Custom Transmission and Engine Components + CNC Machining — High-Precision Powertrain Solutions for Demanding Applications
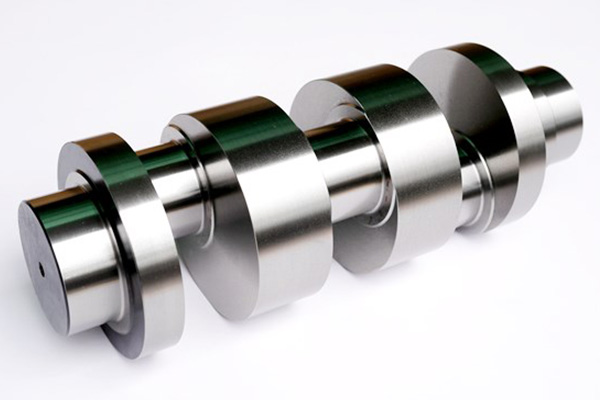
Introduction: The Vital Role of Precision Components in Powertrain Systems
In the automotive, aerospace, heavy machinery, and industrial equipment sectors, transmission and engine systems serve as the heart of mechanical performance. Whether converting fuel into motion or delivering torque through complex gear systems, the components involved must meet the highest standards of dimensional accuracy, wear resistance, and thermal stability. As performance expectations grow and efficiency regulations tighten, the demand for custom transmission and engine components + CNC Machining continues to accelerate.
We offer CNC precision machining solutions for complex powertrain parts — from shafts and gears to housings and flanges — tailored precisely to your engineering drawings, specifications, and industry requirements.
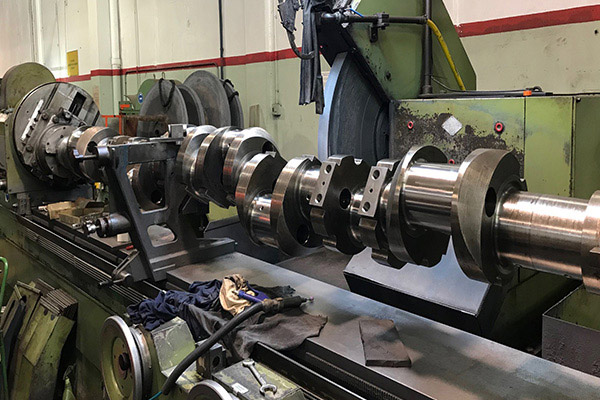
Machining Challenges and Our Solutions
Machining transmission and engine parts presents some of the most rigorous challenges in modern manufacturing:
- High Precision and Functional Tolerances: Parts such as crankshafts, camshafts, and synchronizer hubs must maintain tight geometric tolerances (e.g., ±0.005mm) to ensure smooth rotation, alignment, and longevity.
- Complex 3D Geometries: Components like helical gears, splined shafts, and engine blocks often feature intricate profiles that require multi-axis simultaneous machining.
- Material Hardness and Post-Processing: Many components undergo heat treatment to reach high hardness levels (up to 60 HRC), requiring robust tooling and grinding for final finishing.
- Thermal and Mechanical Loads: Transmission and engine parts operate under extreme conditions — high RPMs, thermal cycling, and mechanical stress — demanding superior material properties and surface treatments.
Our Solution:
We provide a full-service CNC machining workflow, including rough and finish machining, precision grinding, dynamic balancing, and thermal treatment coordination. With 5-axis CNC centers, advanced CAM programming, and high-precision inspection systems, we produce parts that meet both form and function — reliably, efficiently, and repeatably.
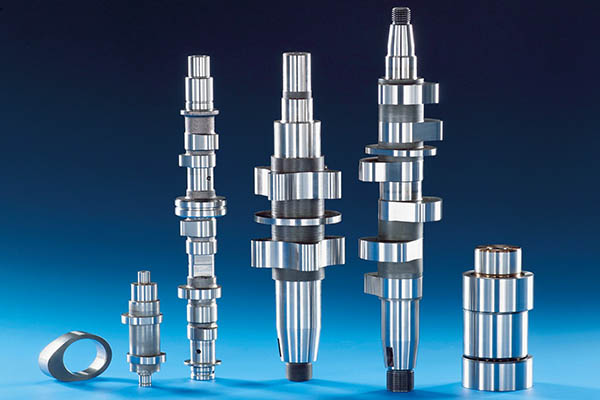
Common Materials and Their Characteristics
Selecting the right material is crucial for achieving optimal performance and durability in powertrain applications. We machine a wide range of transmission and engine-grade materials:
- Alloy Steels (e.g., 4140, 4340, 8620): High strength and toughness; often used for gears, shafts, and couplings.
- Carbon Steels (C45, S45C): Cost-effective for medium-load parts such as flanges, brackets, and covers.
- Stainless Steels (304, 316, 17-4PH): Used in components requiring corrosion resistance or clean-room operation, such as turbo housings or exhaust parts.
- Cast Iron & Ductile Iron: Often chosen for transmission housings and engine blocks due to vibration damping properties and machinability.
- Aluminum Alloys (6061, 7075): Ideal for lightweight engine covers, brackets, and transmission casings in motorsport or aerospace applications.
- Titanium & Inconel (optional for high-performance sectors): Used in extreme environments like aerospace engines or racing systems.
All materials are traceable and available with certifications compliant with ISO, ASTM, or DIN standards.
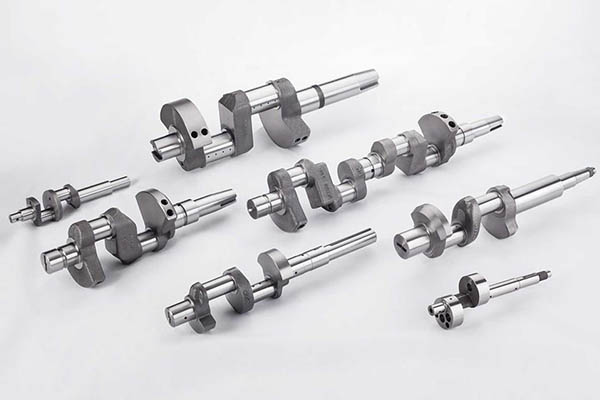
CNC Machining Capabilities
Our capabilities are built to handle the strict demands of powertrain component machining, from prototyping to large-scale production:
- Tolerances and Finish:
- Dimensional tolerance: ±0.005mm or tighter as required
- Surface finish: up to Ra 0.2μm on sealing or rotating surfaces
- Concentricity, perpendicularity, and flatness ensured via full QA
- Equipment Overview:
- 5-Axis CNC Machining Centers: Ideal for complex gear housings and irregular engine parts
- CNC Lathes with Live Tooling: For shaft-type components such as crankshafts and axles
- CNC Cylindrical and Surface Grinders: For post-heat-treatment finishing and bearing fits
- Dynamic Balancing Machines: To ensure rotational stability of high-speed components
- Zeiss CMM & Optical Scanning: For full 3D inspection and report delivery
- Supplementary Processes:
- Heat treatment (quenching, carburizing, nitriding)
- Shot peening, black oxide, or phosphate coating
- Surface hardening and polishing
- Assembly and sub-assembly if required
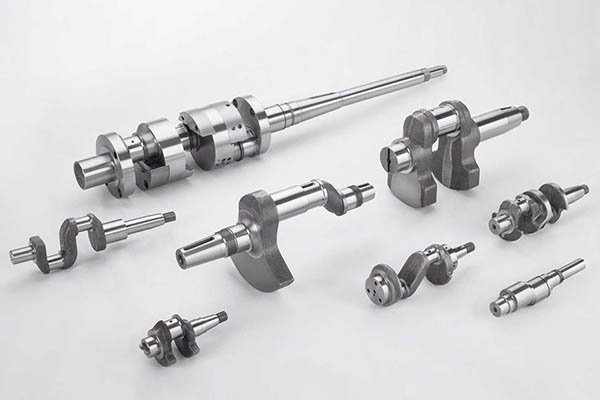
Typical Machined Components and Applications
We manufacture a wide variety of custom transmission and engine components + CNC Machining services across industries:
- Transmission System Parts:
- Gear Shafts & Pinions: Heat-treated and precision-ground
- Differential Housings & Flanges: CNC-milled from alloy steel or cast iron
- Splined Shafts & Couplings: With high-accuracy gear teeth profiles
- Engine System Components:
- Crankshafts & Camshafts: Multi-step machining with tight tolerances on journals
- Cylinder Head & Engine Covers: Complex shapes requiring 5-axis milling
- Valve Seats, Guides & Rocker Arms: Machined from hardened materials for durability
- Support Components:
- Bearings Housings & Oil Seals: Sealing-critical surfaces polished to low Ra values
- Brackets, Mounts & Adapters: Lightweight but rigid, often made from aluminum
These components power vehicles, aircraft, generators, marine systems, and heavy equipment — each requiring absolute reliability and zero tolerance for failure.
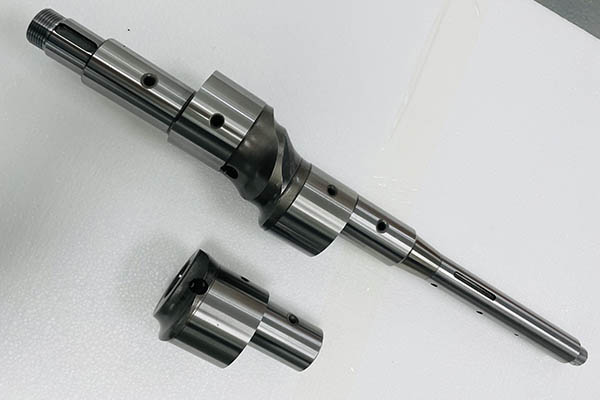
Project Case Study (Optional)
A recent project involved manufacturing a precision ground camshaft and synchronized gear system for a performance vehicle application. The parts, made from 4340 alloy steel, were machined to ±0.003mm tolerances, heat-treated to 58 HRC, and finished via cylindrical grinding. After 100% inspection with CMM, the components were dynamically balanced before delivery. The client reported a 15% increase in RPM tolerance and a measurable improvement in transmission smoothness.
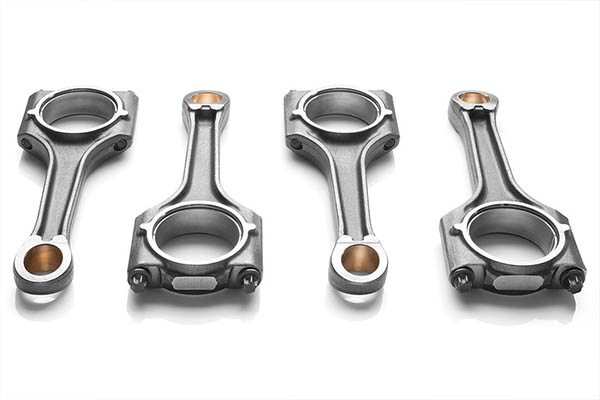
Get Started with Your Custom Transmission & Engine Parts Today
When it comes to custom transmission and engine components + CNC Machining, you need more than just precision — you need a partner who understands fit, function, and long-term performance. We bring advanced equipment, expert technicians, and full QA systems to every project, ensuring parts that perform under the harshest conditions.
Contact us now to get a quote, submit your 3D models or 2D drawings, and discover how we can help bring your powertrain system to life with precision CNC machining.
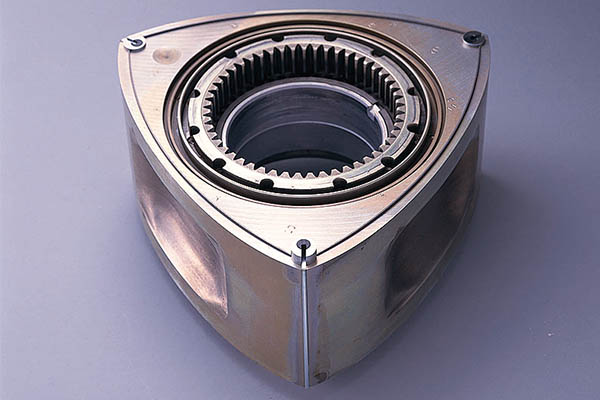
SEO-Embedded Keywords:
custom transmission and engine components + CNC Machining, precision powertrain CNC parts, crankshaft CNC machining, gear shaft manufacturing, ±0.005mm tolerance, 5-axis CNC engine parts, heat-treated alloy steel components, dynamic balancing, high-precision drivetrain machining.
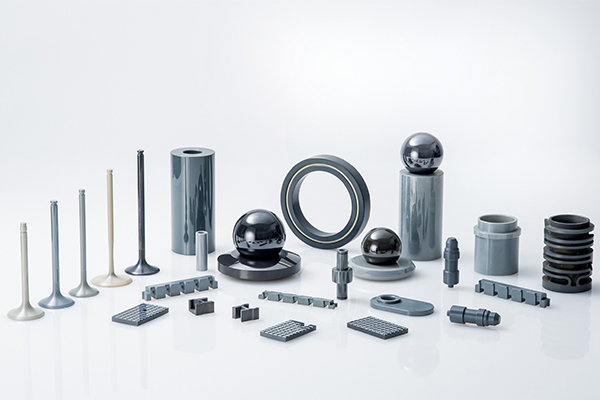