China’s Precision Advantage in Fluid Control Component Manufacturing: From Engineering Depth to Global Delivery
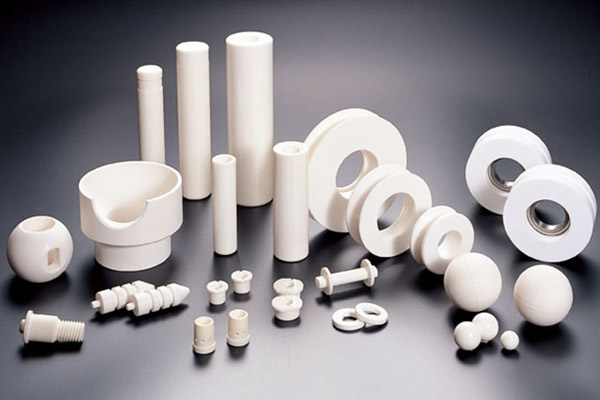
In the world of fluid control systems, precision is everything. Whether managing hydraulic pressure, pneumatic flow, or ultra-pure liquids, the performance of valves, manifolds, pistons, and sealing components depends on micron-level accuracy, tight tolerances, and material compatibility.
As global industries—such as energy, aerospace, food processing, chemical, and medical—demand ever-higher fluid control standards, China’s precision component manufacturers are stepping up as strategic global partners. With nearly 20 years of experience, vertically integrated supply chains, and engineering-driven workflows, Chinese manufacturers offer not just machining, but value-added co-engineering solutions for critical fluid control components.
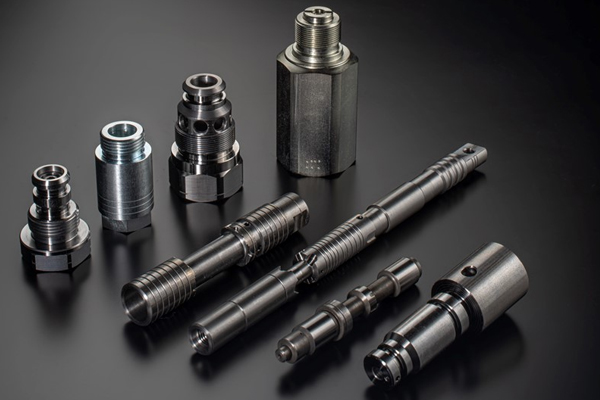
1. Deep Engineering Collaboration from Design to Execution
Fluid control components often involve complex internal geometries, tight sealing surfaces, and flow path optimization. These are not parts that can be produced by simply following a 2D drawing.
That’s why we begin each project by working closely with our customers’ design engineers, providing early-stage technical input to:
- Validate manufacturability of intricate valve bodies or manifolds
- Recommend geometry changes to reduce pressure loss or cavitation
- Ensure surface finishes and concentricity for perfect sealing
- Simulate material behavior under fluid stress and temperature variation
This early co-engineering approach helps eliminate failure risks and shortens development cycles—especially for components used in high-pressure, high-cycle, or corrosive environments.
2. Precision CNC Machining for Fluid Control Components
We specialize in custom machining based on client drawings and technical requirements, offering complete solutions for components such as:
- Valve spools and sleeves
- Hydraulic and pneumatic manifolds
- Pressure regulator housings
- Pump pistons and sealing rings
- Custom nozzles, connectors, and fluid transfer fittings
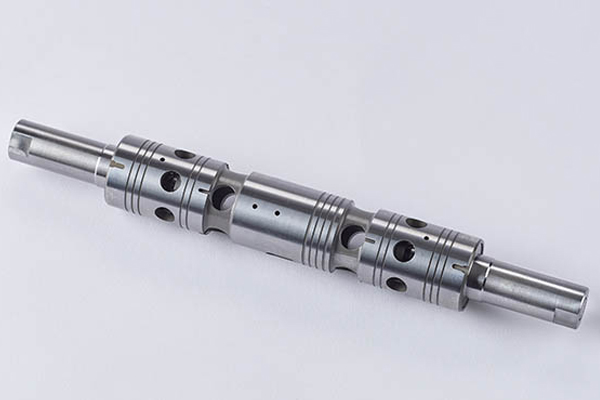
Our capabilities include:
- 3-axis to 5-axis CNC milling and turning
- Deep hole drilling and flow-channel shaping
- Grinding and lapping for sealing surfaces
- EDM for complex cavity and internal flow features
- Tolerance control to ±0.001mm and surface finish up to Ra0.2μm
Each part is carefully inspected to ensure flow accuracy, fit, and long-term operational stability under dynamic conditions.
3. Strategic Materials and Treatment Expertise
In fluid systems, materials are often exposed to chemical corrosion, pressure fluctuation, and high temperature. We maintain long-term relationships with trusted suppliers to ensure stable and traceable sourcing of high-performance materials such as:
- Stainless steel (304, 316L, 17-4PH) for corrosion resistance
- Aluminum alloys (6061, 7075) for lightweight applications
- Brass and copper for thermal conductivity and machinability
- Engineering plastics (PEEK, PTFE, PPSU) for chemical compatibility
- Hardened tool steel and tungsten carbide for wear resistance
We also offer customized heat treatment, surface passivation, hard anodizing, nitriding, and PVD coating to improve durability and extend service life—especially for components in mobile hydraulics, offshore energy, and food-grade environments.
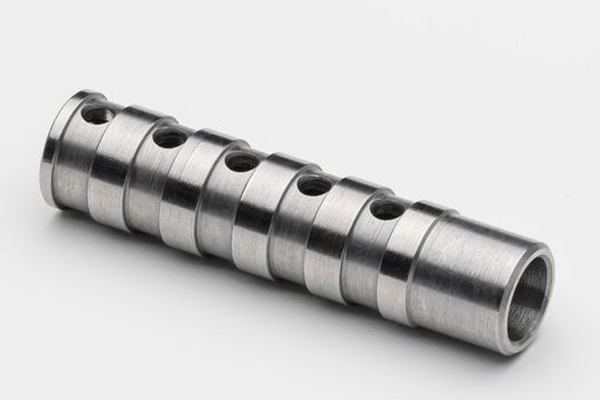
4. 20 Years of Manufacturing Experience with Continuous Process Optimization
With nearly two decades in precision machining, our team understands the intricacies of flow-sensitive components, from matching concentricity in valve cores to holding micron-level tolerances in pump pistons.
We continuously refine our processes through:
- CAM-based toolpath simulation
- Real-time machining parameter optimization
- In-process measurement and SPC (Statistical Process Control)
- Dedicated fixtures for concentricity and runout accuracy
- Full traceability and inspection using CMM, roughness testers, and roundness gauges
These practices allow us to meet the stringent demands of medical fluid delivery systems, aerospace hydraulics, and industrial automation equipment.
5. Reliable, On-Time Delivery for Global OEMs
In the fluid control industry, a late or out-of-spec part can shut down an entire line. That’s why we’ve built a supply model based on responsiveness, transparency, and stable delivery performance:
- Weekly production updates and project tracking
- Standard 3–4 week lead times for most custom orders
- Rapid prototyping with fast turnaround
- Export-ready packaging, documentation, and quality certificates
- 98%+ on-time delivery rate across global orders
We support both short-run and long-term production needs, adapting flexibly to client schedules and engineering changes.
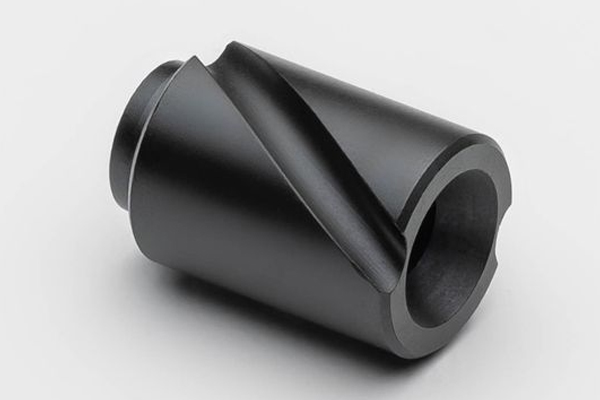
China’s Role in the Future of Fluid Control Manufacturing
As the global demand for clean energy, medical safety, and smart industrial systems rises, fluid control systems are becoming more complex—and more critical. Chinese manufacturers are well-positioned to support this shift, offering engineering knowledge, cost-effective production, material agility, and dependable timelines.
From co-developing ultra-precision hydraulic spools to machining flow-optimized manifolds for medical systems, we’re proud to be the silent force behind the precision and control that global industries rely on.
Let’s build the future of fluid control, together—with precision, depth, and trust.