Expert CNC Machining for High-Precision Global Clients
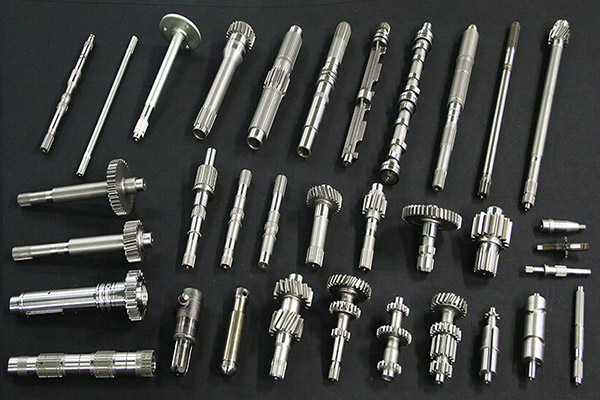
===INTRO:
In today's fast-paced manufacturing landscape, high-precision CNC machining has become a cornerstone for industries worldwide. As global demands for intricate parts and components grow, leading CNC machining experts are stepping up to meet these challenges with advanced technology, unmatched expertise, and tailored solutions. Whether it's aerospace, medical devices, or high-tech electronics, the ability to deliver precise, reliable parts consistently is vital. This article explores how top-tier CNC machining firms are serving international clients, tackling complex projects, and pushing the boundaries of what's possible in high-precision manufacturing.
---
## Leading CNC Machining Experts Deliver Precision for Global Clients
Top CNC machining companies are recognized for their commitment to excellence, precision, and customer satisfaction. Serving clients across continents requires not only sophisticated machinery but also a team of experienced engineers who understand the nuances of high-precision manufacturing. These experts leverage state-of-the-art CNC equipment capable of micron-level accuracy, ensuring that every component meets strict specifications. Their global outreach means they are well-versed in diverse standards and industry requirements, from aerospace to medical applications. Such firms are often certified to international standards, providing clients assurance of quality and consistency. By integrating advanced inspection and testing methods, these experts guarantee that each part adheres precisely to the design, reducing waste and minimizing rework. Their reputation is built on reliability, timely delivery, and the ability to handle complex, high-precision projects that others might shy away from. This global client base benefits immensely from their tailored solutions and technical expertise. Moreover, these firms continually invest in cutting-edge CNC technology, staying ahead of industry trends and ensuring maximum precision. Their extensive experience across various sectors fosters innovative problem-solving approaches, making them invaluable partners for international clients with demanding specifications.
---
## Custom CNC Solutions Designed According to Customer Specifications
Every client has unique requirements, and leading CNC machining providers excel at translating these into precise, customized solutions. From initial consultation to final delivery, the process is highly collaborative, ensuring the final product aligns perfectly with the customer's vision. Advanced CAD/CAM software facilitates detailed design analysis and simulation, allowing engineers to optimize manufacturing processes before actual machining begins. Custom fixtures, jigs, and dedicated tooling are often developed to accommodate complex geometries and tight tolerances. This tailored approach reduces machining time, improves accuracy, and enhances overall efficiency. High-precision CNC shops meticulously review drawings and specifications, offering suggestions to improve manufacturability without compromising quality. They also provide material recommendations based on the application's performance needs, durability, and cost considerations. The ability to produce small batch prototypes or large-volume runs with identical precision is a hallmark of these expert providers. Their flexibility in handling various materials—metals, plastics, composites—further ensures versatility for a broad range of industries. Ultimately, their customer-centric approach fosters long-term partnerships built on trust, quality, and mutual growth.
---
## Tackling High-Complexity Parts with Advanced CNC Machining Techniques
Manufacturing high-complexity parts requires more than just powerful machines; it demands sophisticated techniques and innovative solutions. Leading CNC specialists utilize multi-axis machining centers, such as 5-axis and even 7-axis machines, enabling intricate geometries and undercuts to be machined in a single setup. These capabilities drastically reduce production time and improve positional accuracy. Additionally, high-precision milling, turning, and grinding processes are integrated to achieve tight tolerances and superior surface finishes. For parts with internal cavities or complex contours, wire EDM and other non-traditional methods are employed to overcome limitations of standard machining. Specialized tooling and custom programming optimize cutting paths, minimizing material waste and reducing cycle time. High-precision CNC providers also leverage technology like adaptive control and real-time monitoring to detect and correct deviations during manufacturing. Handling difficult materials such as titanium, Inconel, or ceramics often involves heat management and specialized cutting techniques. These advanced methods enable the production of components with complex features that are critical in aerospace, medical, and other high-end applications. Their expertise in high-complexity machining translates into innovative, reliable solutions for challenging projects.
---
## Material Expertise: Selecting the Right Materials for Precision Parts
Material selection is a critical factor in achieving high precision and durability in CNC machined parts. Leading CNC providers boast extensive knowledge of a broad spectrum of materials, including various metals, plastics, and composites. They understand how each material behaves during machining, including factors like machinability, thermal expansion, and wear resistance. For high-precision applications, materials such as titanium, stainless steel, aluminum alloys, and exotic superalloys are frequently used due to their strength-to-weight ratios and corrosion resistance. Medical and aerospace industries often require biocompatible or high-performance materials, necessitating exacting standards and careful handling. The choice of material impacts not only the machining process but also the final product's performance and lifespan. Experts advise clients on material grades, treatments, and finishes to optimize functionality. For example, surface treatments like anodizing or coating can enhance corrosion resistance or wear properties. Knowledge of material properties allows for better tool selection, cutting parameters, and process optimization. By combining material expertise with advanced CNC technology, manufacturers can produce parts that meet stringent specifications and endure demanding service conditions.
---
## Extensive CNC Machining Experience Ensures Quality and Reliability
Experience is the backbone of excellence in high-precision CNC machining. Established providers often have decades of hands-on knowledge, enabling them to handle a diverse array of projects with confidence. Their long-term track record reflects an understanding of subtle machining nuances, from tool wear to thermal effects, that influence quality. Such experience allows them to develop effective process controls, quality assurance protocols, and troubleshooting strategies. Moreover, seasoned professionals are adept at refining programs for efficiency without sacrificing accuracy, reducing lead times and costs. They also maintain comprehensive documentation and inspection records, ensuring traceability and compliance with international standards. Their familiarity with a variety of industry-specific requirements—such as aerospace tolerances or medical sterilization standards—further enhances reliability. Continuous staff training and process upgrades keep their skills sharp and technology current. This wealth of experience translates into confidence for clients who depend on precision, repeatability, and consistent quality in their critical components. It also fosters innovation, as experienced teams can adapt techniques from various sectors to solve emerging manufacturing challenges.
---
## Overcoming Common Challenges in Precision CNC Manufacturing
High-precision CNC manufacturing presents several challenges, including achieving tight tolerances, complex geometries, and managing difficult materials. Leading experts proactively address these hurdles through meticulous planning and advanced technology. For instance, vibration damping and temperature control are crucial in maintaining accuracy during machining of delicate parts. Proper fixture design and clamping techniques prevent deformation or misalignment. When working with hard-to-machine materials like titanium or Inconel, specialists utilize specialized tools, cutting fluids, and optimized speeds to prevent tool wear and material chatter. Managing tolerances in complex assemblies requires multi-axis machining and precise program control. Moreover, thorough inspection at each stage—using coordinate measuring machines (CMMs) or optical systems—ensures deviations are caught early. Addressing surface finish challenges involves selecting appropriate tools and machining parameters. Knowledge of potential issues and their solutions enables manufacturers to deliver flawless components consistently. Overcoming these challenges is a testament to the expertise and commitment of top CNC providers dedicated to exceeding client expectations.
---
## Case Study: Solving Difficulties in High-Precision Component Production
A prominent example of expert CNC machining overcoming complex challenges involves the production of aerospace engine components. These parts require extraordinary precision, complex geometries, and materials like Inconel, known for its toughness and high-temperature stability. The client faced issues related to dimensional deviations and surface integrity. The CNC team analyzed the part drawings and identified potential sources of error, such as thermal expansion and tool deflection. They then employed 5-axis machining centers with high-stiffness fixtures and integrated real-time monitoring systems. Advanced cutting tools and coolant strategies minimized heat and vibration during machining. Multiple inspection points throughout the process ensured adherence to stringent tolerances. The team also optimized the sequence of operations to reduce residual stresses and improve surface finish. As a result, the client received parts with perfect dimensional accuracy and exceptional surface quality, ready for demanding aerospace applications. This case exemplifies how expertise and innovative techniques can resolve even the most difficult manufacturing challenges, reinforcing the importance of experience in high-precision CNC machining.
---
## Ensuring Accuracy in Complex Geometries Through Expert Techniques
Producing complex geometries demands highly specialized CNC techniques and a thorough understanding of machining dynamics. Experts utilize multi-axis machines to access hard-to-reach features and achieve intricate shapes in a single setup, reducing errors and improving consistency. They employ advanced toolpath strategies, such as adaptive clearing and high-efficiency milling, to optimize material removal and surface quality. Simulation software is used extensively to predict machining behavior and prevent issues like tool collision or excessive forces. When dealing with internal cavities or undercuts, wire EDM and other non-contact methods are integrated into the process. Precision fixtures and custom jigs ensure stability during machining, maintaining accuracy for complex features. Surface finishing techniques like polishing, buffing, or coating are applied to achieve the desired aesthetic and functional qualities. Through rigorous quality control, including CMM inspection, they verify that the finished parts meet exact specifications. The combination of innovative technology and seasoned expertise guarantees that complex geometries are realized with pinpoint accuracy.
---
## Importance of Customization in Meeting Unique Client Requirements
Customization is at the heart of high-precision CNC manufacturing, enabling clients to obtain parts that precisely match their needs. Leading CNC providers work closely with clients during the design phase to assess manufacturability, recommend modifications, and optimize performance. Custom jigs, fixtures, and tooling are often developed to handle special geometries or high-volume production runs efficiently. Adjustments in cutting parameters, tool selection, and process sequencing are tailored for each project, ensuring maximum accuracy and surface quality. For instance, medical implant manufacturers may require biocompatible finishes and strict sterilization standards, while aerospace clients demand components that withstand extreme conditions. By offering flexible manufacturing options, such as small batch prototyping or large-scale production, the providers cater to diverse business models. This level of customization results in parts that perform reliably in their intended applications, reducing rework, delays, and costs. It also fosters stronger client relationships, built on trust that their specific needs are understood and met through innovative solutions.
---
## Global Success Stories in High-Precision CNC Machining
Numerous companies worldwide have achieved remarkable success through strategic partnerships with expert CNC machining firms. These success stories often involve overcoming complex manufacturing hurdles and delivering mission-critical components. For example, aerospace giants rely on high-precision CNC providers for engine parts that demand tight tolerances and material integrity. Medical device manufacturers depend on these experts to produce implants and surgical instruments with consistent quality. In the electronics industry, precision CNC machining enables the creation of miniaturized, intricate components for high-tech devices. Such collaborations typically result in significant cost savings, improved product performance, and faster time-to-market. These case studies highlight the importance of technological innovation, experienced personnel, and a customer-centric approach. They demonstrate that by leveraging advanced CNC techniques and material expertise, companies can solve seemingly insurmountable production challenges. The global reach of these success stories underscores the universal demand for high-precision, reliable manufacturing solutions and the vital role of expert CNC providers in meeting this need.
---
## Innovations in CNC Technology for Enhanced Precision and Efficiency
The CNC machining industry continually evolves, driven by technological innovations that enhance precision, speed, and reliability. Developments such as high-speed spindle technology, improved cutting tools, and adaptive control systems enable more complex parts to be produced faster and more accurately. Multi-axis machining, including 5-axis and beyond, provides greater flexibility for complex geometries. Cloud-based manufacturing and IoT integration facilitate real-time data monitoring, predictive maintenance, and process optimization. Additive manufacturing techniques are increasingly integrated with traditional CNC methods, enabling hybrid fabrication for complex or multi-material parts. Laser cutting, robotic automation, and AI-driven programming further streamline workflows and reduce human error. Advanced inspection technologies, including 3D scanning and machine learning algorithms, improve quality assurance. These innovations empower manufacturers to meet the ever-growing demands of precision, complexity, and efficiency in global markets. Staying at the forefront of technological advancement is essential for CNC experts aiming to deliver cutting-edge solutions and maintain a competitive edge.
---
## Building Long-Term Partnerships with Global High-Precision Clients
Establishing long-term relationships is a key goal for leading CNC machining providers. These partnerships are built on trust, consistent quality, and mutual understanding of project goals. By providing reliable delivery, flexible production options, and responsive customer service, CNC experts become integral to their clients' supply chains. Regular communication and proactive problem-solving foster collaboration and innovation, allowing both parties to adapt to evolving market needs. Offering comprehensive post-processing, finishing, and inspection services adds value and simplifies the supply chain. Sharing technical expertise and insights helps clients optimize their designs and reduce costs. Many successful partnerships involve joint development projects, where continuous improvement and innovation are prioritized. As global competition intensifies, these long-term collaborations ensure stability, quality, and a competitive advantage for clients across industries. Ultimately, trust and demonstrated competence forge enduring relationships that benefit both manufacturers and their international customers.
---
High-precision CNC machining stands as a testament to technological innovation, material mastery, and expert craftsmanship. For global clients seeking intricate, reliable, and high-quality components, partnering with experienced CNC specialists makes all the difference. Whether tackling complex geometries, working with advanced materials, or customizing solutions to meet unique specifications, these experts deliver excellence at every step. As the industry continues to evolve with new innovations, the importance of skill, experience, and tailored service remains paramount. Building lasting partnerships rooted in trust and shared success, CNC machining companies are shaping the future of manufacturing—one precision part at a time.