Precision Machining for Automotive Applications: Why the Global Auto Industry Trusts China’s Manufacturing Expertise
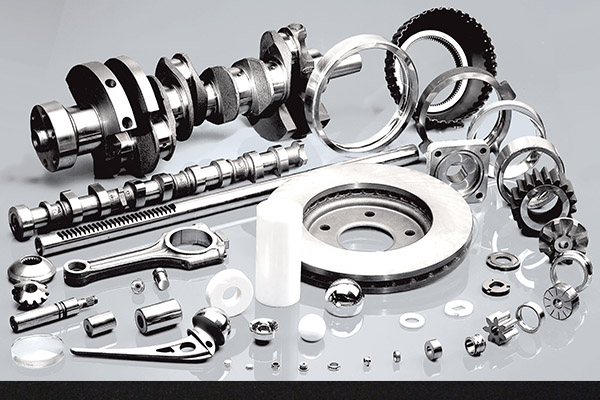
The automotive industry stands at the crossroads of mass production, precision engineering, and constant innovation. Whether it’s the structural components of an EV motor, transmission housings, safety-critical brake parts, or lightweight aluminum suspension arms, manufacturers demand parts that deliver exceptional tolerance control, repeatability, and performance under real-world stress.
As global carmakers transition toward electrification, automation, and sustainability, China has emerged not only as the world’s largest vehicle production base but also as a strategic hub for high-precision component manufacturing.
With nearly two decades of experience in CNC machining, materials sourcing, and process optimization, Chinese manufacturers are powering global auto OEMs and Tier 1 suppliers through design collaboration, advanced manufacturing, and reliable delivery.
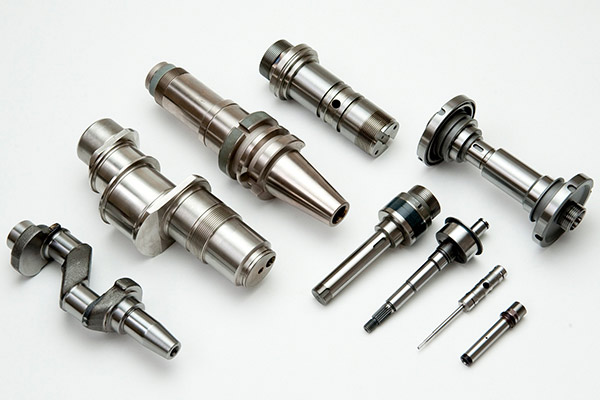
1. Early Collaboration with Automotive Design Engineers
Success in automotive manufacturing starts long before the first chip is cut. At the early stage of the project, we work closely with automotive design teams to:
- Understand functional requirements (load bearing, thermal cycling, NVH control)
- Review and optimize part geometry for Design for Manufacturability (DFM)
- Suggest cost-effective material substitutions and lightweight alternatives
- Identify potential tolerance bottlenecks or assembly issues
- Co-develop prototypes aligned with ISO/TS 16949 or IATF 16949 expectations
This tight coordination shortens time-to-market while ensuring design integrity and production scalability.
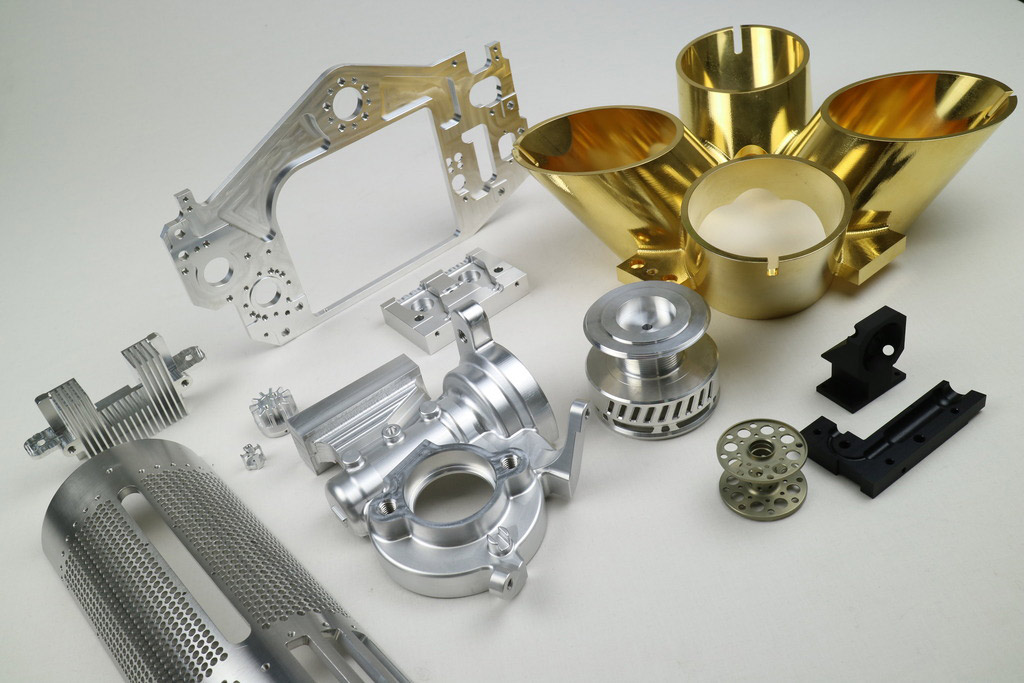
2. Drawing-Based, Custom CNC Machining for Automotive Parts
We support drawing-based production for a wide range of precision automotive parts, including:
- EV motor housings, battery brackets, cooling plates
- Transmission cases, differential housings, and gear supports
- Brake system parts (caliper brackets, pistons, mounts)
- Suspension arms, linkages, and knuckles
- Engine accessory mounts and heat shields
Machining capabilities include:
- 5-axis milling, multi-axis turning, and twin-spindle precision
- High-speed machining of aluminum and magnesium alloys
- Thin-wall machining for thermal management and weight reduction
- Tolerance control up to ±0.005mm for mating pairs and rotating assemblies
- Internal/external threading, oil channel drilling, and cross-hole boring
We are equipped to handle high-mix, medium-volume production that meets the rigorous standards of automotive repeatability and consistency.
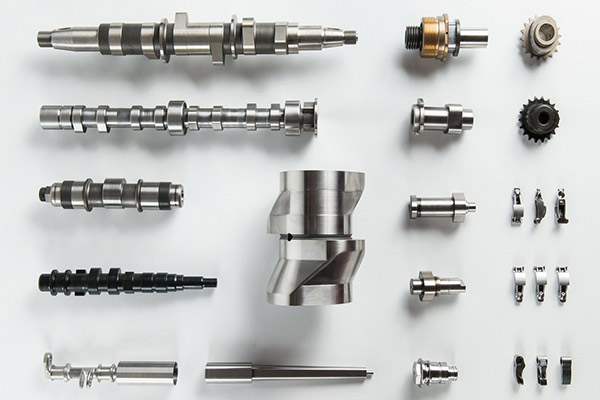
3. Material Expertise & Surface Engineering for Automotive Durability
Material performance is critical in automotive parts that experience extreme temperatures, corrosive fluids, and fatigue stress. We provide full material support and control, including:
✅ Common materials we process for automotive clients:
- Aluminum alloys (6061, 6082, ADC12, A356-T6) for lightweight structures
- High-strength steels (SCM435, 20CrMnTi, 42CrMo) for drivetrain and suspension
- Stainless steels (SS304, SS316L) for exhaust and corrosion-prone environments
- Engineering plastics and composites for thermal and acoustic insulation
- Heat-resistant alloys for e-mobility power components
✅ Surface treatments tailored to function:
- Anodizing, hard anodizing for aluminum
- Zinc-nickel plating and electrophoretic coating for corrosion protection
- Precision polishing and passivation for sealing interfaces
- Nitriding, carburizing, and T6 heat treatment for wear resistance
All treatments come with certification and process control records, ensuring full compliance with customer and industry requirements.
4. Nearly 20 Years of Automotive Machining Experience
For nearly two decades, we have been a trusted supplier for automotive part manufacturers and integrators globally. Our strengths include:
- Proven track record in serial production with PPAP and FAI documentation
- Use of CMMs, height gauges, surface testers, and concentricity instruments for full inspection
- Ability to manufacture parts from prototype through mass production
- Quality management systems aligned with IATF 16949 processes
- SPC (Statistical Process Control) and 100% inspection for safety-critical parts
Whether it’s a single-lot prototype for EV validation, or a long-term supply contract for ICE components, we ensure zero-defect tolerance and automotive-grade consistency.
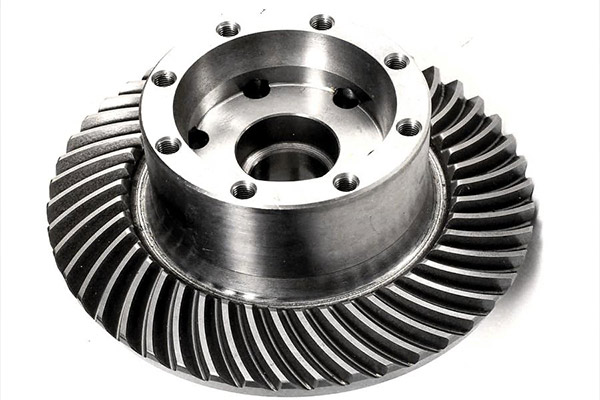
5. Scalable, On-Time Delivery for Global Automotive Supply Chains
We understand the just-in-time (JIT) nature of the automotive industry. Our manufacturing system is built for speed, flexibility, and reliability:
- Clear production timelines and supply forecasts
- Short lead times from 7 to 30 days depending on part complexity
- Batch traceability and component serialization
- Export packaging standards and logistics coordination
- Stable monthly delivery for long-cycle programs
Whether you’re a Tier 1 integrator, a startup in EV innovation, or a legacy automotive brand, we deliver parts that fit your speed, cost, and compliance needs.
Why China Is Driving the Future of Precision Automotive Manufacturing
China’s edge in automotive component production stems from:
- A mature manufacturing ecosystem with advanced machining clusters
- Competitive access to raw materials and surface treatment resources
- Deep experience with global OEM standards and certifications
- Strong engineering teams fluent in technical drawings and GD&T
- A culture of quality, efficiency, and continuous improvement
By combining precision, flexibility, and scale, Chinese precision manufacturers help global automotive brands achieve faster innovation, better margins, and dependable quality—across fuel, hybrid, and electric platforms.
Drive your automotive vision forward—with precision components made in China.
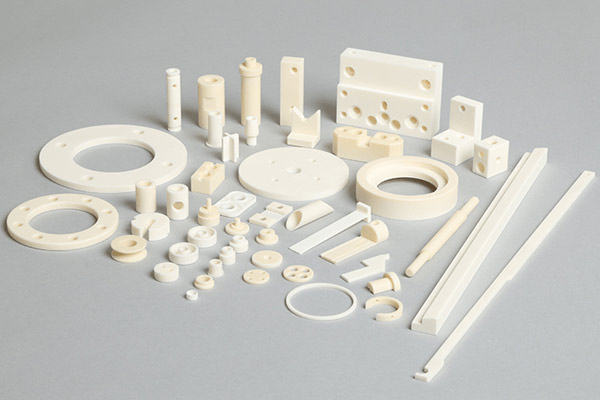