Custom High-Precision Parts + CNC Machining — Ultra-Tight Tolerances for Critical Applications
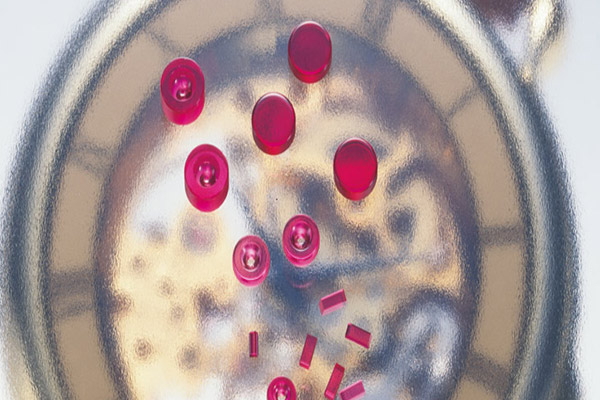
Introduction: The Growing Demand for High-Precision CNC Components
Across industries such as aerospace, medical, optics, semiconductor, and automation, the demand for custom high-precision parts + CNC Machining is reaching new heights. These sectors rely on components that meet exceptionally tight tolerances, often within microns, to guarantee reliable performance, safety, and efficiency. Whether for mission-critical assemblies or nano-level positioning mechanisms, the precision of each part directly impacts the function of the whole system.
Our CNC machining services are engineered to meet the most demanding quality standards, supporting custom part production based on your drawings, 3D models, or technical specifications. With decades of machining experience and a deep understanding of materials and tolerances, we provide ultra-precise components that consistently meet and exceed customer expectations.
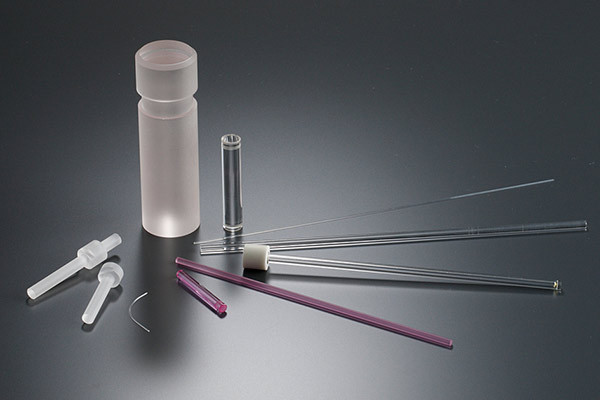
Machining Challenges and Our Solutions
Manufacturing ultra-high-precision parts presents a number of complex challenges that go beyond standard machining:
- Tight Tolerance Control: Many high-end applications require dimensional tolerances of ±0.001mm or less, with strict geometric tolerances (roundness, flatness, concentricity) and surface roughness specifications.
- Challenging Materials: Materials like hardened tool steels, titanium alloys, ceramics, and engineering plastics can be difficult to machine without introducing thermal distortion, burrs, or surface degradation.
- Complex Geometries and Micro Features: Parts often feature intricate internal channels, micro holes, and non-standard forms that require multi-axis interpolation and advanced CAM programming.
- Measurement and Verification: Traditional gauges are not enough. High-precision metrology tools are required to validate tolerances consistently and ensure zero-defect delivery.
Our Solution:
We deploy a combination of 5-axis CNC machining, ultra-precision grinding, EDM, and micro-milling techniques, combined with stringent quality control using CMMs, laser scanners, and optical comparators. Our climate-controlled inspection lab ensures all measurements remain stable and accurate. Every part is produced under strict process control and delivered with full inspection documentation upon request.
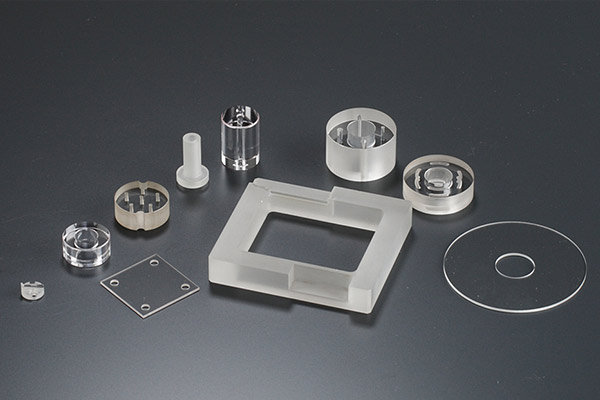
Common Materials and Their Characteristics
To meet the functional and environmental demands of high-precision parts, we work with a diverse range of advanced materials:
- Tool Steels (D2, H13, S136): Commonly used for wear-resistant components requiring high hardness and dimensional stability.
- Titanium Alloys (Ti-6Al-4V): Lightweight, high-strength, and corrosion-resistant—ideal for aerospace, medical, and optical components.
- Stainless Steels (304, 316L, 17-4PH): Corrosion-resistant and biocompatible, perfect for medical and semiconductor applications.
- Ceramics (Zirconia, Alumina): Excellent for insulation, wear resistance, and temperature tolerance. Often used in optical and chemical equipment.
- Aluminum Alloys (6061, 7075): Lightweight and easy to machine, ideal for structural components where tight tolerances are critical.
- High-Performance Plastics (PEEK, PTFE, Delrin): Used for chemical resistance, insulation, or frictionless environments in laboratory and medical systems.
Each material is selected based on its suitability for specific operating environments, whether involving heat, friction, chemicals, or hygiene.
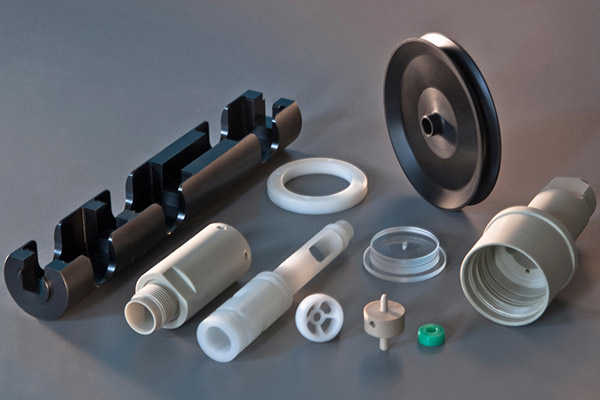
CNC Machining Capabilities
We offer end-to-end capabilities to meet the most stringent high-precision part requirements:
- Tolerances and Finish:
- Dimensional: ±0.001mm, roundness/flatness ≤ 0.002mm
- Surface Finish: As smooth as Ra 0.02μm
- Concentricity/Perpendicularity: Validated via CMM and roundness instruments
- Equipment and Technology:
- 5-Axis CNC Machining Centers (Mikron, Hermle): For complex multi-sided parts
- Ultra-Precision Grinding (Studer, Okamoto): For roundness-critical components
- EDM and Wire Cutting: Ideal for internal contours, sharp corners, and hard materials
- Micro-Drilling and Milling: Hole diameters as small as 0.1mm
- Zeiss CMM and Roundness Testers: For full geometric inspection
- Cleanroom Packaging: For optical, medical, or semiconductor-ready parts
- Certifications and QA:
- Full traceability and inspection reports
- PPAP, FAI, and material certifications available on request
- ISO-compliant processes and documentation
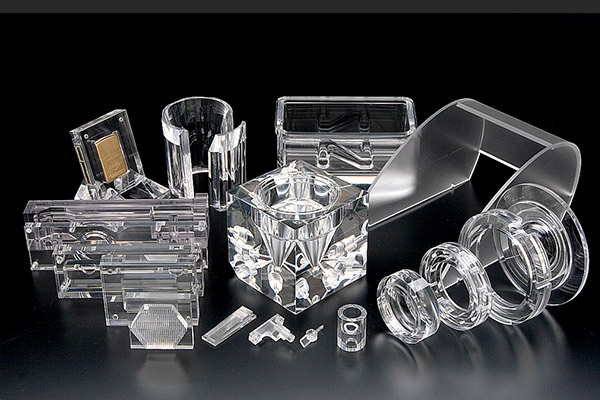
Common CNC Machined High-Precision Parts
We manufacture a wide range of custom high-precision parts + CNC Machining for specialized applications:
- Optical Components: Lens holders, sensor mounts, and ceramic isolation rings with high reflectivity and tight concentricity.
- Medical and Lab Devices: Surgical instruments, pump rotors, and diagnostic system parts requiring cleanroom-ready finishes and biocompatibility.
- Semiconductor Equipment: Wafer handling fixtures, ceramic bushings, and ultra-flat positioning plates.
- Aerospace and UAV Components: Lightweight titanium shafts, precision bearings housings, and alignment-sensitive brackets.
- Measurement Instruments: Dial gauge frames, probe arms, and micro-adjustment devices with zero play.
- Automation and Robotics: Sensor mounts, end effectors, and encoder plates requiring micro-tolerances and repeatable geometry.
Each part is manufactured according to client-supplied drawings or CAD data and optimized for function, manufacturability, and cost-efficiency.
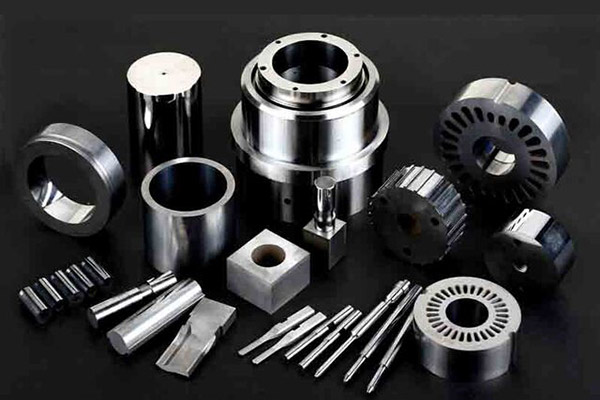
Client Project Example (Optional)
One recent project involved producing a set of ultra-flat ceramic optical rings with a surface roughness of Ra 0.02μm and parallelism under 0.001mm. The components were used in a high-end optical alignment system and required high-temperature insulation, chemical resistance, and extreme dimensional accuracy. Our advanced grinding and polishing workflow delivered flawless results — exceeding the customer’s requirements and reducing their alignment calibration time by over 30%.
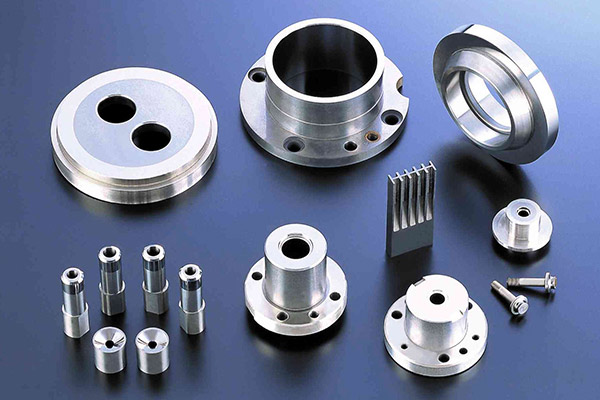
Partner with a High-Precision CNC Machining Specialist
When failure is not an option, trust a manufacturing partner that delivers absolute accuracy. We are your reliable source for custom high-precision parts + CNC Machining, combining world-class equipment, certified processes, and decades of technical experience.
Contact us today to upload your technical drawings or 3D files. Our engineering team will analyze your design, recommend optimal materials and processes, and provide a rapid, accurate quotation.
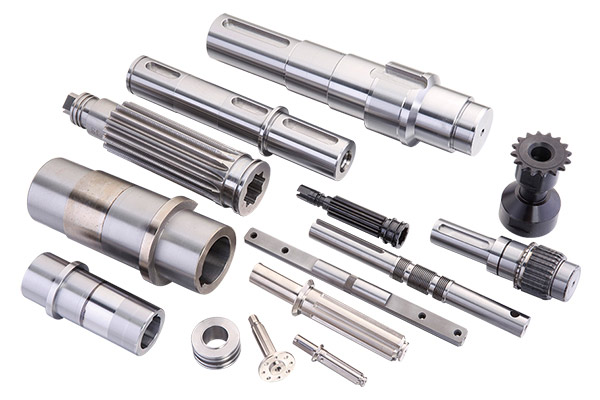