EDM and Wire Cut Machining Expert in Precision CNC Machining
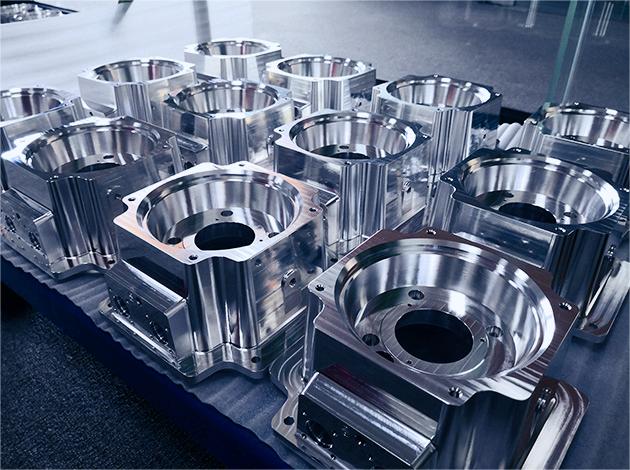
Precision Demands in High-Performance Manufacturing
As the demand for highly intricate and high-precision components continues to grow across industries such as aerospace, medical devices, semiconductor, mold tooling, and automotive systems, traditional subtractive machining processes alone are often not sufficient. Parts with tight internal features, sharp corners, deep cavities, or fine tolerances frequently require Electrical Discharge Machining (EDM) and Wire Cut EDM to meet their functional and geometric requirements.
As an established EDM and Wire Cut Machining expert, we specialize in producing complex components with ultra-fine precision and surface integrity. Our CNC machining capabilities are enhanced with advanced EDM technologies to handle difficult-to-machine materials and geometries with high accuracy and repeatability.
Machining Challenges and Engineering Solutions
EDM and Wire Cut machining are not just alternatives to traditional methods—they are essential solutions for challenging scenarios where conventional cutting cannot meet design goals.
Challenges in high-precision part manufacturing include:
- Tight internal contours and micro-slots that cannot be milled or drilled without tool breakage.
- Sharp inside corners and deep cavities that require non-contact material removal.
- Materials with high hardness or thermal resistance (e.g., tool steel, carbide, titanium).
- High dimensional accuracy and ultra-fine finishes that are beyond the scope of standard CNC.
- Deformation risks during machining of thin-walled parts or small components.
Our solutions:
- Sinker EDM (Die-Sinking) for producing intricate 3D cavities, blind holes, and sharp corners without mechanical stress.
- Wire Cut EDM for high-precision profiling of punches, dies, gear teeth, and thin-walled parts.
- Micro EDM for ultra-small features and miniature components, often used in electronics and medical instruments.
- Automated multi-axis EDM systems to handle complex part geometries with continuous, unattended machining.
- Thermal deformation control, ensuring parts remain dimensionally stable during long discharge cycles.
Together with CNC milling, turning, and grinding, our EDM capabilities form a comprehensive precision manufacturing solution.
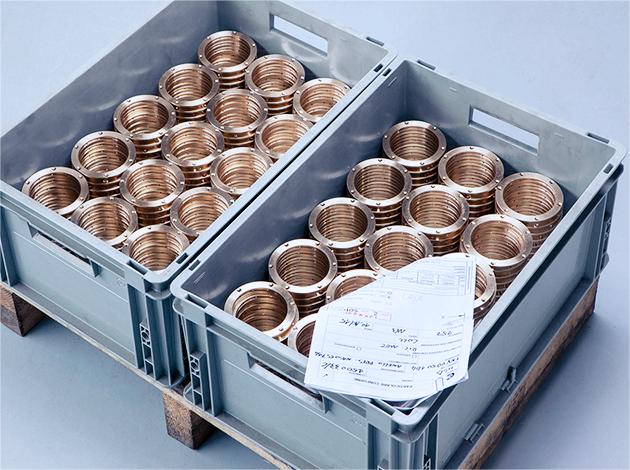
Common Materials for EDM and Wire Cut Machining
EDM excels in machining electrically conductive materials, even those that are extremely hard or thermally resistant. Common materials include:
- Tool Steel (D2, H13, SKD11): Common in mold and die making due to wear resistance and hardness.
- Tungsten Carbide: Extremely hard and wear-resistant, often requiring EDM for shaping.
- Stainless Steel (304, 316, 420, 17-4PH): Used in medical, aerospace, and food-grade applications.
- Titanium Alloys (Ti-6Al-4V): Lightweight and corrosion-resistant, frequently used in aerospace and surgical components.
- Inconel & Nickel Alloys: High-performance metals used in turbines and high-heat environments.
- Copper and Graphite Electrodes: Often used as tooling in EDM processes.
All materials are traceable and sourced from verified suppliers, with optional heat treatment and certification available upon request.

Our EDM and CNC Machining Capabilities
As a CNC machining and EDM specialist, we offer a complete suite of services for precision part production:
EDM Capabilities:
- Wire Cut EDM: ±0.002 mm accuracy; capable of taper cutting and fine wire (<0.1 mm)
- Sinker EDM: Deep cavity machining with minimal corner radii
- Small Hole EDM: Hole diameters from 0.2 mm, ideal for starter holes in hardened material
- Multi-axis EDM: For advanced shapes and compound angle features
Complementary CNC Capabilities:
- CNC Milling & Turning: 3-, 4-, and 5-axis machines for pre- and post-EDM operations
- Surface & Cylindrical Grinding: For flatness and roundness control after EDM
- Tolerance Range: Up to ±0.001 mm for critical features
- Surface Finish: Down to Ra ≤ 0.2 μm on EDM-cut surfaces with optional polishing
Inspection and Quality Control:
- CMMs with scanning probes for full 3D inspection
- Profile projectors and air gauges for internal dimension verification
- Wire EDM calibration software for real-time compensation of wire deflection and wear
- Documentation: Full dimensional reports, material certificates, and process traceability
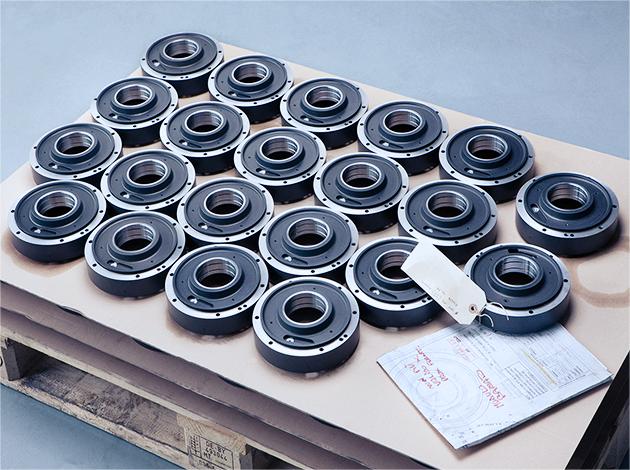
Typical Components and Applications
We manufacture custom components using EDM and CNC machining for a wide array of sectors:
- Precision Tooling: Punches, dies, inserts, and mold cores
- Medical Devices: Bone plates, surgical blades, implant components
- Aerospace Systems: Fuel injector components, turbine blade features, titanium fasteners
- Electronics: Connector molds, micro-structure patterns, high-frequency RF housings
- Fluid Control: Valve ports, orifice plates, micro-holes for nozzles
Every part is built to customer specifications, CAD models, or technical drawings, with optional reverse engineering support for obsolete or legacy components.
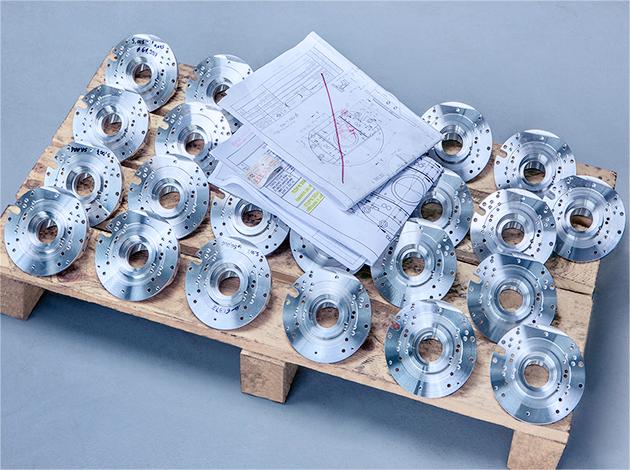
Case Example: Wire Cut EDM for Aerospace Titanium Nozzles
We recently completed a production run of titanium aerospace nozzles requiring ultra-fine internal geometry and extremely tight tolerances:
- Material: Ti-6Al-4V
- Wall Thickness: 0.3 mm
- Tolerances: ±0.003 mm on flow channels
- Process: Pre-milling → Wire EDM profiling → Sink EDM detail machining → Polishing → Inspection
The nozzles passed 100% flow testing and met all aerospace-grade dimensional specifications, providing superior thermal and corrosion resistance in application.
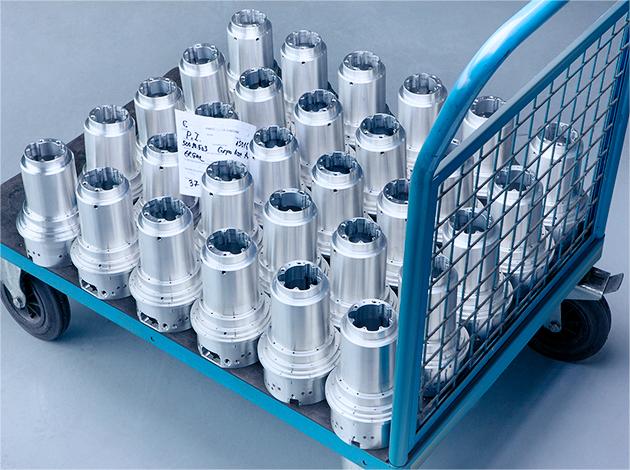
Work With a Trusted EDM and CNC Machining Expert
When it comes to producing parts with extreme accuracy, intricate detail, and complex geometries, EDM and Wire Cut machining are unmatched. As your EDM and Wire Cut machining expert in CNC precision manufacturing, we provide the technology, experience, and commitment to deliver high-performance parts with fast lead times and consistent quality.
► Request a Quote Today — Precision Components Engineered with EDM and CNC Excellence.
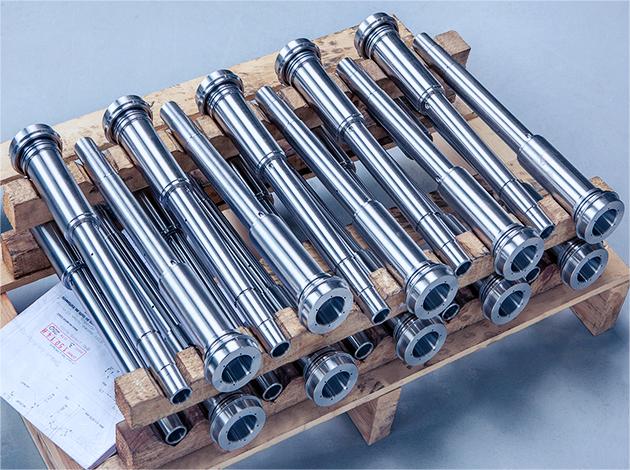