Expert CNC Machining for High-Precision Global Customers
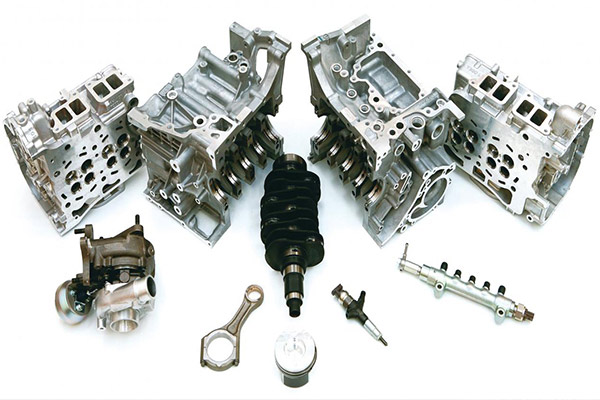
In an era where precision and reliability define success across industries, expert CNC machining has become the backbone of high-performance manufacturing for global clients. From aerospace to medical devices, the demand for intricate, high-precision parts continues to grow. China's CNC machining factories have risen to meet this challenge, offering tailored solutions that cater to demanding international markets. With advanced technology, skilled craftsmanship, and a focus on custom specifications, these manufacturers deliver unparalleled quality in complex component production. This article explores how leading CNC machining experts provide high-precision results worldwide, emphasizing customization, material mastery, and innovative problem-solving. We will also examine real-world cases illustrating their ability to overcome tough machining challenges and the importance of expertise in achieving excellence in this competitive field.
## Leading CNC Machining Experts Deliver High-Precision Results Globally
Over the years, China’s CNC machining industry has transformed into a hub of high-precision manufacturing, serving customers around the globe. These experts leverage cutting-edge technology, including multi-axis machining centers and sophisticated control systems, to produce components with tolerances often within microns. Their reputation is built on the ability to deliver consistent quality, even for the most complex geometries or specialized materials. Many of these factories operate under strict international standards, ensuring products meet the demanding requirements of aerospace, automotive, and medical sectors. Customer trust is further cemented through rigorous quality assurance processes, including detailed inspections, certifications, and traceability. In a highly competitive market, these companies stand out by providing reliable, fast turnaround times while maintaining excellence at every stage of production. Their global reach is supported by advanced logistics and flexible production capabilities, allowing seamless service across different time zones and industries. This widespread presence has made China a key player in high-precision CNC machining for international clients.
## Custom CNC Manufacturing Aligned Precisely to Client Drawings
One of the hallmarks of top-tier CNC machining is the ability to translate detailed customer drawings into real, functional parts with exact specifications. The process begins with comprehensive understanding and analysis of the client’s design, often involving CAD models and technical drawings. Expert CNC manufacturers meticulously review these plans, identifying potential challenges in material selection, tolerances, or complex features. They then develop optimized machining strategies that ensure each detail is accurately realized. Customization is crucial—whether it’s unique geometries, tight tolerances, or special finishes, the manufacturers tailor their tools and processes accordingly. This level of precision requires not only advanced machinery but also highly skilled operators who interpret drawings with an eye for detail. Communication with clients is key, allowing iterative adjustments to refine the design for manufacturability without compromising functionality. Ultimately, this dedication to custom alignment guarantees that every part produced fits seamlessly into the customer’s assembly or product line.
## Tackling Complex and High-Difficulty CNC Machining Challenges
High-precision manufacturing often involves complex geometries, tiny features, or high-strength materials that push traditional machining limits. Leading CNC experts excel in tackling these difficult challenges through innovative tooling, multi-axis machining, and adaptive strategies. For instance, machining intricate internal channels or micro-features requires specialized micro-tools and precise control. Tough materials like aerospace alloys or composite composites demand advanced cutting techniques and cooling methods to prevent deformation or tool wear. Difficult geometries such as undercuts, deep cavities, or complex surface contours are managed via multi-axis CNC centers that allow for multiple angles and orientations, reducing the need for extensive part re-positioning. Overcoming these challenges also involves rigorous process validation and trial runs to ensure accuracy. The industry’s ability to handle such high-difficulty parts is a testament to their technological investment and expertise, enabling production of cutting-edge components for demanding sectors.
## Advanced Material Utilization for Superior CNC Precision Parts
The choice of material plays a pivotal role in CNC machining quality, especially for high-precision applications. Leading manufacturers employ a broad spectrum of advanced materials—such as titanium, aerospace-grade aluminum, stainless steels, ceramics, and composites—to meet client requirements for strength, weight, and durability. Each material presents unique machining characteristics; some are hard and abrasive, requiring specific tooling and cutting parameters, while others demand specialized surface treatments. Skilled machinists understand the nuances of working with these materials, optimizing speeds, feeds, and coolant use to achieve optimal finishes and tight tolerances. They also leverage material properties to enhance component performance, such as corrosion resistance or thermal stability. The ability to accurately process a diverse range of advanced materials ensures that parts meet stringent quality standards for high-stress or critical environments. This material mastery underpins the reliability and longevity of the finished products, essential for the global markets served.
## Extensive Experience in Handling Tough and Unique Materials
Handling tough or unconventional materials in CNC machining demands extensive experience and technical finesse. Many high-precision components require working with materials like superalloys, hardened steels, or ceramic composites, which are inherently difficult to machine. Experienced CNC manufacturers have accumulated years of hands-on knowledge, enabling them to develop specialized tooling, cooling, and cutting strategies tailored to these materials. This expertise minimizes tool wear and reduces production time while ensuring the desired surface finish and dimensional accuracy. For instance, processing aerospace superalloys often involves slow feed rates, high-temperature cutting tools, and precise control of cutting forces. Similarly, working with composites necessitates careful management of fiber orientation and chip removal to prevent damage. Such proficiency allows companies to successfully produce parts that meet the rigorous demands of industries like aerospace, medical implants, and precision instruments. Their capacity to work with these challenging materials gives clients confidence in the durability and performance of the final products.
## Overcoming Global CNC Processing Difficulties with Innovative Solutions
Global CNC machining faces numerous challenges, from logistical delays to material inconsistencies and complex design requirements. Leading manufacturers combat these obstacles through innovative solutions such as automation, real-time monitoring, and advanced process optimization. Automation reduces manual intervention, ensuring consistent quality and faster throughput. Real-time data collection and feedback enable operators to make immediate adjustments, preventing defects and reducing waste. Moreover, innovative fixturing and clamping solutions facilitate complex geometries and reduce setup times. When confronted with supply chain disruptions, these companies often develop alternative sourcing strategies and flexible manufacturing workflows to maintain delivery schedules. Additionally, they invest in R&D to explore new tooling materials and cutting techniques capable of processing difficult materials and designs efficiently. This proactive approach to problem-solving enhances overall productivity and quality, making them reliable partners for international clients with high-precision needs.
## Ensuring Quality and Accuracy in High-Precision CNC Components
Quality assurance is the backbone of high-precision CNC machining. Leading factories implement comprehensive quality management systems, including rigorous inspections, dimensional measurements, and non-destructive testing. They utilize high-precision coordinate measurement machines (CMMs), optical comparators, and surface roughness testers to verify that each part conforms to design specifications. Traceability systems track every stage of production, ensuring accountability and facilitating corrective actions if deviations occur. Furthermore, process calibration and equipment maintenance are prioritized to maintain machining accuracy over time. Many manufacturers also seek certifications such as ISO or AS9100, reflecting their commitment to quality standards. Continuous staff training and process audits help identify areas for improvement, fostering a culture of excellence. The result is a consistent delivery of high-precision components that fulfill the exacting standards of clients worldwide.
## Case Studies: Solving Classic Global CNC Machining Problems
Throughout their history, top CNC machining firms have encountered and resolved numerous challenging cases that highlight their expertise. One example involved manufacturing micro-scale components with extremely tight tolerances for medical devices, requiring innovative tooling and meticulous process control. Another case saw the successful machining of aerospace-grade titanium parts with complex internal channels, demanding multi-axis machining and advanced cooling techniques. A third example involved producing high-strength, wear-resistant parts from hardened steel, where customized tooling and slow machining speeds minimized deformation. These case studies demonstrate how adaptable and inventive these companies are, often working closely with clients to optimize designs for manufacturability without sacrificing performance. Their problem-solving capabilities not only resolve immediate production issues but also push the boundaries of CNC machining technology and techniques. Such success stories reinforce trust and showcase their leadership in high-precision manufacturing.
## Importance of Skilled Expertise in High-Precision CNC Manufacturing
The cornerstone of high-precision CNC machining is undoubtedly skilled personnel. Experienced machinists and engineers interpret complex drawings, select appropriate tools, and develop precise machining strategies. Their deep understanding of materials, machine behavior, and process parameters directly influences part quality and turnaround times. Continuous training and knowledge sharing ensure that operators stay updated with technological advancements and best practices. Skilled teams can quickly troubleshoot issues such as tool wear, dimensional inconsistencies, or surface defects, minimizing downtime. Furthermore, craftsmanship and attention to detail are essential when working with intricate geometries or micro-features. The human element ensures that automation and technology are effectively leveraged and that quality standards are consistently met. Investing in talent is therefore fundamental to maintaining a competitive edge in global high-precision CNC manufacturing.
## Achieving Complex Geometries with State-of-the-Art CNC Techniques
Modern CNC machining techniques have evolved to enable the production of highly complex geometries that were previously unachievable. Multi-axis machining centers, including 5-axis and 7-axis machines, allow for free movement of the tool relative to the workpiece, enabling intricate contours, undercuts, and internal features. High-speed spindles and advanced toolpaths reduce machining time while ensuring precision. Additionally, additive manufacturing is sometimes combined with CNC to create hybrid approaches for complex designs. CAD/CAM software plays a vital role in simulating and optimizing these complex toolpaths before actual production. These technological advances enable the realization of innovative designs in sectors such as aerospace, medical implants, and electronics. The ability to produce complex geometries with high accuracy opens new horizons for product innovation and functional performance. Leading CNC manufacturers continually invest in these state-of-the-art techniques to meet evolving client demands.
## Collaborating Worldwide: Providing Reliable CNC Machining Services
Global collaboration is essential in today’s interconnected manufacturing landscape. Leading CNC machining companies serve clients across continents, often working remotely from initial design to final inspection. They utilize digital communication platforms, cloud-based file sharing, and virtual prototyping to facilitate seamless collaboration. This approach ensures clarity of specifications, quick feedback, and iterative improvements. Multicultural teams bring diverse expertise, while international standards and certifications guarantee consistent quality regardless of geographic location. The ability to coordinate across time zones, adapt to different regulatory environments, and meet varied logistical requirements makes these manufacturers reliable partners worldwide. Localized support, flexible production capacities, and multilingual customer service further enhance their global reach. As industries become increasingly globalized, such collaborative capabilities are vital for delivering high-precision CNC components efficiently and reliably.
## Future Trends in High-Precision CNC Processing for Global Markets

CNC
Looking ahead, the future of high-precision CNC machining holds exciting possibilities driven by technological innovation. Automation and artificial intelligence will enable smarter, more autonomous production lines, improving efficiency and quality control. Additive manufacturing will increasingly complement traditional CNC processes, allowing for complex, lightweight structures and rapid prototyping. The development of new, more durable cutting tools and advanced materials will expand machining capabilities for even tougher or more exotic substrates. Additionally, Industry 4.0 practices—integrating data analytics and IoT—will optimize manufacturing workflows and predictive maintenance. Sustainability efforts will drive the adoption of eco-friendly cooling and energy-efficient machinery. As global markets evolve, the emphasis will remain on delivering highly customized, precise, and reliable components through innovative solutions and expert craftsmanship. The ongoing convergence of digitalization and precision engineering promises a new era of high-performance CNC manufacturing on the international stage.