Expert CNC Machining for High-Precision Overseas Clients
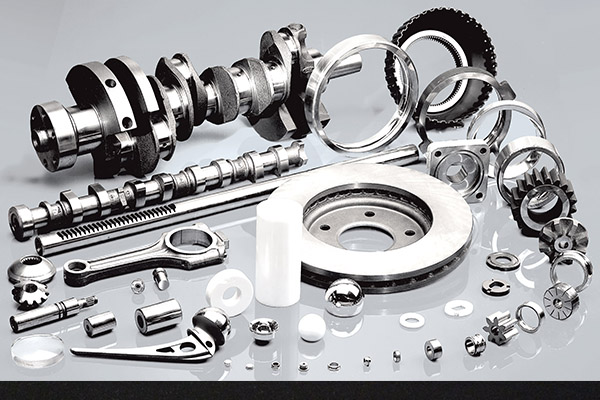
# Expert CNC Machining for High-Precision Overseas Clients
---
### Introduction to Expert CNC Machining for Overseas High-Precision Clients
In today’s global manufacturing landscape, the demand for high-precision CNC machining has never been greater. Overseas clients, from aerospace to medical device industries, require components that meet rigorous standards for accuracy, durability, and complexity. Partnering with an experienced Chinese CNC manufacturer offers a strategic advantage, leveraging cutting-edge technology and skilled craftsmanship to turn intricate blueprints into reality. These partnerships facilitate international businesses to access high-quality, cost-effective manufacturing solutions without compromising on precision or turnaround time. Understanding the nuances of expert CNC machining is essential for clients seeking reliable, high-performance parts on a global scale. This article explores the core aspects of high-precision CNC services, emphasizing customization, tackling complex parts, and the importance of extensive experience in achieving excellence.
---
### Custom CNC Machining: Turning Blueprints into Reality
Custom CNC machining is the backbone of high-precision manufacturing, transforming detailed design drawings into tangible components. For overseas clients, this process begins with comprehensive communication to understand specific requirements, tolerances, and material preferences. Advanced CNC equipment, combined with skilled operators, interprets complex blueprints through computer-aided manufacturing (CAM) software, ensuring every detail is replicated faithfully. Custom machining emphasizes adaptability, allowing for prototypes, small batches, or large production runs tailored to client needs. The ability to produce intricate geometries, such as micro-holes or tight-tolerance features, demands high-caliber machinery and meticulous process control. An experienced Chinese manufacturer offers customization options that meet international standards, ensuring clients receive parts that precisely match their specifications, whether for aerospace, medical, or precision instrument applications.
---
### Tackling High-Difficulty Parts with Advanced CNC Techniques
High-difficulty parts often present unique manufacturing challenges, including complex geometries, ultra-tight tolerances, and demanding material properties. Overcoming these hurdles requires advanced CNC techniques such as multi-axis machining, precision grinding, and specialized tooling. For example, aerospace components with intricate internal channels or medical implants with micro-level precision demand sophisticated programming and machine calibration. Chinese CNC manufacturers have invested heavily in multi-axis CNC centers, enabling the production of complex parts in fewer setups, reducing errors, and improving consistency. Techniques like high-speed machining and adaptive control optimize cutting conditions to achieve superior surface finishes and dimensional accuracy. Addressing these high-difficulty parts showcases a manufacturer’s technical expertise and commitment to quality, especially when working with challenging materials like titanium, stainless steel, or composite materials.
---
### Material Selection Strategies for Complex CNC Projects
Material choice plays a pivotal role in the success of high-precision CNC projects. Different applications demand specific material properties, such as strength, corrosion resistance, or thermal stability. In overseas markets, clients often require components made from aerospace-grade aluminum, medical-grade stainless steel, or high-performance plastics. Chinese CNC manufacturers excel in material handling, offering extensive experience in machining various substrates, including difficult-to-machine alloys like Inconel or titanium. Proper material selection involves assessing machinability, cost implications, and end-use performance. Advanced knowledge of cutting parameters and tooling compatibility is essential to prevent defects like warping, cracking, or surface imperfections. Strategic material management ensures that each project meets stringent quality standards while adhering to budget and timeline constraints, reinforcing the manufacturer’s reputation for reliable high-precision production.
---
### The Role of Extensive Experience in Achieving Precision
Experience is a cornerstone of excellence in CNC machining. seasoned manufacturers understand how to interpret complex drawings, select optimal tooling, and fine-tune machine parameters for maximum accuracy. Chinese CNC specialists have accumulated decades of hands-on experience, enabling them to anticipate potential fabrication issues before they arise. This expertise translates into better process control, fewer reworks, and consistent quality across batches. Moreover, experienced manufacturers can suggest design modifications to improve manufacturability without sacrificing functionality, ultimately saving time and costs. Their deep understanding of material behaviors, machine capabilities, and international standards ensures precision parts are delivered reliably. For overseas clients, partnering with an established manufacturer with a proven track record guarantees high-quality results, even for the most demanding specifications.
---
### Overcoming Global CNC Machining Challenges: Case Studies
Global CNC projects often encounter challenges such as language barriers, logistical delays, and varying quality standards. One notable case involved the production of aerospace engine components requiring micro-tolerance features and exotic materials. The Chinese manufacturer employed precision multi-axis CNC centers, thorough quality inspections, and rigorous process documentation to meet stringent requirements. Another case involved medical devices needing biocompatible materials machined to tight tolerances. By optimizing cutting parameters and implementing advanced surface finishing techniques, the manufacturer overcame material-specific machining difficulties. These case studies highlight the importance of technical expertise, flexible problem-solving, and meticulous quality control in overcoming international manufacturing hurdles. They reaffirm that experienced CNC partners can turn complex, high-stakes projects into successful outcomes through innovation and professionalism.
---
### Ensuring Quality and Accuracy in International CNC Orders
Quality assurance is paramount when manufacturing for overseas clients. Reliable Chinese CNC manufacturers adopt comprehensive quality management systems, including ISO certifications and strict inspection protocols. From raw material verification and in-process inspections to final dimensional checks, every step ensures adherence to specifications. The use of coordinate measuring machines (CMM), 3D scanning, and surface roughness testing guarantees precision and surface quality. Additionally, traceability systems record each production stage, providing clients with transparency and confidence. Effective communication and collaboration are vital, allowing clients to participate in quality control processes and receive timely updates. By establishing robust quality assurance measures, manufacturers minimize the risk of defects, reduce rework, and ensure that every part shipped overseas meets the highest standards of accuracy.
---
### Innovations in CNC Technology for High-Precision Manufacturing
Technological advancements continually elevate the capabilities of CNC machining. Innovations such as high-speed spindle technology, 5-axis simultaneous machining, and automation have expanded the horizons of precision manufacturing. For instance, the integration of AI-driven process optimization enhances efficiency and consistency, especially for complex parts. The adoption of advanced tooling materials, like diamond-coated cutters, improves surface finishes and reduces tool wear. Additionally, Industry 4.0 concepts enable real-time monitoring and predictive maintenance, minimizing downtime. Chinese manufacturers actively incorporate these innovations to stay competitive and meet the evolving demands of global high-precision markets. These technological improvements allow for faster turnaround times, better tolerances, and the ability to produce intricate, high-value components with unprecedented accuracy.
---
### Collaborating with Overseas Clients for Custom CNC Solutions
Successful international CNC projects hinge on close collaboration and clear communication. Chinese manufacturers emphasize understanding clients’ unique needs and maintaining transparency throughout the process. This involves initial consultations, detailed technical discussions, and providing feedback on design feasibility. Digital file sharing, virtual prototyping, and collaborative review sessions streamline the development process. Flexibility in accommodating modifications and iterative testing ensures the final product aligns with client expectations. Building long-term partnerships is vital, as it fosters mutual trust, continuous improvement, and shared success. Emphasizing customer-centric approaches, these manufacturers position themselves as reliable partners capable of delivering tailored CNC solutions that match diverse international standards and specifications.
---
### Safety and Quality Control in High-Precision CNC Production
Maintaining safety and quality is essential in high-precision CNC machining, especially when working with hazardous or sensitive materials. Chinese manufacturers implement strict safety protocols, including machine safety checks, operator training, and workplace safety standards. Quality control extends beyond inspection, encompassing environmental controls, contamination prevention, and adherence to health regulations. Automated inspection systems and statistical process control (SPC) enable real-time detection of deviations, reducing scrap rates and rework. Moreover, comprehensive documentation and compliance with international standards like ISO9001 ensure traceability and accountability. By prioritizing safety alongside meticulous quality control, manufacturers deliver reliable, consistent, and safe components suitable for critical applications worldwide.
---
### Future Trends in CNC Machining for Global Markets
The future of high-precision CNC machining is driven by innovation, sustainability, and digital transformation. Trends include the adoption of smart factories utilizing Industry 4.0 technologies, enabling real-time data analysis and autonomous process adjustments. Additive manufacturing integration with CNC, known as hybrid machining, will expand design possibilities and reduce lead times. Sustainability efforts focus on optimizing material usage, reducing waste, and employing eco-friendly cutting fluids. Additionally, AI and machine learning will further enhance predictive maintenance and process optimization. As global markets demand ever-smaller, more complex, and higher-performance components, Chinese CNC manufacturers are positioned to lead through continuous innovation, ensuring they remain vital partners for international clients seeking cutting-edge manufacturing solutions.
---
### Why Choose a Reliable Chinese CNC Manufacturer for Your Projects
Partnering with a dependable Chinese CNC manufacturer offers numerous advantages for overseas clients. These manufacturers boast advanced machinery, extensive experience, and a strong emphasis on quality and customization. Cost-effective production without sacrificing precision makes China an attractive option for high-volume and complex projects. Furthermore, established manufacturers foster transparent communication, adherence to international standards, and flexible service options. Their ability to handle diverse materials and intricate geometries ensures that clients receive high-quality parts tailored to their specifications. Choosing a reliable Chinese CNC partner means accessing innovative technology, skilled craftsmanship, and efficient logistics, all of which are essential for success in competitive global markets.
---
### OUTRO:
In summary, expert CNC machining from China provides a powerful solution for overseas clients demanding high-precision, complex components. From detailed customization and advanced techniques to material expertise and rigorous quality control, these manufacturers are equipped to meet the toughest challenges. As technology continues to evolve, so too will the capabilities of Chinese CNC providers, ensuring they remain at the forefront of high-precision manufacturing. By choosing a reputable partner with extensive experience and innovation, international businesses can confidently bring their designs to life with precision, efficiency, and excellence.