Expert CNC Machining Services for Precision and Complex Parts Globally
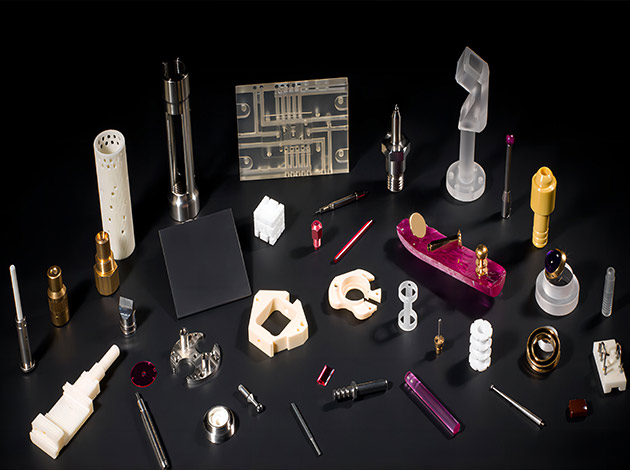
===INTRO:
In today's rapidly evolving manufacturing landscape, the demand for high-precision, complex parts is soaring across industries worldwide. From aerospace to medical devices, the need for meticulous craftsmanship and advanced machining techniques has never been greater. Expert CNC machining services have become the backbone of this precision-driven manufacturing, enabling companies to produce intricate components with tight tolerances and durable materials. This article explores how professional CNC machining providers, especially those based in China and serving global clients, leverage their experience, advanced technology, and material expertise to overcome manufacturing challenges and deliver exceptional results worldwide. Whether customizing parts to exact specifications or handling tough materials, these services are vital for industries that require reliability, accuracy, and consistency at every stage of production. Let’s delve into the core aspects that make expert CNC machining a game-changer for complex global parts.===
## Unlocking Precision: Expert CNC Machining for Complex Global Parts
CNC (Computer Numerical Control) machining is a sophisticated process that automates the control of machining tools with high precision, allowing manufacturers to produce complex geometries that traditional methods cannot achieve. Expert CNC machining services excel at transforming detailed digital designs into real-world components, often involving multi-axis operations that can handle intricate features and tight tolerances. For global clients, this means reliable production of complex parts regardless of size or complexity. These services are essential in industries like aerospace, where every millimeter counts, or in medical fields, where precision can be a matter of life and death. Chinese CNC manufacturers, such as those listed on reputable platforms, have developed extensive capabilities in this domain, offering customized solutions tailored to specific project requirements. Their expertise ensures that each part meets the highest standards of accuracy, durability, and quality, making them trusted partners for international clients.
In addition, advanced CNC machines can process a variety of materials, from metals to composites, further expanding the scope of complex component manufacturing. This flexibility allows companies to innovate and optimize their products while maintaining strict quality controls. The use of CAD/CAM integration streamlines the design-to-production process, reducing errors and accelerating delivery times. Ultimately, expert CNC machining unlocks the potential for complex designs to become tangible products with precision and reliability, even across borders.
Furthermore, with the ongoing development of multi-axis machining technology, manufacturers can now create highly detailed and precise features that were once impossible or too costly to produce. This opens up new avenues for innovation in product design, enabling more functional, lightweight, and durable components. As global supply chains grow more sophisticated, the ability of CNC service providers to consistently deliver complex parts at scale becomes a crucial competitive advantage. For industries demanding tight tolerances and high-quality finishes, expert CNC machining stands out as the indispensable solution for modern manufacturing challenges.
## Custom CNC Solutions Tailored to Your Unique Manufacturing Needs
Every manufacturing project is unique, often requiring bespoke solutions that standard processes cannot provide. Custom CNC machining services excel in this space by offering tailored manufacturing processes that align precisely with the client's design specifications and functional requirements. From initial consultation to final production, experienced CNC service providers work closely with clients to understand their specific needs—be it complex geometries, unique material considerations, or specific finishing requirements.
Chinese CNC manufacturers, such as those operating under strict international standards, have built a reputation for their flexibility and customer-centric approach. They can adapt their machinery, tooling, and process parameters to optimize output for a wide range of applications. Whether producing small batch prototypes or high-volume production runs, these service providers ensure each component meets exact specifications.
Moreover, custom CNC solutions involve rigorous quality control measures, including in-process inspections and surface finishing techniques, to guarantee consistency and precision. This is especially critical when manufacturing parts for industries like aerospace or medical devices, where tolerances are often measured in microns.
The ability to tailor machining strategies to material properties and design intricacies allows manufacturers to reduce waste, improve efficiency, and lower costs. Advanced software integration enables seamless communication between designers and machinists, ensuring that every detail is faithfully reproduced. Custom CNC machining is not just about producing parts; it’s about delivering a comprehensive, solutions-oriented service that aligns with your project goals and timeline.
By leveraging extensive experience and state-of-the-art technology, Chinese CNC providers can handle even the most complex and difficult-to-machine materials, providing a competitive edge for international clients seeking precision and reliability. This customized approach ensures that each part is a perfect fit for its intended application, ultimately enhancing product performance and customer satisfaction.
## High-Precision CNC Machining for Critical and Complex Components
Precision is the cornerstone of high-stakes industries such as aerospace, medical, and defense. CNC machining services dedicated to high-precision manufacturing have refined their processes to achieve tolerances often within a few microns. Such accuracy is essential when producing critical components that influence safety, performance, and longevity.
Expert Chinese CNC machining companies have accumulated extensive experience in handling complex parts that demand meticulous attention to detail. They utilize advanced multi-axis machines, high-precision measurement tools, and sophisticated programming techniques to ensure every feature aligns perfectly with design intent. For example, parts like turbine blades, surgical implants, or intricate gear assemblies require exceptional precision that only top-tier CNC services can deliver.
The challenge in producing these components lies not only in achieving tight tolerances but also in maintaining consistency across production batches. This necessitates rigorous quality control protocols, including 3D scanning, coordinate measuring machines (CMM), and real-time feedback systems. Such measures ensure each piece adheres to strict specifications, reducing the risk of failure or rework.
Furthermore, high-precision CNC services are adept at working with a variety of advanced materials, such as titanium, Inconel, or composite materials, which are often used in critical applications for their strength and lightweight properties. The machining process must account for material properties like hardness, thermal expansion, and machinability to maintain accuracy.
Overall, the demand for critical, complex components continues to grow, and expert CNC machining services are vital to meeting these needs. Their ability to produce high-precision parts reliably across the globe helps industries push the boundaries of technology and innovation, ensuring safety, durability, and performance in the most demanding applications.
## Advanced Materials in CNC Machining: Ensuring Durability and Accuracy
The selection of materials plays a pivotal role in CNC machining, especially when it involves high-performance, durable components. Advanced materials such as aerospace-grade alloys, ceramics, composites, and special steels are increasingly in demand for their strength-to-weight ratio, corrosion resistance, and thermal stability. CNC providers, particularly in China with extensive experience, are adept at machining these challenging materials to exact tolerances.
Working with such materials requires specialized tooling, cutting strategies, and cooling techniques to prevent deformation or damage during machining. For instance, Inconel and titanium alloys are known for their toughness and are often used in high-temperature environments. Machining these materials demands high power, precision, and expertise to avoid issues like tool wear or material warping.
Chinese CNC manufacturers have invested in advanced equipment equipped with high-performance tools and monitoring systems that can handle these demanding materials efficiently. This ensures that clients receive parts that are not only accurate but also have enhanced properties like corrosion resistance or thermal stability.
Moreover, material choice influences the finishing process. Some materials require specific surface treatments or coatings to improve wear resistance or reduce friction. CNC companies are well-versed in applying such treatments post-machining, further extending component lifespan and performance.
The ability to accurately machine a broad spectrum of advanced materials positions these CNC services as invaluable partners for industries where failure is not an option. They guarantee the durability and precision of each part, ultimately supporting the development of products that can withstand extreme conditions and demanding operational environments.
## Overcoming Global Manufacturing Challenges Through Expert CNC Services
Manufacturing on a global scale introduces unique challenges—geographical distances, varied standards, material sourcing issues, and tight schedules. Expert CNC machining services mitigate these hurdles through their extensive experience, technological capabilities, and quality assurance systems.
Chinese CNC manufacturers, serving international clients, have established robust logistics, communication, and compliance frameworks that ensure seamless collaboration regardless of location. They understand the importance of aligning with various industry standards such as ISO, ASTM, or proprietary specifications, and work diligently to meet or exceed these requirements.
One common challenge is managing complex designs that need precise execution across different production batches. Skilled CNC service providers use advanced programming, real-time monitoring, and adaptive machining techniques to maintain consistency and quality. This expertise is crucial when producing parts with intricate features or critical tolerances.
Material procurement and supply chain management are other hurdles. Experienced CNC companies often have established relationships with reliable suppliers, enabling them to source high-quality materials consistently. This reduces delays and ensures that material properties are maintained throughout the manufacturing process.
Furthermore, global manufacturing demands fast turnaround times without sacrificing quality. CNC providers leverage automation, high-speed machining centers, and efficient workflow management to deliver parts on time, helping clients stay competitive in their markets.
By focusing on quality control, compliance, and logistical efficiency, expert CNC services turn complex global manufacturing challenges into manageable processes. Their experience bridges geographical gaps and ensures that clients receive precise, reliable parts regardless of where they are produced.
## Experienced Machining Teams Delivering Consistent Quality Worldwide
The backbone of any successful CNC machining operation is a team of experienced professionals who understand the nuances of complex manufacturing. These teams bring years of expertise in programming, operation, inspection, and quality assurance, ensuring consistent results across every batch.
Chinese CNC service providers have cultivated a highly skilled workforce, often trained in both traditional craftsmanship and modern technological techniques. This blend of skills enables them to tackle difficult-to-machine materials and intricate designs efficiently.
Team expertise is especially critical when working on parts that require ultra-tight tolerances, complex geometries, or specialized surface finishes. Experienced operators can adjust machining parameters on the fly, troubleshoot issues, and optimize tools to improve productivity and quality.
In addition, their comprehensive understanding of materials allows them to select the right tooling, cutting speeds, and cooling strategies, reducing tool wear and improving surface quality. This expertise translates into longer tool life, less rework, and higher overall efficiency.
Quality assurance is integrated into every step of the process. Skilled inspectors use advanced measurement systems like CMMs or laser scanners to verify dimensional accuracy, ensuring each part conforms to strict specifications. They also implement strict SPC (Statistical Process Control) measures to monitor consistency over production runs.
Global clients benefit from this professionalism through reliable delivery of high-quality parts. Trusting experienced teams means reducing risk, minimizing waste, and achieving the precision needed for critical applications, thereby reinforcing the reputation for excellence that Chinese CNC manufacturers are known for worldwide.
## Case Studies: Tackling Tough CNC Machining Problems Across Industries
Across various industries, CNC machining companies have faced and solved some of the most challenging manufacturing problems, demonstrating their expertise and problem-solving capabilities. These case studies reveal how complex part production is achieved despite technical difficulties.
In aerospace, a manufacturer needed turbine blades with complex internal cooling channels. The challenge was machining precise internal features without compromising structural integrity. The solution involved multi-axis machining with custom tooling and precise coolant control—resulting in blades that met stringent safety standards.
Medical device producers required titanium implants with micro-scale features. The challenge was maintaining tight tolerances over complex geometries while ensuring biocompatibility. Expert CNC companies employed high-precision machines, specialized tooling, and rigorous inspection, delivering implants that met all regulatory requirements.
In the automotive sector, a project involved producing lightweight, high-strength composite components with complex surface textures. The challenge was to combine CNC machining with precise finishing to achieve aesthetics and durability. The solution involved tailored process parameters and post-machining treatments, meeting both functional and visual standards.
Another example includes manufacturing high-performance heat exchangers using advanced alloys like Inconel. The difficulty was machining these materials without causing deformation or excessive tool wear. The company used high-power machines with specialized coatings and cooling techniques, ensuring longevity and precise geometries.
These case studies reflect how expertise, innovation, and flexibility in CNC machining can overcome formidable challenges. They exemplify the importance of experience in problem-solving and the ability to adapt processes for tough materials and complex designs. Many industries trust these solutions for their most critical components, setting benchmarks for quality and precision globally.
## Why Material Selection Matters in High-Precision CNC Manufacturing
Choosing the right material is fundamental to the success of high-precision CNC machining projects. Material properties directly influence machinability, durability, weight, and performance, especially in critical applications.
Advanced materials like aerospace alloys, engineering plastics, ceramics, and composites are increasingly favored for their specific benefits. For example, titanium offers excellent strength-to-weight ratio and corrosion resistance, making it ideal for medical implants and aircraft parts.
Chinese CNC service providers have gained extensive expertise in working with these challenging materials. They understand how different materials respond to machining processes, which tooling and cooling methods are most effective, and how to prevent issues like warping, cracking, or excessive tool wear.
Material selection also impacts surface finish and tolerances. Some materials are more prone to surface roughness or require additional treatments like polishing or coating. Proper choice and handling of materials ensure that finished parts meet the strict quality standards demanded by high-precision industries.
Furthermore, selecting appropriate materials can enhance the functional performance of the final product, such as improving thermal stability or wear resistance. This consideration is vital for components exposed to extreme conditions or high stress.
In summary, informed material selection driven by industry standards, project requirements, and manufacturing capabilities is crucial. It ensures that CNC-machined parts not only meet dimensional specifications but also perform reliably over their service life, thereby safeguarding investment and operational efficiency.
## Designing for Manufacturability: How Custom CNC Machining Benefits Your Project
Designing parts with manufacturability in mind can significantly reduce costs, lead times, and production risks. Custom CNC machining services advocate for design-for-manufacturing (DFM) principles that optimize parts for efficient machining without sacrificing functionality.
Collaborating with experienced CNC providers early in the design phase allows for insights into how complex geometries, tolerances, and material choices impact manufacturability. These professionals can suggest design modifications that simplify tooling, reduce machining time, or improve surface quality.
For instance, adding draft angles, fillets, or avoiding undercuts can facilitate easier machining and assembly. Removing unnecessary features or consolidating multiple parts into a single piece also streamlines production and reduces assembly costs.
Chinese CNC manufacturers leverage their extensive experience to provide valuable feedback, helping clients avoid costly rework or delays. They can identify potential issues like tool accessibility or excessive machining steps and propose alternative solutions that still meet project objectives.
Designing with tolerances and surface finishes in mind from the outset ensures that parts are produced to spec without extensive post-processing. This proactive approach enhances overall efficiency and quality.
Ultimately, a well-thought-out design tailored for CNC manufacturing leads to faster turnaround, lower costs, and higher quality outcomes. It empowers clients to innovate confidently, knowing their designs are optimized for precise, reliable production across diverse industries worldwide.
## Global CNC Machining: Meeting International Standards and Expectations
Operating in a global market requires CNC machining providers to adhere to a variety of international standards and client expectations. Ensuring compliance with regulations such as ISO, ASTM, or industry-specific standards is critical for quality, safety, and interoperability.
Chinese CNC service providers have made significant strides in aligning their processes with international quality standards, obtaining relevant certifications, and implementing rigorous quality management systems. This commitment reassures clients that parts produced abroad meet their home country’s regulatory requirements.
Meeting expectations also involves transparent communication, timely delivery, and consistent quality. Skilled teams utilize advanced inspection tools, documentation, and traceability systems to monitor production quality and provide comprehensive reports.
Furthermore, understanding cultural differences, language barriers, and logistical complexities is vital for international collaboration. Experienced CNC services excel at managing these factors through dedicated project managers and multilingual support.
Adapting to different industry standards—whether for aerospace, automotive, medical, or energy sectors—requires specialized knowledge and attention to detail. Custom solutions are designed to meet or surpass these standards, ensuring seamless integration into clients’ supply chains.
By maintaining high standards and building trust through transparency and compliance, global CNC machining providers establish long-term relationships with clients worldwide, supporting their growth and innovation in diverse markets.

Supplier of customized sapphire and ruby parts from drawings
## The Role of Experience in Achieving Complex Part Tolerances
Experience is arguably the most valuable asset in CNC machining, especially when dealing with complex parts requiring tight tolerances. Seasoned machinists and engineers understand the subtleties of cutting parameters, tool wear, and material behavior, enabling them to consistently produce precise components.
Chinese CNC manufacturers with decades of experience have accumulated extensive knowledge of various materials and complex geometries. Their expertise allows them to optimize setups, select appropriate tooling, and implement adaptive machining strategies that minimize errors.
Achieving complex tolerances often involves using precision measurement tools like CMMs, laser scanners, and optical comparators. Experienced teams interpret measurement data accurately, making real-time adjustments to maintain tight control over dimensions.
Moreover, their familiarity with multi-axis machining and intricate toolpaths ensures that even the most complex features are fabricated with exactness. This skill is crucial when manufacturing parts for industries like aerospace or medical implants, where deviations can compromise safety or performance.
Experience also contributes to problem-solving when unexpected issues arise, such as tool deflection or thermal distortions. Veteran machinists can quickly diagnose and rectify these problems, saving time and avoiding costly rework.
In sum, experience transforms CNC machines into precise, reliable tools capable of producing the most challenging parts. It underpins the trust that clients place in their suppliers to deliver consistent, high-quality, high-tolerance components across diverse projects globally.
## Future Trends in CNC Machining: Innovation and Precision Worldwide
The future of CNC machining is poised for continued innovation driven by advances in technology, materials, and automation. Industry leaders are investing heavily in smart manufacturing, AI-driven optimization, and new material sciences to push the boundaries of precision and complexity.
Additive manufacturing (3D printing) is increasingly integrated with CNC processes, enabling hybrid solutions that combine the strengths of subtractive and additive techniques for complex, lightweight, and high-performance parts. This synergy enhances design freedom and reduces lead times.
Automation and Industry 4.0 principles are transforming CNC shops into intelligent factories capable of real-time data collection, predictive maintenance, and autonomous adjustments. These innovations improve efficiency, reduce downtime, and ensure consistently high quality.
Materials science continues to evolve, with new composites, alloys, and ceramics expanding what is possible in high-precision machining. These advanced materials open opportunities for lighter, stronger, and more durable components in aerospace, medical, and energy sectors.
Furthermore, virtual simulation and digital twins enable manufacturers to test and optimize machining processes before actual production, minimizing errors and material waste. This proactive approach enhances precision and reduces costs.
Chinese CNC manufacturers are actively adopting these global trends, harnessing their experience to deliver innovative, precise, and sustainable solutions worldwide. As technology progresses, the scope of what can be achieved with CNC machining will continue to expand, opening new horizons for industries and applications across the globe.
In conclusion, the future of CNC machining is bright, marked by continuous innovation, smarter processes, and ever-increasing precision, ensuring that complex, high-quality parts remain accessible worldwide.