High-Precision Grinding and CNC Machining for High-Wear Components
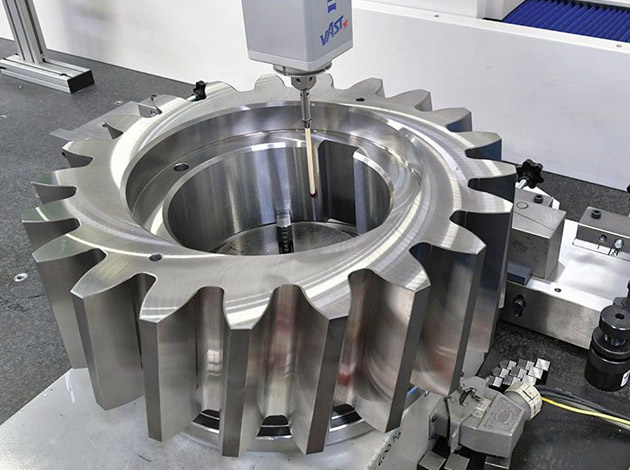
Precision Demands in High-Wear Applications
Industries such as hydraulics, fluid control, aerospace, and high-performance machinery require components that not only meet tight dimensional tolerances but also withstand extreme wear, friction, and pressure over prolonged periods. These critical parts must demonstrate high precision, high surface finish (Ra ≤ 0.02 μm), and exceptional durability.
Manufacturers in these sectors depend on a precision grinding and CNC machining expert capable of delivering high-precision, high-surface-finish, and high-wear-resistance solutions. From valve spools and sleeves to plungers and control rods, these components often operate in harsh environments where failure is not an option. This requires consistent manufacturing excellence, advanced inspection capabilities, and a deep understanding of materials and surface engineering.
Grinding and Machining Challenges — And Our Solutions
Producing components that require micron-level tolerances and mirror-like surface finishes presents unique challenges:
- Maintaining concentricity and roundness across long shaft components;
- Achieving ultra-low surface roughness (Ra ≤ 0.02 μm) to reduce friction and leakage;
- Preventing deformation or residual stress during grinding;
- Managing hard-to-machine materials such as tool steel, tungsten carbide, or ceramics;
- Ensuring high repeatability across production batches.
These challenges are addressed through:
- Swiss and German precision grinding equipment, capable of achieving roundness tolerances ≤ 0.001 mm;
- Cryogenic cooling systems and advanced dressing techniques to control thermal effects;
- Multi-step processing, combining CNC turning, hardening, cylindrical grinding, and lapping;
- Digital twin simulations to optimize tooling and process flow;
- In-process metrology and post-process inspection using roundness testers, CMMs, and surface roughness gauges.
These processes enable us to deliver high-precision, high-surface-quality CNC machined components that meet or exceed demanding application requirements.
Frequently Used Materials and Their Advantages
For parts that demand high wear resistance and dimensional stability, material selection is critical. We commonly work with:
- Tool Steel (e.g., D2, H13, Cr12MoV): Offers high hardness and excellent wear resistance after heat treatment, ideal for valve components and dies.
- Alloy Steel (e.g., 42CrMo, 20CrMnTi): Provides toughness and fatigue resistance, suitable for shafts, sleeves, and spools.
- Stainless Steel (e.g., 440C, 316L, 17-4PH): Combines corrosion resistance with good mechanical properties; commonly used in hydraulic and medical equipment.
- Tungsten Carbide and Ceramic Materials: Extremely hard and wear-resistant; used in plunger sleeves and sealing elements in high-pressure environments.
- Titanium Alloys (e.g., Ti-6Al-4V): Lightweight and corrosion-resistant, ideal for aerospace and marine applications.
All materials are handled with full traceability and undergo heat treatment or surface hardening processes such as nitriding, carburizing, or PVD coatings, depending on the performance requirements.
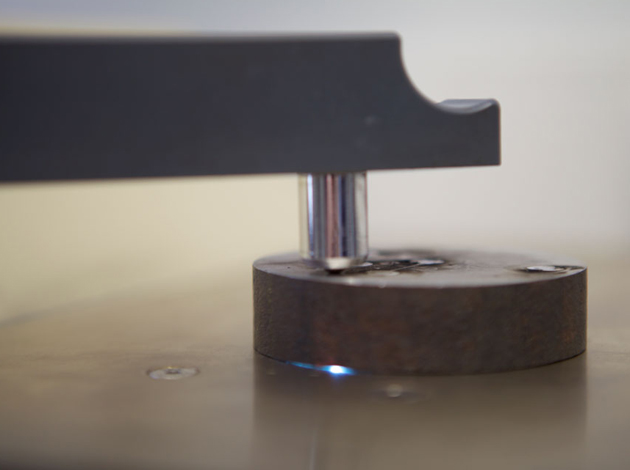
Advanced Grinding & CNC Machining Capabilities
As a high-precision CNC machining and precision grinding expert, we provide end-to-end manufacturing of complex components requiring:
- Tolerances: Down to ±0.001 mm on diameter and length; concentricity ≤ 0.002 mm; roundness ≤ 0.001 mm.
- Surface Finish: Achievable Ra ≤ 0.02 μm using cylindrical grinding, centerless grinding, and lapping.
- Component Sizes: Lengths up to 800 mm; diameters from 2 mm to 200 mm.
- Machining Technologies: Swiss-type CNC turning, multi-axis milling, precision grinding (OD/ID, centerless), EDM, and polishing.
Inspection & Quality Control:
- Zeiss CMMs for 3D tolerance verification;
- Tokyo Seimitsu roundness and cylindricity testers;
- MarSurf surface roughness testers for Ra/Rz evaluation;
- Air gauge systems for bore precision;
- Full dimensional inspection reports and statistical process control available upon request.
Our combination of precision machining, hardening processes, and grinding excellence makes us the go-to solution provider for high-precision, high-surface-finish, high-wear-resistance parts.

Common Components and Industry Applications
We support a wide range of industries with precision-ground and CNC machined parts, including:
- Hydraulic Systems: Valve spools, valve sleeves, plungers, pistons, and control rods for directional, pressure, and flow control.
- Aerospace Actuators: Servo valve spools and sleeves, landing gear bushings, and high-precision shafts.
- Industrial Pumps: Rotor pins, plungers, sealing rods, and guide sleeves.
- Medical Devices: Surgical tool components and dosing pump plungers requiring biocompatible stainless steels and ultra-smooth finishes.
- Fluid Control Valves: Needle valve cones, seats, sleeves, and poppet components requiring precision sealing and alignment.
All parts can be customized based on your technical drawings and specifications. We also offer reverse engineering services for legacy or undocumented parts.
Project Example: High-Precision Valve Spool Assembly
One notable example involved manufacturing a high-precision valve spool and sleeve assembly used in a high-pressure fluid control system. Requirements included:
- Material: 20CrMnTi carburized and hardened to HRC 58–62
- Roundness tolerance: ≤ 0.0015 mm
- Surface roughness: Ra ≤ 0.02 μm
- Concentricity between shaft and bore: ≤ 0.002 mm
- 100% inspection on CMM and air gauges
The finished part passed all high-pressure leak and flow performance tests and helped the customer reduce valve actuation delay by over 20%.
Partner with a Precision Grinding & CNC Machining Expert
When your application demands tight tolerances, exceptional surface quality, and outstanding wear resistance, choose a supplier who specializes in high-precision, high-surface-finish, high-wear-resistance grinding and CNC machining.
With cutting-edge equipment, highly trained technicians, and a deep understanding of materials and applications, we are ready to support your most demanding projects.
👉 Request a Quote Today – From Rough to Mirror Finish, We Deliver Precision That Lasts.