High-Precision Custom CNC Machining for Fluid Control Components
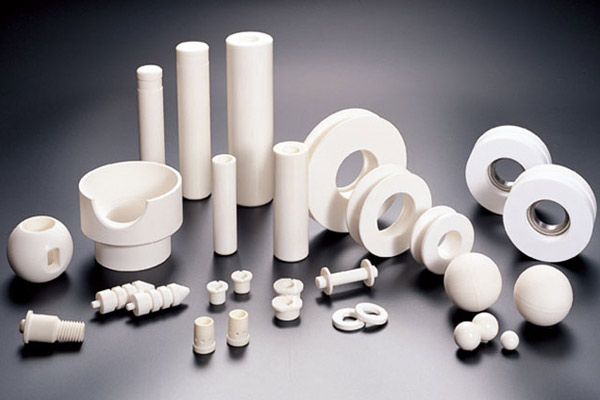
===INTRO:===
In the realm of fluid control systems, precision isn’t just a desirable trait—it’s a necessity. Industries such as aerospace, medical devices, automotive, and chemical processing demand high-precision fluid control components that operate reliably under stringent conditions. As the complexity of these systems increases, so does the need for custom CNC machining solutions capable of delivering intricate, durable, and highly accurate parts. This article explores the critical role of high-precision custom CNC machining in manufacturing fluid control components, highlighting how advanced techniques and materials meet industry demands for precision, quality, and performance.
The Growing Demand for High-Precision Fluid Control Components in Industry
The modern industrial landscape is characterized by rapid technological advancements and increasingly complex systems. Fluid control components—such as valves, regulators, flow meters, and pumps—are integral to these systems, ensuring the precise regulation of liquids and gases. As applications become more sophisticated, the standards for the components’ accuracy, durability, and reliability escalate accordingly.
Industries like aerospace require components that can withstand extreme conditions while maintaining tight tolerances for safety and performance. In medical devices, minuscule deviations can compromise patient safety, making precision paramount. Automotive systems depend on fluid control parts that must operate flawlessly over millions of cycles. Chemical processing plants need components resistant to corrosive substances, with precise dimensions to prevent leaks or malfunctions.
This heightened demand drives the need for custom CNC machining solutions that can produce intricate geometries with tight tolerances. The ability to tailor parts to specific applications offers manufacturers a competitive edge, enabling them to meet unique industry standards and compliance requirements. As a result, high-precision CNC machining has become a cornerstone in the production of fluid control components.
The trend toward miniaturization and integration further amplifies this need. Smaller components with complex internal passages require advanced CNC techniques capable of achieving fine details and consistent quality. Consequently, manufacturers investing in high-precision CNC machining can ensure their fluid control parts not only meet current demands but are also adaptable for future innovations.
Furthermore, the shift toward automation and Industry 4.0 has emphasized the importance of reproducibility and quality control in manufacturing. High-precision CNC machining facilitates this with advanced software, real-time monitoring, and automation, ensuring every component produced adheres to strict specifications. As industries continue evolving, the demand for high-precision, custom CNC-machined fluid control parts will only intensify.
In essence, the critical importance of fluid control components across diverse sectors underscores the need for manufacturing processes capable of meeting exacting standards. High-precision CNC machining emerges as the ideal solution—combining technological sophistication with manufacturing flexibility—to deliver components that uphold safety, reliability, and performance.
Overcoming Manufacturing Challenges with Advanced CNC Machining Solutions
Producing fluid control components with high precision presents several manufacturing challenges. Achieving tight tolerances, complex geometries, and superior surface finishes requires advanced equipment, skilled craftsmanship, and meticulous quality control.
One primary challenge is machining intricate internal features such as micro-channels, orifices, and precise threads, often with diameters less than a millimeter. Traditional manufacturing methods may struggle to produce these features with the necessary accuracy or may result in high rejection rates. CNC machining, especially when combined with multi-axis capabilities, overcomes this by allowing complex geometries to be machined in a single setup, reducing errors and improving efficiency.
Material selection poses another challenge. Many fluid control components require materials that are corrosion-resistant, lightweight, or capable of withstanding extreme pressures and temperatures. Machining these materials—such as stainless steel, brass, titanium, or specialized plastics—requires specific cutting tools and parameters to prevent deformation, cracking, or surface defects. Advanced CNC machines equipped with adaptable tooling systems enable precise machining across diverse materials.
Surface finish quality is critical in fluid control parts to prevent leaks and ensure smooth flow. Achieving mirror-like finishes on complex geometries demands sophisticated tooling, optimized cutting parameters, and sometimes post-processing. CNC machines with high spindle speeds, rigid tool holders, and multi-axis movement facilitate achieving these finishes consistently.
Another challenge is maintaining consistent tolerances across large production runs. Variations in machine calibration or tool wear can lead to dimensional discrepancies. High-precision CNC machines feature real-time feedback systems, such as laser or touch probes, allowing for immediate adjustments and ensuring each part remains within strict tolerances.
With the integration of Industry 4.0 technologies, manufacturers now leverage data analytics, predictive maintenance, and automation to minimize downtime and defects. Automated inspection systems, integrated directly into the machining process, can detect deviations early, reducing waste and rework.
Lastly, compliance with industry standards and certifications—such as ISO, ASME, or CE—adds complexity. Advanced CNC machining centers equipped with traceability features enable manufacturers to document every step of production, ensuring adherence to strict regulatory requirements. These integrated solutions collectively help overcome manufacturing challenges, delivering precise, reliable fluid control components at scale.
Key Materials Used in Custom CNC Machining of Fluid Control Parts
Selecting the right material is fundamental to the performance and longevity of fluid control components. Different applications demand materials that can withstand specific environmental conditions, such as corrosion, high pressure, or temperature extremes. Custom CNC machining supports a wide array of materials tailored to diverse needs.
Stainless Steel is one of the most commonly used materials in fluid control components due to its excellent corrosion resistance, strength, and durability. Grades such as 316 and 17-4 PH are popular choices, especially in applications involving aggressive fluids or humid environments. CNC machining stainless steel requires high-quality tools and precise control to prevent work hardening and achieve smooth finishes.
Brass is favored for its excellent machinability and corrosion resistance, particularly in water and low-pressure applications. Its ease of machining makes it suitable for producing complex geometries quickly. Brass components are often used in valves, fittings, and flow regulators where moderate strength suffices.
Titanium offers a combination of high strength-to-weight ratio, corrosion resistance, and biocompatibility, making it ideal for medical and aerospace fluid control parts. Machining titanium requires specialized tooling and cooling strategies due to its tendency to gall and work harden, but CNC machines are well-equipped to handle these challenges.
Plastic materials such as PTFE (Teflon), PEEK, and PVDF are used when chemical resistance, low friction, or electrical insulation is needed. These plastics are lightweight and can be machined to tight tolerances using CNC methods. They are especially valuable in chemical processing or medical applications where metal contamination must be avoided.
Specialized alloys, like Monel or Hastelloy, are employed in highly corrosive environments. While more challenging to machine, these materials can be processed with advanced CNC equipment equipped with hardened cutting tools and optimized parameters.
Beyond material selection, surface treatment processes such as passivation, anodizing, or coating are often applied post-machining to enhance corrosion resistance or reduce friction further. The ability of CNC machining to work with these diverse materials allows manufacturers to customize fluid control components precisely to their client’s specifications and application demands.
Choosing the appropriate material involves considering factors like operating pressure, temperature range, chemical exposure, and mechanical stress. CNC machining’s flexibility ensures that each material is machined to achieve optimal performance, reliability, and lifespan for fluid control systems.
Showcasing Our Precision: Tolerance, Equipment, and Quality Assurance
Our commitment to high-precision CNC machining of fluid control components is reflected in our rigorous quality standards, advanced equipment, and meticulous attention to tolerances. We understand that even the tiniest deviation can compromise the function and safety of fluid control systems.
Our CNC machining centers are equipped with multi-axis capabilities, including 3-, 4-, and 5-axis machines, allowing us to produce complex geometries and internal features with exceptional accuracy. These machines enable high-volume manufacturing while maintaining tight tolerances of ±0.005mm or better, suitable for critical fluid control applications.
We utilize advanced software such as CAD/CAM systems for precise programming, ensuring that each part is designed and manufactured to exact specifications. Real-time monitoring tools—including laser measurement systems and touch probes—are integrated into our machinery to detect deviations early, minimizing inaccuracies and waste.
Our quality assurance processes are comprehensive. Every component undergoes thorough inspection using coordinate measuring machines (CMM), optical comparators, and surface finish analyzers. These inspections verify dimensional accuracy, surface quality, and conformity to industry standards like ISO 9001 and ASME BPE.
Furthermore, our staff is highly trained in best practices for machining high-precision parts. Continuous training ensures they are proficient with the latest CNC technologies and inspection techniques. We also implement strict process controls and documentation, enabling traceability from raw material sourcing to final inspection.
To meet the demanding standards of industries such as aerospace, medical, and chemical processing, we adhere to strict cleanliness protocols and perform non-destructive testing (NDT) when necessary. This guarantees that every fluid control component leaving our facility performs reliably and adheres to the highest quality benchmarks.
Our focus on precision, coupled with state-of-the-art equipment and quality systems, ensures we deliver fluid control parts that meet the most stringent tolerances. This guarantees optimal performance, longevity, and safety for your critical systems.
Common Fluid Control Components and Their Critical Applications
Fluid control systems encompass a variety of components, each with unique roles and critical specifications. Custom CNC machining enables the production of these parts with precise dimensions and complex features tailored to their specific applications.
Valves are perhaps the most common fluid control components, regulating flow, pressure, and direction of fluids within a system. CNC-machined valves, such as globe, ball, or needle valves, require tight tolerances to prevent leaks and ensure smooth operation, especially in high-pressure environments like oil and gas or aerospace.
Flow meters measure the volume or mass of fluids passing through a system. Precise internal geometries and smooth surface finishes are essential for accurate readings. CNC machining allows for the creation of complex internal features like micro-channels and precise orifices that are critical for measurement accuracy.
Regulators control pressure levels within fluid systems, ensuring consistent operation. They often include precision-machined diaphragms, springs, and adjustment mechanisms. Achieving these intricate features requires advanced CNC techniques and tight dimensional control.
Pumps and pump components facilitate fluid movement, often requiring tight clearances and durable materials. Impellers and housings are custom-machined to ensure efficiency and longevity, especially under demanding conditions like chemical exposure or high temperatures.
Fittings and connectors serve as interfaces between different system parts, necessitating high-precision threads and sealing surfaces. CNC machining ensures these parts fit perfectly, minimizing leakage and assembly issues.
In critical applications, such as medical devices, aerospace, or chemical processing, the integrity of these components determines overall system safety and efficiency. High-precision CNC machining enables the production of parts that conform to strict specifications, operate reliably under adverse conditions, and meet regulatory standards.
Understanding the specific functions and environmental requirements of each component guides the material selection, design, and manufacturing process. This tailored approach ensures that each fluid control part performs optimally within its intended application, reducing downtime and maintenance costs.
As fluid control systems evolve toward greater complexity and miniaturization, the importance of precision machining becomes even more evident. Custom CNC machining offers the flexibility and accuracy required to meet these modern demands, ensuring your components are of the highest quality and performance.
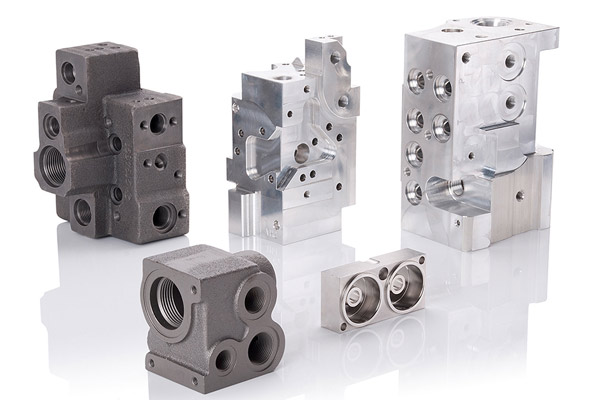
Custom machining of high-precision parts for fluid control
Partnering with Us: Success Stories in Custom CNC Machining Projects
Our expertise in high-precision custom CNC machining for fluid control components has helped numerous clients achieve their project goals efficiently and reliably. From initial design consultation to final inspection, we provide comprehensive support tailored to each application.
One notable success involved producing complex stainless steel valves for a chemical processing plant. Our team utilized multi-axis CNC machines to machine intricate internal passages with tight tolerances of ±0.002mm. The result was a leak-proof, corrosion-resistant valve that exceeded client expectations for durability and performance.
In the medical industry, we partnered with a manufacturer of implantable flow regulators. Using biocompatible titanium, we achieved micron-level internal features and smooth surface finishes critical for patient safety. Our precise machining and rigorous quality control ensured compliance with medical standards and accelerated their time-to-market.
A leading aerospace company entrusted us with fabricating lightweight fluid control components from titanium alloys. Our advanced CNC equipment enabled high-precision machining of thin-walled structures with complex internal channels, all while maintaining strict dimensional tolerances essential for flight safety.
For a custom flow meter project in the automotive sector, we developed micro-channel geometries from high-performance plastics. The parts required exceptional surface finishes and precise internal features to ensure accurate measurements under dynamic conditions. Our process optimization resulted in high yield and consistent quality.
These success stories exemplify our capability to handle diverse materials, complex geometries, and stringent industry standards. Our dedicated team collaborates closely with clients, providing design suggestions, material recommendations, and process optimizations to ensure optimal outcomes.
Partnering with us means gaining a reliable manufacturer committed to quality, precision, and innovation. Whether it’s a small prototype or large-scale production, our advanced CNC machining solutions are designed to meet your specific needs, helping you stay competitive in demanding markets.
Contact us today to discuss your fluid control component project and discover how our high-precision CNC machining expertise can bring your ideas to life with unmatched accuracy and quality.
===OUTRO:===
In today’s competitive industrial landscape, delivering reliable, high-precision fluid control components is crucial for success. Through advanced CNC machining technology and a deep understanding of material properties and industry standards, we are committed to providing custom solutions that meet the most demanding specifications. From complex internal geometries to tight tolerances, our capabilities ensure your components perform flawlessly under challenging conditions. Partner with us to accelerate your product development, reduce lead times, and achieve excellence in fluid control systems. Reach out today to explore how our high-precision CNC machining services can elevate your projects and drive your business forward.