China CNC Manufacturer Specializing in Precision Custom Parts for Global Clients
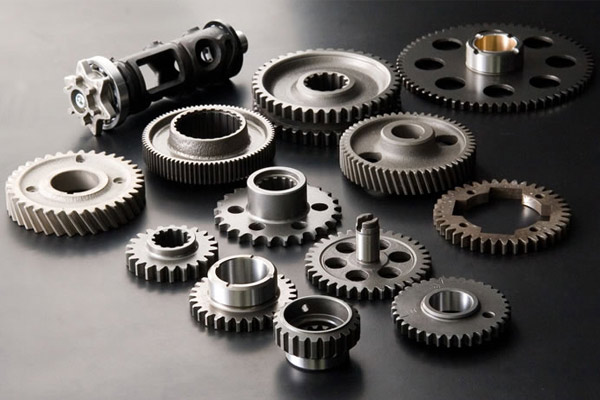
===INTRO:
In today’s highly competitive manufacturing landscape, the demand for precision-engineered components has never been greater. China, renowned for its robust industrial base, has emerged as a leading hub for CNC machining services, especially for clients requiring complex, high-precision parts. These manufacturers boast advanced technology, extensive experience, and a customer-centric approach, making them trusted partners for global companies seeking custom solutions. This article explores how a top Chinese CNC manufacturer specializes in delivering intricate, high-difficulty parts with impeccable quality, utilizing superior materials and innovative techniques to meet diverse international needs.
===
## Leading China CNC Manufacturer Specializing in Custom Precision Parts
China’s CNC manufacturing sector has rapidly evolved, positioning itself at the forefront of global precision machining. Leading firms in this space, such as those exemplified by the company at https://www.sppgy.com/index/applications/detail.html?id=182, prioritize customized solutions tailored to client specifications. These manufacturers invest heavily in state-of-the-art CNC equipment capable of handling complex geometries and tight tolerances.
Flexibility is a hallmark of these Chinese CNC companies, enabling them to serve an array of industries from aerospace and medical devices to automotive and electronics. They excel in turning detailed technical drawings into high-precision prototypes and mass-produced parts, often exceeding international standards. Their ability to adapt to unique project requirements makes them a preferred partner for global clients seeking reliable, one-stop manufacturing solutions.
Moreover, these manufacturers emphasize quality assurance through rigorous inspection protocols. They employ advanced measurement tools, such as coordinate measuring machines (CMMs), to verify that every component meets strict dimensional tolerances. This commitment ensures that parts are consistently delivered with the highest precision, fostering long-term trust and repeat business.
Another competitive edge is the integration of automation and smart manufacturing processes. Automating workflows not only boosts productivity but also enhances accuracy and repeatability. As a result, Chinese CNC manufacturers can offer faster turnaround times without compromising quality, a vital factor in today’s fast-paced supply chains.
The ability to handle both small-batch and large-scale production is crucial. Leading Chinese firms have the infrastructure to support prototype development, pilot runs, and high-volume manufacturing, making them versatile partners for international clients. Their extensive experience with various industry standards and materials allows them to adapt to diverse project demands efficiently.
Customer support and technical consultation are also integral to their service. Many Chinese CNC manufacturers provide comprehensive pre-production analysis, helping clients optimize designs for manufacturability. This proactive approach minimizes errors and reduces overall project costs, ensuring a smooth production journey from design to delivery.
Sustainability and eco-friendly practices are increasingly incorporated into manufacturing processes. Leading Chinese CNC providers adopt green machining techniques, reduce waste, and use environmentally responsible materials, aligning with global trends toward sustainable manufacturing.
In summary, these manufacturers’ focus on custom solutions, technological advancement, strict quality control, and customer collaboration positions them as top-tier providers on the international stage. Their ability to produce high-difficulty, precision parts consistently meets the rigorous demands of global industries.
---
## Expertise in Handling High-Difficulty CNC Machining Projects Globally
Handling high-difficulty CNC projects demands not only advanced equipment but also seasoned expertise. Chinese manufacturers excel in tackling complex geometries, micro-machining, and tight tolerances that challenge even the most experienced engineers worldwide. Their engineers and technicians possess deep knowledge of material behaviors, machining strategies, and innovative techniques.
One of the key factors is the extensive experience accumulated over years of working on diverse projects. This hands-on knowledge enables them to anticipate potential manufacturing issues and develop effective solutions early in the process. For instance, high-precision components for aerospace applications require meticulous planning to avoid deformation or inaccuracies caused by thermal stress during machining.
Chinese CNC firms frequently undertake multidisciplinary collaborations, bringing together design, engineering, and manufacturing teams to optimize complex projects. They utilize cutting-edge CAD/CAM software to simulate machining processes, reducing trial-and-error and ensuring feasible production paths. This proactive planning minimizes errors and accelerates project timelines.
Handling difficult materials—such as titanium, Invar, or composites—poses additional challenges. These materials often require specialized tools, cutting parameters, and cooling techniques. Chinese manufacturers have mastered these nuances, enabling them to produce high-quality parts from difficult-to-machine materials reliably and efficiently.
Furthermore, they are adept at managing multi-axis machining centers, which allow for intricate multi-surface and sculpted parts to be produced in a single setup. This reduces assembly errors and enhances precision, particularly important in high-stakes sectors like medical implants or aerospace components.
The ability to work with micro-scale features—such as tiny holes, slots, and threads—demonstrates their mastery in micro-machining. This expertise is essential for industries like electronics and medical devices, where component miniaturization is critical. Achieving such fine detail requires specialized equipment, stable environments, and experienced operators.
Quality control is integral when dealing with high-difficulty projects. Chinese manufacturers implement comprehensive inspection routines, including 3D scanning and non-destructive testing, ensuring every complex part adheres to exact specifications. This rigorous oversight guarantees the functionality and safety of high-precision components.
An often-overlooked aspect is the problem-solving capability of these manufacturers. When unexpected challenges arise—such as material inconsistencies or design ambiguities—they leverage their expertise to devise innovative machining strategies, often involved in refining designs to improve manufacturability without sacrificing performance.
In essence, the mastery in handling high-difficulty CNC projects allows Chinese manufacturers to serve demanding clients across the globe. Their blend of experience, technical prowess, and problem-solving ability ensures that even the most complex components are produced with precision, reliability, and efficiency.
---
## Advanced Material Selection and Application for Complex CNC Components
Choosing the right materials is fundamental to achieving the desired performance, durability, and precision in CNC machined parts. Chinese manufacturers excel in selecting and applying advanced materials tailored to specific project requirements. Their extensive knowledge spans metals, composites, ceramics, and innovative alloys, enabling them to optimize each component’s functionality.
Metallic materials such as aerospace-grade titanium, stainless steels, aluminum alloys, and superalloys are frequently used in high-end applications. These materials demand specialized machining techniques due to their hardness, thermal properties, and potential for deformation. Chinese firms have developed precise cutting parameters and cooling methods to handle these challenging materials effectively.
Additionally, composite materials—like carbon fiber-reinforced plastics—are increasingly in demand for lightweight, high-strength components. Machining composites requires controlled tooling and new approaches to prevent delamination or fiber damage. Chinese CNC manufacturers are well-versed in these processes, producing complex composite parts with high dimensional accuracy.
Ceramic materials, valued for their heat resistance and electrical insulation properties, are utilized in electronics and aerospace components. Customizing tools and implementing precise temperature controls allow these manufacturers to machine ceramics without cracking or chipping, ensuring quality and longevity of parts.
The application of advanced alloys, such as Inconel or hastelloy, showcases their ability to work with materials that perform under extreme conditions. These superalloys are vital in turbine blades, chemical processing, and other high-stress environments, and manufacturing them requires specialized knowledge and tooling, which Chinese manufacturers provide.
Material sourcing and supply chain management are also vital. Many Chinese CNC providers maintain strong relationships with raw material suppliers worldwide to ensure the authenticity and consistency of materials used. This consistency is crucial for parts that demand strict performance criteria.
Post-machining treatments, including heat treatment, surface finishing, and coatings, further enhance material properties. Chinese manufacturers often integrate these processes into their workflow, delivering parts with improved wear resistance, corrosion protection, or aesthetic appeal.
Environmental considerations are increasingly influencing material choices. Recyclable, eco-friendly materials and processes are adopted to meet global sustainability standards, aligning manufacturing practices with eco-conscious client values.
Custom material development is another specialty—working with clients to develop new alloys or composite formulations tailored to specific performance, weight, or cost requirements. This innovation-driven approach sets Chinese manufacturers apart in the competitive global market.
Ultimately, their expertise in advanced material selection and application ensures that complex CNC components not only meet design specifications but also excel in real-world performance, durability, and reliability.
---
## Key Case Studies Solving Global CNC Precision Challenges
Several case studies exemplify how Chinese CNC manufacturers tackle some of the most complex and demanding precision machining challenges globally. These real-world examples highlight their problem-solving capabilities, technical expertise, and commitment to quality.
One notable case involved manufacturing aerospace components with extremely tight tolerances—within a few microns. The Chinese manufacturer employed multi-axis machining centers and advanced inspection systems to produce parts with flawless precision, overcoming material deformation issues associated with titanium alloys. This project demonstrated their ability to meet aerospace regulatory standards and achieve high repeatability.
Another example was in the medical device sector, where micro-machining of intricate surgical tools required high precision and smooth surface finishes. Through micro-tools, controlled environment machining, and specialized polishing techniques, they successfully delivered parts that met stringent hygiene and performance standards, facilitating their use in minimally invasive surgeries.
A challenging project involved machining high-temperature superalloys for turbine blades. These materials are difficult to cut due to their hardness and thermal properties. The manufacturer optimized cooling techniques, tool materials, and cutting speeds, resulting in high-precision blades that improved engine efficiency. Their experience with such difficult materials was vital to success.
A further case was the production of complex electronic housings from composites and ceramics, where micro-scale features and complex geometries were required. Using multi-axis CNC and innovative fixture designs, they managed to produce parts with high accuracy and repeatability, ensuring compatibility with sensitive electronic components.
In the automotive industry, a client required large-volume, high-precision prototypes for new engine components. The manufacturer implemented flexible production lines and rigorous quality checks, reducing lead times and ensuring consistency across batches. This project underscored their capacity for scalable, high-quality manufacturing.
Environmental and sustainability challenges were addressed in a project involving the mass production of eco-friendly, recyclable components. The manufacturer integrated green machining techniques, waste reduction practices, and eco-conscious materials, demonstrating their commitment to sustainable manufacturing.
Throughout these case studies, the importance of collaboration, technological innovation, and quality management shines through. They exemplify how Chinese CNC manufacturers are capable of solving some of the most complex precision challenges faced globally. Their tailored solutions, combined with deep technical expertise, continue to earn international trust and recognition.
---
## The landscape of CNC machining in China continues to evolve rapidly, driven by technological innovation, skilled expertise, and a customer-focused approach. Leading manufacturers have established themselves as global leaders in producing custom, high-precision components that meet the most demanding standards across various industries. Their ability to handle complex geometries, choose advanced materials, and solve intricate production challenges makes them indispensable partners in today’s global manufacturing ecosystem. As international clients seek reliable, efficient, and innovative solutions, China’s CNC industry is poised to deliver excellence, pushing the boundaries of what is possible in precision engineering.