China’s CNC Machining Experts: Precision, Materials, and Complex Challenges
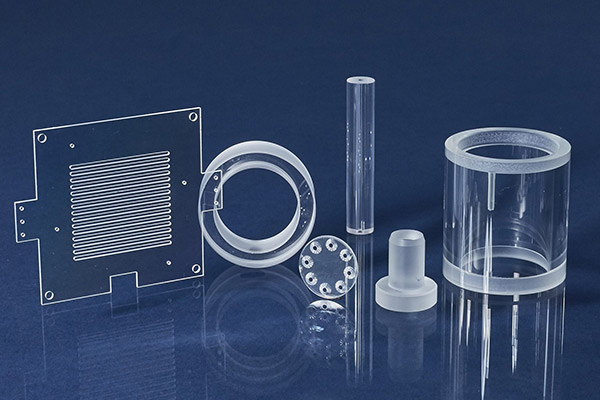
===INTRO:
In today’s global manufacturing landscape, China has emerged as a powerhouse in CNC machining, offering unparalleled expertise in producing high-precision, complex components for international clients. With a strong focus on customization, advanced materials, and tackling intricate design challenges, Chinese CNC machining experts continuously push the boundaries of what’s possible. Their experience, technological capabilities, and commitment to quality make them trusted partners for industries ranging from aerospace to medical devices. This article explores how China’s CNC machining sector ensures precision and customization, utilizes advanced materials and techniques for complex parts, and addresses global manufacturing challenges through innovative solutions and expertise.
## China’s CNC Machining Experts: Ensuring Precision and Customization
Chinese CNC machining companies have earned a reputation for delivering components with exceptional accuracy, closely matching client specifications. Precision is the foundation of their service, achieved through state-of-the-art CNC equipment, rigorous quality control, and skilled operators. These experts understand that every detail matters, especially when manufacturing parts for high-stakes applications like aerospace, defense, and medical devices.
Customization is another core strength. Chinese manufacturers excel at translating complex drawings and CAD models into tangible parts, adhering strictly to clients’ unique requirements. They offer tailored solutions, from prototype development to mass production, accommodating specific material choices, surface finishes, and tolerances. This flexibility allows clients to innovate confidently, knowing their designs will be faithfully realized.
Furthermore, their experience in working with a diverse range of materials enhances their ability to produce custom components. Whether it's titanium for aerospace, stainless steel for medical implants, or exotic alloys for specialized industries, Chinese CNC experts adapt their processes to achieve optimal results. This versatility is crucial in a competitive global market where bespoke solutions are often needed.
Reliability and consistency are key factors in their success. Chinese CNC machining firms implement strict quality assurance protocols, including in-process inspections and final testing, to maintain tight tolerances and prevent defects. Their ability to reproduce complex parts accurately, batch after batch, has strengthened their reputation among international clients.
Moreover, the OEM and ODM services provided by these experts mean they can handle entire projects—from initial design consultation to final delivery—ensuring that the finished product aligns perfectly with client expectations. This comprehensive approach fosters long-term partnerships based on trust and mutual success.
The integration of advanced software, such as CAM and CAD systems, allows for precise programming and simulation before actual machining begins. This step minimizes errors and optimizes toolpaths, ensuring the highest levels of precision and efficiency.
Additionally, Chinese CNC manufacturers invest heavily in employee training and technological upgrades, staying ahead of industry standards. Their teams possess deep expertise in complex machining operations, ensuring that even the most challenging designs are executed flawlessly.
In summary, China’s CNC machining experts are distinguished by their relentless pursuit of precision, customization, and quality. Their technical expertise and adaptive capabilities make them invaluable partners for global industries demanding high-precision components.
## Advanced Materials and Techniques for High-Complexity Components
The fabrication of high-complexity components demands not only precision but also a deep understanding of diverse materials and advanced machining techniques. Chinese CNC machining companies have developed extensive experience working with materials ranging from traditional metals to cutting-edge composites, enabling them to meet the stringent demands of various industries.
Titanium, known for its strength-to-weight ratio and corrosion resistance, is frequently used in aerospace and medical applications. Chinese manufacturers utilize specialized cutting tools and optimized machining parameters to effectively process titanium, overcoming challenges such as its tendency to gall and its heat sensitivity. Advanced cooling systems and high-speed machining techniques help achieve smooth surfaces and tight tolerances.
Stainless steel, especially medical-grade variants, is another material frequently handled. Achieving fine surface finishes and precise geometries in stainless steel requires meticulous process control, which Chinese experts are adept at managing. Their experience ensures that parts meet strict hygiene and safety standards without compromising on accuracy.
Exotic alloys like nickel-based superalloys, used in high-temperature environments, pose significant challenges due to their hardness and thermal properties. Chinese CNC specialists employ high-performance cutting tools, high-pressure coolant systems, and optimized machining strategies to successfully process these materials, enabling components for turbines and engines.
Composite materials, including carbon-fiber-reinforced plastics, are increasingly incorporated into complex assemblies. Chinese firms utilize CNC routers and laser machining for composites, ensuring minimal fiber damage and precise cuts. This versatility allows clients to integrate lightweight, durable components into their products.
In addition to traditional subtractive machining, additive manufacturing techniques such as 3D printing are being integrated into the workflow for complex geometries. Combining CNC machining with additive processes allows for rapid prototyping and production of parts with internal channels and intricate features that are difficult to produce through conventional means.
Advanced surface treatment methods, like electro-polishing, laser engraving, and protective coatings, are frequently applied to enhance the functionality and aesthetics of complex parts. Chinese experts tailor these finishing processes based on material type and application requirements.
The incorporation of smart automation and IoT technology into machining centers allows for real-time monitoring and adaptive adjustments during processing. This improves efficiency and reduces errors, especially when dealing with high-value, complex components made from expensive materials.
By mastering a broad spectrum of materials and continuously refining their techniques, Chinese CNC machining firms can produce high-complexity parts with demanding specifications, ensuring quality and performance in critical applications.
## Tackling Global Challenges: Lessons from Complex Manufacturing Cases
Chinese CNC machining companies have faced and overcome numerous global manufacturing challenges, showcasing their resilience and innovative problem-solving capabilities. Their experience with complex cases provides valuable lessons for the international manufacturing community.
One notable challenge involved producing ultra-precise aerospace components with tight tolerances and intricate geometries. Chinese experts utilized advanced multi-axis machining centers, coupled with rigorous process simulation, to achieve the required precision. Their approach underscored the importance of integrating software with hardware for complex, high-accuracy parts.
Another case involved processing difficult-to-machine materials like superalloys for jet engine components. The solution lay in employing high-pressure coolant systems, coated cutting tools, and optimized cutting parameters. This case exemplifies how understanding material behavior and adapting machining strategies can overcome significant technical challenges.
Medical device manufacturing often requires parts with complex internal channels and high surface finish standards. Chinese CNC firms adopted combining subtractive machining with micro-drilling and laser etching techniques. This hybrid approach allowed them to produce intricate, high-precision components that meet rigorous health and safety standards.
A particularly demanding challenge was the mass production of high-precision optical components with micron-level tolerances. The Chinese manufacturers invested in cleanroom environments, precision fixtures, and automated inspection systems. Their meticulous quality control processes ensured consistency across large batches, reducing waste and rework.
Global environmental concerns prompted Chinese firms to focus on sustainable manufacturing practices. They developed eco-friendly cooling and lubrication solutions, minimized material waste, and adopted energy-efficient machining practices. These efforts demonstrate a commitment to responsible manufacturing while maintaining high standards.
During the COVID-19 pandemic, Chinese CNC companies swiftly adapted to produce vital medical equipment and parts. Their ability to upscale production and meet urgent delivery deadlines highlighted the importance of operational flexibility and supply chain resilience.
Cross-border collaborations and knowledge sharing have played a significant role in tackling complex manufacturing challenges. Chinese firms actively participate in international forums, learn from global best practices, and continuously innovate to stay ahead.
The lessons learned from these diverse cases reinforce that embracing technological advancements, investing in skilled personnel, and fostering a problem-solving mindset are essential for overcoming complex manufacturing hurdles. Chinese CNC machining experts exemplify these principles, inspiring global manufacturers to push boundaries and achieve excellence.
China’s CNC machining sector stands as a testament to the country’s technological prowess and adaptability in the face of complex manufacturing challenges. Through a deep understanding of materials, meticulous attention to precision, and innovative problem-solving, Chinese experts continue to deliver high-quality, customized components for international clients. Their ability to tackle intricate designs and demanding specifications not only elevates their global reputation but also provides valuable lessons for the industry at large. As manufacturing continues to evolve with new materials and technologies, China’s CNC machining specialists remain at the forefront, driving innovation and setting new standards for excellence worldwide.