Precision Manufacturing for the Global Energy Sector: Why China Is Powering the Future
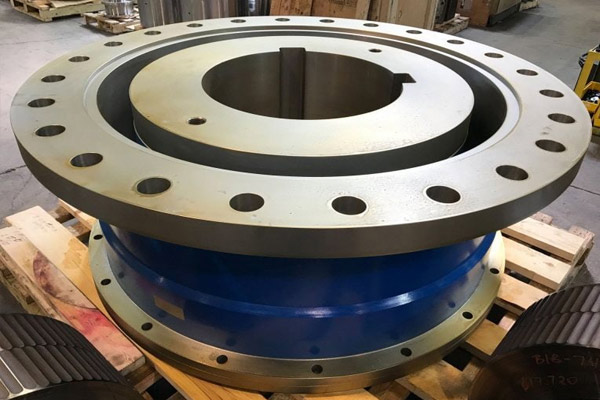
In the energy sector—whether traditional oil & gas, nuclear, or renewable energy like wind and hydrogen—reliability, safety, and precision are non-negotiable. The components that keep turbines spinning, pipelines flowing, and control systems operating demand tight tolerances, corrosion-resistant materials, and high mechanical integrity.
As the world transitions toward more diversified and efficient energy systems, China has become a critical player in the global precision manufacturing supply chain. From CNC-machined sealing flanges for offshore drilling to custom-machined components for hydrogen electrolyzers, Chinese high-precision suppliers bring not only competitive pricing but also deep technical collaboration, material control, and on-time global delivery.
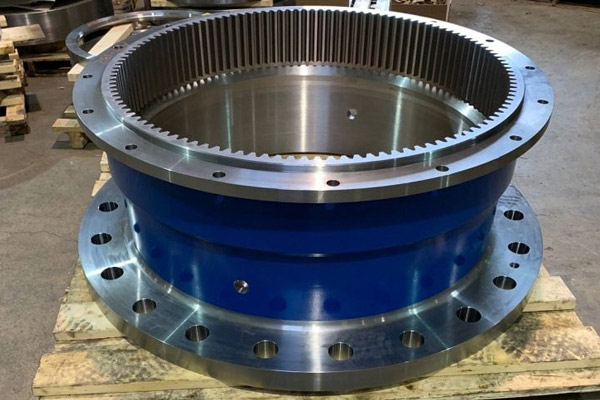
1. Early-Stage Engineering Collaboration with Global Energy OEMs
Energy components are rarely “off-the-shelf.” Most are highly customized based on environmental load, pressure class, temperature variation, and regulatory compliance.
That’s why our engineering team begins every project by collaborating closely with energy system designers and project engineers to:
- Understand operating environments (e.g., high pressure, offshore, cryogenic)
- Review drawings and provide DFM feedback for manufacturability
- Suggest material alternatives to meet long-term corrosion resistance
- Optimize complex geometries such as turbine blades, impellers, or flow restrictors
- Align on quality standards like NACE, API, or ASME specifications
This collaborative approach ensures that the final component is not only machinable but field-proven—ready to perform in mission-critical systems for decades.
2. Custom CNC Precision Based on Drawings and 3D Models
We support drawing-based and 3D-modeled production of custom components across a wide range of applications in energy systems, including:
- Flanges, couplings, and valve seats for oil & gas
- High-strength shafts, pins, and brackets for wind turbines
- Pump bodies and sealing housings for hydrogen and LNG systems
- Electrical insulation holders and pressure vessel interfaces
- Sensor housings and high-vacuum enclosures for nuclear systems
Machining capabilities include:
- 3- to 5-axis CNC milling and turning
- Deep-hole drilling and internal channel cutting
- Threaded connections per ANSI/ASME standards
- Tight-tolerance sealing surfaces (Ra < 0.2μm)
- Precision matching for assembly-critical pairs
Our precision allows energy OEMs to achieve leak-free connections, smooth energy transfer, and safe system integration, even in the harshest environments.
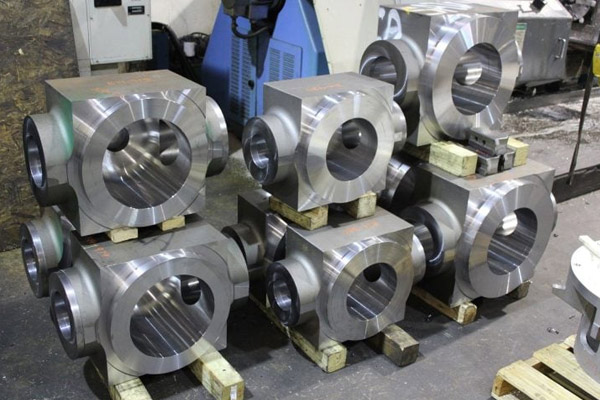
3. Strategic Material Selection & Surface Treatments for Extreme Conditions
Materials in the energy sector face extreme mechanical, thermal, and chemical stresses. We work closely with material suppliers to offer machining with full traceability for:
- Stainless steel grades (316L, Duplex, Inconel, Hastelloy) for corrosion resistance
- High-strength carbon steels for structural parts (AISI 4140, 4340)
- Copper alloys and aluminum for electrical and lightweight applications
- Ceramics and high-performance plastics for insulation or chemical compatibility
We also provide:
- Heat treatment (normalizing, quenching & tempering)
- NACE-compliant corrosion protection
- Anodizing, passivation, electroless nickel plating, and PTFE coating
- Full documentation (MTR, RoHS/REACH, hardness reports, and certificates of conformity)
This ensures that components meet global compliance standards while withstanding years of exposure to pressure, saltwater, high temperature, or hydrogen embrittlement.
4. Two Decades of Precision Manufacturing Experience
For nearly 20 years, we’ve served energy industry clients across Europe, North America, and Southeast Asia. Our manufacturing processes are built for repeatability, traceability, and zero-defect outcomes—essential for parts used in:
- Wind turbine yaw systems and blade hubs
- Deep-sea exploration rigs
- Nuclear facility control interfaces
- Solar panel assembly and inverter enclosures
- Battery housing and power grid hardware
With continuous investment in advanced metrology, SPC process controls, and ISO-certified systems, we offer:
- First article inspection (FAI)
- In-process quality control and 100% critical dimension checking
- Full lot traceability
- Digital measurement records
You’re not just buying parts—you’re buying process assurance and product confidence.
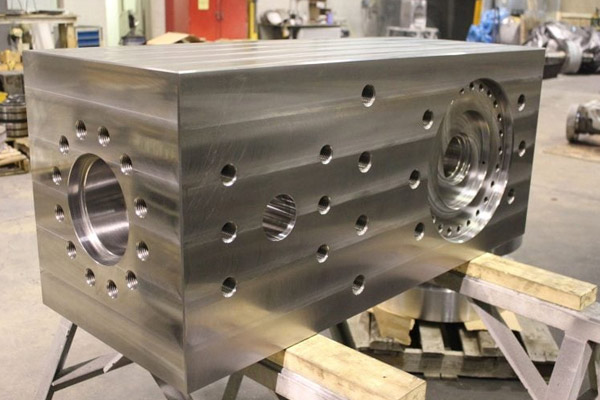
5. Reliable, Scalable Global Supply with On-Time Delivery
In the energy industry, delays cost more than money—they jeopardize safety and long-term ROI. Our lean supply chain and digital production tracking enable us to deliver:
- Fast prototyping and sample validation
- Small-to-large batch production scalability
- Lead times from 7 to 30 working days depending on complexity
- Stable long-term supply for recurring needs
- Professional export packaging, labeling, and logistics coordination
Whether you’re in wind turbine development in Europe, building hydrogen infrastructure in Asia, or constructing oilfield systems in the Middle East, we act as your reliable, global-ready supply partner.
China’s Role in the Future of Energy Precision Manufacturing
China is not just a production center—it is an engineering and innovation base that powers the global energy industry through high-precision parts that meet real-world demands. With a combination of:
- Deep industry experience
- Stable material supply
- Machining expertise
- Flexible production capacity
- Strong quality culture
…Chinese precision manufacturers are helping the world transition toward cleaner, safer, and more reliable energy systems.
Let’s build a sustainable energy future—through precision, collaboration, and trust.
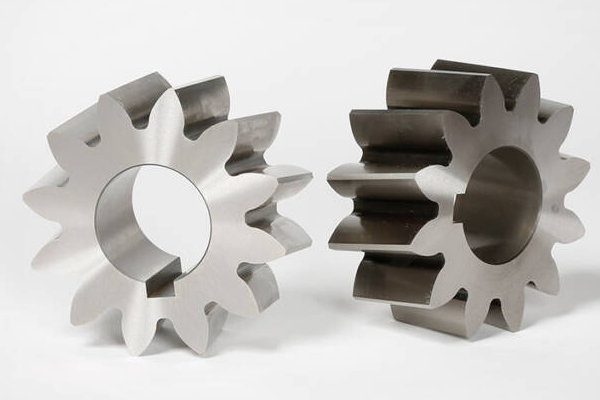