Custom CNC Machining for High-Precision Global Clients
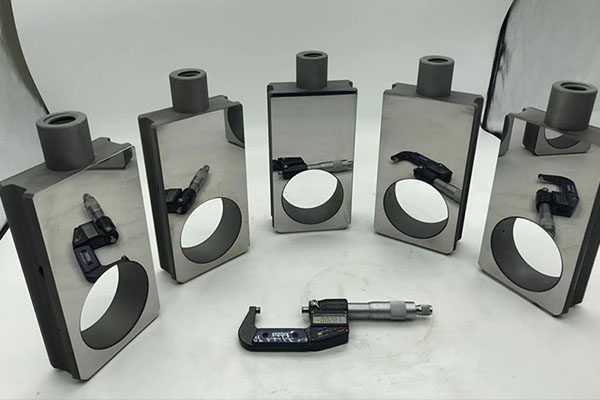
# Customized CNC Machining Solutions for Global High-Precision Needs
===INTRO:===
In today’s highly competitive global manufacturing landscape, the demand for high-precision, customized CNC machining solutions continues to grow exponentially. Companies across industries—ranging from aerospace and medical devices to electronics and automotive—require parts that meet exacting specifications, often involving complex geometries and difficult materials. China’s CNC machining manufacturers, equipped with advanced technology and extensive experience, are rising to meet these challenges by offering tailored solutions designed to deliver impeccable quality and precision. This article explores how custom CNC machining bridges the gap between intricate design requirements and real-world manufacturing, serving high-precision clients worldwide.
---
## Customized CNC Machining Solutions for Global High-Precision Needs
Custom CNC machining is about more than just cutting metal; it’s about translating intricate designs into tangible, functional parts with extraordinary accuracy. For global clients, this means adhering to strict tolerances, complex geometries, and specific material properties. Custom solutions enable manufacturers to produce unique components that are critical for high-tech applications, including aerospace, medical implants, and precision instrumentation. These solutions are often developed through collaborative efforts, combining client specifications with advanced machining capabilities to optimize efficiency, cost, and quality. International clients seek reliable partners who can handle small batch prototypes as well as high-volume production, ensuring consistency across every piece produced. Staying ahead in this domain requires embracing innovative processes, extensive equipment, and a deep understanding of material behaviors. Chinese CNC machining providers have invested heavily in such capabilities, making them competitive on a global scale. They also emphasize transparency, communication, and flexibility, helping clients navigate the complexities of custom manufacturing.
---
## Leveraging Advanced Techniques for Complex High-Precision Parts
The core of high-precision CNC machining lies in employing advanced techniques that allow for the creation of highly complex parts. Techniques such as multi-axis machining, synchronized turning and milling, and micro-machining enable the production of parts with intricate geometries that traditional methods cannot achieve. For example, five-axis machining allows for high-precision cuts on complex surfaces, significantly reducing the need for secondary operations. Additionally, the integration of CAD/CAM software ensures that every detail is meticulously planned before machining begins, minimizing errors. Laser measurement and in-process inspection tools guarantee tolerances are maintained throughout production. Chinese manufacturers have adopted these technologies, ensuring that even the most challenging designs are manufactured to exact specifications. These techniques are especially vital when working with high-value materials like titanium, stainless steel, or specialized composites where precision and surface finish are critical. By leveraging such innovations, Chinese CNC providers can deliver parts that meet the most demanding standards worldwide.
---
## The Importance of Material Selection in Custom CNC Machining Projects
Material selection plays a crucial role in the success of high-precision CNC projects. Different applications require specific properties—be it strength, corrosion resistance, or biocompatibility. Selecting the right material can determine not only the performance of the finished part but also its machinability and longevity. For instance, aerospace components often demand titanium or superalloys that withstand extreme conditions, while medical implants require biocompatible stainless steel or specialized ceramics. Chinese CNC machining manufacturers possess a broad material portfolio, enabling them to advise clients on optimal choices based on application needs and machining constraints. Proper material handling and processing are essential to prevent deformation, warping, or surface defects during manufacturing. Furthermore, understanding material behavior under CNC processes helps in developing customized tooling and cutting parameters. This careful alignment of material properties with machining techniques ensures high precision, durability, and functionality of the final product.
---
## How Experience Shapes Successful High-Precision CNC Manufacturing
Experience is arguably the most valuable asset in high-precision CNC machining. Seasoned manufacturers have encountered and solved myriad challenges—ranging from tight tolerances and complex geometries to difficult materials and rapid prototyping needs. Their accumulated knowledge allows for proactive problem-solving, process optimization, and quality control. For example, experienced Chinese CNC shops understand the nuances of machining exotic alloys versus standard steels, enabling them to select appropriate tools and cutting conditions. They also have refined inspection routines, such as coordinate measuring machines (CMM) and surface profilometers, to ensure every part conforms to specifications. Moreover, troubleshooting common issues like tool wear, residual stresses, or surface imperfections becomes second nature for veterans. This depth of expertise translates into reliable, consistent outputs, even for the most challenging high-precision projects. Clients benefit from the confidence that comes with working with manufacturers who have a proven track record of delivering precision, quality, and efficiency.
---
## Overcoming Challenging Tolerance Requirements with Expert CNC Processes
Achieving ultra-tight tolerances—often within microns—is a hallmark of high-precision CNC machining. Such precision is vital for aerospace components, medical devices, and electronics where even minor deviations can lead to failure. Overcoming these challenges requires meticulous planning, advanced machinery, and skilled operators. Chinese CNC suppliers employ multi-axis machines, real-time monitoring, and adaptive control systems that dynamically adjust cutting parameters to maintain consistent tolerances. Additionally, implementing rigorous quality assurance protocols, including in-process inspections, reduces the risk of errors. Fine finishing techniques like electro-polishing or laser trimming further enhance surface accuracy. The integration of Industry 4.0 concepts—such as data-driven process optimization—also plays a role in maintaining tight tolerances across production runs. These efforts, combined with experienced craftsmanship, enable Chinese CNC providers to successfully meet and exceed demanding tolerance specifications for global clients.
---
## Case Study: Tackling Difficult Materials in CNC Machining
Working with challenging materials such as titanium, Inconel, or ceramics presents significant hurdles in CNC machining. These materials are known for their toughness, corrosion resistance, and high melting points, making them difficult to cut and shape. A notable case involved manufacturing high-precision aerospace brackets from titanium alloy in China. The project required tight tolerances and a flawless surface finish, despite the alloy’s abrasive nature. The solution involved using specialized cutting tools, optimized spindle speeds, and cooling strategies to reduce tool wear and heat generation. Additionally, the manufacturer employed multi-axis CNC machining to access complex geometries efficiently. This case underscored the importance of material knowledge, process adaptation, and precision inspection. It also demonstrated how Chinese CNC shops leverage their experience and advanced equipment to conquer material challenges, delivering components that meet stringent aerospace standards. Such success stories reinforce the capability of Chinese manufacturers to handle the most difficult materials effectively.
---
## From Drawings to Reality: Precision Customization for Unique Components
Transforming detailed technical drawings into high-precision components requires close collaboration, meticulous planning, and advanced machining capabilities. For global clients, custom CNC machining offers the flexibility to produce unique parts that might involve complex geometries, tight tolerances, and specialized features. Initially, detailed CAD models are converted into CNC programs via sophisticated CAM software, ensuring every detail is accurately translated. Manufacturers then set up dedicated tooling, verify machine calibration, and perform trial runs to validate the process. Throughout production, rigorous inspections ensure the finished parts match the original design specifications. Chinese CNC manufacturers excel at this process, combining their technical expertise with flexible manufacturing systems. This approach minimizes errors, reduces lead times, and ensures that every component is a faithful realization of the client’s vision. It embodies the art and science of precision manufacturing, turning intricate drawings into real-world solutions.
---
## Addressing Global Clients’ Demanding Specifications with Precision Craftsmanship
Global clients often impose strict specifications—be it in tolerances, surface finishes, or material properties—that demand the highest levels of craftsmanship. Chinese CNC machining companies have responded by building quality systems aligned with international standards, such as ISO 9001 and AS9100. They employ advanced inspection tools, training programs for operators, and continuous process improvements to meet these exacting standards. Custom fixtures and jigs are designed to ensure consistent positioning and repeatability, especially in high-volume runs. Furthermore, transparent communication channels and detailed documentation help clients monitor progress and verify compliance. Precision craftsmanship extends beyond technical execution; it encompasses attention to detail, accountability, and a customer-centric approach. These qualities allow Chinese manufacturers to satisfy demanding global clients across various sectors, ensuring that each component not only meets specifications but exceeds expectations.
---
## High-Quality CNC Machining for Aerospace and Medical Applications
In aerospace and medical industries, the stakes are high—parts must meet rigorous safety, reliability, and performance standards. Chinese CNC machining firms have gained certifications and experience to serve these critical sectors effectively. For aerospace, components often require titanium, high-strength aluminum, or superalloys, machined with extreme precision and surface quality. Medical applications demand biocompatible materials and sterile finishing processes, along with traceability throughout production. These manufacturers implement strict quality controls, including cleanroom environments, validated processes, and comprehensive testing. They also customize solutions to meet specific industry standards such as AS9100 aerospace quality management and ISO 13485 for medical devices. By combining advanced technology with industry-specific expertise, Chinese CNC providers deliver high-precision parts that uphold the safety and performance standards essential for aerospace and healthcare.
---
## Innovative Approaches to Machining Complex Geometries and Structures
Modern engineering increasingly involves complex geometries—think curved surfaces, internal channels, and intricate structures—that challenge traditional manufacturing methods. To address this, Chinese CNC machining companies are adopting innovative approaches such as additive manufacturing integration, hybrid machining centers, and robotic automation. These methods enable the production of complex, lightweight, and highly functional components. For instance, combining CNC milling with 3D printing allows for rapid prototyping and complex internal features. Similarly, multi-axis machines can produce parts with minimal setups, reducing errors and lead times. Advanced simulation software helps optimize tool paths for complex shapes, while in-process monitoring ensures accuracy. Such innovations enable the creation of cutting-edge components for industries like defense, aerospace, and high-end electronics, reinforcing China’s position as a leader in complex high-precision manufacturing.
---
## Ensuring Consistency and Accuracy in Mass Production of High-Precision Parts
Achieving consistency across large production volumes is essential for high-precision manufacturing. Variability can lead to defects, increased costs, and compromised performance. Chinese CNC manufacturers rely on robust quality management systems, advanced automation, and data analytics to maintain uniformity. They implement strict process controls, including temperature monitoring, tool wear tracking, and real-time feedback systems. Automated fixturing and batch processing reduce human errors and enhance repeatability. Additionally, statistical process control (SPC) techniques are used to analyze production data and identify potential deviations early. The integration of Industry 4.0 technologies enables predictive maintenance and process optimization. These strategies ensure that every part, whether in small batches or mass production, meets the same high standards of accuracy and quality, satisfying global clients’ demanding specifications.
---
## Lessons Learned from Classic Global CNC Machining Challenges
Throughout their extensive experience, Chinese CNC manufacturers have encountered and overcome numerous global challenges—such as machining difficult alloys, tight tolerances, and complex geometries. One key lesson is the importance of early process validation and rigorous inspection protocols to prevent costly rework. Another is the necessity of continuous skill development and equipment upgrades to stay ahead of technological advancements. Flexibility and close communication with clients help address evolving design changes and unforeseen issues. Moreover, adopting a proactive approach to material research and process innovation ensures resilience against manufacturing hurdles. These lessons have shaped best practices that maximize efficiency, reduce errors, and improve overall quality. Sharing such knowledge helps global clients understand the value of partnering with experienced manufacturers capable of mastering even the most formidable high-precision machining challenges.
---
### OUTRO:
High-precision CNC machining is both an art and a science—demanding expertise, advanced technology, and meticulous attention to detail. Chinese CNC manufacturers, leveraging extensive experience, innovative techniques, and a broad material portfolio, are increasingly vital players in the global high-precision market. They deliver tailored, complex components that meet the stringent standards of aerospace, medical, and high-tech industries. By continuously refining their processes and embracing new approaches, these manufacturers demonstrate their capability to turn challenging designs into reality. For international clients seeking dependable partners capable of navigating the intricacies of custom CNC machining, China’s high-precision providers stand out as strategic allies committed to quality, precision, and innovation.