Precision Manufacturing for Cold Heading & Fastening: China’s Competitive Edge in High-Performance Tooling and Components
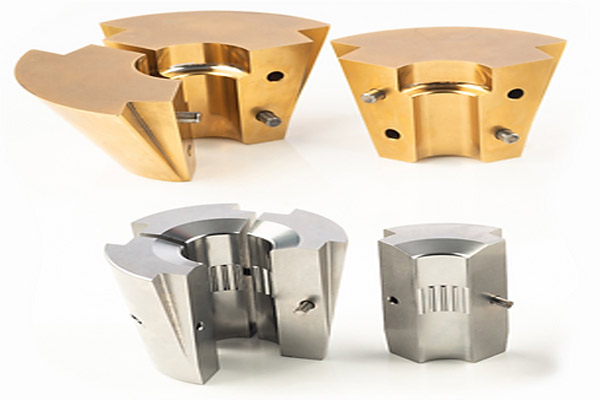
The cold heading and fastening industry forms the backbone of countless products across automotive, aerospace, construction, and electronics. From micro fasteners for consumer electronics to high-strength bolts in structural steel, the demand for dimensional precision, mold durability, and production efficiency is critical.
Chinese high-precision machining manufacturers are increasingly becoming global partners of choice for tooling suppliers, fastener makers, and OEMs—thanks to a combination of engineering collaboration, advanced materials management, decades of processing experience, and reliable delivery systems.

1. Design-Involved Engineering: From Concept to High-Efficiency Production
Cold heading molds and fastener dies are not off-the-shelf items. Their geometry, material flow paths, tolerances, and wear resistance are highly customized. We actively engage with engineering teams in the early design phase to co-develop cold forming and fastening solutions that reduce failure rates and maximize efficiency.
Our team assists clients with:
- Drawing review and DFM (Design for Manufacturability) optimization
- Material behavior simulation under high-pressure forming
- Die life cycle assessment and design refinement
- Customization of multi-station die sets for progressive cold forming
By offering these upstream technical services, we help customers reduce production trial-and-error and enhance first-pass yield—particularly important for high-volume production lines.
2. Custom Machining for Cold Heading Tooling and Precision Fasteners
We provide custom CNC machining based on detailed drawings and functional requirements, supporting both tooling and end-use component production. Parts we regularly manufacture include:
- Cold heading punches and dies
- Hex die sets and trimming dies
- Progressive forming tools
- Special fasteners, nuts, pins, and sleeves
- Anti-loosening and special-shaped components
All components are produced with tolerances up to ±0.001mm, and surface roughness can reach Ra0.2μm, ensuring reliable performance in high-speed forming or fastening lines.
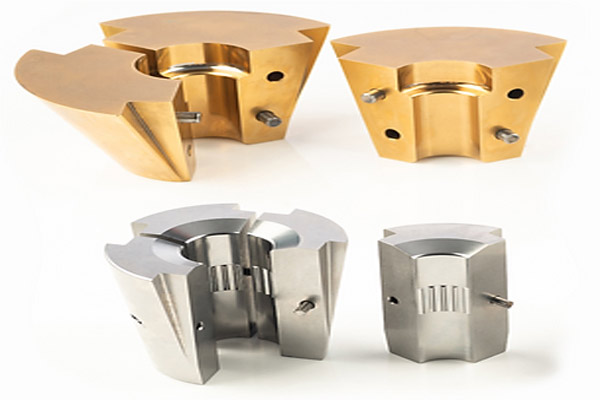
3. Advanced Materials and Heat Treatment Expertise
Material choice is mission-critical in cold heading and fastener manufacturing. We maintain long-term cooperation with certified suppliers of wear-resistant, high-hardness steels, ensuring consistency and longevity of every tool and part. Commonly used materials include:
- Tungsten carbide
- SKH-9 / HSS
- SKD11 / D2
- DC53 / H13
- M2, M42, and powder metallurgy steel
- Stainless steel and alloy steel for finished fasteners
We offer full support for heat treatments such as vacuum hardening, cryogenic treatment, nitriding, and surface coatings like TiN/TiCN, enhancing both hardness and anti-friction properties.
4. 20 Years of Deep Machining Experience for High-Load Applications
With nearly two decades of experience in precision CNC machining for forming and fastening components, we understand how to control key factors such as coaxiality, wear clearance, impact tolerance, and fatigue performance.
Our facilities are equipped with:
- High-precision CNC milling, turning, and EDM machines
- Surface and cylindrical grinders for die finishing
- Advanced CMMs and roundness testers
- Die cavity inspection tools for dimensional matching
Our production team ensures that each die or fastener not only meets dimensional standards but also withstands the real-world conditions of mass production.
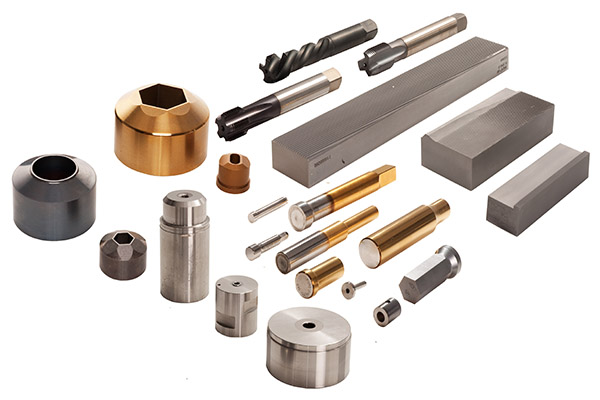
5. On-Time Delivery and Global Manufacturing Reliability
Fastener and tooling supply chains are highly time-sensitive. A single delay in die delivery can halt an entire production line. We prioritize on-time delivery with quality assurance, providing:
- Flexible capacity for urgent orders or product revisions
- Export-standard packaging and full documentation (QC reports, heat treatment certificates, etc.)
- Weekly progress updates and digital traceability
- Stable long-term production support for OEMs and Tier 1 suppliers
With a consistent on-time delivery rate above 97%, we’re helping global fastener and tool producers stay on schedule and competitive.
China’s Precision Advantage in Cold Heading & Fastening Components
Today’s global manufacturing demands not just low cost—but precision, consistency, and technical depth. In the cold heading and fastening sector, Chinese suppliers are stepping forward with real capability: early-stage co-engineering, material and process expertise, and world-class delivery systems.
If you are looking for a reliable machining partner to help optimize your tooling life, improve forming accuracy, and accelerate your production cycles—we’re ready to support your success.
Build strength and precision from the ground up—with us.
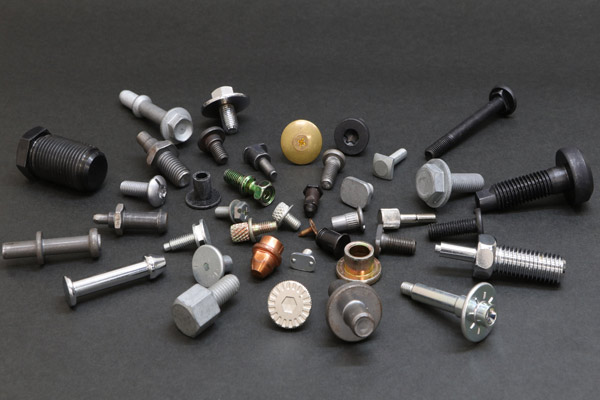
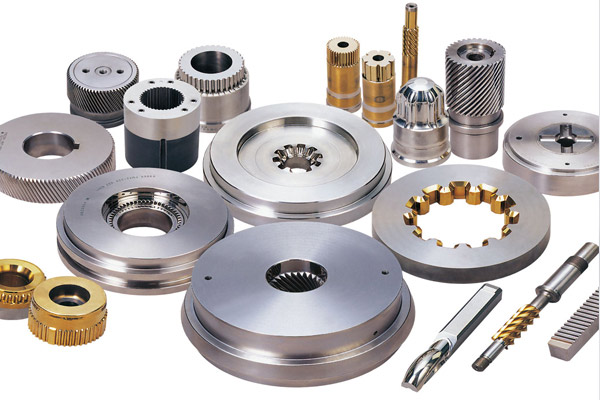