Precision Machining for Food, Beverage & Packaging Equipment: China’s Manufacturing Advantages
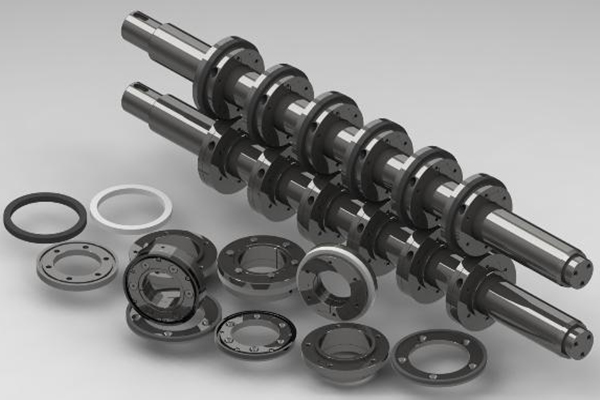
In the highly regulated and fast-paced world of food, beverage, and packaging machinery, equipment must deliver precision, hygiene, and efficiency—all while operating continuously under pressure. From stainless steel conveyor shafts and filling valve components to custom rotary parts for high-speed packaging systems, manufacturers rely on suppliers who understand both precision and compliance.
Over the past two decades, China has become a global leader in precision component manufacturing for the food and beverage industry. At the heart of this transformation are manufacturers like us—companies with deep experience in CNC machining, material traceability, and industry-specific engineering collaboration.
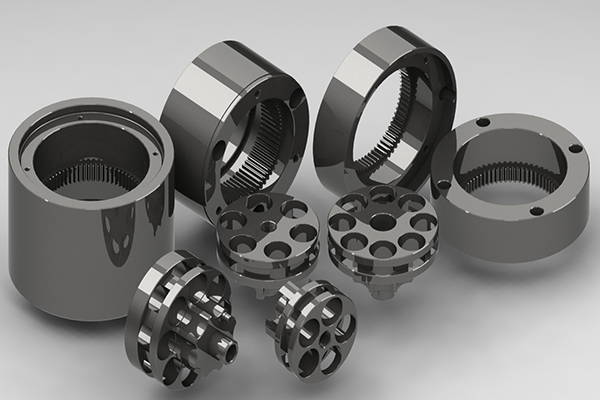
1. Collaborative Design Support: Bridging Engineering with Manufacturability
In this sector, performance cannot be compromised—cleanability, safety, and continuous uptime are essential. That’s why we work closely with food and beverage equipment designers and R&D teams to:
- Review functional requirements such as clean-in-place (CIP) compatibility, NSF/ISO standards, and rotary vs. linear movement
- Optimize designs for corrosion resistance, food safety, and low-friction contact
- Suggest geometry improvements for seamless sealing, wear reduction, or lower torque operation
- Provide design-for-manufacturing (DFM) feedback to shorten lead times and improve structural reliability
- Ensure every part matches not just the drawing—but the real-world application
We act as a true engineering partner, bringing precision and practicality together for better product outcomes.
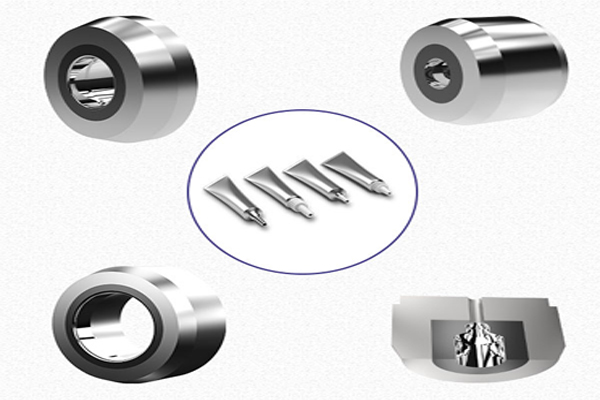
2. Drawing-Based, Custom Machining for Food & Packaging Components
Every machine in the food and packaging industry—from filling stations and capping machines to slicers and thermoformers—has its own set of precision demands. We offer customized, drawing-based CNC machining for parts such as:
- Stainless steel shafts, couplings, and cam followers
- Precision bushings, spacers, pistons, and manifolds
- Rotary index parts, sprockets, rollers, and brackets
- Fluid control nozzles, valve bodies, and actuator components
- Linear rails, guides, and sensor holders for automated systems
Capabilities include:
- 5-axis CNC milling, multi-spindle turning, and high-polish surface machining
- Tolerance control to ±0.01 mm for smooth movement and zero leakage
- Deburring, internal polishing, and chamfering for food-safe finishing
- Low-friction surface machining and sealing face optimization

3. Material Expertise Tailored to Hygiene and Corrosion Resistance
The industry mandates high standards for non-contamination, cleanability, and durability. We offer material sourcing, traceability, and surface treatments specific to food-grade applications:
✅ Common materials used:
- 316L stainless steel – high corrosion resistance for acids and CIP cleaning
- 304 stainless steel – standard for general contact and non-corrosive liquids
- Food-grade aluminum (6061/6082) – lightweight parts for automated actuators
- POM/Delrin, PTFE, UHMW-PE – for low-friction, non-metal contact surfaces
- Titanium and duplex steel – for specialty corrosive environments
✅ Surface finishes and certifications:
- Ra < 0.8μm polishing for direct food contact
- Electro-polishing for sanitary flow applications
- Passivation and pickling per ASTM A967
- Anodizing and PTFE coating for wear surfaces
- Full traceability, including material certs, RoHS, REACH, FDA (on request)
4. Nearly 20 Years of Precision Experience for Clean Industry Demands
Food and packaging OEMs rely on decades of machining expertise to ensure parts don’t just meet specs—they exceed expectations. Our team brings:
- Experience producing high-volume, high-precision parts for global F&B brands
- Fully equipped quality lab: CMM, roughness testers, roundness gauges, thread checkers
- Experience handling FDA-compliant materials and packaging-grade alloys
- Zero-defect approach: ISO9001 quality system with batch control, inspections, and traceability
- Prototyping and optimization of mechanical parts for fluid dynamics, wear, and heat
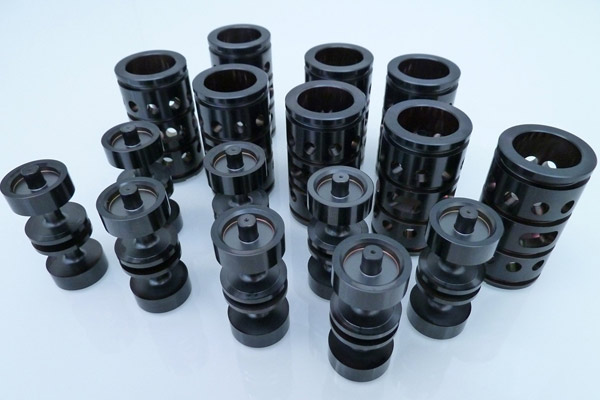
5. Flexible Production + On-Time Global Delivery
Downtime in a food production line can result in massive waste and revenue loss. We’re equipped to deliver on time, every time:
- Fast DFM + quoting for complex assemblies
- Production lead times from 7 to 25 days
- Just-in-time (JIT) shipping for international orders
- Anti-rust packaging and cleanroom-safe wrapping
- Batch serial number marking for full product traceability
- Logistics support from port to plant
Why Leading Food & Beverage OEMs Choose Chinese Precision Machining
China’s high-precision manufacturing industry offers a unique value proposition for F&B clients worldwide:
✔ Strong collaboration with engineers for performance-focused design
✔ Access to FDA- and EU-compliant materials and treatments
✔ Precision control for zero-defect, high-volume components
✔ Fast delivery and flexibility for scaling
✔ Lower total cost of ownership without sacrificing quality
As a trusted manufacturer to global F&B equipment brands, we help build faster, cleaner, and more reliable machines—from packaging lines in Europe to bottling systems in North America.
Partner with us to manufacture hygienic, high-performance components for the future of food and beverage automation.
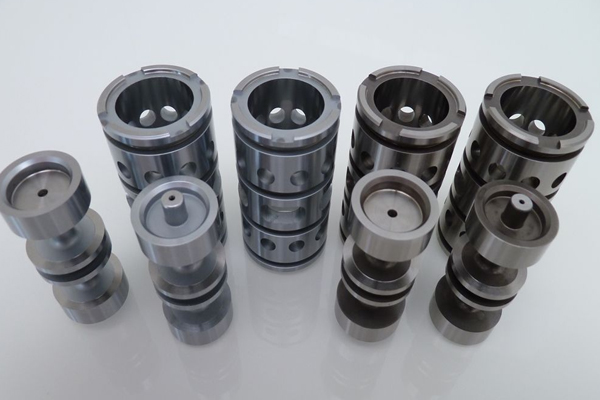