Expert CNC Machining for High-Precision Global Clients
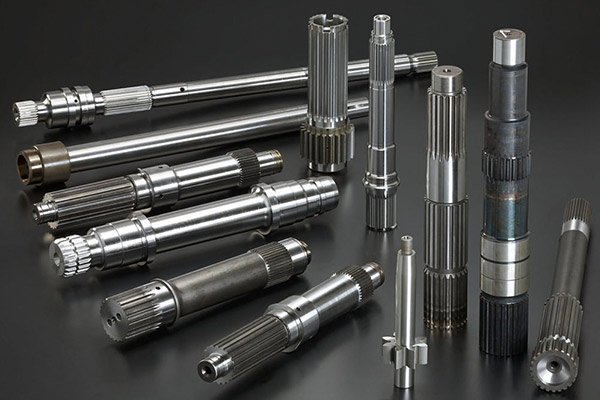
===INTRO:
In the world of manufacturing, especially in high-precision applications, CNC (Computer Numerical Control) machining stands out as a cornerstone technology. As global demand for intricate, reliable, and high-quality components grows, expert CNC machining providers from China are increasingly positioned as trusted partners for international clients. These specialists excel in delivering custom solutions that meet stringent specifications, tackling complex projects with advanced materials, and overcoming challenging manufacturing obstacles. This article explores how leading Chinese CNC machining companies are setting the standard for excellence worldwide, emphasizing precision, adaptability, and technical mastery in every aspect of their work.
Leading CNC Machining Experts Delivering Precision Worldwide
Chinese CNC machining manufacturers have established themselves as global leaders through their commitment to precision and quality. With decades of experience, these companies leverage state-of-the-art equipment and cutting-edge technologies to produce components that meet the most demanding standards. Their teams of skilled engineers and technicians work meticulously to interpret detailed design drawings, ensuring every dimension and tolerance is adhered to. This global reach is supported by robust logistics and quality assurance systems, allowing reliable delivery across continents. Their reputation for precision machining has attracted clients from aerospace, medical devices, automotive, and high-tech industries, all seeking components that are both complex and reliable. The capacity to handle high-volume orders without sacrificing accuracy distinguishes these experts from others in the field. Furthermore, these companies invest heavily in continuous training and technological upgrades, staying ahead of the curve and consistently improving their capabilities. This dedication to excellence ensures that international clients receive products that meet or exceed their expectations, regardless of geographical location. As the demand for high-precision components grows, these Chinese CNC specialists continue to expand their expertise, reinforcing their position as global leaders. Their ability to deliver consistent, high-quality results makes them indispensable partners for companies worldwide seeking reliable manufacturing solutions. The combination of advanced technology, experienced personnel, and global logistics forms the backbone of their success in delivering precision on an international scale. Ultimately, these experts are shaping the future of high-precision CNC machining through their unwavering commitment to quality and client satisfaction.
## Custom CNC Solutions Tailored to Unique Customer Specifications
Every high-precision project begins with a thorough understanding of a customer’s unique needs. Leading Chinese CNC machining providers excel at translating complex, detailed drawings into physical parts that precisely match specifications. They collaborate closely with clients to clarify technical requirements, material choices, and functional objectives, ensuring the final product aligns with their vision. Customized solutions often involve multi-step processes, including prototyping, iterative testing, and fine-tuning, to achieve perfect outcomes. These companies pride themselves on their flexibility, accommodating a wide array of geometries—from tiny, intricate components to large, complex assemblies. Advanced CAD/CAM software and simulation tools enable them to plan and optimize machining strategies before production begins, reducing errors and enhancing precision. They also adapt their machinery and techniques to suit specific project demands, whether that involves high-tolerance machining, surface finishing, or specialized treatments. By maintaining close communication throughout the process, they ensure the end product fulfills exact customer expectations. Their ability to tailor processes for each project demonstrates a deep understanding of diverse industry requirements, from aerospace to medical devices. Moreover, they often offer value-added services like surface treatment, heat treatment, and assembly, providing a comprehensive manufacturing solution. This customer-centric approach not only ensures precise results but also fosters long-term partnerships built on trust and reliability. Custom CNC solutions from these experts exemplify how innovation and flexibility can meet the most complex and exacting specifications worldwide.
High-Precision Machining for Complex and Challenging Components
Manufacturing intricate parts with tight tolerances and complex geometries presents significant challenges. Chinese CNC machining specialists have developed advanced techniques to handle these demanding projects effectively. They often work on components with micro-features, tiny holes, or delicate internal cavities that require extreme precision. To achieve this, they utilize multi-axis machines, high-speed spindles, and specialized tooling that enable complex cuts and detailed finishes. Handling challenging materials such as titanium, stainless steel, or composites adds further difficulty, demanding expert knowledge of material behavior and cutting parameters. These companies employ meticulous process planning, including fixture design and process simulation, to minimize deformation and ensure dimensional stability. When dealing with challenging shapes, they often use advanced CNC programming to optimize tool paths for maximum efficiency and accuracy. Their experience in troubleshooting issues like tool wear, thermal expansion, and vibration ensures parts are produced within tight tolerances consistently. Additionally, they implement rigorous inspection protocols, including coordinate measuring machines (CMM) and other precision measurement tools, to verify each component’s accuracy. Their expertise extends to complex assemblies, where multiple precisely machined parts are assembled into functional systems. Delivering high-precision, complex components consistently positions these companies as go-to experts for innovative industries such as aerospace, defense, and medical technology. Their ability to tackle and master difficult machining challenges has set new standards for quality and reliability on a global scale.
## Utilizing Advanced Materials for Superior CNC Machining Results
The selection of materials plays a pivotal role in machining performance and component durability. Leading Chinese CNC providers boast extensive experience working with a broad spectrum of advanced materials, including titanium alloys, stainless steels, aluminum, ceramics, and composites. Each material presents unique machining challenges—some require specialized cutting tools, cooling strategies, or surface treatments to optimize results. Titanium, for example, is renowned for its strength-to-weight ratio but demands precise control of cutting parameters due to its propensity for work hardening. Similarly, ceramics and composites require delicate handling to prevent cracking or delamination during machining. These companies stay abreast of material innovations and tailor their tooling and process parameters accordingly. They also perform detailed material analysis to understand properties such as hardness, thermal conductivity, and machinability, ensuring optimal outcomes. Using high-quality, certified materials further guarantees consistency and performance in the final components. The ability to machine difficult materials accurately opens doors to high-performance applications like aerospace structural parts or medical implants. Moreover, advanced surface finishing techniques, such as coating or polishing, are often applied to enhance material properties, corrosion resistance, and aesthetic appeal. The strategic use of innovative materials not only improves product lifespan but also contributes to weight reduction and functional enhancements. Expert handling of these materials demonstrates their technical prowess and commitment to delivering superior CNC machined parts across diverse industries worldwide.
Extensive Experience in Handling Difficult and Intricate Parts
Handling intricate parts with tiny features, tight tolerances, or complex geometries requires a deep well of experience and technical knowledge. Chinese CNC machining companies have accumulated extensive expertise over years of working on high-precision projects across various sectors. Their teams understand the nuances of machining delicate features without causing deformation or damage, employing precise fixturing and vibration control methods. They are adept at managing multi-step processes involving multiple materials and finishing requirements, ensuring each stage maintains strict quality standards. Their experience allows them to anticipate potential issues, such as thermal distortion, residual stresses, or tool deflection, addressing these proactively during production. Skilled programmers create optimized tool paths that maximize efficiency while preserving part integrity. The companies also utilize advanced inspection and measurement techniques, including 3D scanning and CMM, to verify intricate features accurately. They are comfortable working with extremely small tolerances, often in the range of microns, which is critical for high-performance applications. Their ability to consistently produce complex, detailed parts builds confidence with clients that demand reliability and precision. This extensive hands-on experience is invaluable when tackling projects that push the boundaries of manufacturing capabilities. Ultimately, their expertise in managing difficult components underscores their reputation as specialists capable of delivering high-precision solutions for the most challenging requirements worldwide.
## Overcoming Global Manufacturing Challenges with Expert Techniques
Manufacturing components for international markets often involves navigating issues like supply chain disruptions, strict regulatory standards, and tight delivery schedules. Chinese CNC machining experts employ innovative techniques and flexible strategies to overcome these global challenges. They optimize production workflows to minimize lead times, often through rapid prototyping and agile manufacturing practices. Their knowledge of international standards, such as ISO, ASTM, and industry-specific regulations, ensures that parts meet all quality and safety requirements. When facing material shortages or logistical hurdles, they leverage local sourcing and diversified supply chains to maintain delivery schedules. Advanced process control systems enable real-time monitoring and adjustment, reducing errors and waste. Additionally, they employ automation and robotics to increase efficiency and consistency, critical for meeting high-volume demands. Their experience working with international clients gives them a nuanced understanding of cultural, logistical, and compliance considerations, which they incorporate into their manufacturing processes. Facing global challenges, these experts focus on quality assurance, transparency, and communication to build trust. Their ability to adapt and implement best practices globally makes them invaluable partners in complex, international manufacturing projects. This proactive approach ensures that clients receive high-precision parts on time, regardless of external uncertainties.
Case Studies of Complex CNC Machining Successes Globally
Numerous success stories highlight the capabilities of Chinese CNC machining companies in producing complex, high-precision components for clients worldwide. One notable case involved manufacturing aerospace engine parts requiring micro-tolerance levels and specialized materials like titanium and nickel alloys. By employing multi-axis CNC machines and rigorous inspection protocols, the company delivered parts that met strict aerospace standards. Another example involved medical implant production, where intricate geometries and biocompatible materials demanded exceptional precision and surface finish. The company’s expertise in handling ceramics and stainless steel ensured the implants’ durability and safety. In the automotive sector, a client required complex prototypes with detailed internal channels, which were achieved through advanced 5-axis machining and precise fixture design. These case studies demonstrate how these companies leverage their experience, advanced technology, and material expertise to overcome manufacturing challenges. Such success stories serve as proof of their ability to manage projects that demand technical mastery and meticulous quality control. They also highlight the importance of innovative process planning and inspection in achieving high-precision results. These global case examples inspire confidence among prospective clients seeking reliable partners for their most complex projects. Ultimately, they exemplify how Chinese CNC experts turn challenging designs into reality with precision and efficiency.
## The Importance of Accurate Design Translation in CNC Processes
Translating complex CAD/CAM designs into physical parts requires meticulous attention to detail. Inaccuracies at this stage can lead to costly errors and deviations from specifications. Leading Chinese CNC specialists prioritize precise design translation, utilizing high-end software and simulation tools to verify tool paths and predict potential issues. They work closely with clients to clarify design intent, tolerances, and material considerations before production begins. Their experienced engineers can identify potential manufacturability issues early, suggesting design adjustments that improve process efficiency and accuracy. They also perform virtual Machining simulations to optimize tool paths, reduce cycle times, and minimize material waste. During actual manufacturing, they implement rigorous inspection procedures, including 3D scanning and coordinate measuring machines, to ensure the parts match the original CAD data within tight tolerances. Proper design translation not only ensures accuracy but also enhances manufacturability and cost-effectiveness. These companies understand that clear communication and detailed documentation are essential for successful project execution. By emphasizing accurate design transfer, they reduce rework, improve consistency, and guarantee that the final product meets all specifications. This focus on precision from design to production forms the backbone of their reputation for delivering high-quality CNC-machined components worldwide.
Ensuring Quality and Precision in Every Custom Machined Part
Quality assurance is central to delivering reliable, high-precision CNC machined components. Chinese manufacturers implement comprehensive quality management systems aligned with international standards. They conduct multi-stage inspections, starting from raw material verification to in-process checks and final quality control. Advanced measurement tools such as CMM, optical comparators, and surface roughness testers ensure every part adheres to exact tolerances. Their teams are trained to identify and rectify issues early, preventing defects from progressing further in production. They also utilize statistical process control (SPC) to monitor critical manufacturing parameters, ensuring process stability and consistency over large batches. For high-precision applications, surface finishing processes like polishing, anodizing, or coating are meticulously performed to meet aesthetic and functional requirements. Documentation and certification accompany each batch, providing transparency and traceability for clients. Moreover, continuous process improvement initiatives help identify bottlenecks and enhance quality standards. The company’s dedication to precision and quality builds trust with clients from diverse industries, where failure is not an option. By integrating advanced inspection technologies and rigorous quality protocols, these CNC experts guarantee every part they produce is of the highest quality, meeting the most demanding specifications worldwide.
## How Material Selection Impacts Machining Performance and Durability
Choosing the right material affects not only the manufacturing process but also the performance and longevity of the final product. Chinese CNC machining companies emphasize understanding the properties and behaviors of various materials to optimize machining strategies. For high-strength, lightweight applications, materials like aluminum and titanium alloys are preferred, but they require precise cutting parameters to prevent deformation or tool wear. For applications demanding wear resistance, stainless steel or specialized composites are selected, each presenting unique machining challenges. The companies' extensive experience in material science enables them to recommend suitable materials based on application requirements, environmental conditions, and cost considerations. Proper material preparation, including heat treatment or surface coating, enhances durability and corrosion resistance. They also consider machinability factors such as chip formation, thermal conductivity, and cutting forces to refine their approach. Material selection directly impacts manufacturing efficiency, as some materials may necessitate slower feed rates or specialized tooling. Durable, high-performance components rely on the synergy between material properties and manufacturing techniques. These experts understand that material choice is fundamental to ensuring the final product's reliability, performance, and lifespan in demanding applications worldwide.
Navigating International Standards for High-Precision CNC Manufacturing
Operating within the framework of international standards is crucial for global CNC machining success. Chinese manufacturers are well-versed in standards such as ISO, ASTM, and industry-specific regulations, ensuring their products are compliant and internationally acceptable. They incorporate these standards into their quality assurance processes, from material certification to inspection procedures. Certification processes, such as ISO 9001, demonstrate their commitment to quality management and continuous improvement. They also adapt to client-specific standards, which may involve additional testing or documentation requirements. Staying current with evolving regulations enables these companies to serve markets with strict compliance needs, such as aerospace or medical industries. Their teams are trained on international standards interpretation, ensuring that design, manufacturing, and inspection protocols align with global expectations. This adherence minimizes regulatory risks and facilitates smooth approval processes across different countries. Furthermore, transparent documentation and traceability provide clients with confidence that their components meet all legal and safety requirements. Navigating complex international standards demands expertise, diligence, and a proactive approach—qualities that top Chinese CNC machining experts embody to serve clients worldwide effectively.
## Building Trust with Global Clients Through Consistent Excellence
Long-term relationships with international clients are built on trust, consistency, and superior quality. Chinese CNC machining companies have established this trust by consistently delivering high-precision components that meet or exceed expectations. Transparent communication, timely delivery, and a focus on quality control play vital roles in fostering loyalty. They actively seek client feedback and implement continuous improvements to enhance their services. Demonstrating compliance with international standards and providing detailed inspection reports further solidifies trust. They also invest in after-sales support, troubleshooting, and technical advice to ensure client satisfaction beyond the initial order. Their reputation is reinforced by successful collaborations on complex projects, where technical expertise and reliability are critical. Building a global brand involves embracing innovation, maintaining open communication, and upholding the highest standards of quality and integrity. These companies understand that trust is earned over time through consistent performance, attention to detail, and commitment to excellence. As they continue to expand their global footprint, their focus remains on establishing enduring partnerships rooted in mutual success. Ultimately, their dedication to delivering precision and reliability makes them preferred partners for high-precision manufacturing worldwide.