How Chinese CNC Manufacturers Excel in Precision and Complex Machining
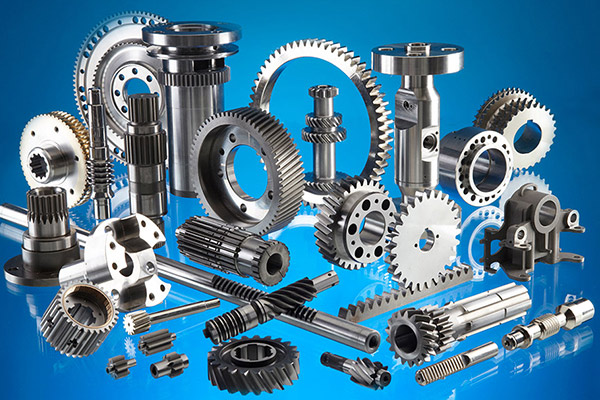
# How Chinese CNC Manufacturers Excel in Precision and Complex Machining
---
##
In recent years, Chinese CNC manufacturers have gained a formidable reputation on the global stage for their exceptional capabilities in high-precision and complex machining. As the demand for intricate components in industries like aerospace, medical devices, and automotive continues to grow, these manufacturers have risen to the challenge by integrating advanced technology, extensive experience, and innovative processes. Their ability to customize parts according to detailed specifications, handle difficult materials, and deliver consistent quality positions them as key players in the global CNC landscape. This article explores how Chinese CNC companies excel in these areas, highlighting their strategic approaches, technological advancements, and commitment to quality.
---
## Chinese CNC Manufacturers Lead in High-Precision Machining Excellence
Chinese CNC manufacturers have made remarkable strides in achieving high-precision machining, often matching or surpassing international standards. They invest heavily in state-of-the-art equipment such as multi-axis CNC mills, lathes, and grinding machines, which enable them to produce components with tolerances within microns. These facilities are equipped with sophisticated control systems that allow for intricate programming and real-time adjustments, ensuring precision at every step.
Furthermore, they prioritize continuous staff training, fostering a team of highly skilled engineers and technicians who understand the nuances of precision manufacturing. Such expertise enables them to interpret complex design files and translate them into accurate physical parts. The integration of AI and automation further enhances their ability to maintain consistent quality, reduce errors, and optimize production workflows.
Another factor is the adoption of advanced measurement and inspection technologies like coordinate measuring machines (CMM) and laser scanners. These tools allow for thorough quality control, ensuring that each part adheres strictly to specified tolerances. As a result, Chinese CNC manufacturers have established a reputation for delivering high-precision components that meet rigorous international standards.
In addition, many manufacturers participate in industry certifications and quality management systems such as ISO 9001, which uphold high standards throughout their processes. This commitment to excellence not only builds trust among global clients but also positions China as a leading hub for precision machining.
The ability to produce high-precision parts consistently is a cornerstone of their success, especially in sectors where minute deviations can lead to critical failures. The combination of advanced machinery, skilled personnel, and strict quality controls ensures that Chinese CNC firms remain competitive in precision-driven markets worldwide.
---
## Customizing Complex Parts to Meet International Industry Standards
One of the most compelling strengths of Chinese CNC manufacturers is their expertise in customizing complex parts according to detailed client specifications and international standards. Whether it's aerospace engine components, medical implants, or precision tooling, these companies excel at translating complex drawings into physical realities.
They operate with a "design-to-production" approach, working closely with clients to understand their unique requirements. This involves detailed consultations, technical assessments, and iterative prototyping to ensure the final product aligns with functional and quality standards. By utilizing advanced CAD/CAM software, manufacturers can generate precise toolpaths that accommodate intricate geometries and tight tolerances.
Furthermore, Chinese CNC firms are adept at handling diverse design complexities, such as micro-machining tiny features, deep cavities, or multi-material assemblies. They leverage multi-axis machining centers capable of executing complex movements that traditional equipment cannot achieve, thereby enabling the production of sophisticated parts with high accuracy.
To meet international industry standards, these manufacturers strictly adhere to global quality protocols, including testing, certifications, and documentation. They often possess certifications like ASME, ISO, and specific industry standards, ensuring their parts are compliant and reliable for critical applications.
Customization isn't limited to geometry; material selection is also tailored to meet demanding performance criteria. Whether working with titanium, Inconel, ceramics, or composites, Chinese CNC providers adapt their machining strategies to optimize surface finish, structural integrity, and durability.
Overall, their capacity to deliver tailored, complex components enables global clients to access high-quality, precision-engineered parts without the need for extensive local manufacturing facilities, making China a go-to destination for complex CNC solutions.
---
## Advanced Material Application Enhances Machining Durability and Precision
Chinese CNC manufacturers are pioneers in applying advanced materials to produce durable and high-precision components, especially in sectors demanding high-performance materials like aerospace, medical, and energy. Their proficiency in working with difficult-to-machine materials such as titanium alloys, superalloys, ceramics, and composites significantly enhances the lifespan and performance of the finished parts.
Handling such materials requires specialized tools, cutting parameters, and cooling techniques to prevent deformation and achieve desired surface finishes. Chinese manufacturers are well-versed in these challenges, investing in high-quality tooling and coolant systems to optimize machining processes. This expertise allows them to extend tool life, reduce waste, and improve overall efficiency.
Material versatility is another strength. They adapt to various project requirements by selecting the most suitable materials to meet specific operational demands. For instance, aerospace components often demand lightweight yet robust alloys, while medical devices require biocompatible materials with high precision.
Moreover, their experience with advanced materials enables them to develop innovative solutions like functionally graded materials or composite components, which are increasingly demanded by high-tech industries. This capability involves precise control of material properties during machining, often requiring multi-step processes and specialized techniques.
The application of advanced materials also involves thorough testing and quality assurance to confirm mechanical properties, surface integrity, and dimensional accuracy. Chinese manufacturers utilize non-destructive testing, ultrasonic analysis, and microscopy to ensure material performance aligns with industry standards.
Overall, mastery in advanced material application not only boosts the durability of machined parts but also enhances their functional precision, making Chinese CNC manufacturers valuable partners in high-stakes, high-performance industries.
---
## Overcoming Difficulties in High-Precision CNC Manufacturing Processes
High-precision CNC manufacturing often involves overcoming significant technical challenges. Chinese manufacturers have demonstrated exceptional problem-solving capabilities in tackling these difficulties, which range from material constraints to complex geometries.
One common challenge is achieving tight tolerances on intricate, small-scale features. Overcoming this requires not only advanced equipment but also rigorous process calibration and environmental control to minimize vibrations, thermal expansion, and other variables that could compromise accuracy.
Another challenge involves machining hard or exotic materials that tend to wear out tools quickly or cause deformation. Chinese firms address this by utilizing specialized cutting tools, optimized cutting parameters, and innovative cooling techniques like cryogenic or minimum quantity lubrication (MQL). These approaches extend tool life and maintain precision.
Difficult geometries, such as deep cavities or complex contours, demand multi-axis machining strategies. Chinese manufacturers incorporate high-precision multi-axis machines capable of angled and simultaneous movements, enabling the production of sophisticated shapes with consistent accuracy.
Furthermore, managing residual stresses and deformation during machining is crucial. They employ finite element analysis (FEA) and other simulation tools during the planning stage to predict and mitigate these issues proactively.
Automation and real-time monitoring play vital roles in overcoming manufacturing difficulties. Sensors detect deviations during machining, allowing immediate adjustments that prevent errors and scrap. This continuous feedback loop ensures high-quality output even in complex projects.
In essence, Chinese CNC companies leverage a combination of technological sophistication, process optimization, and problem-solving expertise to surmount the toughest manufacturing challenges, maintaining their reputation for delivering precise and complex components.
---
## Extensive Experience Drives Innovation in Complex Machining Solutions
Experience is a vital asset for Chinese CNC manufacturers, especially when it comes to complex and high-precision machining projects. Decades of accumulated knowledge allow these companies to innovate continuously, developing new techniques and refining existing processes.
Their extensive experience enables them to understand the subtle interplay between material properties, tooling, machine capabilities, and environmental conditions. This holistic understanding translates into optimized machining strategies that improve efficiency and accuracy.
Many Chinese CNC companies have built their expertise on working with a wide variety of industries and materials, giving them a broad perspective on potential problems and innovative solutions. This cross-industry exposure fosters creativity and adaptability in tackling unique challenges.
Experience also translates into better risk management. Veteran engineers can foresee potential issues early in the project lifecycle, adjusting parameters or suggesting alternative approaches that prevent costly errors or delays. Their familiarity with complex geometries and materials allows for smoother project execution.
Furthermore, these companies invest in ongoing training and knowledge transfer, ensuring that their workforce remains at the forefront of technological developments. Such continuous learning fuels innovation, from adopting new cutting-edge equipment to implementing advanced software tools.
Case studies of challenging projects—like ultra-precision medical implants or aerospace engine parts—highlight the depth of expertise Chinese manufacturers possess. Their ability to consistently deliver successful outcomes fosters trust and long-term collaborations with global clients.
In the rapidly evolving landscape of high-precision manufacturing, experience remains a key driver of innovation, empowering Chinese CNC firms to meet increasing demands for complexity and accuracy.
---
## Analyzing Global Case Studies of Challenging CNC Projects
Examining global case studies reveals how Chinese CNC manufacturers tackle some of the most challenging machining problems faced by international clients. These examples showcase their problem-solving capabilities, technological adaptability, and commitment to quality.
One notable case involved manufacturing micro-components for medical devices with extremely tight tolerances and complex geometries. Chinese firms utilized ultra-precision CNC machines combined with cleanroom environments, successfully meeting stringent industry standards and delivering consistent results.
In another project, a client from the aerospace sector required turbine blades made from Ni-based superalloys. The Chinese manufacturer employed high-pressure cooling systems and specialized tools, overcoming the difficulties posed by the material's toughness and thermal sensitivity. The result was durable, high-precision parts that performed reliably under extreme conditions.
A particularly challenging case involved machining deep cavities in aerospace structural components. Chinese firms adopted multi-axis high-speed machining centers and used advanced simulation software to optimize toolpaths, ensuring that the complex shapes were machined accurately without deformation or defects.
Similarly, the production of complex prototypes with intricate internal channels for fluid flow demanded innovative approaches. Chinese manufacturers combined additive manufacturing insights with traditional CNC techniques, creating hybrid processes that achieved desired geometries and surface finishes.
These case studies demonstrate that Chinese CNC companies are not only capable of meeting difficult technical specifications but also excel at customizing solutions for diverse industries worldwide. Their strategic use of technology and experience enables them to solve complex problems efficiently.
By continually analyzing and learning from such challenging projects, Chinese manufacturers push the boundaries of what's possible in high-precision CNC machining, cementing their position as global leaders.
---
## Precision Engineering: Achieving Tolerance in Complex Components
Precision engineering lies at the heart of complex CNC manufacturing. Achieving narrow tolerances in intricate parts requires meticulous attention to detail at every stage of production. Chinese manufacturers excel in this domain through rigorous process control and sophisticated measurement techniques.
They begin with precise design interpretation, utilizing advanced CAD/CAM software to generate optimized toolpaths that account for material behavior and machine dynamics. This precision planning minimizes deviations during machining.
During production, the use of high-quality, multi-axis CNC machines equipped with closed-loop feedback systems maintains tight tolerances. These machines constantly monitor position and adjust in real-time to counteract any deviations caused by thermal expansion, vibration, or tool wear.
Inspection plays a critical role. Chinese firms employ state-of-the-art coordinate measuring machines (CMM), laser scanners, and optical systems to verify dimensions at multiple points. This allows for immediate correction and ensures each component meets the specified tolerances.
The integration of statistical process control (SPC) techniques helps monitor variations and identify trends over time. Such data-driven approaches enable proactive adjustments, reducing scrap rates and increasing yield.
Material stability and environmental control also influence tolerances. Many manufacturers operate in climate-controlled environments to prevent temperature fluctuations from affecting dimensional accuracy.
Achieving such high levels of precision consistently distinguishes Chinese CNC manufacturers in competitive markets. Their expertise in the nuances of precision engineering ensures clients receive components that perform reliably in the most demanding applications.
---
## How Chinese CNC Companies Tackle Material Versatility and Special Alloys
The ability to machine a wide range of materials, including special alloys and composites, is a key factor behind China's competitive edge in CNC manufacturing. Chinese firms have developed extensive expertise in handling diverse materials, adapting their techniques accordingly.
Working with materials like titanium, Inconel, stainless steels, ceramics, and composites requires specialized tooling, cutting strategies, and coolant systems. Chinese companies invest in high-performance tools such as polycrystalline diamond (PCD), cubic boron nitride (CBN), and carbide tools designed for tough materials.
They also optimize cutting parameters—speed, feed, and depth—to balance productivity with tool life and surface quality. For example, machining superalloys involves slower feeds and high-pressure cooling to prevent overheating and deformation.
Material-specific challenges, like work-hardening or chip removal difficulty, are addressed through customized fixturing, multi-step machining processes, and the use of ultrasonic or laser-assisted cutting techniques. This ensures precision while minimizing tool wear.
In addition, Chinese manufacturers stay updated on the latest advancements in material sciences, enabling them to machine newer alloys and composite materials efficiently. They also develop proprietary processes and coatings to enhance machining performance.
Their versatility extends to fabricating parts for demanding environments—marine, aerospace, medical—that require materials with exceptional strength, corrosion resistance, or biocompatibility. This breadth of material capability makes them a go-to partner for complex, high-performance components.
Ultimately, their mastery of material versatility allows Chinese CNC firms to meet the rigorous standards of international clients across various high-tech industries.
---

In recent years, Chinese CNC manufacturers have gained a formidable reputation on the global stage for their exceptional capabilities in high-precision and complex machining. As the demand for intricate components in industries like aerospace, medical devices, and automotive continues to grow, these manufacturers have risen to the challenge by integrating advanced technology, extensive experience, and innovative processes. Their ability to customize parts according to detailed specifications, handle difficult materials, and deliver consistent quality positions them as key players in the global CNC landscape. This article explores how Chinese CNC companies excel in these areas, highlighting their strategic approaches, technological advancements, and commitment to quality.
## The Role of Cutting-Edge Technology in Complex CNC Manufacturing
The adoption of cutting-edge technology is integral to Chinese CNC manufacturers’ success in complex machining. Advanced machinery, software, and automation tools enable them to produce intricate parts with unmatched precision and efficiency.
High-speed multi-axis machining centers are standard, capable of executing complex geometries in a single setup. These machines reduce production time, improve accuracy, and allow for complex contouring that would be impossible with traditional tools.
Innovations in CNC control systems, incorporating AI and machine learning algorithms, enable real-time process optimization. These systems can predict tool wear, adjust cutting parameters dynamically, and ensure consistent quality throughout production runs.
Additive manufacturing integration is another emerging trend. Chinese firms combine CNC machining with 3D printing to create hybrid processes, allowing for rapid prototyping and complex internal features that traditional machining cannot achieve alone.
Advanced simulation software plays a vital role. Before machining begins, digital twins and FEA models help optimize toolpaths and predict potential issues, reducing trial-and-error and material waste.
Inspection technology has also evolved with the use of laser scanners and inline measurement systems that provide immediate feedback, ensuring parts meet strict tolerances.
Furthermore, Industry 4.0 principles—smart factories, data analytics, IoT connectivity—are being implemented to streamline operations, enhance traceability, and foster continuous improvement.
These technological innovations collectively empower Chinese CNC manufacturers to handle the most complex machining tasks efficiently, reliably, and to the highest standards.
---
## Collaboration and Customization: Meeting Unique Client Requirements
Chinese CNC manufacturers excel in fostering collaborative relationships with clients, allowing for highly customized solutions. Their approach involves understanding the client's specific needs, application context, and quality expectations.
They often engage in early-stage design consultations, offering suggestions to improve manufacturability while maintaining functionality. This collaborative process ensures that complex parts are not only feasible to produce but optimized for performance and cost-effectiveness.
Customization extends beyond geometry; material selection, surface finishing, and coating options are tailored to meet environmental, mechanical, or cosmetic requirements dictated by international standards.
Many Chinese firms operate flexible manufacturing cells capable of rapid changeover, enabling small batch runs and prototypes that allow clients to test and iterate designs quickly.
Open communication channels and transparent project management practices foster trust and ensure that any issues are addressed promptly. Clients receive detailed documentation, including inspection reports and process data, for traceability and compliance.
They also provide after-sales support, such as technical advice on assembly or maintenance, further customizing their services to meet long-term client needs.
By emphasizing collaboration and customization, Chinese CNC companies deliver high-value, precision-engineered parts that precisely match client specifications, leading to successful partnerships and repeat business.
---
## Quality Control and Inspection Ensuring Consistent Precision Output
Quality control is fundamental to the reputation of Chinese CNC manufacturers, especially when producing complex components with tight tolerances. They employ rigorous inspection protocols at every stage to maintain consistent precision.
Initial inspections involve verifying incoming materials against certifications and testing for defects. During machining, inline measurement systems monitor critical dimensions in real-time, allowing immediate adjustments if deviations are detected.
Post-process inspection utilizes advanced equipment such as coordinate measuring machines (CMM), laser scanners, and optical comparators. These tools assess dimensional accuracy, surface finish, and geometric tolerances with high precision.
Data collected from inspections are analyzed statistically to identify process variations and implement corrective measures proactively. Many companies operate a quality management system certified to ISO 9001 or similar standards, ensuring systematic adherence to quality protocols.
Additionally, non-destructive testing methods like ultrasonic inspection and X-ray are used for critical aerospace or medical parts to detect internal flaws or stresses that could compromise performance.
Traceability is emphasized, with detailed records maintained for each batch, facilitating audits and compliance with international standards. This meticulous approach ensures that every component leaving the factory meets or exceeds client expectations.
The outcome is a robust quality assurance system that guarantees precision, reliability, and repeatability in high-stakes applications, reinforcing China's position as a reliable source of complex CNC machined parts.
---
## Future Trends in Chinese CNC Machining for High-Precision Applications
Looking ahead, Chinese CNC manufacturing is poised to embrace several innovative trends that will further enhance their capabilities in high-precision and complex machining. Integration of Industry 4.0 concepts, such as smart factories and IoT, will enable more intelligent and autonomous production environments.
The adoption of artificial intelligence and machine learning algorithms will refine process optimization, predictive maintenance, and quality control, reducing downtime and enhancing accuracy. This will be especially beneficial for producing highly complex components with minimal errors.
Advances in additive manufacturing combined with traditional CNC machining will open new avenues for creating intricate geometries, internal channels, and lightweight structures, expanding design possibilities for sectors like aerospace and medical implants.
Material science developments will enable Chinese firms to work with emerging high-performance alloys and composites, further expanding their application scope in demanding industries.
Sustainability initiatives, including eco-friendly cutting fluids, energy-efficient machines, and waste reduction strategies, will become standard, aligning manufacturing practices with global environmental standards.
Moreover, greater emphasis on digital twin technologies and virtual prototyping will improve design for manufacturability, reducing lead times and costs.
Finally, strengthening global collaborations and knowledge sharing will accelerate innovation and ensure Chinese CNC manufacturers stay at the forefront of high-precision machining, meeting the evolving needs of international markets.
---
##
Chinese CNC manufacturers have established themselves as leaders in high-precision and complex machining through their extensive experience, technological innovation, and relentless pursuit of quality. Their ability to customize intricate parts, work with diverse materials, and overcome manufacturing challenges underscores their pivotal role in supporting global industries demanding the highest standards of precision. As they continue to adopt advanced technologies and embrace future trends, Chinese CNC companies are well-positioned to shape the next era of high-tech manufacturing. Their commitment to excellence not only drives industry innovation but also solidifies China's reputation as a global hub for top-tier CNC machining solutions.