships. Such partnerships are instrumental in navigating the complexities of global supply chains and maintaining high standards in high-precision CNC machining.
By addressing these communication and specification challenges proactively, Chinese CNC manufacturers can successfully serve international clients, delivering complex, high-quality parts that meet global expectations.
---
## Future Trends in High-Precision CNC Machining for Global Markets
The landscape of high-precision CNC machining is continually evolving, driven by technological advancements, industry demands, and global economic shifts. Looking ahead, several key trends are poised to shape the future of this vital manufacturing sector.
One prominent trend is the integration of smart manufacturing and Industry 4.0 principles. Real-time data analytics, machine learning, and IoT-enabled devices will enable predictive maintenance, process optimization, and enhanced quality control, leading to higher efficiency and reliability.
Hybrid manufacturing processes combining CNC machining with additive manufacturing (3D printing) will become more prevalent. This synergy allows for the creation of complex geometries, internal features, and lightweight structures that are difficult to produce with traditional methods alone.
Automation and robotics will continue to reduce manual intervention, improve consistency, and enable flexible production lines capable of rapidly switching between different parts or designs. Fully automated quality inspection integrated into the machining process will further ensure tight tolerances and defect-free components.
Materials science will drive innovation in working with new, advanced materials that offer superior performance, such as high-temperature alloys, composites, and bio-compatible ceramics. Developing specialized tooling and machining techniques to handle these materials will be a focus area.
Sustainability considerations will influence future practices, with an emphasis on reducing waste, energy consumption, and environmental impact. Eco-friendly cutting fluids, waste recycling, and energy-efficient machines align with the global push toward sustainable manufacturing.
Customization and rapid prototyping will expand as digital design tools enable faster turnarounds from concept to production. This agility supports industries like aerospace, medical, and electronics, where time-to-market is critical.
Emerging technologies like artificial intelligence-driven design for manufacturability (DfM) will help optimize parts for ease of machining, cost-effectiveness, and performance, fostering innovation in product development.
Collaboration platforms and digital twin technologies will allow remote monitoring, control, and troubleshooting, facilitating global cooperation and reducing the need for on-site presence.
Finally, the proliferation of high-precision CNC machining services in developing regions, including China, will position them as key players in the global supply chain, leveraging cost advantages, advanced technology, and skilled talent to meet growing international demand.
In summary, the future of high-precision CNC machining will be characterized by intelligent automation, sustainable practices, material innovation, and increased global collaboration—driving forward the capabilities and reach of manufacturers worldwide.
---
**===OUTRO:===**
High-precision CNC machining for global clients is a continually advancing field that demands technological expertise, innovative problem-solving, and meticulous quality management. Chinese manufacturers, with their rich experience in handling complex, custom parts across diverse materials, are well-positioned to meet these challenges. As technology evolves and markets expand, embracing new tools, materials, and collaborative strategies will be essential. The ongoing pursuit of precision, efficiency, and sustainability promises a dynamic future for this critical manufacturing sector, supporting industries worldwide in achieving their most ambitious engineering goals.