Expert CNC Machining for High-Precision Custom Metal Parts
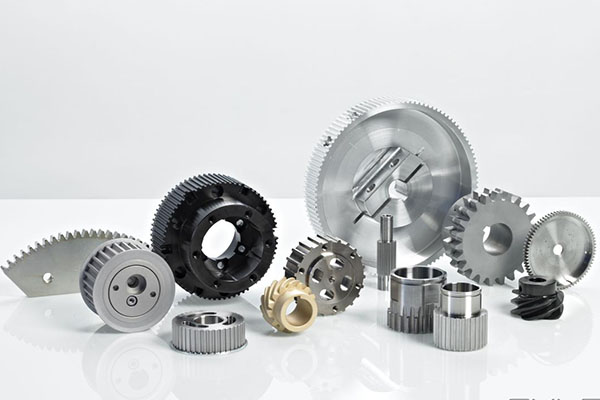
In today’s manufacturing landscape, the demand for high-precision, custom metal parts continues to grow across various industries—from aerospace and medical devices to electronics and automotive sectors. Achieving such exacting standards requires more than just standard machining techniques; it demands expertise in CNC (Computer Numerical Control) machining. Expert CNC machining firms leverage advanced technology, skilled craftsmanship, and meticulous quality assurance processes to turn complex designs into functional, durable components. This article explores the critical role of specialized CNC machining services in producing high-precision, custom metal parts, emphasizing the importance of material selection, handling complex geometries, and maintaining consistent quality throughout the manufacturing journey.
The Importance of Expert CNC Machining in High-Precision Metal Parts
Expert CNC machining is fundamental for producing high-precision metal components that meet rigorous specifications. Unlike manual methods, CNC machining offers unmatched accuracy, repeatability, and efficiency, making it ideal for complex, small-batch, or prototype runs. Skilled machine operators understand not only the technical capabilities of their equipment but also how various factors—such as cutting speeds, tool paths, and coolant application—affect final tolerances. Their expertise ensures that each part conforms to the tightest tolerances, sometimes within just a few microns. High-precision machining also minimizes material waste, reduces post-processing needs, and accelerates production cycles, providing clients with cost-effective solutions. Moreover, expert CNC shops can interpret detailed drawings and convert them into precise tool paths, ensuring that intricate geometries and fine features are accurately realized.
Custom CNC Machining: Turning Your Designs into Reality
Custom CNC machining transforms digital designs into tangible metal parts with exceptional precision. Clients often provide detailed CAD files or technical drawings that specify dimensions, surface finishes, and material requirements. Skilled CNC manufacturers then create a comprehensive manufacturing plan, selecting suitable tools and machining strategies tailored to the project. This process involves multiple steps, including programming, setup, and calibration, to ensure the machine operates flawlessly during production. The ability to adapt to unique design features—such as complex contours, internal cavities, or micro-scale details—sets expert CNC machining apart. These firms also often include services such as prototyping, testing, and iterative adjustments, ensuring that each custom part aligns perfectly with client specifications. The result is a highly accurate, durable component that functions reliably in demanding environments.
Handling Complex and High-Difficulty Parts with Precision
High-precision CNC machining excels at fabricating parts with complex geometries and high difficulty levels. These components often feature intricate internal channels, sharp corners, thin walls, or micro-fine features that challenge conventional manufacturing methods. Expert machinists utilize advanced strategies such as multi-axis machining, micro-milling, and specialized tooling to achieve the desired outcomes. They also plan machining sequences meticulously to avoid issues like tool deflection, vibrations, or thermal distortion. For example, aerospace components requiring tight tolerances and complex shapes demand a high degree of skill and technology to ensure safety and performance. Similarly, medical devices with micro-features necessitate precise control over every micron. Handling such difficult parts requires not only sophisticated equipment but also a deep understanding of material properties, cutting dynamics, and process optimization.
Selecting the Right Materials for Your Custom Metal Components
Material selection plays a pivotal role in the success of high-precision CNC machining projects. Different metals—such as aluminum, stainless steel, titanium, or specialty alloys—offer unique characteristics in terms of strength, corrosion resistance, weight, and machinability. Expert CNC shops advise clients on the most suitable materials based on the application’s specific requirements, including environmental conditions and load-bearing needs. For instance, aerospace components often require titanium or high-strength alloys, while medical implants may demand biocompatible stainless steel or cobalt-chromium alloys. The choice of material also influences machining parameters, tool selection, and surface finish. Proper handling and preparation of raw materials are essential to minimize defects like warping or internal stresses, which can compromise precision and durability. Skilled manufacturers understand the nuances of working with various metals and can optimize processes accordingly to ensure high-quality, reliable parts.
The Role of Advanced Equipment in Achieving Tight Tolerances
Achieving tight tolerances in high-precision CNC machining hinges on the use of advanced, state-of-the-art equipment. Multi-axis CNC machines, high-speed spindles, and precision tool holders enable complex geometries to be machined with minimal error. Sophisticated control systems provide real-time monitoring and adjustments, ensuring consistent accuracy throughout production runs. Additionally, high-quality measurement and inspection tools—such as coordinate measuring machines (CMM)—are integrated into the process to verify dimensions at every stage. Automation and robotics further enhance repeatability and reduce human error. These technological advancements are crucial for meeting the stringent tolerances demanded by industries like aerospace, medical, and electronics. An investment in cutting-edge equipment not only improves precision but also shortens lead times, enabling faster turnaround for high-value, complex projects.
Why Experience Matters in High-Precision CNC Machining
Experience is perhaps the most valuable asset for CNC machining providers specializing in high-precision parts. Seasoned manufacturers have encountered and overcome a wide array of challenges, from material inconsistencies to complex toolpath strategies. Their familiarity with different metals and machining techniques enables them to optimize processes for maximum accuracy and efficiency. Experienced firms can interpret intricate technical drawings and suggest design modifications to improve manufacturability without compromising functionality. They also possess a deep understanding of potential defects like burrs, internal stresses, or surface imperfections, knowing how to prevent or correct them. Such expertise fosters innovation and continuous improvement, ensuring that clients receive parts that meet the highest standards. Ultimately, a track record of successful projects and satisfied clients underscores the critical importance of experience in delivering reliable, high-precision CNC machining services.
Overcoming Common Challenges in Custom Metal Part Fabrication
Fabricating custom metal parts with high precision involves navigating numerous challenges, including material distortions, tool wear, and complex geometries. Material properties such as hardness and thermal conductivity can affect machining stability and surface finish. Tool wear is another concern, especially when working with hard metals, requiring meticulous tool management and replacement strategies. Complex internal features or micro-sized details demand precise setup and calibration, often pushing the limits of machine capabilities. Thermal expansion during machining can cause slight deviations, so managing heat and maintaining stable working conditions are vital. Expert CNC shops employ advanced simulation software, rigorous quality checks, and iterative testing to identify and mitigate potential issues early in the process. Their ability to adapt machining parameters and implement corrective actions ensures consistent, high-quality results despite these challenges.
Global Case Studies: Solving Classic CNC Machining Difficulties
Across the globe, top-tier CNC machining companies have tackled classic difficulties such as manufacturing micro-scale medical components, aerospace parts with extreme tolerances, or high-strength alloy gears. For example, in aerospace, engineers faced the challenge of machining ultra-thin-walled components with minimal deformation, solved by employing multi-axis machining combined with real-time monitoring. Medical device manufacturers have encountered micro-milling challenges, overcoming them through specialized tooling and controlled environments to prevent micro-cracking or warping. In the electronics sector, miniaturized connectors required precise slotting and drilling on hard-to-machine materials, achieved through optimized cutting parameters and vibration damping techniques. These case studies exemplify how expertise, advanced machinery, and innovative process planning can resolve longstanding manufacturing difficulties, setting new standards for high-precision CNC production.
From Drawings to Finished Parts: The Complete CNC Manufacturing Process
Transforming detailed technical drawings into finished high-precision metal parts involves a comprehensive process. It begins with the design review and material procurement, ensuring that specifications are feasible and materials are of high quality. Next, CAD/CAM programming translates the 3D models into precise machine instructions, considering optimal tool paths and cutting parameters. Setup and calibration of CNC machines follow, requiring meticulous attention to detail to ensure all axes are aligned and tools are correctly mounted. During machining, real-time monitoring helps detect and correct deviations promptly. Post-machining processes, such as surface finishing, deburring, and heat treatment, prepare the parts for final inspection. Quality control is conducted using advanced measurement tools like CMMs, verifying dimensions against specifications. The entire journey from concept to finished part demands seamless coordination, technical expertise, and rigorous quality assurance at every stage.
Ensuring Quality and Consistency in High-Precision CNC Projects
Maintaining consistent quality in high-precision CNC machining projects hinges on stringent quality control protocols. This includes initial material inspection, continuous process monitoring, and comprehensive final inspection. Real-time data collection during machining helps identify deviations early, allowing for immediate adjustments. Regular calibration of machines ensures that tolerances are maintained over long production runs. Advanced inspection equipment like 3D scanners and coordinate measuring machines validate critical dimensions and surface finishes. Documentation and traceability are also vital, providing clients with confidence in the quality of each batch. Moreover, implementing ISO or industry-specific standards reinforces process consistency and quality assurance. Skilled operators and quality assurance teams collaborate closely to uphold these standards, ensuring each part meets the exacting requirements of high-precision applications.
The Benefits of Partnering with a Reliable CNC Machining Vendor
Partnering with a reputable CNC machining provider offers numerous advantages for high-precision projects. Such firms bring a wealth of experience, technical expertise, and access to cutting-edge technology, ensuring superior quality and faster turnaround times. They can adapt to complex design requirements and provide valuable insights to optimize manufacturability and cost-efficiency. Reliable vendors also prioritize quality assurance, implementing strict inspection protocols and traceability measures. This partnership fosters innovations like design for manufacturability (DFM) consultations, helping clients refine their drawings for better results. Additionally, trusted CNC partners often support scalable production, from prototypes to mass manufacturing, ensuring consistency throughout. Ultimately, working with a dependable vendor reduces risks, enhances product reliability, and accelerates time-to-market for high-precision metal parts.

CNC
Future Trends in CNC Machining for High-Precision Applications
The future of CNC machining for high-precision applications is driven by technological innovations such as AI-driven process optimization, machine learning, and automation. These advancements promise even tighter tolerances, faster cycle times, and reduced human intervention. Additive manufacturing combined with CNC processes will enable hybrid fabrication methods, expanding design possibilities for complex geometries. The adoption of Industry 4.0 principles facilitates real-time data analytics, predictive maintenance, and smarter quality control. Materials science will also evolve, with new alloys and composites that offer enhanced performance and machinability. Furthermore, sustainable manufacturing practices—such as energy-efficient machines and eco-friendly coolants—are becoming more prevalent. These innovations will empower manufacturers to deliver higher quality, more complex, and environmentally responsible high-precision components worldwide.
Expert CNC machining plays an indispensable role in delivering high-precision, custom metal parts for demanding industries across the globe. By leveraging advanced equipment, material expertise, and many years of experience, top-tier CNC firms can successfully navigate complex geometries, tight tolerances, and material challenges. Their commitment to quality assurance and process innovation ensures that clients receive reliable, durable components that meet the highest standards. As technology continues to evolve, CNC machining will become even more precise, efficient, and sustainable, opening new possibilities for innovative product design and manufacturing excellence. Partnering with a skilled CNC provider is not just a strategic choice but a critical step toward achieving manufacturing success in today’s competitive global market.