Expert CNC Machining for High-Precision Global Clients
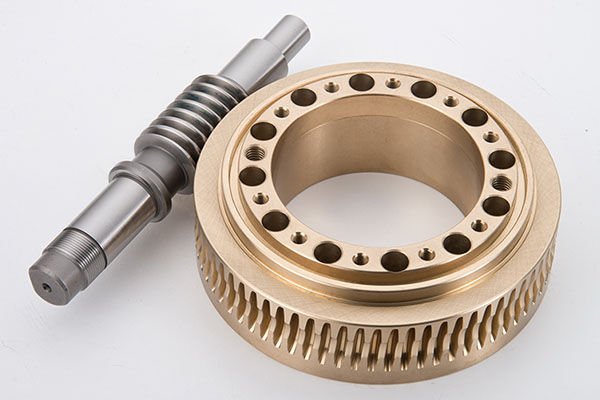
===INTRO:
In today’s highly competitive global manufacturing landscape, the demand for high-precision CNC machining services has skyrocketed. Companies across various industries seek reliable partners capable of delivering complex, high-tolerance components with impeccable accuracy. Whether it’s aerospace, medical devices, automotive, or consumer electronics, the need for expert CNC machining is critical to achieving product excellence. This article explores the importance of advanced CNC machining for international clients, emphasizing the significance of customization, material expertise, and technological innovation. We delve into how experienced engineers and proven strategies overcome common challenges, ensuring consistent quality and strengthening long-term collaborations. For global high-precision needs, partnering with a skilled CNC machining provider is not just a choice; it’s a necessity for success in today’s demanding marketplace.===
## The Importance of Custom CNC Machining for Global High-Precision Needs
Custom CNC machining is essential for meeting the unique specifications of high-precision projects worldwide. Unlike mass-produced parts, custom machining involves tailoring processes to exact design requirements, ensuring perfect fit and function. For international clients, this means translating complex blueprints into tangible components with tight tolerances often within microns. The ability to adapt to diverse design complexities and material choices underscores the importance of customization. It allows manufacturers to optimize machining strategies for specific applications, whether it’s intricate aerospace parts or medical implants that demand flawless precision. Customized CNC solutions also facilitate rapid prototyping and iterative design improvements, reducing time-to-market and avoiding costly rework. Moreover, the flexibility of custom machining supports small batch productions and highly specialized parts that are not feasible with conventional methods. As global markets evolve, the demand for tailored manufacturing solutions continues to grow, making customization a cornerstone of high-precision CNC service providers.
## Leveraging Advanced CNC Techniques for Complex Component Manufacturing
The evolution of CNC technology has revolutionized how complex components are manufactured on a global scale. Advanced techniques such as multi-axis machining, high-speed milling, and micro-machining enable the production of intricate geometries with unparalleled precision. For example, five-axis machining allows for multi-directional tool movement, facilitating the creation of complex shapes without the need for multiple setups. This results in higher accuracy, reduced machining time, and superior surface finishes. Additionally, the adoption of CNC automation and adaptive control systems helps optimize cutting parameters in real-time, ensuring consistency in high-precision tasks. Laser machining, EDM (Electrical Discharge Machining), and ultrasonic-assisted processes further expand the capability to machine difficult materials and achieve micro-level details. These advanced techniques are vital for industries that require tight tolerances and complex features, such as aerospace components with intricate cooling channels or medical devices with miniature parts. Leveraging these innovations enables global clients to realize designs that were previously impossible or prohibitively expensive.
## Material Selection and Usage in Precision CNC Machining Processes
Selecting the right material is fundamental to achieving high-precision results in CNC machining. Different applications demand specific properties, such as strength, thermal stability, corrosion resistance, or biocompatibility. Common materials include aerospace alloys like titanium and aluminum, medical-grade stainless steels, engineering plastics, and exotic composites. Each material presents unique machining challenges, requiring tailored cutting parameters and tooling. For instance, titanium offers excellent strength-to-weight ratio but is difficult to machine due to its toughness and tendency to work harden. Conversely, plastics like PEEK or PTFE require careful handling to prevent deformation or melting. Experts in CNC machining understand how to utilize these materials effectively, selecting appropriate cutting tools, feed rates, and cooling methods to ensure precision and surface quality. Proper material handling also reduces tool wear and extends the lifespan of machinery, which is crucial for maintaining consistent quality across large volumes or complex parts. Material expertise is thus a key differentiator for top-tier CNC service providers serving overseas clients with high-precision demands.
## Achieving High-Tolerance Results Through Expert Machining Skills
High-tolerance manufacturing is the hallmark of expert CNC machining, demanding meticulous attention to detail and exceptional skill. Achieving tolerances within microns requires not only advanced equipment but also seasoned craftsmanship. Skilled machinists and engineers interpret complex CAD/CAM files, optimizing tool paths to minimize errors. Fine-tuning machine settings, such as spindle speeds and feed rates, based on material and geometry, ensures consistent accuracy throughout the production process. Additionally, precision measurement tools like coordinate measuring machines (CMMs) play a vital role in verifying dimensional accuracy and ensuring compliance with strict specifications. Expert operators also anticipate and compensate for potential issues, such as thermal expansion or tool deflection, which could compromise tolerances. Achieving high-tolerance results consistently is a testament to the expertise embedded within the CNC facility, making it possible to produce components that meet exacting standards for critical applications worldwide.
## Overcoming Common Challenges in Precision CNC Production Globally
Global CNC machining projects often face challenges such as material variability, geometric complexity, and strict quality standards. One common issue is machining difficult materials like hardened steel or composites, which demand specialized tooling and processes to prevent tool wear and deformation. Another challenge involves complex geometries requiring multi-axis operations and precise fixturing, which can introduce alignment errors. Thermal management is also critical, as temperature fluctuations can cause dimensional inaccuracies, especially in micro-machining. The variability of supply chains and regulations across countries adds further complexity to maintaining consistent quality standards. To overcome these challenges, expert CNC providers employ comprehensive quality control systems, advanced software for process simulation, and rigorous inspection protocols. Continuous staff training and investing in the latest technology are essential strategies for addressing these issues effectively. By proactively managing these obstacles, manufacturers can deliver high-precision components reliably to clients worldwide.
## Case Studies: Solving Difficult Machining Problems Worldwide
Real-world case studies highlight the ingenuity and expertise required to tackle global machining challenges. One such case involved machining ultra-hard ceramic components for aerospace applications, where conventional cutting tools failed due to extreme hardness. By implementing diamond-coated tooling and optimizing cutting parameters, the team achieved the desired tolerances without damaging the material. Another example featured the production of micro-engineered medical implants made from titanium alloys with complex internal channels. Utilizing five-axis micro-machining and laser-assisted techniques, the project met stringent biocompatibility and precision standards. A different case addressed the difficulty of machining high-strength steel for automotive safety parts, where adaptive control systems reduced heat generation and tool wear, ensuring dimensional stability. These examples demonstrate how tailored solutions, innovative technology, and accumulated experience solve even the most challenging high-precision problems across diverse industries and geographies.
## The Role of Skilled Engineers in Ensuring Machining Accuracy
Behind every successful high-precision CNC project is a team of skilled engineers. Their expertise bridges the gap between complex design intent and manufacturable reality. Engineers analyze CAD files to identify potential manufacturing issues, recommend design modifications, and select optimal tooling and fixturing solutions. They also develop precise machining strategies, incorporating considerations such as tool paths, cutting speeds, and cooling methods. Continuous process monitoring and real-time adjustments are vital to maintaining tolerances and surface finishes. Moreover, experienced engineers are adept at troubleshooting unforeseen issues, minimizing downtime, and ensuring rapid turnaround. Their knowledge of material behaviors, machine dynamics, and industry standards guarantees that each batch of components meets exact specifications. These professionals are the cornerstone of any high-precision CNC service provider, especially those serving demanding clients across borders.
## Customized Solutions for Diverse Industries and High-Precision Demands
Different industries have unique high-precision requirements, and successful CNC machining providers tailor their solutions accordingly. Aerospace applications demand components with ultra-high tolerances, lightweight materials, and resistance to extreme conditions. Medical devices require biocompatible materials, micro-fabrication capabilities, and strict cleanliness standards. Automotive high-performance parts often involve high-strength alloys and complex geometries that need precise assembly. Consumer electronics call for miniature, detailed parts with flawless surface finishes. To meet these varied demands, CNC providers develop customized manufacturing processes, select industry-specific materials, and incorporate regulatory compliance protocols. This flexibility and specialization enable the production of high-quality components that adhere to the stringent standards of each sector. Offering tailored solutions not only enhances client satisfaction but also positions the provider as a trusted partner in complex manufacturing ecosystems worldwide.
## Ensuring Quality Control and Consistency in Global CNC Services
Maintaining consistent quality across international projects is critical for high-precision CNC machining. Advanced inspection techniques, such as CMM, laser scanning, and optical measurement, are standard practices for verifying part dimensions and surface integrity. A rigorous quality management system, aligned with international standards like ISO 9001 or AS9100, ensures that processes meet global benchmarks. Traceability of materials, tooling, and production data further enhances reliability and accountability. Regular calibration of equipment and continuous staff training are essential to uphold precision standards. Automated inspection and data analysis tools help detect deviations early, preventing defective parts from reaching clients. The implementation of comprehensive quality control protocols reassures global customers of consistent, high-quality outputs. Effective quality management ultimately builds trust and long-term partnerships in highly competitive international markets.
## Innovations in CNC Technology That Enhance Precision and Efficiency
Recent technological advancements continue to push the boundaries of CNC machining precision and productivity. The integration of artificial intelligence and machine learning allows for smarter tool path optimization and predictive maintenance, reducing downtime and errors. Developments in high-speed spindle technology and precision tooling improve surface finish and dimensional accuracy. Additive manufacturing combined with CNC subtractive processes enables hybrid manufacturing solutions for complex geometries. Enhanced software capabilities, such as simulation and virtual prototyping, minimize material waste and rework. Automation solutions, including robotic loading and unloading, streamline high-volume production while maintaining consistency. These innovations lead to faster turnaround times, reduced costs, and higher quality standards, fulfilling the high-precision expectations of global clients. Staying at the forefront of CNC technology is vital for providers aiming to deliver the best solutions worldwide.
## The Impact of Experience on Handling High-Difficulty Machining Tasks
Experience is the backbone of mastery in high-precision CNC machining. Seasoned providers have encountered and solved countless complex problems, from machining exotic alloys to micro-fabrication. Their familiarity with various materials, machine behaviors, and intricate designs enables quick diagnosis and effective solutions. Experienced teams can optimize processes to extend tool life, minimize errors, and meet tight tolerances consistently. They also understand how to adapt to unforeseen challenges, such as material anomalies or unexpected geometric constraints. Long-standing expertise fosters a proactive approach to quality, safety, and efficiency, benefitting clients with reliable and precise components. It also means they can handle high-difficulty projects that require innovative thinking and meticulous execution. In the realm of global high-precision manufacturing, experience truly translates into trust, quality, and success.

CNC
## Building Long-Term Partnerships Through Reliable CNC Machining Services
Reliable CNC machining services are the foundation of long-term business relationships. Consistent quality, on-time delivery, and transparent communication foster trust and customer loyalty. For international clients, working with a reputable provider means minimized risks, especially when dealing with complex, high-stakes projects. Offering flexible solutions, ongoing technical support, and continuous process improvements demonstrates commitment to client success. Building partnerships also involves understanding clients’ evolving needs, providing innovative solutions, and maintaining strict confidentiality. Over time, a trusted CNC partner becomes an integral extension of a client’s supply chain, supporting their growth and innovation. Strong relationships are reinforced through shared commitments to quality, responsiveness, and mutual respect. Ultimately, these long-term collaborations enable both parties to thrive in competitive global markets, continuously pushing the boundaries of high-precision manufacturing.
Expert CNC machining tailored for high-precision demands plays a crucial role in the success of global industries. By leveraging advanced techniques, material expertise, and seasoned engineering talent, reliable providers can meet the most challenging requirements of international clients. Continuous innovation and a focus on quality control ensure consistent excellence, fostering long-lasting partnerships built on trust and mutual growth. As technology and industry standards evolve, the importance of experienced, adaptable, and dedicated CNC service providers will only increase, driving global manufacturing toward new heights of precision and efficiency.