China’s CNC Machining Experts Deliver Precision for Global High-End Projects
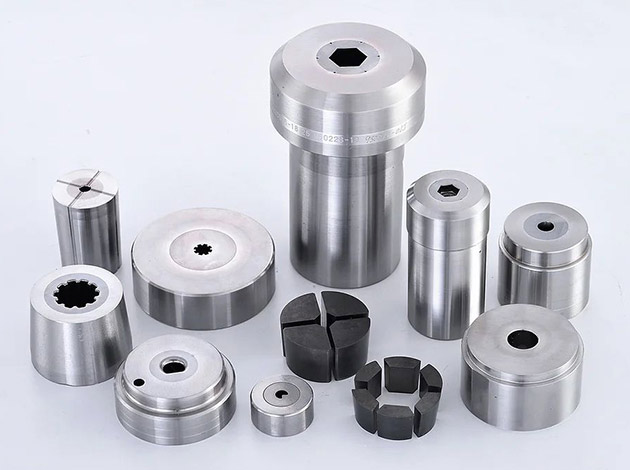
===INTRO:
As global industries increasingly demand precision-engineered components, China’s CNC machining industry has emerged as a leader in delivering high-quality, customized solutions for complex projects. Boasting advanced technology, extensive experience, and a focus on innovation, Chinese CNC manufacturers are now at the forefront of supporting international clients with high-end, precision components. This article explores how China’s CNC machining experts excel in tackling sophisticated challenges, ensuring consistent quality, and paving the way for future technological advancements in the field.
---
## China’s CNC Machining Industry Leads in Precision for Global Projects
China’s CNC machining industry has rapidly evolved into a powerhouse of high-precision manufacturing, especially for international clients with demanding specifications. The country’s manufacturers utilize state-of-the-art equipment and rigorous quality control protocols to ensure every component meets tight tolerances. Their capability to handle complex, high-precision projects positions China as a trusted partner worldwide. From aerospace to medical devices, Chinese CNC firms are renowned for their ability to produce intricate parts with exceptional accuracy.
Moreover, the industry’s competitive pricing combined with technological excellence attracts global companies seeking reliable yet cost-effective suppliers. The integration of automation and smart manufacturing systems enhances efficiency, reduces errors, and accelerates project delivery times. As a result, China’s CNC machining industry now plays a pivotal role in supporting high-end, precision-dependent sectors worldwide.
Advancements in multi-axis machining and high-speed processing allow Chinese factories to produce components with intricate geometries that were once considered unfeasible. These capabilities are backed by strict adherence to international standards, ensuring that exported parts perform reliably under demanding conditions. Consequently, China’s reputation as a high-precision CNC machining hub continues to grow on the global stage.
The industry’s commitment to continuous innovation and upgrading equipment ensures they stay ahead of market trends. This proactive approach enables Chinese CNC manufacturers to meet evolving client needs, especially for projects requiring micro-level tolerances and complex assemblies. Their robust infrastructure and skilled workforce underpin their dominance in the global high-end machining arena.
Furthermore, Chinese CNC companies often collaborate closely with clients from the initial design phase through to production, providing valuable insights and optimization suggestions to enhance part performance. This seamless cooperation fosters trust and long-term relationships, reinforcing China’s position as a reliable source for precision manufacturing.
In addition to quality, China’s CNC machining firms emphasize scalability, allowing clients to ramp up or down production based on project demands. Such flexibility is critical for high-end projects where precision and timing are paramount. With the ability to adapt quickly, Chinese manufacturers support diverse sectors, including aerospace, defense, healthcare, and high-tech industries.
Finally, the country’s strategic focus on research and development fuels continuous improvement in machining techniques and materials. This relentless pursuit of excellence ensures that Chinese CNC experts remain capable of delivering increasingly complex and high-value components. Such industry momentum signifies China’s leadership in the realm of precision CNC machining on a global scale.
---
## Custom CNC Solutions Tailored to High-Precision Overseas Client Needs
Custom CNC machining is at the heart of China’s success in serving international markets. Each project is approached with a client-centric mindset, emphasizing tailored solutions that meet specific design, material, and performance requirements. Chinese manufacturers excel at translating detailed drawings and technical specifications into precise, high-quality components, often exceeding client expectations.
The process begins with comprehensive consultations to understand the nuanced needs of clients, especially for high-end applications that demand micro-level accuracy. Based on these discussions, Chinese CNC experts develop customized machining programs, selecting appropriate tools, processes, and tolerances to ensure optimal results. This personalized approach minimizes errors and enhances efficiency.
One of China’s key strengths is their capability to process a broad range of materials—from titanium and stainless steel to advanced composites and ceramics. High-value materials require specialized tooling and precise control, which Chinese firms have mastered through years of experience and continuous technological upgrades. As a result, clients receive components that are not only accurate but also durable and fit for demanding environments.
The ability to produce complex geometries—such as intricate cavities, micro-holes, and fine threads—is vital for high-precision projects. Chinese CNC manufacturers employ multi-axis machining, high-precision spindles, and advanced software to realize these intricate designs with extreme accuracy. They often collaborate closely with designers to optimize part layouts for manufacturability, reducing time and cost.
Moreover, quality assurance is deeply integrated into the customization process. Chinese firms utilize advanced inspection equipment, including coordinate measuring machines (CMMs) and laser scanners, to verify every batch against strict tolerances. This rigorous verification ensures that each component aligns precisely with the original specifications, crucial for high-end applications like aerospace and medical implants.
The flexibility in order quantities—from small prototypes to large production runs—is another advantage. Chinese manufacturers can swiftly adapt their processes to accommodate urgent project timelines without compromising quality. This agility is particularly valuable for overseas clients operating in fast-paced industries.
Additionally, Chinese CNC service providers often offer value-added solutions such as surface finishing, heat treatment, and assembly, ensuring a comprehensive approach to high-precision manufacturing. This integrated service model simplifies supply chains for international clients, saving time and resources.
Communication and transparency are prioritized throughout the process. Many companies leverage digital platforms to provide real-time updates, drawings, and inspection reports, fostering trust and clarity. This openness helps clients make informed decisions and ensures alignment at every stage.
In essence, China’s CNC machining industry thrives on delivering custom solutions that precisely match client needs, especially for high-end, complex projects. Their adaptability, material expertise, and unwavering commitment to quality make them ideal partners for global companies seeking reliable, high-precision components.
---
## Overcoming Complex Challenges in High-End CNC Machining Applications
High-end CNC machining often involves overcoming intricate challenges—such as tight tolerances, complex geometries, and demanding materials—that require exceptional skill and technology. Chinese CNC experts have developed robust strategies and technological capabilities to address these difficulties effectively.
One common challenge is machining difficult materials like titanium, Inconel, and ceramics, which are essential in aerospace, medical, and high-performance industries. These materials often pose issues like rapid tool wear and thermal deformation. Chinese manufacturers counter this by selecting specialized cutting tools, optimizing cutting parameters, and applying advanced cooling techniques to maintain precision and prolong tool life.
Another challenge is achieving micro-level tolerances in tiny, complex parts. Chinese firms utilize high-precision, multi-axis CNC machines equipped with advanced control systems that enable real-time monitoring and correction of machining processes. Such precision control ensures that even the most intricate features meet strict specifications.
Complex geometries—such as internal cavities, micro-holes, or curved surfaces—require sophisticated programming and multi-axis machining strategies. Chinese CNC experts employ advanced CAD/CAM software combined with 5-axis or multi-axis machining centers to realize these designs accurately. They also conduct extensive simulation and prototyping to prevent errors before actual production.
Dealing with heat distortion and material deformation during machining is another significant challenge. Chinese manufacturers implement temperature control systems and carefully select machining parameters to mitigate these effects. Their experience allows them to predict and compensate for such issues, ensuring consistent part quality.
Furthermore, managing complex assembly requirements and tight tolerances across multiple components demands rigorous inspection and quality control protocols. Chinese firms utilize in-line inspection tools, such as laser measurement systems, to monitor and adjust processes dynamically. This approach minimizes scrap and rework, maintaining high standards throughout production.
Supply chain challenges, including sourcing reliable high-quality materials and maintaining consistent process parameters, are addressed through strong supplier relationships and standardization practices. Chinese manufacturers invest in staff training and process documentation to sustain repeatability and precision.
In some cases, international clients face unique challenges—such as the need for ultra-lightweight parts or components with specific acoustic or thermal properties. Chinese CNC experts adapt by experimenting with innovative materials and processing techniques, often collaborating with material scientists to develop custom solutions.
Ultimately, overcoming these complex challenges requires a combination of technological innovation, skilled craftsmanship, and meticulous process management. Chinese CNC machining companies continually refine their methods to ensure that even the most demanding high-end projects are delivered with precision and reliability.
---
## Advanced Material Usage in CNC Processing for Premium Projects
High-end projects often demand components made from advanced materials characterized by their strength, light weight, or resistance to extreme conditions. Chinese CNC machining experts have mastered the handling of these materials, ensuring their properties are preserved and optimized through precise processing.
Titanium and its alloys are widely used in aerospace and medical applications due to their strength-to-weight ratio and corrosion resistance. Machining titanium requires specialized tooling and cooling strategies to prevent work hardening and deformation. Chinese firms leverage their extensive experience and tailored machining parameters to produce high-precision titanium components reliably.
Inconel, a superalloy known for its heat resistance, presents additional challenges due to its toughness and tendency to work-harden. Chinese manufacturers employ high-speed, high-torque spindles combined with advanced cutting tools and controlled environments to achieve accurate results without damaging the material.
Ceramics and composites are increasingly popular in electronics and high-performance engineering. These materials are brittle and require delicate handling. Chinese CNC factories utilize specialized grinding and polishing processes, along with precision fixturing, to ensure flawless outcomes. Their expertise minimizes cracking and ensures dimensional stability.
High-performance polymers like PEEK and PTFE are also processed with high precision for medical implants and aerospace parts. Adjustments in feed rates, spindle speeds, and cooling are critical to prevent melting or deformation, and Chinese manufacturers optimize these parameters for each material.
For each material, comprehensive testing and inspection are integral. Chinese CNC firms employ non-destructive testing (NDT), ultrasonic inspection, and microscopic analysis to verify the integrity and consistency of complex, high-value components.
Sustainable processing techniques are increasingly adopted as well, such as dry machining or eco-friendly coolants, to reduce environmental impact while maintaining quality. These innovations align with global standards and client expectations.
The ability to process a diverse range of advanced materials underpins China’s reputation for high-end CNC machining. Their tailored approaches ensure that materials’ unique properties are preserved, enabling the production of components that meet the rigorous demands of premium industries.
In sum, mastery over advanced material processing is a cornerstone of China’s high-precision CNC industry, positioning them as indispensable partners for global projects requiring the highest quality standards.
---
## The Role of Extensive Experience in Achieving High-Quality CNC Results
Experience is arguably the most valuable asset for China’s CNC machining industry. Decades of accumulated expertise enable Chinese manufacturers to navigate the complexities of high-precision, high-value projects with confidence and competence.
Veteran technicians and engineers bring a deep understanding of material behaviors, machining physics, and process optimization. Their insights help anticipate potential issues, such as tool wear, thermal distortion, or dimensional deviations, allowing preemptive adjustments that save time and costs.
Experience also fosters an intuitive grasp of how to select appropriate tooling, cutting parameters, and fixturing for diverse materials and geometries. Such knowledge is critical when producing micro-scale features or complex assemblies, where even minor errors can be catastrophic.
Chinese CNC firms regularly invest in staff training and skill development, ensuring that their teams stay updated with the latest industry standards and technological advancements. This commitment to continuous learning translates into higher quality outputs and innovative problem-solving capabilities.
Additionally, seasoned manufacturers have accumulated a vast library of successful strategies and lessons learned from challenging projects worldwide. This historical knowledge base enables them to approach new projects with confidence, minimizing trial-and-error and accelerating production timelines.
Experience also enhances their ability to collaborate effectively with international clients. Understanding different cultural expectations and technical standards allows Chinese manufacturers to tailor solutions that meet or exceed global requirements.
Many Chinese CNC companies participate in industry exhibitions, technical forums, and research collaborations, further enriching their expertise. Such engagements keep them at the cutting edge of machining techniques and materials science.
The importance of experience is evident in their capacity to handle high-stakes projects, such as aerospace components or medical implants, where failure is not an option. Their ability to consistently deliver precision results builds trust and long-term partnerships.
Ultimately, extensive hands-on experience combined with a proactive approach to innovation ensures that China’s CNC experts can produce the highest quality parts, even under the most demanding specifications. This wealth of knowledge continues to be a driving force behind China’s global leadership in high-end CNC machining.
---
## Case Studies: Solving Global Difficulties in CNC Manufacturing
Real-world examples showcase China's CNC industry’s prowess in overcoming formidable manufacturing challenges. These case studies illustrate how Chinese experts leverage their skills and technology to deliver solutions that meet the highest standards.
One notable case involved manufacturing aerospace engine components made from titanium alloys. The challenge was to produce micro-scale features within strict tolerances while preventing work hardening. Chinese firms utilized high-precision 5-axis machining combined with innovative cooling techniques, achieving the required accuracy and surface finish.
In another instance, a medical device manufacturer required complex ceramic parts with internal micro-channels. The brittleness of ceramics posed a significant risk of cracking. Chinese specialists optimized grinding and polishing processes, introduced custom fixtures, and employed non-destructive testing to ensure flawless parts.
A defense contractor sought lightweight, high-strength components made of Inconel for extreme thermal environments. The Chinese company used high-speed machining and specialized tools to counteract the superalloy’s toughness, successfully producing parts that complied with stringent specifications.
In the field of high-performance electronics, processing advanced composite materials presented challenges related to material delamination and deformation. Chinese CNC experts adapted their machining parameters and incorporated real-time monitoring to maintain dimensional stability, meeting tight tolerances.
A notable example also involves the production of high-precision molds for optical lenses, requiring micro-precision and ultra-smooth surfaces. Chinese manufacturers employed laser-assisted machining and precision polishing techniques, achieving the desired optical quality.
These case studies highlight that success hinges on a deep understanding of material behaviors, innovative process adjustments, and rigorous inspection protocols. Chinese companies often develop customized solutions, collaborating closely with clients to overcome unique challenges.
The ability to resolve such complex difficulties not only demonstrates technical excellence but also builds global confidence in China’s capacity to support high-end industries. These success stories continue to inspire further innovation within the industry.
In sum, these case examples underscore the importance of experience, technological adaptability, and problem-solving ingenuity—traits that define China’s CNC machining leaders on the international stage.
---
## Precision Engineering: From Drawings to Finished Components
Transforming detailed engineering drawings into flawless finished parts is the core of China’s CNC machining excellence. This process demands meticulous attention to detail, advanced technology, and skilled craftsmanship to ensure every component aligns perfectly with design intent.
The journey begins with comprehensive review and interpretation of technical drawings. Chinese CNC experts analyze tolerances, surface finish requirements, and material specifications to develop precise machining plans. They often collaborate with designers to clarify ambiguous features and optimize manufacturability.
High-precision CAD/CAM software is employed to generate toolpaths that accurately realize complex geometries. Simulation and virtual prototyping help identify potential issues before actual machining, saving time and reducing waste. This proactive approach enhances the likelihood of successful production.
During manufacturing, strict process control is maintained. Chinese firms utilize multi-axis machining centers equipped with real-time monitoring systems to ensure dimensional accuracy. Adaptive feedback mechanisms allow automatic corrections, maintaining tight tolerances throughout production.
Post-machining, components undergo comprehensive inspection using coordinate measuring machines (CMMs), laser scanning, and optical comparators. These measurements verify adherence to specifications at micro-level precision. Any deviations are promptly addressed through adjustments in the manufacturing process.
Surface finishing and treatment further refine components, especially for high-end applications requiring specific surface textures or coatings. Chinese industry leaders employ advanced polishing, anodizing, or coating techniques to meet exacting aesthetic and functional standards.
The final step involves assembly and testing, where components are integrated into larger systems. This holistic approach ensures that individual parts not only meet dimensional standards but also function seamlessly within the intended application.
Throughout this journey, documentation and traceability are maintained rigorously. Digital records of inspections, process parameters, and material certifications provide transparency and quality assurance for international clients.
This meticulous process—from interpreting drawings to delivering finished parts—embodies China’s commitment to precision engineering. Their ability to convert complex designs into high-quality components underpins their global reputation as reliable high-end CNC machining partners.
---
## High-Precision Machining Techniques for Complex and Demanding Parts
Complex parts requiring high precision demand sophisticated machining techniques. China’s CNC industry has adopted and refined a range of methods to produce challenging components with superior accuracy and surface quality.
Multi-axis machining is fundamental for producing intricate geometries. 5-axis and multi-axis centers allow for cutting complex shapes in a single setup, reducing errors associated with multiple fixtures and reorientations. Chinese manufacturers excel in programming and optimizing these machines for maximum efficiency.
High-speed machining techniques enable faster material removal rates while maintaining precision. These methods reduce machining time and improve surface finishes, crucial for high-end applications such as optical molds and aerospace parts.
Micro-machining techniques are employed for components with micro-holes, fine threads, or micro-patterns. Chinese firms utilize ultra-precision spindles, laser measurement, and specialized tooling to achieve micro-level features with tight tolerances.
Electro-discharge machining (EDM), including wire EDM and sinker EDM, complements traditional milling and turning for hard materials and intricate shapes. Chinese companies leverage advanced EDM technology to produce parts that are otherwise impossible with conventional methods.
Surface texturing and finishing techniques, such as laser texturing, abrasive flow machining, or chemical polishing, enhance functional properties like friction, wear resistance, or aesthetic appeal. These processes are carefully integrated into the production chain.
Real-time process monitoring and adaptive control systems help maintain consistent quality across complex parts. Data-driven adjustments prevent defects and ensure that each component meets exact specifications.
Lastly, additive manufacturing (3D printing) is increasingly integrated with CNC processes to create complex internal structures or prototypes before final machining. Chinese firms are exploring hybrid methods to push the boundaries of complexity and precision.
By combining these advanced techniques, China’s CNC experts can successfully produce demanding parts that require tight tolerances, fine features, and high surface quality—capabilities essential for pioneering high-end industries worldwide.
---
## How China’s CNC Experts Ensure Consistency in Quality and Accuracy
Consistency in quality and accuracy is critical for high-end CNC machining, especially when producing parts for aerospace, medical, or defense applications. Chinese CNC manufacturers prioritize stringent quality assurance protocols to uphold high standards across all production stages.
They employ comprehensive inspection systems, including coordinate measuring machines (CMMs), laser scanners, and optical comparators, to verify dimensions and surface finishes against specifications. Data collected is analyzed to identify trends and prevent deviations.
Process standardization plays a vital role. Chinese companies develop detailed operating procedures and employ statistical process control (SPC) methods to monitor key parameters. Deviations trigger immediate adjustments, ensuring persistent accuracy.
Staff training and skill development are continuous priorities. Experienced technicians and engineers are empowered to recognize potential issues early, troubleshoot effectively, and implement corrective actions swiftly.
Monitoring equipment condition and calibration is rigorously maintained to prevent measurement inaccuracies. Regular calibration schedules and maintenance routines sustain measurement reliability.
Material traceability is another essential aspect. Certificates of raw materials and in-process inspections ensure that only compliant materials are used, maintaining consistency in high-value components.
Furthermore, Chinese firms foster a culture of quality through quality management systems such as ISO 9001 and AS9100. Certification demonstrates their commitment to maintaining internationally recognized standards.
Client inspection reports and feedback are actively integrated into the quality assurance process. Transparent communication about quality metrics builds trust and allows for continuous improvement.
Finally, the adoption of Industry 4.0 principles—such as data analytics, IoT sensors, and automated quality checks—enhances real-time monitoring and predictive maintenance, further ensuring consistent precision in high-end projects.
Through these comprehensive measures, China’s CNC experts guarantee that each component consistently meets the exacting standards expected by global clients, establishing a reputation for reliability and excellence.
---
## Innovations in CNC Technology Supporting Complex High-End Projects
Innovation is the driving force behind China’s leadership in high-precision CNC machining. Manufacturers continually integrate new technologies to meet the escalating demands of complex, high-end projects.
One significant advancement is the adoption of intelligent automation, such as robotic arms and automated material handling systems, which increase precision and repeatability while reducing human error. These innovations enable high-volume, consistent production of intricate parts.
Multi-axis machining centers with enhanced control systems facilitate the creation of complex geometries with minimal setups. Real-time feedback and adaptive control ensure that deviations are corrected instantly, maintaining tight tolerances.
The integration of digital twin technology allows manufacturers to simulate machining processes virtually, optimizing toolpaths and predicting potential issues before actual production. This proactive strategy reduces trial-and-error and accelerates project timelines.
High-speed, high-precision spindle technology enables faster material removal without sacrificing accuracy. Coupled with high-frequency vibration damping systems, these spindles produce superior surface finishes on demanding materials.
Laser additive manufacturing is increasingly incorporated for creating complex internal structures or repairing high-value components. This hybrid approach combines subtractive and additive methods to push the boundaries of design and functionality.
Advanced software solutions, including AI-powered CAM and CAD platforms, optimize machining strategies, improve efficiency, and reduce programming errors. Such tools are vital for handling complex parts with multiple features.
Inspection technologies are also evolving with 3D scanning and non-contact measurement systems, providing rapid, comprehensive quality checks. Data from these systems feed into continuous process improvements.
Nanotechnology and surface coating innovations enhance the functional properties of finished components, such as wear resistance or thermal stability, further supporting high-performance applications.
Through these technological innovations, Chinese CNC companies are continually expanding their capabilities to address the most demanding high-end projects globally, ensuring precision, efficiency, and innovation.
---
## Key Factors in Successful Custom CNC Machining for International Clients
Success in providing custom CNC solutions for international clients hinges on several critical factors. Chinese manufacturers recognize these and have embedded them into their operational philosophy.
First, a thorough understanding of client requirements—both technical and strategic—is essential. Detailed communication ensures that design intent, materials, tolerances, and functional needs are accurately captured and translated into manufacturing processes.
Second, technological capability and equipment readiness—such as multi-axis machining centers, advanced inspection tools, and material processing expertise—are fundamental to achieving high precision and complex geometries.
Third, skilled workforce and continuous staff training ensure that craftsmanship and technical knowledge keep pace with evolving industry standards and innovations.
Fourth, rigorous quality management systems and process controls guarantee consistency and reliability across production batches. Certification standards like ISO 9001 and AS9100 build trust in global markets.
Fifth, flexibility and responsiveness—being able to adapt to design changes or urgent project timelines—are crucial for international clients operating in dynamic environments.
Sixth, an integrated approach to quality assurance, from raw material sourcing to final inspection, minimizes defects and rework, saving time and costs.
Seventh, proactive collaboration and transparent communication, including digital data exchange and real-time updates, foster trust and ensure alignment throughout the project lifecycle.
Eighth, a focus on sustainable practices and eco-friendly processes aligns with global environmental standards, resonating with international clients’ corporate social responsibility goals.
Finally, continuous innovation and investment in new technologies ensure that Chinese CNC manufacturers stay competitive and capable of handling the most complex and high-value projects.
By aligning these factors with their operational practices, China’s CNC industry consistently delivers successful, high-precision, customized solutions that meet or exceed international client expectations.
---
## The Future of CNC Machining: Trends and Challenges in Global Markets
Looking ahead, the CNC machining industry faces both exciting opportunities and formidable challenges. For China’s industry to maintain its leadership, adaptation and innovation will be paramount.
Emerging trends include increased adoption of Industry 4.0 technologies, such as IoT, big data analytics, and cloud-based manufacturing management, which enhance process visibility and predictive maintenance. These technologies will enable even greater precision, efficiency, and customization.
Additive manufacturing (3D printing) is poised to complement subtractive CNC processes, allowing for complex internal structures and rapid prototyping. Hybrid manufacturing solutions will become more prevalent, offering new design possibilities and cost efficiencies.
Material science advancements will continue to expand the range of usable high-performance materials, demanding further process innovation to handle their unique properties. Sustainable and eco-friendly machining practices will also gain importance, driven by global environmental standards.
However, challenges persist. The industry must address rising labor costs, the need for highly skilled operators, and intellectual property protection concerns. Ensuring workforce talent and safeguarding innovations will be critical.
Maintaining consistent quality across an increasingly complex supply chain and global market demands ongoing investments in quality control, automation, and standardization.
Global geopolitical shifts may influence trade policies, tariffs, and supply chain stability, necessitating strategic agility among Chinese manufacturers.
Finally, staying at the forefront of technological innovation while managing costs will be essential to compete with other emerging manufacturing hubs. Embracing sustainable practices and fostering international collaborations can open new avenues for growth.
In conclusion, China’s CNC machining industry is well-positioned to navigate these trends and challenges, leveraging its technological expertise, experience, and innovative spirit to support the evolving needs of global high-end projects.