Expert CNC Machining for High-Precision and Complex Parts Worldwide
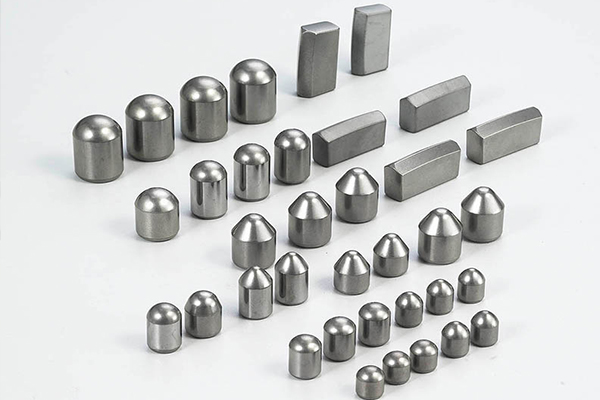
# Expert CNC Machining for High-Precision and Complex Parts Worldwide
===INTRO:===
In today’s global manufacturing landscape, the demand for high-precision, complex parts has skyrocketed across industries such as aerospace, medical, automotive, and advanced electronics. As the complexity of designs increases, so does the need for sophisticated CNC machining capabilities that can deliver consistent quality and intricate detail. Chinese CNC machining manufacturers have risen to this challenge, offering tailored solutions for overseas clients seeking reliable, high-precision processing. This article explores the evolving world of expert CNC machining, emphasizing the significance of custom solutions, material versatility, experience, and innovative technology in overcoming manufacturing challenges worldwide.
## The Rise of Expert CNC Machining for Global High-Precision Parts
Over recent years, expert CNC machining has become a cornerstone of precision manufacturing worldwide. The market’s rapid growth is driven by industries demanding increasingly complex components, often with tight tolerances and specialized material requirements. Chinese manufacturers have established themselves as key players by investing in advanced equipment and honing their technical expertise. Their focus on custom machining services allows clients to achieve high-precision results that meet exact specifications. The global shift toward localized, reliable manufacturing solutions has further propelled the adoption of expert CNC techniques, making complex parts more accessible regardless of geographic location.
With a broad spectrum of CNC capabilities, including multi-axis milling, turning, and finishing, these manufacturers can handle diverse design intricacies. Moreover, the integration of automation and quality control systems ensures their output remains consistent across batches. This rise of expert CNC machining signifies a movement towards more sophisticated manufacturing paradigms, where precision, durability, and customization are non-negotiable. As a result, companies worldwide now view CNC machining not just as a production method, but as a strategic partner in their product innovation cycles.
The key advantage offered by these experts lies in their ability to interpret complex CAD drawings accurately and transform intricate digital designs into physical realities. This precision is crucial for high-tech sectors where even minute errors can compromise performance. Chinese manufacturers leverage their comprehensive experience to optimize machining processes for difficult geometries and challenging materials. This global proliferation of expert CNC machining is shaping the future of manufacturing, delivering high-quality parts at competitive prices, and reducing lead times significantly.
Another notable trend is the emphasis on full customization. As industries evolve, the need for bespoke components tailored to unique specifications becomes more evident. Expert CNC machining providers excel at turning these tailored designs into precise physical products, supporting innovation and enabling the creation of next-generation devices. Their ability to adapt quickly to new design requirements, combined with cost-effective solutions, makes them indispensable in the global supply chain of high-precision parts.
Furthermore, the integration of Industry 4.0 technologies such as IoT, artificial intelligence, and real-time data analytics is elevating CNC machining standards. These advancements facilitate predictive maintenance, process optimization, and enhanced quality assurance, further strengthening the reliability of high-precision manufacturing. Chinese manufacturers embracing these innovations are setting a competitive edge in the international market, ensuring their clients receive top-tier, precision-engineered components consistently.
In conclusion, the rise of expert CNC machining for high-precision parts underscores a trend towards smarter, more adaptable manufacturing solutions. As industries demand increasingly complex and reliable components, Chinese CNC providers are proving their capability to meet these challenges head-on with advanced technology, extensive experience, and a commitment to customization.
## Custom CNC Solutions: Turning Complex Designs into Reality
Custom CNC solutions are at the heart of modern precision manufacturing, especially when translating complex, detailed designs into tangible parts. This approach involves tailoring machining processes to suit specific project requirements, which often include intricate geometries, tight tolerances, and specialized materials. Chinese CNC manufacturers excel in this domain by offering comprehensive services that start from detailed drawing interpretation to the final finishing stages, ensuring every aspect aligns with client specifications.
One of the key aspects of custom solutions is the ability to realize highly complex designs that are impossible to produce with conventional methods. Advanced multi-axis CNC machines allow for the machining of parts with multiple intersecting geometries, deep cavities, and intricate features. This capability is especially critical for industries such as aerospace, where component precision directly impacts safety and performance. By leveraging these technologies, Chinese manufacturers can produce parts that meet the most stringent standards globally.
Material selection plays a crucial role in custom CNC solutions. Whether working with titanium, stainless steel, aluminum, or specialized composites, the machining process must be adapted accordingly. Custom solutions often involve optimizing cutting parameters, tool selection, and cooling methods to handle challenging materials effectively. Experience in working with a wide range of materials ensures that complex parts are produced with high accuracy, surface quality, and structural integrity.
Furthermore, custom CNC solutions involve close collaboration and communication with clients throughout the manufacturing process. From initial design review and prototype development to full-scale production, manufacturers work to refine the process, ensuring the final product matches the envisioned design. This collaborative approach minimizes errors, reduces waste, and shortens lead times, providing a significant competitive advantage.
The flexibility of custom CNC solutions also extends to post-processing and finishing techniques. Achieving the desired surface finish, dimensional accuracy, and functional coatings require precise control and expertise. Chinese CNC specialists utilize advanced finishing methods such as laser marking, anodizing, and polishing to meet specific aesthetic and functional demands, thereby adding value to the final product.
In addition, custom CNC solutions are particularly advantageous for low-volume or prototype manufacturing, where economies of scale are less significant. The ability to produce small batches with high precision allows clients to test, validate, and iterate their designs rapidly. This agility is vital for innovative products in highly competitive markets, ensuring that complex designs are brought from concept to reality efficiently.
Overall, custom CNC solutions epitomize the fusion of technical expertise, advanced machinery, and collaborative client engagement. Chinese manufacturers’ proficiency in turning complex designs into high-quality physical parts underscores their vital role in the global high-precision manufacturing landscape.
## Mastering High-Precision CNC Machining for Critical Industries
High-precision CNC machining is indispensable in industries where failure is not an option. Aerospace, medical devices, semiconductors, and defense sectors demand components with ultra-tight tolerances, impeccable surface finishes, and material integrity. Chinese CNC manufacturers have proven their mastery in meeting these rigorous standards, positioning themselves as reliable partners for critical industry applications.
In aerospace, for instance, components such as turbine blades, structural brackets, and engine parts require exceptional accuracy to ensure safety and efficiency. These parts often involve complex geometries made from high-performance materials like titanium and superalloys. Chinese CNC machining providers utilize multi-axis machining centers and advanced metrology systems to deliver parts that meet the strict specifications of aerospace OEMs.
Medical device manufacturing also benefits significantly from high-precision CNC processes. Producing intricate implants, surgical instruments, and diagnostic equipment demands not only dimensional accuracy but also biocompatible surface finishes. Chinese manufacturers leverage their expertise in handling delicate materials such as stainless steel, surgical-grade alloys, and medical plastics, ensuring components are sterilizable, durable, and safe for use in sensitive environments.
Semiconductor industry components, such as sputtering targets and photomask frames, require micron-level precision. CNC machining solutions tailored for these applications involve stringent quality control measures and specialized tooling to achieve the necessary accuracy. The capacity of Chinese CNC firms to deliver these highly specialized parts underscores their mastery in high-precision manufacturing for critical sectors.
Defense applications further exemplify the importance of expert CNC machining. Components used in military equipment, radar systems, and missile technology demand high reliability, robustness, and adherence to international standards. Chinese manufacturers often work under strict confidentiality agreements while maintaining their high standards for precision and material integrity.
In addition to achieving precise dimensions, these industries require consistency across large production runs. This consistency is supported by rigorous calibration, real-time monitoring, and advanced inspection techniques, ensuring each part matches the original specifications exactly. The mastery of CNC machining in these sectors underscores the importance of experience, technological investment, and a deep understanding of industry-specific requirements.
Furthermore, the role of continuous innovation in machining techniques and tool development cannot be overstated. Chinese manufacturers actively adopt new cutting technologies, such as high-speed spindle systems and super-precision tools, to push the boundaries of what is achievable in high-precision manufacturing. These efforts significantly enhance the quality, efficiency, and reliability of critical components.
Ultimately, mastery in high-precision CNC machining allows Chinese manufacturers to serve some of the world’s most demanding industries with confidence. Their ability to produce complex, reliable, and compliant parts underscores their vital contribution to global critical infrastructure and technological advancement.
## Advanced Material Application in CNC Machining Processes
The capability to process a wide array of advanced materials is a hallmark of expert CNC machining providers. As industries explore innovative materials for enhanced performance, Chinese manufacturers have adapted their techniques to handle everything from lightweight composites to superalloys. This versatility is essential for producing high-precision, complex parts that meet demanding specifications.
Titanium and its alloys, for example, are popular in aerospace and biomedical applications due to their strength-to-weight ratio and corrosion resistance. Machining these materials requires specialized tools, optimized cutting parameters, and coolant systems to prevent workpiece deformation or tool wear. Chinese CNC firms have accumulated extensive experience in processing titanium, ensuring parts are produced with tight tolerances and pristine surface finishes.
High-performance steels, such as stainless, tool, and Maraging steels, are widely used in tooling, medical, and structural applications. Their hardness and toughness pose challenges for machining, necessitating the use of high-speed tools, precise feed rates, and temperature control. Chinese manufacturers excel in this domain by deploying advanced milling and grinding techniques to achieve precise dimensions without compromising material properties.
In addition to metals, advanced composites like carbon fiber-reinforced plastics (CFRP) and ceramics are increasingly utilized for their lightweight and high-strength attributes. Machining these materials demands not only specialized equipment but also careful control of cutting forces and dust management. Chinese CNC experts have developed processes that prevent fiber fraying and delamination, ensuring the integrity and performance of composite parts.
Specialized materials such as Inconel, Hastelloy, and other superalloys used in extreme environments require even more advanced machining strategies. These superalloys are highly heat-resistant but difficult to machine due to their work-hardening properties. Chinese CNC providers adapt by utilizing high-precision coolant systems, cutting-edge tooling, and optimized machining paths.
The application of additive manufacturing combined with CNC machining is also expanding, allowing for hybrid processes that produce complex parts from difficult materials. This integration enhances design flexibility and reduces material waste, offering more efficient solutions for highly specialized components.
The mastery of working with diverse materials underscores the importance of continuous technological upgrades, skill development, and in-depth knowledge of material behavior. Chinese CNC machining companies invest heavily in research and development, ensuring they stay ahead in processing the most challenging materials on the market.
By expanding their material processing capabilities, Chinese manufacturers can cater to a broader range of industries and applications, providing high-precision parts that meet the stringent standards of tomorrow’s advanced technology sectors.
## Overcoming Challenging Manufacturing Tasks with Expert Skills
Manufacturing complex and high-precision parts often involves overcoming numerous technical challenges. Chinese CNC machining experts bring a wealth of experience, innovative techniques, and problem-solving skills to tackle these difficulties efficiently. Their expertise ensures that even the most demanding tasks are completed accurately and reliably.
One common challenge is machining deep, narrow cavities or intricate internal geometries. These features require specialized tooling, multi-axis machining, and careful planning to avoid tool deflection and ensure accurate dimensional control. Chinese manufacturers utilize high-precision CNC machines with multiple axes and advanced simulation software for optimal tool path planning.
Handling difficult materials such as superalloys, ceramics, or composites further complicates manufacturing. These materials may have high hardness, low thermal conductivity, or abrasive properties, making them prone to rapid tool wear or deformation. Skilled operators and engineers optimize cutting parameters, select appropriate tools, and implement cooling techniques to mitigate these issues.
Tight tolerances and surface finish requirements demand rigorous quality control. Experts employ comprehensive inspection methods, including coordinate measuring machines (CMM) and optical comparators, to verify part accuracy at every stage. Feedback loops are used to adjust machining parameters dynamically, ensuring continuous adherence to specifications.
Another challenge involves managing complex heat treatment and finishing processes. Some components require precise surface treatments, polishing, or coatings that must be integrated seamlessly with CNC machining. Chinese manufacturers coordinate these processes to maintain dimensional stability and functional performance.
Design complexity often introduces manufacturability issues. Experienced CNC specialists work closely with designers during the prototyping phase, offering insights on how to modify features for easier machining without compromising functionality. This proactive collaboration reduces costly rework or delays.
The integration of automation and digital monitoring tools enhances the ability to detect and correct issues in real time. Machine sensors track parameters such as vibration, temperature, and cutting forces, allowing operators to respond quickly and prevent defects.
Finally, ongoing training and continuous skill development are vital for overcoming manufacturing challenges. Chinese CNC companies invest in their workforce, encouraging innovative problem-solving and mastery of the latest machining techniques. This human expertise, combined with technological advancements, makes it possible to address even the most complex manufacturing tasks effectively.
## Case Studies: Solving Global CNC Machining Difficulties
Examining real-world examples highlights how Chinese CNC manufacturers have successfully overcome global machining challenges through expertise and innovation. These case studies demonstrate their ability to deliver solutions for diverse industries with complex requirements.
In one aerospace project, a client required a series of titanium components with complex internal channels and tight tolerances. The Chinese manufacturer employed multi-axis CNC milling combined with advanced simulation software to optimize tool paths. The result was parts that met all specifications, with surface finishes exceeding industry standards, in a significantly shortened lead time.
A medical device company sought to produce intricate surgical instruments from stainless steel with high surface smoothness. The Chinese CNC team utilized precision grinding, polishing, and coating techniques alongside meticulous process controls. The outcome was instruments that adhered to strict biocompatibility and sterilization requirements, passing all regulatory inspections.
For a semiconductor industry client, the challenge involved machining extremely thin and precise frames from specialized alloys. The Chinese specialists used ultra-high-speed spindles and micro-milling tools to achieve micron-level accuracy. The parts' consistent quality enabled the client to improve production yields and device performance.
An automotive supplier faced difficulties machining deep, narrow cavities in high-hardness steel for engine components. The Chinese experts employed custom-designed tooling, adaptive cooling systems, and real-time monitoring to prevent tool wear and deformation. The successful production reduced waste and improved component lifespan.
In a defense application, a client demanded components with complex geometries from superalloys that resist extreme conditions. The Chinese manufacturer adopted cutting-edge high-pressure coolant systems and high-precision tool management, overcoming material work-hardening and achieving defect-free parts with tight tolerances.
These case studies exemplify the problem-solving capacity of Chinese CNC machining providers. Their ability to adapt, innovate, and collaborate effectively with clients demonstrates their leadership in overcoming global manufacturing difficulties.
## The Importance of Experience in High-Complexity CNC Projects
Experience is arguably the most critical factor in executing high-complexity CNC projects successfully. Chinese manufacturers that have accumulated years of hands-on expertise understand the nuances of machining challenging geometries, materials, and quality standards. Their seasoned knowledge ensures efficient project execution and high-quality outcomes.
Veteran engineers and operators can interpret complex CAD drawings accurately, foreseeing potential manufacturing issues before production begins. This foresight allows for process optimization, reducing errors, rework, and waste. Their familiarity with various machining strategies enables them to select the most suitable methods for each unique project.
In handling difficult materials, experienced teams know how to adjust cutting speeds, feeds, and tooling to extend tool life and maintain accuracy. They also understand when to employ specialized processes like cryogenic machining or ultrasonic cutting to achieve desired results. Such insights are invaluable in high-stakes industries like aerospace and medical devices.
Experience also plays a vital role in troubleshooting unexpected issues during production. Seasoned professionals can quickly identify root causes of defects, implement corrective actions, and prevent recurrence. This rapid response capability minimizes downtime and ensures consistent supply chain reliability.
Furthermore, experienced CNC providers understand the importance of comprehensive quality control. They have established rigorous inspection protocols, calibration routines, and documentation practices that meet international standards. Their familiarity with industry-specific certifications adds confidence for clients operating in highly regulated sectors.
The ability to adapt to evolving technology trends is another benefit of extensive experience. Veteran manufacturers invest in continuous training and process upgrades, enabling them to leverage the latest CNC innovations, materials, and finishing techniques effectively.
In essence, the depth of experience translates into higher success rates, better surface finishes, precise tolerances, and overall improved manufacturing reliability. For clients, partnering with experienced Chinese CNC specialists means trusting in a proven track record of delivering complex, high-precision parts that meet exacting standards.
## How Precise Drawing Interpretation Enhances Manufacturing Quality
Accurate interpretation of engineering drawings and CAD models is fundamental to producing high-precision, complex parts. Chinese CNC manufacturers emphasize meticulous reading and understanding of detailed technical documents, which forms the foundation of quality manufacturing.
Precise drawing interpretation involves analyzing every aspect of the design, including dimensions, tolerances, surface finishes, and material specifications. Skilled engineers visualize how the part will be machined, identifying potential manufacturing challenges early in the process. This proactive approach minimizes errors and ensures that the final product aligns perfectly with the original concept.
Advanced CAD/CAM software plays a pivotal role in translating drawings into machine instructions. Chinese manufacturers utilize sophisticated simulation tools that predict machining paths, identify potential collisions, and optimize cutting sequences. These virtual tests help prevent costly mistakes before actual production begins.
Clear communication with clients is also essential. When drawings contain ambiguous or complex features, experienced interpreters consult with designers to clarify intent, suggest design modifications, or recommend alternative manufacturing methods. Such collaboration enhances the manufacturability and reduces lead times.
In high-precision projects, even minor misinterpretations can result in dimensional inaccuracies or surface defects. Therefore, rigorous inspection and verification procedures are employed throughout the process. Coordinate measuring machines (CMM) and optical comparators validate each critical dimension, ensuring the part conforms precisely to the drawings.
Standardization of documentation, including detailed process sheets and inspection reports, promotes consistency and traceability. These records provide evidence of compliance with industry standards and facilitate quality audits.
The impact of precise drawing interpretation extends beyond accuracy. It influences tooling design, fixture setup, and process planning, all of which contribute to efficiency and repeatability. When design intent is faithfully translated into manufacturing, the risk of rework, delays, and material waste diminishes significantly.
Ultimately, mastering the interpretation of complex drawings ensures that Chinese CNC machining services deliver parts that surpass client expectations in quality, functionality, and reliability. This expertise is a cornerstone of successful high-precision manufacturing on a global scale.
## Innovations in CNC Technology for Difficult-to-Machine Materials
Advancements in CNC technology have revolutionized the processing of difficult materials, unlocking new possibilities for high-precision, complex parts. Chinese manufacturers actively incorporate these innovations to meet the ever-growing demands of industries like aerospace, medical, and defense.
One key innovation is the development of high-speed spindle systems that enable faster material removal rates while maintaining accuracy. These spindles can operate at thousands of RPMs, reducing machining time for tough materials such as titanium and superalloys. The increased speed also improves surface finish quality, crucial for functional and aesthetic purposes.
The introduction of ultra-precision tools with harder, more wear-resistant coatings—such as diamond-like carbon (DLC) and TiAlN—extends tool life and enables finer machining of abrasive materials. These tools facilitate the production of components with intricate details and tight tolerances, even in challenging substrates.
Active cooling systems, including high-pressure coolant delivery and cryogenic cooling options, are now standard in advanced CNC machines. These systems effectively reduce heat generation, prevent workpiece deformation, and suppress tool wear when machining high-temperature or work-hardened materials.
Smart sensor integration allows real-time monitoring of cutting forces, vibrations, and temperature during machining. Data from these sensors help optimize cutting parameters dynamically, preventing defects and enhancing process stability. Such intelligent systems are particularly beneficial when machining exotic alloys and composites.
Furthermore, additive manufacturing combined with CNC machining—often referred to as hybrid manufacturing—enables the fabrication of complex geometries from difficult materials that would be impossible or inefficient with traditional methods alone. This synergy accelerates prototyping and production of sophisticated parts.
In the realm of software, advancements in simulation and CAM programming tools allow for precise planning of tool paths and process parameters tailored to difficult materials. These virtual environments help predict potential issues and refine techniques before actual machining, saving time and resources.
The continuous pursuit of innovation in CNC technology by Chinese manufacturers ensures they remain at the forefront of processing challenging materials. By leveraging these cutting-edge solutions, they can produce high-precision parts that meet the demanding specifications of modern industries worldwide.
## Ensuring Consistency and Accuracy in Large-Scale Production
Maintaining consistency and accuracy over large production runs is a critical challenge in high-precision CNC machining. Chinese manufacturers focus on implementing robust quality management systems, advanced equipment, and process standardization to meet these demands reliably.
Automated CNC machines with high repeatability are fundamental to producing identical parts across batches. These machines are equipped with precise servo controls, high-resolution encoders, and vibration damping systems, ensuring stability and accuracy during extended production runs.
Regular calibration of tools, fixtures, and measurement systems is essential. Chinese manufacturers utilize calibrated CMMs and laser trackers to verify machine accuracy periodically. This proactive approach prevents drift and ensures each part remains within specified tolerances.
Process control software plays a vital role in monitoring machining parameters such as spindle speed, feed rate, and coolant flow. Real-time data collection allows operators to detect deviations instantly and make adjustments, preserving quality consistency.
Standardized fixturing and tooling setups reduce variability caused by part positioning or clamping differences. Customized fixtures designed for specific components improve repeatability and reduce setup times, enhancing overall efficiency.
Training and workforce expertise are crucial for consistency. Skilled operators understand the importance of strict adherence to established procedures, which minimizes human error. Continuous training ensures staff remains proficient in operating complex machinery and quality protocols.
Quality assurance extends beyond in-process inspection. Final evaluation using high-precision measurement tools verifies that all parts conform to design specifications. Statistical process control (SPC) techniques are used to analyze production data and identify trends, facilitating process improvements.
In high-volume manufacturing, implementing lean principles and Six Sigma methodologies helps eliminate waste and reduce variation. These practices optimize workflows, improve productivity, and uphold the highest standards of accuracy and consistency.
The integration of Industry 4.0 technologies, such as IoT sensors and data analytics, further enhances large-scale production control. Predictive maintenance and process optimization ensure machines operate at peak performance, reducing downtime and maintaining quality standards.
By combining technological advancements with disciplined process management and skilled personnel, Chinese CNC manufacturers can deliver large quantities of high-precision parts with unwavering consistency, reinforcing their reputation for excellence on the global stage.
## Collaborating with Overseas Clients for Tailored CNC Solutions
Effective collaboration with overseas clients is essential for delivering tailored CNC solutions that meet specific international standards and project requirements. Chinese manufacturers recognize this importance and prioritize transparent communication, flexible service offerings, and comprehensive support.
From the initial inquiry, detailed technical discussions are conducted to fully understand the client’s design intent, application environment, and quality expectations. Clear documentation and regular updates ensure alignment throughout the manufacturing process, minimizing misunderstandings.
Using advanced CAD/CAM systems and virtual simulation tools allows clients to visualize the machining process and review critical features before production begins. This collaborative planning enhances efficiency and ensures the final product precisely matches the design specifications.
Cultural and language differences can pose challenges, so many Chinese manufacturers employ multilingual teams and establish dedicated project management personnel to facilitate seamless communication. They also adapt to clients’ preferred working hours and communication channels to ensure timely responsiveness.
Customization extends beyond technical specifications. Manufacturers often offer flexible production quantities, prototype development, and rapid turnaround services to accommodate evolving project needs. Their ability to scale production as required provides clients with greater agility in their product development cycles.
Quality standards compliance is a priority, especially for clients in regulated industries. Chinese CNC firms are familiar with global certifications such as ISO, ASME, and industry-specific standards, ensuring parts meet all legal and safety requirements.
Logistics and supply chain management are integral to successful collaboration. Chinese manufacturers coordinate shipping, customs clearance, and delivery schedules meticulously, providing clients with peace of mind regarding timely receipt of their components.
Feedback loops and after-sales support further strengthen partnerships. Clients can request modifications, improvements, or troubleshooting assistance post-delivery, fostering long-term relationships based on trust and mutual success.
Overall, the ability to collaborate effectively with overseas clients enables Chinese CNC manufacturers to deliver highly customized, high-quality parts that adhere to international standards. This global partnership approach bolsters their reputation as trusted suppliers of complex, high-precision components worldwide.
## Future Trends in High-Precision CNC Machining Industry
Looking ahead, the high-precision CNC machining industry is poised for significant technological and strategic advancements. Chinese manufacturers are actively investing in innovations to stay ahead of evolving global demands for complex, reliable, and cost-effective parts.
One prominent trend is the integration of artificial intelligence (AI) and machine learning into CNC systems. These technologies will enable real-time process optimization, predictive maintenance, and defect detection, leading to smarter, more autonomous manufacturing operations.
The development of advanced materials will continue to be a focus. As industries explore lighter, stronger, and more heat-resistant materials, CNC providers will innovate processing techniques to handle these substances efficiently, broadening application possibilities.
Additive manufacturing’s synergy with traditional CNC machining is expected to expand. Hybrid processes will facilitate the production of highly complex geometries with reduced waste and shorter lead times, transforming traditional manufacturing paradigms.
Industry 4.0 and the Internet of Things (IoT) will further enhance production transparency and control. Data-driven decision-making will improve process stability, quality consistency, and supply chain responsiveness, making high-precision manufacturing more agile and resilient.
Sustainability considerations will also influence future trends. Manufacturers will adopt eco-friendly cutting fluids, energy-efficient machinery, and waste-reduction strategies to align with global environmental standards and consumer expectations.
Customization and small-batch, rapid prototyping services will grow in importance, driven by the need for innovation in sectors like biotech, aerospace, and electronics. Flexible, digitally integrated manufacturing systems will make this possible at scale.
Finally, emerging technologies such as quantum computing and nanotechnology could unlock unprecedented levels of precision and material manipulation, opening new horizons for high-precision CNC applications.
In summary, the future of high-precision CNC machining will be characterized by smarter, more sustainable, and highly adaptable manufacturing ecosystems. Chinese manufacturers, with their ongoing commitment to technological innovation and global collaboration, are well-positioned to lead these transformative trends, shaping the next era of precision engineering worldwide.