Expert CNC Machining for High-Precision Global Manufacturing
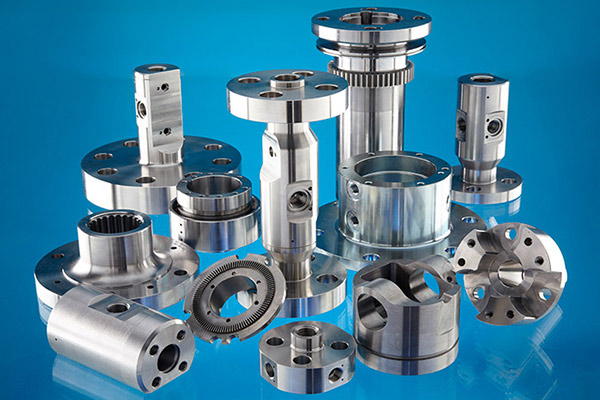
In today’s interconnected manufacturing landscape, achieving high-precision components is more than just a technical challenge; it is a strategic necessity that drives innovation, quality, and competitiveness. Expert CNC machining plays a pivotal role in fulfilling the stringent demands of global industries, from aerospace and medical devices to automotive and electronics. As technology advances, so does the importance of mastering complex machining processes, working with diverse materials, and ensuring consistent quality across borders. This article explores the vital aspects of high-precision CNC manufacturing, emphasizing the expertise, technology, and collaborative efforts that enable manufacturers worldwide to meet ever-evolving standards.
The Importance of Precision in Global CNC Machining Standards
Precision in CNC machining is the backbone of modern manufacturing that directly impacts product performance, safety, and longevity. Global standards set rigorous acceptable tolerance levels, often in microns, to ensure consistency across batches and suppliers. In high-precision industries, even the slightest deviation can lead to product failure or costly recalls.
Meeting these standards requires a combination of advanced equipment, skilled operators, and meticulous quality control processes. As international trade expands, aligning with various regional standards—whether ISO, ASME, or industry-specific norms—becomes essential for seamless integration into global supply chains.
The importance of precision extends beyond dimensional accuracy. Surface finish, internal geometries, and material integrity all contribute to the end product’s functionality. High-precision machining ensures components fit perfectly, reducing assembly time and enhancing overall reliability.
Manufacturers investing in precision CNC technology demonstrate their commitment to quality, helping their clients meet regulatory requirements and achieve higher market competitiveness. Maintaining tight tolerances also minimizes waste, leading to more sustainable manufacturing practices globally.
Furthermore, as industries push towards miniaturization and complex geometries, the demand for precise CNC machining grows exponentially. This trend underscores the necessity of adopting the latest standards and continuous improvement in machining processes.
In essence, precision in CNC machining is not just a technical metric but a strategic asset that underpins the trustworthiness and efficiency of global manufacturing endeavors.
Custom CNC Manufacturing: Turning Your Designs into Reality
Custom CNC manufacturing is the cornerstone of transforming innovative ideas into tangible, high-precision products. It allows for the production of parts that precisely match client specifications, regardless of complexity or volume. This capability is vital for industries where bespoke components are critical, such as aerospace, medical, and high-tech electronics.
The process begins with detailed design analysis, where engineers assess the feasibility of machining intricate features, tight tolerances, and specialized materials. Advanced CAD/CAM software enables precise programming of complex geometries, ensuring every detail from the drawing is accurately translated into machining instructions.
A key advantage of custom CNC manufacturing is its flexibility. Small batch sizes or one-off prototypes can be produced efficiently without the need for expensive tooling changes. This agility accelerates product development cycles and reduces time-to-market for innovative solutions.
Material selection plays a crucial role in custom manufacturing, with options ranging from titanium and stainless steel to advanced composites and ceramics. Skilled machinists understand how to optimize cutting parameters for each material, ensuring quality and tool longevity.
Quality assurance in custom CNC projects involves rigorous inspection protocols, including coordinate measuring machines (CMM), surface roughness testing, and non-destructive evaluation methods. This guarantees that each piece adheres strictly to design specifications.
By leveraging expertise and state-of-the-art machinery, custom CNC manufacturers can produce highly complex parts that meet the most demanding industry standards. Their ability to adapt to unique design challenges makes them invaluable partners in innovative product development.
Ultimately, custom CNC manufacturing bridges the gap between concept and reality, enabling companies worldwide to realize their visions with precision and confidence.
High-Complexity Components: Tackling Challenging Machining Tasks
Manufacturing high-complexity components requires mastery over advanced CNC techniques and a deep understanding of material behavior and tool dynamics. These parts often feature intricate geometries, fine detail, and tight tolerances, making them some of the most challenging to produce.
One common challenge is machining parts with internal channels, complex contours, or multi-axis features. This necessitates multi-axis CNC machines that can approach the workpiece from various angles, minimizing the need for multiple setups and reducing errors.
Challenging materials, such as aerospace-grade titanium or ceramic composites, demand specialized cutting tools, cooling strategies, and machining parameters. Skilled operators must adapt to material-specific difficulties, like high hardness or low thermal conductivity, to prevent tool wear and ensure dimensional stability.
High-precision machining of complex parts often involves a combination of roughing and finishing processes, with each step carefully orchestrated to maintain strict tolerances. Sophisticated simulation software helps predict potential issues, optimize tool paths, and prevent collisions.
Clamping and fixturing are also critical in handling delicate or asymmetrical components. Custom fixtures are often designed to stabilize parts securely while allowing access to all necessary machining surfaces.
Real-world case studies have shown that overcoming these challenges often involves iterative testing, process adjustments, and continuous learning. Employing a collaborative approach between engineers and machinists leads to innovative solutions for complex machining tasks.
The ability to deliver high-complexity components reliably and accurately establishes a manufacturer’s reputation for excellence and problem-solving prowess in global markets.
Material Mastery: Working with Diverse and Advanced Materials
Handling a wide range of materials is fundamental to high-precision CNC machining. Each material presents unique challenges, from machinability and thermal properties to surface finish and corrosion resistance. Mastery over material behavior allows manufacturers to optimize processes and produce reliable, high-quality components.
Metals like aluminum, brass, stainless steel, titanium, and superalloys are common in precision manufacturing. Aluminum’s ease of machining makes it suitable for prototypes and high-volume parts, while titanium and superalloys are favored for their strength-to-weight ratio and heat resistance in aerospace applications.
Advanced ceramics and composites are increasingly used in electronics and medical devices, requiring specialized tools and cooling techniques due to their brittleness and low thermal conductivity. Machining these materials often involves ultra-precise control to prevent cracks or delamination.
Polymer materials, including high-performance plastics like PEEK or PTFE, are also part of diverse machining portfolios. These materials demand specific cutting speeds and feed rates to achieve desired surface finishes without melting or deformation.
Understanding the thermal and mechanical effects of machining on various materials enables the implementation of effective cooling and lubrication strategies, preserving material integrity and prolonging tool life.
Material testing and inspection are integral to ensuring properties remain intact post-machining. Techniques such as ultrasonic testing, microscopy, and hardness measurements help verify quality and suitability for intended applications.
By mastering material-specific challenges, high-precision CNC manufacturers can expand their capabilities and serve industries requiring exacting standards, such as medical implants, aerospace components, and high-tech electronics.
Experienced Machining Experts: Ensuring Quality and Accuracy
The skill and experience of machining experts are vital to achieving and maintaining high standards in CNC manufacturing. Experienced operators can interpret complex drawings, anticipate machining issues, and make on-the-fly adjustments to optimize quality.
Their deep understanding of machine capabilities, tooling options, and process parameters allows for the consistent production of parts within tight tolerances. Such expertise often translates into fewer reworks, reduced lead times, and cost savings for clients.
Training and continuous education are essential for professionals working in high-precision environments. Staying updated with the latest machine technologies, software innovations, and industry standards ensures that operators remain capable of handling complex tasks effectively.
Problem-solving skills are particularly crucial when dealing with high-precision components. Experts can troubleshoot machining anomalies, such as tool deflection, vibration, or surface defects, swiftly correcting course to prevent scrap and delays.
Quality control personnel with extensive experience conduct detailed inspections, identifying minute deviations that could compromise performance. They collaborate closely with machinists to implement corrective actions and process improvements.
Moreover, expertise extends to process development—designing efficient machining strategies that balance speed, accuracy, and tool life. This holistic approach results in high-quality output aligned with client specifications.
Ultimately, investing in skilled professionals elevates a manufacturer’s capability to produce complex, high-precision parts consistently, fostering trust and long-term relationships with global clients.
Overcoming Common CNC Processing Challenges Worldwide
Despite technological advances, CNC machining faces common challenges such as tool wear, thermal distortion, and fixture stability. Addressing these issues is essential for maintaining high accuracy across diverse applications and environments.
Tool wear remains a significant concern, especially when machining hard or abrasive materials. Using high-quality, appropriately coated tools and implementing effective cooling strategies extend tool life and maintain cutting precision.
Thermal distortion can lead to dimensional inaccuracies. Manufacturers counteract this by controlling ambient temperatures, employing in-process temperature compensation, and selecting materials with low thermal expansion coefficients.
Fixture stability is critical for precision. Custom-designed fixtures and advanced clamping techniques prevent movement or deformation during machining operations, especially for complex or delicate parts.
Vibration and chatter are common challenges impacting surface finish and dimensional accuracy. Balancing spindle speeds, optimizing tool paths, and employing damping techniques help mitigate these issues.
Material inconsistency, such as internal stresses or surface imperfections, can also cause processing difficulties. Pre-machining treatments like stress relief or surface conditioning improve machinability and final quality.
Global manufacturers often face logistical hurdles, including supply chain disruptions and varying quality standards. Strong supplier relationships, rigorous incoming material inspection, and transparent quality protocols are vital.
By adopting continuous improvement practices, leveraging advanced software simulations, and fostering skilled teams, companies worldwide can effectively overcome these common challenges in high-precision CNC machining.
Case Studies: Solutions for Complex and High-Precision Parts
Real-world case studies highlight innovative approaches and successful problem-solving in high-precision CNC manufacturing. For example, a medical device manufacturer required micro-scale components with complex internal channels. The solution involved multi-axis machining combined with meticulous fixture design and in-process inspection, ensuring compliance with medical standards.
In aerospace, a supplier faced difficulties machining titanium parts with tight tolerances. Through process simulation, specialized cooling techniques, and custom tooling, they achieved a consistent, high-quality output while extending tool life—saving costs and time.
A high-tech electronics firm needed intricate ceramic parts with smooth surface finishes. The manufacturer employed ultra-precision grinding and polishing, along with controlled atmospheres to prevent microcracks, resulting in parts that met strict performance criteria.
Another example involves the production of custom prototypes with complex geometries. Rapid prototyping techniques integrated with CNC machining allowed for quick iterations, enabling clients to refine designs before full-scale production.
These case studies demonstrate that understanding material behavior, employing advanced technology, and fostering collaboration between designers and machinists are key to overcoming high-precision manufacturing challenges.
Ultimately, sharing success stories helps build confidence among global clients, showcasing a manufacturer’s capability to solve unique and demanding problems.

CNC
The Role of Advanced Equipment in Achieving Tight Tolerances
High-precision CNC machining relies heavily on state-of-the-art equipment capable of executing complex tasks with exceptional accuracy. Multi-axis machines, high-speed spindles, and precision tooling are fundamental in achieving tight tolerances.
Multi-axis CNC machines, such as 5-axis or even 7-axis setups, allow for comprehensive access to complex geometries, reducing the need for multiple setups and minimizing cumulative errors. This capability is vital for high-precision, high-complexity parts.
High-speed spindles with advanced vibration damping ensure smooth operation, reducing surface defects and enhancing dimensional stability. Precision ball screws, linear guides, and high-quality bearings contribute to consistent movement and positioning accuracy.
Automated tool changers and intelligent tool management systems improve efficiency and ensure optimal tooling for each machining stage, reducing downtime and maintaining precision.
Laser measurement systems, in-process gauging, and real-time machine calibration enable immediate detection of deviations, allowing for on-the-fly corrections that uphold strict tolerances.
Furthermore, software integration with machine tools facilitates advanced simulations, tool path optimization, and process automation, reducing human error and increasing repeatability.
Investing in such cutting-edge equipment positions manufacturers at the forefront of high-precision manufacturing, capable of consistently delivering parts that meet the most demanding standards worldwide.
Customization and Flexibility in CNC Machining Services
Flexibility is a key attribute of expert CNC machining services, allowing manufacturers to adapt quickly to changing client needs and design modifications. Customization extends beyond just producing parts—it encompasses process tailoring, material selection, and finishing options.
Manufacturers often develop specialized machining solutions for unique geometries, including custom tooling, fixtures, and adaptive machining strategies. This flexibility enables the production of complex parts that would be impossible or cost-prohibitive with traditional methods.
In addition, short lead times and small batch capabilities cater to prototyping, R&D projects, and limited production runs, helping clients accelerate their development cycles. Digital workflows and agile project management further enhance responsiveness.
Post-machining options, such as surface treatments, coating, and polishing, can be customized to meet specific functional or aesthetic requirements. This level of service ensures that each part aligns precisely with client specifications.
The ability to handle diverse materials and complex geometries makes a CNC machining provider highly adaptable to various industries, from medical implants to aerospace components. This adaptability also supports iterative design processes, enabling rapid modifications and improvements.
Ultimately, a flexible CNC manufacturing partner adds value by providing tailored solutions, reducing costs, and enabling innovation for clients operating in competitive global markets.
Ensuring Consistency: Quality Control in High-Precision Manufacturing
Quality control is integral to maintaining high standards in CNC machining, especially for parts that demand extreme precision. A rigorous inspection process ensures every component adheres to strict dimensional and functional criteria.
Coordinate Measuring Machines (CMMs) are widely used to verify complex geometries and tolerances, providing detailed 3D measurements of finished parts. These data are compared against design specifications to identify deviations.
Surface finish assessments, including roughness measurements, ensure that components meet aesthetic and functional requirements—critical in applications like optics or medical devices. Non-destructive testing (NDT), such as ultrasonic inspection or dye penetrant testing, detects subsurface flaws or internal defects.
Statistical process control (SPC) methods monitor production variability, enabling early detection of process drifts and facilitating corrective actions. Documentation and traceability are maintained meticulously for certification purposes.
Automated inspection systems integrated with manufacturing equipment allow for real-time quality checks, reducing manual errors and increasing throughput. Regular calibration of machines and tools further sustains measurement accuracy over time.
Training staff in quality standards and fostering a culture of continuous improvement are essential for consistent high-precision output. Transparent communication with clients regarding inspection results builds trust and ensures satisfaction.
By prioritizing quality control, manufacturers can deliver parts that consistently meet global standards, reinforcing their reputation and fostering long-term collaborations.
Collaborating with Overseas Clients: Communication and Precision
Effective communication is vital when working with international clients, especially in high-precision manufacturing where clarity and accuracy influence outcomes. Clear technical documentation, including detailed drawings, specifications, and inspection criteria, lays the foundation for successful collaboration.
Language barriers can be mitigated through the use of visual aids, detailed process descriptions, and multilingual support. Regular updates, photos, and inspection reports help keep clients informed and involved throughout the production cycle.
Time zone differences require flexible scheduling and prompt responses to queries or design changes. Digital communication platforms and cloud-based project management tools facilitate seamless coordination.
Understanding cultural nuances enhances mutual trust and simplifies decision-making. Manufacturers should demonstrate transparency regarding lead times, potential risks, and quality issues, fostering a partnership approach.
Customized service offerings, such as rapid prototyping or on-site visits, can further strengthen collaboration. Additionally, adhering to international standards and certifications reassures overseas clients of the manufacturer’s commitment to quality.
Technology-driven solutions like virtual reality or 3D previews enable clients to visualize parts before production, reducing misunderstandings.
Ultimately, successful overseas collaboration hinges on transparent, proactive communication, precision in manufacturing, and a shared commitment to quality—ensuring mutual growth and long-term success.
Future Trends in CNC Machining for Global High-Precision Industries
The future of high-precision CNC machining is driven by technological innovation and industry demands for even greater accuracy, efficiency, and sustainability. Automation and intelligent systems will play increasingly significant roles, enabling fully autonomous machining processes with minimal human intervention.
Artificial intelligence (AI) and machine learning algorithms will optimize tool paths, predict maintenance needs, and enhance process stability, reducing downtime and costs. Advanced robotics will handle complex assembly and inspection tasks, expanding manufacturing capabilities.
Additive manufacturing (3D printing) integrated with CNC machining will enable hybrid processes that produce complex geometries with high precision and material efficiency. This synergy will open new avenues for design and production flexibility.
Materials science will continue to evolve, with the development of ultra-advanced composites, bio-compatible materials, and smart materials that respond to environmental stimuli, requiring innovative machining solutions.
Sustainable manufacturing practices will become central, emphasizing energy-efficient equipment, recyclable materials, and waste reduction strategies without compromising quality.
Digital twins and virtual factories will allow real-time simulation and optimization of manufacturing workflows, reducing errors and accelerating innovation cycles.
Lastly, as Industry 4.0 advances, global manufacturers will leverage interconnected systems to enhance traceability, security, and collaboration across borders, fostering a truly integrated high-precision production ecosystem.
Embracing these trends will ensure that CNC machining remains at the forefront of high-precision manufacturing, meeting the demands of a rapidly evolving global marketplace and shaping the future of industry.
High-precision CNC machining stands as a cornerstone of modern global manufacturing, enabling the production of complex, reliable, and high-quality components across diverse industries. From mastering material behaviors to leveraging cutting-edge equipment and fostering expert talent, manufacturers worldwide are pushing the boundaries of what is possible. As technology continues to evolve, so too will the capabilities of CNC machining in delivering even tighter tolerances, greater flexibility, and smarter solutions. Collaboration, innovation, and a steadfast commitment to quality will remain essential in meeting the high standards demanded by industries that underpin the future’s technological advancements. With continuous progress and adaptation, expert CNC machining will undoubtedly continue to shape a more precise, efficient, and sustainable manufacturing future worldwide.