Expert CNC Machining for High-Precision Global Customers
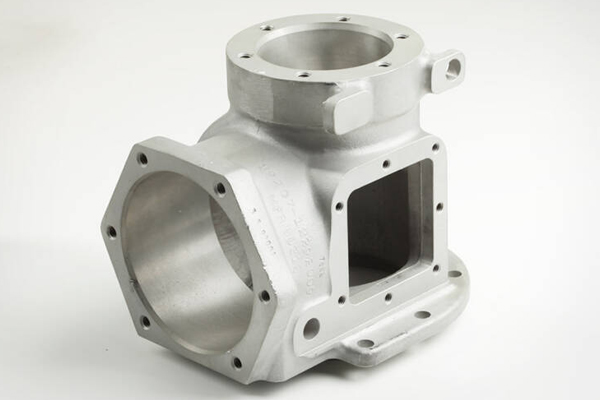
# Delivering Precision: Expert CNC Machining for Global Clients
===INTRO:===
In today’s fast-paced, high-tech world, precision engineering is more crucial than ever. For companies around the globe, sourcing reliable CNC machining services that can handle complex, high-precision components is essential. Whether it’s aerospace, medical, automotive, or electronics industries, the demand for meticulous craftsmanship and advanced manufacturing techniques is relentless. This article explores how expert Chinese CNC machining services are meeting the needs of international customers by delivering tailored solutions, overcoming material challenges, and maintaining top quality at scale.
## Delivering Precision: Expert CNC Machining for Global Clients
CNC machining has become a cornerstone of modern manufacturing, especially for clients requiring high-precision parts. Expert Chinese CNC service providers pride themselves on their ability to deliver complex components with tolerances often within microns. These companies have invested heavily in state-of-the-art equipment, skilled labor, and rigorous quality control processes. Their reputation is built on consistently meeting or exceeding customer expectations across continents.
The key to success in this domain is understanding the unique needs of global clients. Each industry has its standards, whether aerospace’s demanding safety margins or medical devices’ sterility and accuracy requirements. Expert CNC shops tailor their processes accordingly, ensuring that each part is produced according to detailed specifications.
Moreover, these Chinese manufacturers leverage extensive experience in handling diverse materials—from high-grade titanium to advanced composites—making them versatile partners. Their capability to adapt to different design intricacies and technical drawings allows international clients to trust their production pipeline without concern for quality or delivery delays.
Another aspect of delivering precision is their commitment to continuous improvement. They incorporate the latest CNC technology, such as multi-axis machining and automated quality inspection tools, to enhance accuracy. This approach ensures that even the most complex geometries are machined flawlessly, reducing rework and waste.
Communication and transparency are vital when working across borders. Leading Chinese CNC providers maintain clear channels with customers, offering real-time updates and detailed inspection reports. This transparency fosters confidence and facilitates smooth collaboration, critical for high-stakes projects.
At the heart of these services is a culture of innovation and quality assurance. Many providers have ISO, TS, and other international certifications, ensuring compliance with global standards. Such credentials reassure international clients that their high-precision components are manufactured under strict quality management systems.
Furthermore, cost-effectiveness plays a significant role. By optimizing manufacturing processes and leveraging local expertise, Chinese CNC shops can offer high-quality services at competitive prices, making them attractive partners for global businesses seeking to scale production without compromising precision.
In conclusion, delivering high-precision CNC machining to international clients requires a blend of advanced technology, skilled craftsmanship, and meticulous quality control. Chinese manufacturers are proving to be reliable, innovative, and adaptable partners capable of meeting the rigorous demands of global markets.
## Custom CNC Solutions Designed to Meet Unique Customer Specifications
Every client has unique requirements, especially in high-precision manufacturing. Custom CNC solutions are essential to meet these specifications, whether they involve complex geometries, tight tolerances, or specialized materials. Chinese CNC machining companies excel at translating detailed technical drawings into reality, offering tailored services that align with customer needs.
The process begins with thorough consultation. Experienced engineers analyze the design files, identify potential challenges, and propose optimal manufacturing strategies. This proactive approach ensures that each project is feasible and efficient, minimizing costly errors or delays.
One of the strengths of Chinese CNC providers is their ability to handle diverse and demanding specifications. From ultra-fine features in medical implants to precision engine components in automotive industries, these companies utilize multi-axis machines, high-speed spindles, and advanced tooling to achieve the desired outcomes.
Material selection plays a pivotal role in custom solutions. Whether a client needs corrosion-resistant stainless steel, lightweight aluminum alloys, or exotic materials like Inconel, the Chinese manufacturers have extensive experience working with these substances. They understand the material properties and adjust machining parameters accordingly to prevent issues such as deformation, cracking, or surface defects.
Another critical aspect is the customization of finishing processes. Beyond basic machining, these providers offer polishing, coating, anodizing, or surface treatments tailored to the end-use of the part. This ensures not only functional performance but also aesthetic appeal, which can be vital in consumer-facing applications.
Quality assurance is embedded throughout the process. Custom CNC solutions include rigorous inspection stages, using coordinate measuring machines (CMM), laser scanning, and other nondestructive testing methods. This guarantees that each part conforms precisely to the specifications, even in high-tolerance scenarios.
Flexibility in production volume is also a key advantage. Chinese CNC shops can accommodate small-batch prototypes as well as large-scale manufacturing runs, providing scalable solutions without compromising precision or consistency.
Customer-centric communication is prioritized to ensure alignment. Detailed documentation, prototypes, and sample parts are often provided during the early stages, allowing clients to verify and approve the design before full-scale production begins.
In essence, custom CNC solutions from Chinese manufacturers are a testament to their engineering prowess and commitment to client success. They adapt to the most demanding specifications, delivering components that meet exact customer expectations every time.
## Tackling High-Complexity Components with Advanced CNC Techniques
High-complexity components are the hallmark of modern engineering, demanding advanced CNC techniques and a high level of expertise. Chinese CNC machining companies have developed robust capabilities for tackling these intricate parts, which often feature complex geometries, tight tolerances, and critical surface finishes.
Multi-axis machining centers, such as 5-axis and even 7-axis machines, enable the production of parts with sophisticated shapes that would be impossible with conventional tools. These machines facilitate smooth, continuous tool paths, reducing the need for multiple setups and ensuring higher accuracy.
Advanced CAM (Computer-Aided Manufacturing) software is extensively used to simulate machining processes, optimize tool paths, and avoid collisions. This pre-emptive planning minimizes errors and enhances efficiency, especially for parts with difficult internal features or undercuts.
High-precision, high-speed spindle technology combined with precision tooling allows Chinese manufacturers to produce components with fine features and tight tolerances, often within thousandths of an inch. Such capabilities are indispensable for aerospace or medical devices where even microscopic deviations can be critical.
Specialized techniques such as micro-machining, laser ablation, and electrical discharge machining (EDM) are employed for ultra-fine detail work. For example, micro-holes, intricate cooling channels, or delicate flanges can be machined with remarkable precision.
Handling high-hardness materials like titanium, Inconel, or hardened steel presents additional challenges. Advanced CNC techniques, including optimized cutting parameters and cooling methods, are used to prevent tool wear and ensure surface integrity when working with these tough substances.
The integration of automation and robotics further enhances the ability to produce complex parts at scale. Automated pallet changers, load/unload systems, and real-time inspection tools enable continuous operation, reducing cycle times and maintaining consistent quality.
Collaborative efforts between engineers and machinists are crucial for high-complexity projects. Chinese providers often have dedicated teams specializing in complex component design, process development, and troubleshooting, ensuring that each project is executed flawlessly.
Case studies abound where Chinese CNC shops have successfully manufactured high-complexity aerospace brackets, medical implants with intricate internal channels, or precision optical components—each requiring mastery of advanced techniques and meticulous attention to detail.
In conclusion, tackling high-complexity components is a testament to the technical prowess and innovative spirit of Chinese CNC manufacturers. Their adoption of cutting-edge machinery and techniques ensures that even the most demanding designs are realized with excellence.
## Material Selection and Usage for High-Performance Machined Parts
The choice of material is fundamental to the performance and durability of high-precision machined parts. Chinese CNC manufacturers have extensive experience working with a broad spectrum of materials, understanding their unique properties, and optimizing machining processes accordingly.
Metals such as aluminum, stainless steel, titanium, and superalloys like Inconel are commonly used for high-performance applications. Each material presents distinct challenges; for example, titanium offers excellent strength-to-weight ratio but requires specialized cutting tools and cooling techniques to prevent work hardening or surface damage.
Polymers like PEEK and PTFE are also processed for applications demanding chemical resistance or bio-compatibility, especially in medical and electronic sectors. These materials often require low-temperature machining and delicate handling to avoid deformation.
Exotic materials such as ceramics, composites, and precious metals are increasingly utilized in advanced industries. Their machining demands precise control over cutting speeds, feeds, and tool selection to prevent cracking, delamination, or surface imperfections.
Material procurement is a critical step, and Chinese CNC shops often collaborate closely with suppliers to ensure consistent quality and supply chain stability. Proper storage, handling, and pre-machining treatments are standard practices to preserve material integrity.
Heat treatment and surface finishing processes are frequently integrated into the manufacturing cycle to enhance material properties. Hardening, anodizing, or coating improve wear resistance, corrosion protection, and aesthetic qualities, aligning with functional requirements.
For high-precision parts, understanding material behavior during machining is vital. Experienced engineers analyze factors such as thermal expansion, residual stresses, and machinability to fine-tune parameters and prevent defects.
The use of simulation software helps predict how materials will respond during cutting, enabling adjustments that extend tool life and improve surface finish. This predictive approach is especially important when working with difficult-to-machine composites or superalloys.
Environmental considerations are also addressed. Many Chinese manufacturers adopt sustainable practices, recycling waste materials, and minimizing the use of hazardous substances, aligning with global environmental standards.
In summary, material selection and utilization form the backbone of high-performance CNC machining. Through deep expertise and technological innovation, Chinese providers ensure that the right materials are used effectively to produce durable, precise, and reliable components for their international clients.
## The Role of Extensive Experience in Achieving Top-Quality CNC Results
Experience is perhaps the most valuable asset a CNC machining provider can possess. Chinese manufacturers leverage decades of accumulated knowledge to tackle complex projects, troubleshoot issues, and refine their processes continually.
With years of working on diverse industries—aviation, healthcare, automotive, electronics—they understand the nuances that influence machining success. This expertise enables them to predict potential challenges and implement effective solutions proactively.
They have developed a comprehensive library of best practices, cutting strategies, and tooling configurations tailored to specific materials and geometries. This repository allows for rapid response to new or unusual design requirements, saving time and reducing costs.
Mentorship and training play vital roles in maintaining high standards. Skilled technicians and engineers pass down their knowledge, ensuring that quality remains consistent even as new technologies emerge.
Experience also translates into better quality control. Seasoned operators recognize subtle signs of tool wear, material inconsistencies, or machine deviations, allowing for timely adjustments that prevent defects.
Many Chinese CNC providers have accumulated a rich portfolio of case studies and successful projects, which serve as references for future endeavors. Learning from past successes and failures accelerates innovation and process optimization.
Furthermore, their ability to interpret complex technical drawings accurately minimizes errors and rework, leading to tighter tolerances and superior surface finishes. This meticulous approach is essential for parts where precision is non-negotiable.
Customer trust is reinforced by this experience. International clients feel confident that their high-value, high-precision components are in capable hands, resulting in long-term partnerships and repeat orders.
The integration of continuous improvement initiatives, such as Six Sigma or Lean Manufacturing, reflects their commitment to refining their craft. Experience guides these initiatives, leading to efficiencies and enhanced product quality.
In essence, extensive experience empowers Chinese CNC manufacturers to deliver top-tier results consistently. Their mastery of the craft, combined with technological advancements, positions them as ideal partners for high-precision, global projects.
## Overcoming Global Challenges in Precision Machining: Case Studies
Manufacturing for international markets introduces a suite of challenges—language barriers, differing standards, logistical complexities, and material sourcing issues. Chinese CNC providers have successfully navigated these hurdles through strategic planning, technological adaptation, and quality assurance.
A notable case involved producing aerospace components with extremely tight tolerances for a European client. The challenge was ensuring precision despite variable supply chain conditions. The Chinese manufacturer responded by implementing advanced inspection techniques and dual sourcing critical materials, ensuring consistent quality.
Another example was medical device machining for a North American firm. Stringent sterilization standards and surface finish requirements necessitated the adoption of specialized equipment and coatings. The provider’s experience in handling such sensitive parts proved invaluable, resulting in successful certification and delivery.
Logistical challenges, such as shipping delays or customs issues, are mitigated by establishing local warehousing and strategic partnerships. This regional presence allows rapid response times and reduces production downtime.
Working with materials like Inconel and composites involves overcoming machining difficulties such as tool wear and material delamination. Through process innovation and specialized tooling, Chinese manufacturers have extended tool life and maintained surface integrity.
Language and communication barriers are addressed with multilingual staff and comprehensive documentation. Using digital platforms for project management and real-time updates fosters transparency and aligns expectations across borders.
Cost fluctuations and currency risks are managed via flexible pricing models and hedging strategies. This financial agility reassures international customers of stable cooperation.
Case studies also highlight successful collaborations where Chinese CNC shops adapted to evolving design specifications or regulatory standards. Their agility and expertise turned potential obstacles into opportunities for innovation and growth.
Overall, these real-world examples demonstrate that Chinese CNC manufacturers possess not only technical skills but also strategic resilience. Their ability to adapt and solve problems has cemented their reputation as reliable partners across the globe.
## Precision Manufacturing for Aerospace: Meeting Stringent Standards
Aerospace components demand the highest levels of precision, reliability, and safety. Chinese CNC machining companies have established robust capabilities to meet these exacting standards, from material selection to final inspection.
Materials such as titanium alloys, aluminum, and high-strength steels are machined with exceptional care, considering their critical roles in aircraft safety. The use of specialized tools and cooling techniques prevents deformation and maintains surface integrity.
Design complexity in aerospace parts—like turbine blades or structural brackets—requires multi-axis machining and advanced programming. Chinese manufacturers employ high-end CAM software and automation to achieve the intricate geometries demanded.
Tolerance control is paramount; parts often require tolerances within microns. Extensive use of coordinate measuring machines (CMM), laser scanning, and non-destructive testing ensures each component conforms to strict specifications.
Compliance with international standards such as AS9100, NADCAP, and ISO 9001 is meticulously maintained. Certification processes involve rigorous audits, documentation, and traceability, which Chinese providers have embraced to gain trust from global aerospace firms.
Surface treatments like anodizing or coating further enhance parts’ resistance to corrosion and wear, extending their service life. Such treatments are integrated seamlessly into the manufacturing process.
Quality control extends beyond inspection; statistical process control (SPC) and real-time monitoring help detect deviations early, ensuring batch consistency and reducing scrap rates.
The ability to produce prototypes rapidly and scale mass production efficiently makes Chinese CNC shops valuable partners. Their experience in aerospace projects translates into reduced lead times without sacrificing quality.
Collaborations with international aerospace companies have led to innovative solutions, such as lightweight structural components that contribute to fuel efficiency.
Ultimately, their adherence to stringent standards, technological sophistication, and quality assurance systems enable Chinese CNC manufacturers to deliver aerospace parts that meet or exceed global expectations.
## Medical Device Machining: Ensuring Accuracy and Sterility
Precision in medical device manufacturing is non-negotiable, where even microns can impact device performance and patient safety. Chinese CNC machining companies have specialized in producing sterile, highly accurate components for the healthcare industry.
Working with biocompatible and sterilizable materials such as stainless steel, titanium, and PEEK requires controlled environments and meticulous process management. Cleanroom facilities are often employed to prevent contamination during critical stages.
Designs with micro-features, internal channels, and delicate geometries necessitate advanced CNC techniques, including micro-milling, laser machining, and EDM. The expertise in these methods ensures functionality without compromising structural integrity.
Surface finish quality is crucial; smooth, polished surfaces prevent bacterial adhesion and facilitate sterilization. Post-machining processes like electro-polishing and passivation are routinely used to meet these biocompatibility standards.
Certification to medical quality standards, such as ISO 13485, is a fundamental requirement. Chinese CNC providers invest in quality management systems that ensure traceability, validation, and compliance with international regulations.
Lead times are critical due to the urgency of medical needs. Experienced manufacturers optimize workflows and maintain flexible production schedules to respond swiftly without sacrificing quality.
The ability to produce small batch prototypes for testing, as well as large-volume production, makes these Chinese suppliers versatile partners. They often collaborate with R&D teams to refine designs for manufacturability and performance.
Adherence to sterilization protocols and packaging standards ensures that parts remain sterile during transit and storage. This integrated approach minimizes risks associated with contamination or defects.
Finally, ongoing technological investments and staff training keep these manufacturers at the forefront of medical machining. Their commitment to innovation ensures they can handle future challenges in the rapidly evolving healthcare landscape.
In summary, high-precision CNC machining for medical devices is a specialized field that Chinese providers have mastered through experience, strict quality control, and advanced technology—all crucial for safeguarding patient health and advancing medical innovation.
## Automotive Component Production: Balancing Speed and Precision
The automotive industry demands high-volume, high-precision manufacturing to keep pace with rapidly evolving vehicle technologies. Chinese CNC machining companies excel at providing efficient, reliable production of critical automotive components, from engine parts to electronic housings.
Speed is vital; these manufacturers utilize automation, robotics, and lean manufacturing principles to shorten cycle times without compromising accuracy. Their extensive equipment base allows them to scale production according to demand.
Precision remains paramount; close tolerances and surface quality are achieved through advanced multi-axis machines, high-precision tooling, and real-time inspection systems. This ensures parts fit perfectly and perform reliably over millions of cycles.
Material diversity in automotive applications—such as aluminum alloys, cast iron, and composites—requires tailored machining strategies. Chinese CNC providers have the expertise to optimize processes for each material, preventing issues like tool wear or surface imperfections.
Cost-effectiveness is achieved through process optimization, bulk procurement, and high-capacity factories. This allows them to offer competitive pricing for large batches, appealing to automakers worldwide.
Design for manufacturability is a key focus, with experienced engineers collaborating with clients to refine parts that are easier and quicker to produce. This approach reduces waste and accelerates time-to-market.
Quality assurance protocols, including SPC, automated inspection, and traceability, are embedded throughout production. This ensures consistency and compliance with automotive safety standards.
Flexibility in handling custom orders or design revisions is another strength. Whether for traditional internal components or innovative electric vehicle parts, Chinese CNC shops adapt swiftly to changing specifications.
Lastly, their global logistics networks ensure timely delivery, even for complex, large-scale projects. This reliability helps automakers maintain their production schedules and meet market demands.
In conclusion, Chinese CNC manufacturers balance speed, precision, and cost, making them valuable partners in the competitive automotive landscape worldwide.
## High-Precision CNC for Electronics and Semiconductor Parts
Modern electronics and semiconductor industries require components with nanometric precision, flawless surface finishes, and impeccable cleanliness. Chinese CNC machining companies have risen to meet these exacting standards through technological innovation and rigorous quality control.
Producing intricate electronic housings, connector parts, or semiconductor chips demands multi-axis CNC machines, ultra-fine tooling, and dust-free environments. Cleanroom facilities are often employed to prevent contamination during manufacturing.
Material considerations are critical; substrates like ceramics, special plastics, and thin metal films are machined with precision, often requiring specialist processes such as micro-milling and laser ablation to achieve the desired features.
Surface quality and flatness are crucial for electronic performance. Post-processing steps like polishing, coating, and plasma treatments enhance electrical insulation, thermal conductivity, and durability.
Traceability and documentation are rigorously maintained, aligning with industry standards such as IPC and ISO. This ensures compliance and facilitates quality audits for clients.
Advanced inspection systems, including 3D laser scanning and electrical testing, verify that parts meet specifications at every stage. Real-time monitoring catches deviations early, ensuring batch consistency.
The rapid turnaround capability allows the industry to keep pace with its fast innovation cycle. Small batch prototyping combined with large-scale production is handled seamlessly by Chinese providers.
Design for manufacturability is emphasized, with engineers working closely with clients to optimize geometries for efficient machining, especially in miniaturized or highly complex components.
Finally, ongoing investments in equipment and talent ensure that Chinese CNC companies stay at the forefront of electronics manufacturing, supporting the industry’s push for smaller, faster, and more reliable devices.
In essence, their mastery of micro-machining, material science, and cleanliness standards makes Chinese CNC manufacturers an integral part of the global electronics supply chain.
## Leveraging Cutting-Edge Technologies for Difficult-to-Machine Materials
Some materials, such as Inconel, titanium alloys, or advanced composites, present significant machining challenges due to their hardness, thermal properties, or chemical reactivity. Chinese CNC manufacturers have adopted cutting-edge technologies to conquer these hurdles.
High-speed, high-torque spindle technology combined with coated, durable cutting tools extends tool life and enhances precision when working with tough materials. This reduces downtime and costs associated with tooling replacement.
Cryogenic and flood cooling techniques are employed to manage heat generation, prevent work hardening, and maintain dimensional stability. These methods are especially effective for superalloys like Inconel used in high-temperature environments.
Specialized tooling, including diamond-coated or ceramic tools, allows for delicate, precise cutting of difficult materials. Their use minimizes surface defects and ensures tight tolerances.
Additive manufacturing techniques, such as hybrid CNC milling combined with 3D printing, are increasingly integrated into production lines. This approach facilitates complex geometries and internal features that traditional methods struggle with.
Advanced simulation software enables engineers to model material behavior during machining, optimizing parameters beforehand. This proactive strategy improves efficiency and reduces material waste.
Cleanroom and controlled environment machining are often necessary, especially for aerospace and medical-grade materials, ensuring contamination-free parts and consistent quality.
Robotic automation and adaptive control systems enable real-time adjustments to cutting conditions, compensating for tool wear and material inconsistencies, thus maintaining stability over long production runs.
Continuous R&D investments keep Chinese manufacturers at the forefront of material machining. Their expertise translates into higher yields, better surface finishes, and parts that meet the most demanding specifications.
In summary, leveraging the latest technology allows Chinese CNC providers to turn challenging materials into reliable, high-performance components, supporting the innovation needs of industries worldwide.
## Ensuring Consistency and Quality in Large-Scale High-Precision Orders
Managing large volumes of high-precision components requires rigor, consistency, and scalable processes. Chinese CNC manufacturers excel in maintaining quality standards across extensive production runs through advanced systems and methodologies.
Standardized procedures, adherence to international certifications, and comprehensive documentation form the backbone of quality assurance. These practices ensure traceability from raw materials to finished parts.
Automation plays a vital role in reducing human error. Automated loading/unloading, in-line inspection, and real-time monitoring systems facilitate consistent output and early detection of deviations.
Advanced statistical process control (SPC) techniques are employed to monitor key parameters continuously. This data-driven approach identifies trends and stabilizes processes before defects occur.
Regular calibration and maintenance of machinery ensure that machines operate within specified tolerances. Preventive maintenance schedules extend equipment lifespan and reduce unscheduled downtime.
Quality control inspectors utilize high-precision CMMs, laser scanners, and other nondestructive testing methods to verify batch conformity. Sampling plans are optimized to balance thoroughness with efficiency.
Supply chain management is streamlined to ensure material quality and timely deliveries. Strategic partnerships with reliable suppliers minimize variability and delays.
Training and workforce development are prioritized to uphold skill levels and foster a culture of quality. Experienced staff can quickly adapt to process changes or new product requirements.
Customer feedback loops and continuous improvement initiatives further enhance process stability. Regular audits and performance reviews ensure compliance with industry standards and customer expectations.
Finally, scalable infrastructure, from large-capacity factories to flexible assembly lines, enables Chinese OEMs to handle high-volume projects without sacrificing precision or quality.
In conclusion, through technological innovation, rigorous quality management, and experienced personnel, Chinese CNC manufacturers successfully deliver large-scale, high-precision orders that meet the most demanding global standards.
---
### OUTRO:
As the world’s manufacturing hub continues to evolve, Chinese CNC machining services are proving their capability, expertise, and reliability in delivering high-precision components across diverse industries. Their ability to customize solutions, manage complex geometries, and uphold stringent quality standards makes them invaluable partners for international companies seeking excellence in manufacturing. With ongoing technological advancements and a deep pool of experienced talent, these providers are poised to remain at the forefront of global precision machining, supporting innovative projects and pushing the boundaries of what’s possible.