Expert CNC Machining for High-Precision Custom Parts Worldwide
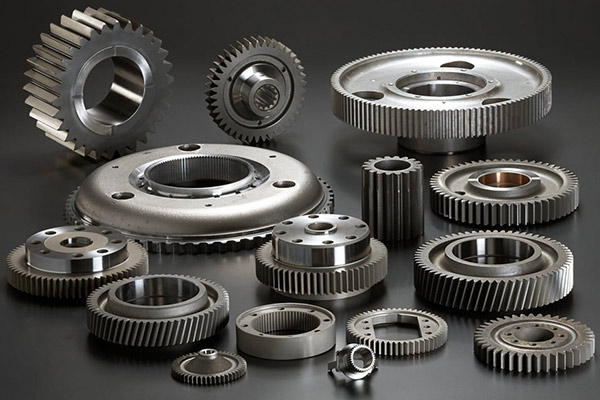
===INTRO:
In today's interconnected manufacturing landscape, the demand for high-precision, custom CNC parts is surging across industries worldwide. From aerospace to medical devices, the need for complex, reliable components necessitates expert machining capabilities and advanced technology. Chinese CNC manufacturers have stepped into this arena, delivering sophisticated solutions tailored to international clients. This article explores how expert CNC machining elevates global manufacturing, emphasizing customization, material mastery, technological advancements, and the critical role of experience in achieving exceptional precision and quality.
## Unlocking High-Precision Custom CNC Parts for Global Markets
High-precision CNC machining has become a cornerstone for industries requiring intricate and reliable components. Chinese manufacturers now serve a worldwide customer base by offering customized solutions that meet exact specifications. The process begins with understanding detailed design requirements, translating them into precise, manufacturable parts through advanced CNC technology. These parts often involve tight tolerances, complex geometries, and demanding material considerations. By leveraging sophisticated equipment and skilled craftsmanship, these manufacturers can produce high-quality, consistent results regardless of geographic boundaries. The ability to customize each part according to client's unique specifications makes CNC machining an indispensable tool in modern manufacturing.
Furthermore, the global market's diverse needs push Chinese CNC providers to develop versatile capabilities. Whether it's small, delicate medical components or large aerospace structural parts, the flexibility of CNC technology allows for efficient production. The integration of CAD/CAM systems ensures that complex designs are accurately interpreted and machined with minimal error. This precision not only enhances product performance but also reduces waste and production costs. As a result, international clients increasingly trust Chinese CNC manufacturers to deliver custom parts that meet their stringent standards, reinforcing the global reach and competitiveness of Chinese machining services.
Advanced CNC machining enables rapid prototyping and small-batch production, which is vital for industries like aerospace, automotive, and healthcare. Clients can experiment with different designs and materials without significant upfront costs. The scalability of CNC manufacturing also allows for easy transition from prototype to mass production once the design is validated. This agility is crucial for companies aiming to bring innovative products to market swiftly. By providing high-precision, custom solutions at competitive prices, Chinese CNC manufacturers are facilitating innovation and helping clients stay ahead in their respective fields.
Quality assurance is integral to unlocking trust in high-precision parts. Many Chinese CNC providers employ rigorous inspection protocols, including coordinate measuring machines (CMM), laser scanning, and other advanced measurement techniques. These ensure that every part adheres strictly to design tolerances, with deviations minimized to micrometer levels. Furthermore, comprehensive documentation and traceability systems bolster confidence for clients who require regulatory compliance or certification. This commitment to quality, combined with customization flexibility, makes Chinese CNC machining a reliable partner for global industries demanding excellence.
Sustainability and efficiency in high-precision machining are also growing priorities. Chinese manufacturers are adopting eco-friendly practices, such as optimizing cutting parameters to reduce material waste and energy consumption. Automation and intelligent manufacturing systems enhance productivity while maintaining precision standards. These efforts not only support global environmental goals but also improve turnaround times and cost-effectiveness, benefitting international customers. As the industry evolves, the integration of Industry 4.0 concepts further enhances the capability of Chinese CNC companies to deliver innovative, high-quality custom parts worldwide.
In summary, unlocking high-precision custom CNC parts for global markets involves a synergy of advanced technology, skilled craftsmanship, rigorous quality control, and flexible manufacturing processes. Chinese CNC providers have positioned themselves as key players by continuously upgrading their equipment and expertise. Their ability to tailor solutions to intricate specifications while maintaining high standards opens new horizons for industries worldwide, fostering innovation and competitiveness in diverse sectors.
---
## How Expert CNC Machining Meets Complex Customer Specifications
Meeting complex customer specifications with CNC machining is both an art and a science. Expert CNC manufacturers understand that each client’s requirements are unique, often involving intricate geometries, fine details, and tight tolerances. To achieve this, they utilize sophisticated design interpretation tools, such as CAD/CAM software, which enable precise translation of conceptual ideas into machine commands. These tools facilitate the creation of complex toolpaths that can handle challenging features like undercuts, deep cavities, and micro-sized components seamlessly.
The process begins with in-depth consultation and thorough review of the design files. Experienced CNC professionals assess the feasibility of manufacturing intricate features and recommend adjustments if necessary to optimize machinability without compromising quality. This collaborative approach ensures that the final product aligns perfectly with the customer’s expectations. Skilled machinists select appropriate cutting tools, speeds, and feeds tailored to the material and complexity of the part. This meticulous planning is essential for achieving high precision and surface finish in complex parts.
Furthermore, expert CNC machining involves iterative testing and validation stages. Prototype runs are often performed to verify that the machine settings produce parts within specified tolerances. Any deviations are analyzed, and adjustments are made to fine-tune the process. Continuous feedback loops and advanced measurement techniques ensure that even the most demanding specifications are met consistently. This level of attention to detail underscores the importance of experience and expertise in complex manufacturing scenarios.
Adaptive problem-solving is a hallmark of true CNC mastery. When encountering design features that are difficult to machine—such as sharp internal corners or complex curves—experts employ specialized tooling, multi-axis machining, and innovative strategies. These solutions allow for efficient processing while maintaining the integrity of delicate features. By leveraging multi-axis machining centers, manufacturers can access hard-to-reach areas and perform multiple operations in a single setup, reducing errors and production time.
Material behavior also plays a crucial role in meeting complex specifications. Different materials respond differently to machining forces, heat, and cutting speeds. Expert CNC operators select optimal parameters and tooling to accommodate these variables, ensuring the accuracy and surface quality of highly detailed parts. This nuanced understanding of material properties is vital for producing reliable, high-performance components across diverse industries.
In addition to technical prowess, communication and project management are critical. Expert CNC providers maintain transparent dialogue with clients throughout the process, providing updates and requesting clarifications to prevent misunderstandings. This proactive engagement minimizes rework and accelerates delivery schedules. It also fosters lasting relationships based on trust and shared commitment to quality.
Custom CNC solutions also extend to post-processing treatments, such as polishing, coating, or heat treatment, which enhance functionality and aesthetics. Professionals coordinate these processes carefully to preserve dimensional accuracy and surface integrity. Such holistic approaches to manufacturing reflect the deep expertise necessary to meet complex customer specifications comprehensively.
In essence, expert CNC machining excels at transforming complex, detailed designs into tangible, high-precision parts. It requires a blend of technical mastery, innovative problem-solving, and effective communication. By leveraging years of experience and advanced technology, Chinese CNC manufacturers are adept at fulfilling the most challenging client requirements worldwide, setting standards for precision and reliability across industries.
---
## The Role of Material Selection in Precision CNC Manufacturing
Material selection is fundamental to achieving high-precision CNC parts that meet both functional and aesthetic requirements. Different materials possess unique machining characteristics, strength profiles, and resistance properties, all of which influence the manufacturing process and final product quality. Chinese CNC manufacturers emphasize understanding these properties to optimize cutting strategies, tooling, and finishing techniques for each material.
Metals like aluminum, titanium, stainless steel, and various alloys are common in precision applications. Aluminum, favored for its lightweight and machinability, allows for rapid production and excellent surface finishes. Titanium, on the other hand, offers exceptional strength-to-weight ratio and corrosion resistance, making it ideal for aerospace and medical industries, but requires specialized tooling and slower machining speeds. Stainless steel provides durability and hygiene, often used in medical devices and food processing equipment, demanding precise control over cutting parameters to avoid deformation or tool wear.
Beyond metals, composite materials such as carbon fiber-reinforced plastics are increasingly used for their lightweight and high-strength properties. Machining composites presents unique challenges, including potential fiber fraying and heat generation, which necessitate specific cutting tools and techniques. Expert CNC manufacturers tailor their processes to handle these materials efficiently, ensuring tight tolerances and excellent surface quality.
Ceramics and advanced polymers are also part of the material palette for high-precision parts. Ceramics offer high temperature resistance and hardness but are brittle and difficult to machine. Polymeric materials like PEEK and PTFE provide chemical resistance and biocompatibility, suitable for medical and industrial applications. Processing these materials requires careful selection of cutting speeds, tool materials, and cooling methods to prevent cracking or melting.
Material properties directly influence tool life and machining efficiency. Harder or abrasive materials, such as tool steels or ceramics, wear tools more quickly, requiring frequent tool changes and process adjustments. Conversely, softer materials allow for faster cutting speeds but may deform if not handled properly. Chinese CNC manufacturers invest in high-quality tooling and adaptive control systems to extend tool life and maintain precision across a variety of materials.
Material finishing processes, including polishing, coating, or surface treatments, are also critical in high-precision applications. These processes enhance corrosion resistance, wear properties, or aesthetic appeal. Proper material selection ensures compatibility with these post-processing steps, leading to better overall performance and longevity of the parts.
In many cases, material cost and availability influence design decisions. Chinese CNC providers offer extensive experience in sourcing and working with a broad range of materials, allowing clients to balance performance requirements with budget constraints. This expertise helps optimize both the manufacturing process and the final product quality.
Understanding the thermal and mechanical behavior of materials during machining enables manufacturers to develop customized strategies that minimize defects like warping, cracking, or residual stresses. Advanced software simulations and empirical data guide these decisions, making high-precision manufacturing more predictable and reliable.
Ultimately, material selection is a strategic component of precision CNC manufacturing. It determines not only how parts are produced but also how they perform in their intended environments. Chinese manufacturers' deep material expertise ensures that clients receive parts that meet strict specifications, perform reliably under operational stresses, and maintain their integrity over time.
---
## Mastering Difficult-to-Machine Materials for High-Quality Parts
Processing difficult-to-machine materials is a hallmark of advanced CNC manufacturing. These materials, often chosen for their unique properties such as high strength, temperature resistance, or chemical stability, demand specialized knowledge, tooling, and machinery. Chinese CNC factories have invested heavily in mastering these challenges, delivering high-quality, precision components for critical industries.
Titanium alloys exemplify challenging materials. Known for their strength-to-weight ratio and corrosion resistance, titanium is notoriously tough to machine due to its low thermal conductivity and tendency to work harden. Skilled operators utilize high-quality carbide or ceramic tools, optimized cutting parameters, and effective coolant strategies to overcome these issues. Multi-axis machining and stable fixturing are also employed to ensure dimensional accuracy and surface finish.
Superalloys like Inconel are another class of difficult materials, often used in aerospace and high-temperature environments. Their high strength at elevated temperatures makes them resistant to deformation but complicates machining. Advanced techniques, including cryogenic cooling and high-pressure coolant systems, are employed to maintain tool life and dimensional precision. These methods reduce heat buildup and prevent material adhesion on cutting tools.
Hard ceramics and tungsten-based materials pose unique challenges due to their extreme hardness and brittleness. Precision grinding and diamond-tipped tools are often necessary for finishing operations. In some cases, laser or electrical discharge machining (EDM) is combined with CNC for complex geometries that are impossible to achieve solely through traditional machining.
Composite materials like carbon fiber-reinforced plastics require careful handling. While they are lightweight and strong, their anisotropic properties can cause fiber pull-out or delamination if not machined properly. Specialized blades, low cutting speeds, and optimized tool paths are critical. These measures prevent damage to fragile fibers and ensure consistent quality.
High-performance plastics such as PEEK, PEI, or PTFE are also difficult to machine due to their tendency to melt or deform under heat. CNC operators carefully control cutting parameters and employ effective cooling techniques. These plastics are vital in medical, aerospace, and electronic applications where precision and cleanliness are paramount.
To successfully machine these materials, Chinese CNC manufacturers develop custom tooling solutions and adapt machine configurations. They often incorporate high-stiffness fixtures, vibration damping systems, and advanced control software. This comprehensive approach minimizes errors, extends tool life, and guarantees parts meet strict tolerances.
Training and experience play vital roles in mastering difficult materials. Skilled technicians are adept at troubleshooting issues such as tool wear, thermal distortion, and surface imperfections. They leverage empirical knowledge and ongoing research to refine processes continually, ensuring high-quality results.
Finally, post-machining processes like heat treatment, surface finishing, and coating are adjusted based on the material's properties. These steps enhance durability, corrosion resistance, or other functional characteristics. By mastering difficult-to-machine materials, Chinese CNC manufacturers provide reliable, high-performance parts that meet the most demanding specifications worldwide.
---
## Custom CNC Solutions: Turning Your Designs into Reality
Transforming customer designs into tangible, high-precision parts requires a comprehensive custom CNC solution framework. Chinese manufacturers excel at converting intricate designs, often provided in CAD files, into finished components through a seamless process that emphasizes accuracy, efficiency, and quality.
The journey begins with detailed design analysis and feasibility assessment. Experienced engineers review the drawings, identify potential manufacturing challenges, and suggest modifications to optimize for CNC machining. This collaborative approach ensures that the final design is both functional and manufacturable within the desired tolerances.
Once the design is validated, the process moves to programming. Advanced CAM software generates optimized toolpaths, considering factors like cutting speeds, tool selection, and machine kinematics. Simulation software is often employed to predict potential issues such as collisions or excessive tool wear, allowing preemptive adjustments. This step ensures smooth production runs and high precision.
Material sourcing and preparation are tailored to each project. Chinese manufacturers leverage extensive supplier networks to procure the appropriate raw materials, whether metals, plastics, or composites. Proper material handling and storage protocols are then followed to maintain quality before machining begins. This attention to detail guarantees that the final parts meet all specifications.
Machining is performed on state-of-the-art multi-axis CNC centers equipped with high-precision spindles, automatic tool changers, and adaptive control systems. These tools can handle complex geometries, deep cavities, and microfeatures efficiently. Real-time monitoring systems track process parameters, allowing operators to make adjustments for maintaining tight tolerances throughout production.
Post-processing services, including surface finishing, heat treatment, coating, or assembly, are integrated into the custom solution. This end-to-end approach ensures that parts not only conform dimensionally but also achieve the desired surface quality and functional properties. Clients benefit from a complete, turnkey solution tailored specifically to their needs.
Quality control is embedded at every stage. From initial inspection of raw materials to final dimensional verification using coordinate measuring machines (CMM), rigorous checks ensure adherence to specifications. Documentation and certification processes provide traceability, essential for highly regulated industries.
Delivery schedules are meticulously planned, leveraging efficient logistics channels to meet tight deadlines. Chinese manufacturers' ability to scale production and adapt to demanding timelines makes them reliable partners for global clients. This agility, combined with technical expertise, brings customer visions to life with precision and consistency.
In essence, custom CNC solutions are about more than just manufacturing; they involve translating innovative ideas into high-quality, functional parts. Chinese CNC providers’ comprehensive capabilities—from design consulting to post-processing—enable clients worldwide to realize their concepts with confidence, fostering innovation and competitive advantage.
---
## Overcoming Common Challenges in High-Precision CNC Machining
High-precision CNC machining presents several inherent challenges, including maintaining tight tolerances, managing complex geometries, and ensuring consistent quality across batches. Chinese manufacturers have developed robust strategies to address these issues, ensuring reliable delivery of high-quality parts for demanding applications.
Achieving and verifying extreme tolerances require advanced measurement equipment and strict process controls. Coordinate measuring machines (CMM) are used extensively to inspect parts during and after machining. When deviations are detected, operators adjust cutting parameters or tooling strategies to correct errors, maintaining process stability. Implementing statistical process control (SPC) helps monitor variability and optimize productivity.
Complex geometries, such as internal cavities, undercuts, or micro-features, challenge traditional machining methods. Multi-axis CNC centers equipped with high-precision spindles and specialized tooling enable access to hard-to-reach areas. Advanced fixture design and vibration damping further improve accuracy. Employing simulation software helps plan efficient toolpaths that prevent errors like tool interference or material deformation.
Material variability can cause inconsistencies in high-precision parts. To mitigate this, Chinese manufacturers utilize comprehensive material testing and quality assurance protocols. Proper storage and handling, along with pre-machining inspections, ensure that each batch of raw material meets stringent standards before processing begins.
Thermal distortion during machining is another common issue, especially with materials sensitive to heat. Adaptive cooling strategies—such as high-pressure coolant delivery and cryogenic systems—are employed to control temperature and minimize residual stresses. These measures preserve dimensional integrity throughout the process.
Maintaining surface quality is critical, particularly for parts requiring fine finishes or functional coatings. Post-machining processes like polishing, electroplating, or anodizing are carefully controlled to avoid dimensional changes. Skilled technicians coordinate these steps to achieve consistent surface properties.
Workholding and fixturing are central to precision manufacturing. Custom fixtures designed with high stiffness and stability prevent vibrations and movement during machining. Clamping methods are optimized to minimize deformation and ensure repeatability, especially for thin or delicate components.
Training and experience are vital for troubleshooting and process optimization. Skilled engineers continuously improve methods based on empirical data and technological advancements. They develop best practices for challenging materials and geometries, reducing rework and scrap rates.
Finally, embracing Industry 4.0 technologies—such as real-time data collection, automation, and machine learning—enables proactive problem detection and process adjustments. These innovations help Chinese CNC manufacturers overcome typical high-precision machining hurdles, ensuring parts meet the most exacting standards with consistency.
---
## Analyzing Classic Global CNC Machining Cases and Lessons Learned
Examining global cases of CNC machining highlights both successes and lessons that can enhance future manufacturing processes. Many Chinese CNC manufacturers have contributed to solving complex, high-precision challenges faced by international clients, gaining invaluable insights along the way.
One notable case involved aerospace components requiring micro-tolerance levels. The challenge was to produce complex turbine blades with intricate internal cooling channels. By employing multi-axis machining, advanced simulation, and rigorous inspection protocols, the manufacturer successfully delivered parts that met strict aviation standards. The lesson: investing in innovative tooling and process validation is essential for tackling demanding aerospace applications.
Medical device manufacturing often involves tiny, highly precise parts with strict biocompatibility requirements. A Chinese manufacturer specialized in micro-machining to produce surgical instruments with extremely tight tolerances. Ensuring cleanliness and avoiding contamination were critical. The key takeaway: integrating cleanroom environments and stringent quality controls is vital for medical-grade components.
In another case, a client required high-strength, heat-resistant components from Inconel alloy used in deep-sea exploration equipment. The difficulty was in machining these tough materials without compromising precision. Solutions included cryogenic cooling techniques and custom tooling. The success underscored that tailored cooling and tooling solutions significantly improve productivity and quality with difficult materials.
A manufacturing challenge common across many cases involves balancing cost, time, and quality. A high-volume automotive supplier needed rapid turnaround for complex engine parts. By adopting automation, optimized process flows, and modular fixture designs, the Chinese supplier achieved both speed and accuracy. The lesson: process integration and automation are key to scaling high-precision production efficiently.
An illustrative example of overcoming geometric complexity involved micro-structures in optical devices. Precise control of toolpaths and vibration damping enabled the production of micro-holes and intricate surfaces. The experience demonstrated that investing in high-precision equipment coupled with skilled operation is crucial for microfabrication.
Lessons learned include the importance of continuous process improvement, investing in employee training, and adopting emerging technologies like AI and IoT for real-time monitoring. Transparency and close communication with clients help address unforeseen challenges early, minimizing delays and ensuring satisfaction.
These global case studies reveal a common theme: success in high-precision CNC machining hinges on technological innovation, skilled personnel, and adaptable workflows. Chinese manufacturers' ability to learn from challenges and apply best practices fosters continual growth and excellence. Such lessons pave the way for even more sophisticated, reliable, and efficient manufacturing solutions worldwide.
---
## The Importance of Extensive Experience in CNC Precision Fabrication
Experience is arguably the most valuable asset in high-precision CNC manufacturing. Skilled operators and engineers with years of hands-on knowledge can navigate complex projects, troubleshoot issues, and optimize processes effectively. Chinese CNC companies recognize this and prioritize cultivating expertise to ensure consistent delivery of high-quality parts.
Long-standing experience translates into a deep understanding of diverse materials and their behaviors during machining. Such insights enable operators to select appropriate tools, speeds, and cooling methods to maximize accuracy and surface quality. This expertise reduces trial-and-error phases, saving time and costs while maintaining strict tolerances.
Experienced professionals are also adept at designing custom fixtures and tooling solutions that stabilize delicate or complex parts during machining. Proper fixturing minimizes vibrations and deformation, which are critical in high-precision work. Their familiarity with various clamping techniques accelerates setup times and enhances process stability.
Furthermore, seasoned technicians can foresee potential issues arising from design features, material properties, or machine limitations. Early detection of risks allows for proactive adjustments, preventing costly rework or scrap. Their problem-solving skills are invaluable, especially in projects with tight deadlines or demanding specifications.
Training programs in Chinese CNC factories emphasize accumulating practical knowledge alongside technical education. Mentorship from veteran operators ensures that institutional knowledge is transferred efficiently, maintaining high standards across teams. This culture of experience-driven excellence elevates overall manufacturing quality.
In addition, experienced staff contribute to process documentation and continuous improvement efforts. They analyze production data, identify bottlenecks, and implement refinements that enhance efficiency and part consistency over time. Their insights often lead to innovations in machining strategies and quality assurance.
Experience also enhances communication with clients. Skilled engineers can interpret complex requirements, suggest design modifications for manufacturability, and provide technical support throughout the project lifecycle. This consultative approach fosters long-term partnerships and repeat business.
Finally, as technology rapidly advances, experienced manufacturers adapt quickly to new equipment and methods. Their foundational knowledge allows them to integrate innovations like automation, Industry 4.0 systems, and advanced measurement tools seamlessly. This adaptability ensures that their high-precision fabrication stays ahead of industry standards.
In essence, extensive experience in CNC precision fabrication is indispensable. It ensures that complex projects are executed flawlessly, risks are minimized, and clients receive parts that meet the highest standards of quality and performance. Chinese manufacturers' emphasis on cultivating this expertise positions them as reliable global partners for high-precision component manufacturing.
---
## Ensuring Dimensional Accuracy in Complex CNC Machining Projects
Achieving and maintaining dimensional accuracy is fundamental in high-precision CNC machining, especially when dealing with complex geometries and tight tolerances. Chinese manufacturers employ a multifaceted approach to ensure that every part conforms to its specifications, thereby guaranteeing functionality and reliability.
The first step involves meticulous planning and design validation. Engineers analyze CAD models to identify potential issues that could affect accuracy, such as warping or over-constrained features. Design adjustments are made when necessary to facilitate precise manufacturing without compromising functionality.
During setup, high-precision fixtures and jigs are custom-designed for each project. These fixtures secure parts firmly, minimize vibrations, and maintain positional stability throughout machining. Using vibration damping components and precise alignment techniques further enhances accuracy.
Advanced machine tools equipped with multi-axis capabilities, high-stiffness structures, and real-time feedback systems play a vital role. These machines can execute complex toolpaths with minimal deviation, while auto-calibration features maintain machine accuracy over extended production runs.
Regular calibration and maintenance of CNC equipment are critical. Chinese manufacturers adhere to strict calibration schedules and quality checks to prevent machine drift. This consistency ensures that dimensional tolerances are upheld across batches, reducing scrap and rework costs.
In-process inspection techniques, such as laser scanning and coordinate measuring machines (CMM), are integrated into production workflows. These non-contact methods allow for rapid, accurate verification of critical dimensions during manufacturing, enabling immediate corrective actions if deviations occur.
Statistical process control (SPC) methods monitor process stability over time. Data collected from inspections help identify trends or anomalies, prompting adjustments before parts fall outside tolerance ranges. This proactive approach maintains high quality throughout the project.
Post-machining processes like precision grinding or polishing are carefully controlled to remove any surface irregularities without affecting dimensions. Controlled heat treatments and surface coatings are also applied with precision to preserve dimensional integrity.
Documentation and traceability systems record all inspection data and process parameters. This transparency not only ensures compliance with industry standards but also provides a quality assurance trail for future reference or audits.
Finally, continuous staff training ensures that operators and inspectors stay updated on best practices and emerging technologies. Knowledgeable personnel are better equipped to handle complex projects and uphold stringent accuracy standards.
In summary, ensuring dimensional accuracy in complex CNC projects involves a combination of precise planning, advanced technology, rigorous inspection, and experienced personnel. Chinese manufacturers' comprehensive strategies and commitment to quality enable them to deliver parts that meet or exceed global tolerance requirements, reinforcing their reputation in high-precision manufacturing.
---
## Advancements in CNC Technology for Challenging Material Processing
Recent technological developments have significantly expanded the capabilities of CNC machining, especially when processing challenging materials like superalloys, ceramics, and composites. Chinese manufacturers are at the forefront of adopting and integrating these advancements to meet the ever-increasing demands of high-precision industries worldwide.
One notable advancement is the development of high-speed, multi-axis machining centers equipped with powerful spindles capable of achieving unprecedented cutting speeds. These machines enable efficient material removal even in tough alloys like Inconel or titanium, reducing production time while maintaining tight tolerances.
The integration of artificial intelligence (AI) and machine learning algorithms has revolutionized process optimization. AI-driven systems analyze real-time data to adjust cutting parameters dynamically, improving tool life, surface finish, and dimensional accuracy when working with difficult materials. These intelligent systems adapt to variations in material properties and machine conditions, enhancing consistency.
Advanced cooling and lubrication technologies, such as cryogenic cooling and high-pressure coolant delivery, are now standard in processing heat-sensitive or abrasive materials. Cryogenic cooling reduces cutting zone temperatures dramatically, leading to longer tool life and improved surface quality. High-pressure coolant systems facilitate chip removal and heat dissipation, crucial for maintaining precision.
The adoption of additive manufacturing techniques, like hybrid CNC machining combined with 3D printing, allows manufacturers to create complex geometries in challenging materials more efficiently. Material deposition or pre-formed blanks are machined into final forms with minimal material waste and enhanced precision.
Tooling innovations, including diamond-coated tools and ceramic cutting inserts, provide the hardness and wear resistance needed for machining ceramics and superhard metals. These tools enable high feed rates and prolonged tool life, making the processing of otherwise difficult materials more economical and reliable.
Furthermore, simulation and virtual machining software enable pre-production analysis. By modeling material behavior and tool interactions, manufacturers can optimize machining strategies before cutting begins, reducing trial-and-error and minimizing errors.
Automation and robotics integration facilitate continuous, unattended machining of challenging materials, increasing productivity and consistency. Automated tool changers, part loaders, and inspection stations work seamlessly together, ensuring high throughput without compromising quality.
Lastly, advancements in sensor technology offer real-time monitoring of process parameters, tool wear, and part quality. These sensors provide immediate feedback, allowing for proactive adjustments that prevent defects and ensure the integrity of high-precision parts.
Overall, these technological innovations empower Chinese CNC manufacturers to master the machining of challenging materials, producing high-quality, complex components that meet the demanding specifications of global industries. Embracing these advancements ensures they remain competitive and capable of tackling the most difficult manufacturing challenges.
---
## China’s Leading CNC Manufacturers Serving International Clients
China has emerged as a global hub for high-quality CNC manufacturing, with numerous leading companies offering comprehensive services to international clients. These manufacturers combine advanced technology, extensive experience, and a strong emphasis on quality control to deliver high-precision, custom parts across industries.
Top Chinese CNC firms are equipped with state-of-the-art multi-axis machining centers, EDM machines, and surface finishing equipment. Their investment in cutting-edge technology allows them to handle complex geometries, micro-machining, and difficult materials with impressive precision and efficiency. This technological prowess is complemented by a skilled workforce dedicated to continuous improvement and innovation.
Many of these companies operate with ISO 9001, ISO 13485, and other internationally recognized certifications, ensuring compliance with global standards. They often provide detailed quality documentation, inspection reports, and certifications, which are critical for clients in regulated industries like aerospace, medical, and automotive.
An advantage of Chinese CNC manufacturers is their competitive pricing, which allows clients to access high-quality components at a fraction of the cost compared to Western suppliers. This cost-effectiveness is achieved through economies of scale, optimized supply chains, and streamlined production workflows.
Customization capabilities are a hallmark. These companies work closely with clients to interpret designs, suggest manufacturability improvements, and develop tailored solutions. Their expertise in high-precision manufacturing enables them to produce prototypes, small batches, or large-volume runs efficiently.
The capacity for rapid turnaround is another key strength. Many Chinese CNC providers have flexible manufacturing setups and nationwide logistics networks that facilitate quick delivery of parts worldwide. This agility helps international clients reduce time-to-market and respond swiftly to market demands.
Post-processing services such as surface finishing, coating, heat treatment, and assembly are frequently offered, providing a full-service solution. This integrated approach simplifies project management for clients and ensures seamless quality control from raw material to finished product.
Communication and customer support are prioritized, with multilingual teams offering technical consultation and project coordination. Transparent communication minimizes misunderstandings, aligns expectations, and fosters long-term partnerships.
Lastly, China’s expanding ecosystem of industry clusters and innovation centers continues to promote technological advancement. Collaborations with universities, research institutes, and technology providers drive continuous improvement in CNC processes and materials handling.
In conclusion, Chinese CNC manufacturers stand out as reliable, innovative, and cost-effective partners for global clients seeking high-precision, customized components. Their commitment to quality, technological excellence, and customer-centric service positions them as leaders in the international manufacturing landscape.
---
### High-precision, custom CNC machining is transforming industries worldwide, driven by technological innovation, skilled expertise, and strategic material mastery. Chinese manufacturers have become key players in this arena, offering tailored solutions that meet the most demanding specifications with reliability and efficiency. As they continue to advance their capabilities and expand their global reach, these companies are set to shape the future of high-precision manufacturing, enabling clients across the globe to turn complex designs into reality with confidence.