High-Precision Ceramic Parts Machining for the Semiconductor and Microelectronics Industry
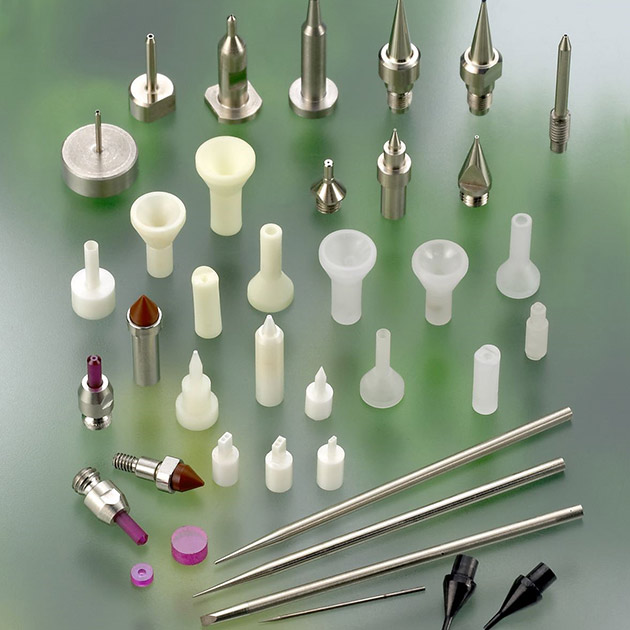
Geometric tolerances within 0.002mm | Dimensional tolerances ±0.001mm
As the semiconductor and microelectronics industry advances toward ever-smaller and more sophisticated components, the demand for ultra-precise, stable, and high-performance materials continues to rise. Among these, technical ceramics have emerged as indispensable materials due to their excellent hardness, wear resistance, chemical inertness, and thermal stability. At our facility, we specialize in the custom machining of complex ceramic components—meeting the most stringent tolerances and supporting some of the world’s most critical innovations.
Advanced Equipment for Extreme Precision
Our workshop is equipped with:
- 5-axis CNC machining centers for complex geometries
- High-speed grinding and polishing machines for ultra-fine surface finish
- Coordinate Measuring Machines (CMM) and Tokyo Seimitsu roundness testers for precision inspection
- Custom jigs and fixtures to ensure repeatability on brittle ceramic materials
These enable us to achieve:
- Geometric tolerances within 0.002mm
- Dimensional tolerances of ±0.001mm
- Surface roughness up to Ra 0.02μm, essential for vacuum, plasma, and cleanroom applications
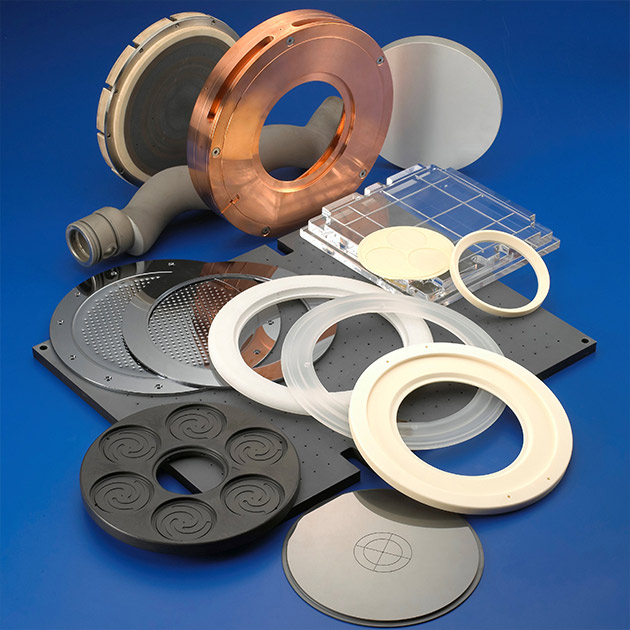
Drawing-Based Custom Machining
We follow a strict drawing-based manufacturing process, where client CAD files are analyzed in-depth by our engineering team. Our experienced technicians work directly with semiconductor R&D teams and design engineers to:
- Interpret geometric dimensions and tolerances (GD&T)
- Design appropriate cutting paths and fixturing
- Select optimal tools and sequences for crack-free machining
- Guarantee first-piece success in fragile, high-value ceramic blanks
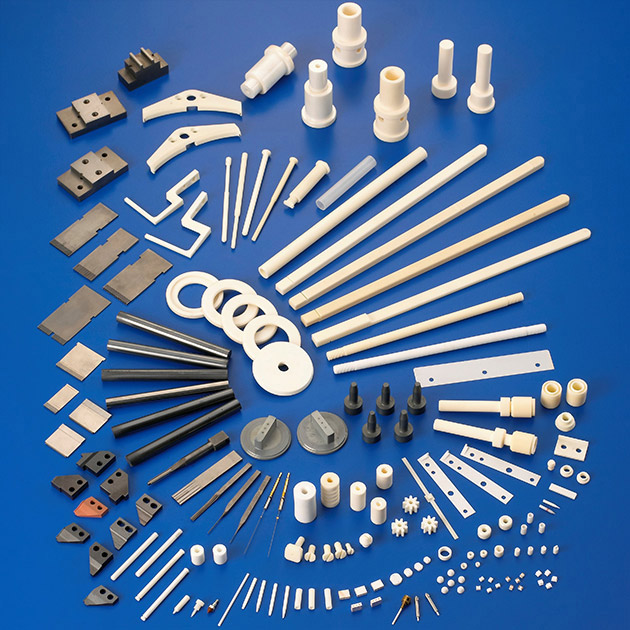
Specialized Ceramic Materials
We have developed strong expertise in machining various technical ceramics, including:
- Alumina (Al₂O₃) – excellent electrical insulation
- Zirconia (ZrO₂) – high strength and fracture toughness
- Silicon Nitride (Si₃N₄) – ideal for thermal shock resistance
- Macor® machinable glass ceramics – prototyping and low-volume R&D components
Each material comes with unique machining requirements, and we optimize tool pathing, coolant strategy, and abrasive selection accordingly.
Process Optimization with 20+ Years of Experience
With over two decades of experience in precision ceramic part production, we’ve accumulated proven process know-how in:
- Micro-crack prevention during grinding
- Thermal compensation during toolpath programming
- Non-destructive inspection for internal defects
- Post-machining polishing and cleaning for cleanroom compatibility
We’ve refined processes that reduce material loss, increase yield, and extend tool life—making high-mix, low-volume production both cost-effective and repeatable.
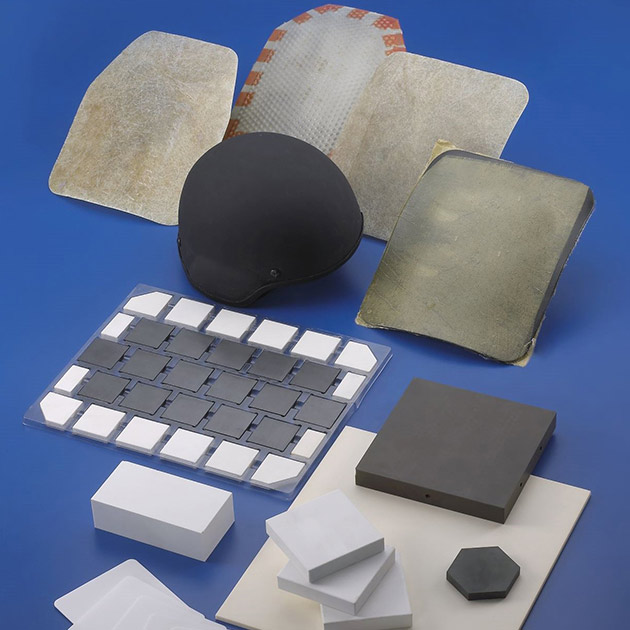
Global Projects & Applications
We’ve participated in numerous high-profile semiconductor equipment programs involving:
- Ceramic guide rings for plasma etchers
- Vacuum-compatible ceramic end effectors
- Ceramic nozzles and insulators for ion implanters
- Precision base plates and fixtures for wafer testing
These components are now running in tools deployed across Asia, Europe, and North America, in fabs producing 5nm-class and sub-10nm nodes.
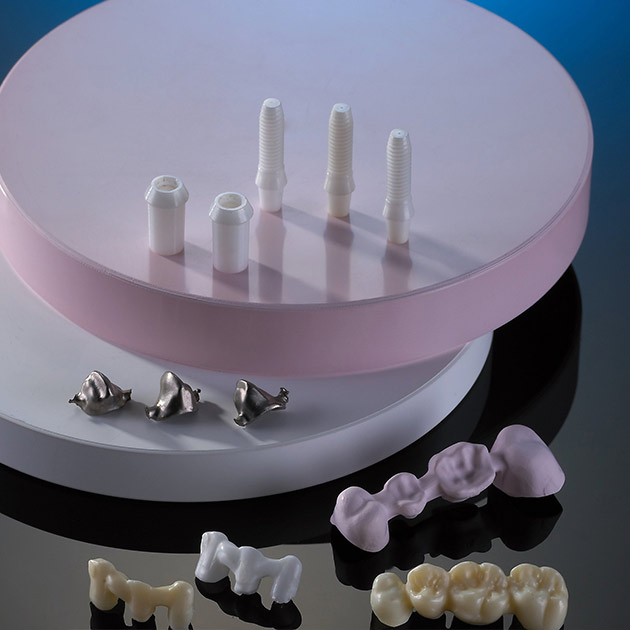
Your Ceramic Machining Partner
Whether you are in need of prototype development, batch production, or R&D collaborations, we are equipped to deliver precision ceramic parts that meet your expectations in both performance and reliability. We welcome the opportunity to contribute to your next innovation in the semiconductor or microelectronics field.
Let’s create the future—one micron at a time.