Why Global Brands Choose China for Precision Mold Manufacturing: Engineering-Driven, Custom-Tailored, On-Time
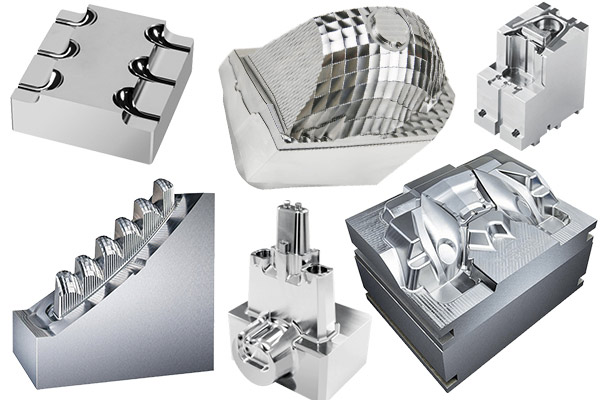
In today’s highly competitive industries—from automotive and medical to consumer electronics and packaging—high-precision molds are essential for achieving consistent product quality, high output, and low defect rates. Behind every molded product lies the silent precision of core, cavity, insert, and slider components—built to withstand millions of cycles under high pressure and temperature.
China has evolved from being a low-cost tooling supplier to a globally trusted partner in mold component precision manufacturing. At the heart of this transformation is a generation of high-precision manufacturers who combine deep engineering expertise, advanced machining, materials insight, and long-term manufacturing experience.
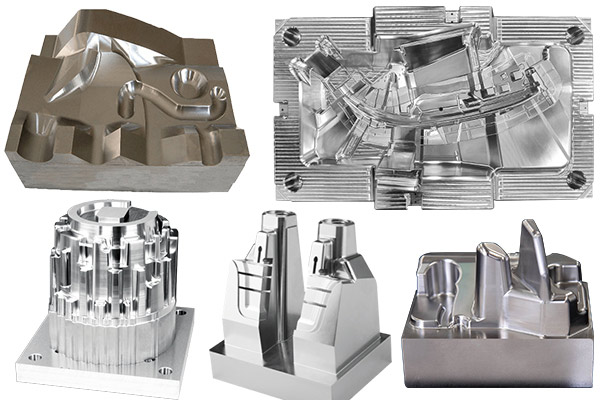
1. Early-Stage Co-Engineering for Complex Mold Structures
Mold performance starts at the design stage. That’s why we engage directly with mold designers and product engineers before production even begins—helping customers improve manufacturability, precision, and long-term mold durability.
Our engineering team assists with:
- DFM (Design for Manufacturability) feedback
- Complex geometry feasibility assessment
- Cooling system interface optimization
- Material compatibility and deformation analysis
- Core–cavity fitment evaluation and tolerance stack-up
By integrating into the product development process, we help customers reduce trial mold iterations, save costs, and speed up time-to-market.
2. Drawing-Based Custom CNC Machining for Mold Components
With every mold having its own design and performance expectations, we provide custom machining services based on client drawings and 3D models, including:
- Core and cavity inserts
- Mold bases, backing plates, guide sleeves
- Sliders, lifters, ejector pins, and wear parts
- Hot runner nozzles and cooling channels
- Multi-cavity stack mold components
We offer ultra-tight tolerance machining (±0.001mm), mirror surface polishing (Ra0.1μm), and full dimensional verification to ensure perfect part matching, interchangeability, and wear resistance under high-cycle molding.
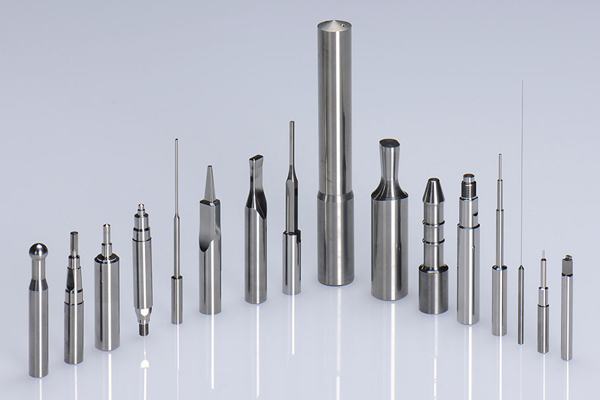
3. Material Expertise and Heat Treatment Know-How
The success of mold components depends heavily on the material’s hardness, toughness, and stability. We work with globally recognized tool steels and engineering alloys, including:
- H13, SKD61, and 1.2344 (hot work die steels)
- S136, 420, and 1.2083 (corrosion-resistant steels for optical and medical molds)
- P20, 1.2311/1.2738 (plastic mold steels)
- Tungsten carbide, copper alloys, and aluminum mold inserts
- High-speed steel (M2, M42) and beryllium copper
We coordinate and manage vacuum hardening, nitriding, cryogenic treatment, and PVD coatings (TiN, DLC) to enhance wear resistance, thermal stability, and polishing performance for transparent or glossy mold surfaces.
4. 20 Years of Precision Craftsmanship and Process Control
With nearly two decades of experience in high-precision mold component manufacturing, we have developed deep technical knowledge in machining:
- Thin-walled cores with high aspect ratios
- Multi-cavity matching with minimal tolerance accumulation
- Deep hole drilling and conformal cooling paths
- EDM for sharp corners and internal structures
- Precision grinding, lapping, and fitment tuning
Every process is monitored by experienced technicians using advanced equipment: Zeiss CMMs, roughness testers, concentricity gauges, and hardness analyzers—ensuring long-lasting mold performance from the first shot to the millionth.
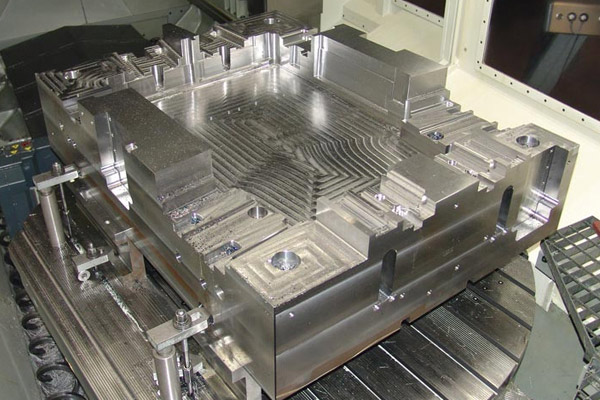
5. Reliable Global Delivery and Long-Term Partnership
We understand that mold deadlines are critical to product launch schedules. That’s why we focus on fast response, stable lead times, and flexible capacity to support global mold makers and OEMs:
- Standard lead times: 7–20 working days depending on complexity
- Weekly progress updates with project manager follow-up
- Emergency prototyping support
- Export-grade anti-rust packaging and traceable QC documentation
- Consistent on-time delivery rate over 96%
Whether you are building single-cavity precision tooling or multi-cavity high-output molds, we act as your extension factory, helping ensure consistent results, fast iteration, and product success.
Why Leading Mold Makers Trust China’s High-Precision Manufacturing Ecosystem
China’s mold manufacturing industry is no longer just about cost-efficiency—it’s about technical reliability, process depth, and precision execution. Backed by strong R&D alignment, vertically integrated resources, and decades of hands-on experience, Chinese high-precision manufacturers are powering global tooling innovation from behind the scenes.
If you’re looking for a machining partner who understands mold dynamics, material behavior, and tooling lifecycle requirements—we’re ready to support you from blueprint to moldroom.
Let’s shape the future of precision tooling—together.
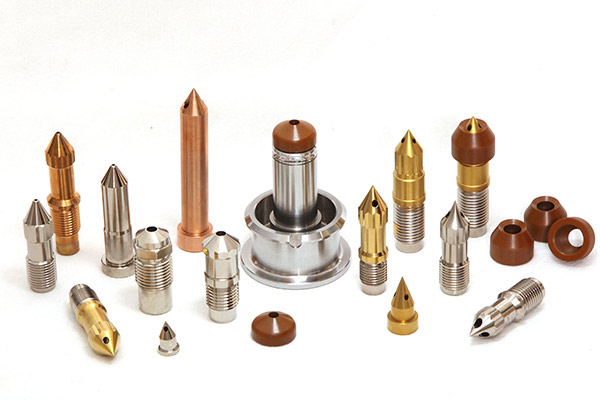