Expert CNC Machining for High-Precision Overseas Customers
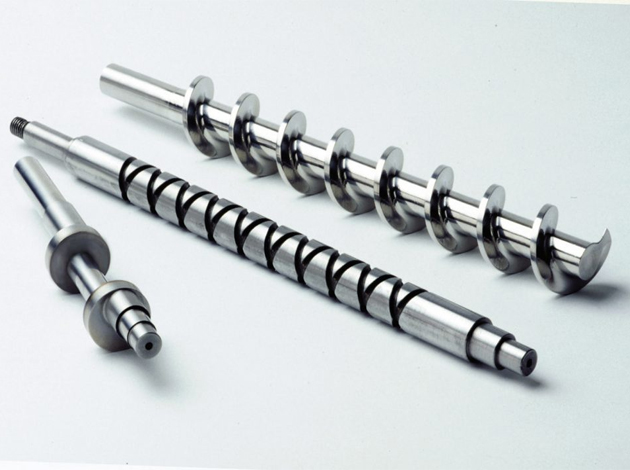
# Introduction to Expert CNC Machining for Global High-Precision Clients
In today’s interconnected manufacturing landscape, high-precision CNC machining has become a cornerstone for industries demanding tight tolerances and complex geometries. As Chinese CNC machining companies expand their reach to serve overseas clients, the emphasis on delivering reliable, customized, and high-quality parts has never been greater. This article explores how expert CNC machining services, rooted in extensive experience and advanced technology, meet the intricate needs of international customers seeking precision components. From custom solutions based on detailed drawings to overcoming global machining challenges, China’s CNC manufacturers are proving their capabilities on the world stage.
---
## Introduction to Expert CNC Machining for Global High-Precision Clients
CNC machining has revolutionized manufacturing, enabling the production of parts with exceptional accuracy and repeatability. For high-precision overseas customers, partnering with expert Chinese CNC manufacturers offers a combination of cost efficiency, technological sophistication, and flexibility. These manufacturers often possess decades of experience, allowing them to understand complex design requirements and material properties thoroughly. They serve diverse industries—medical, aerospace, optical, and more—where a single micron’s deviation can impact the entire project.
Expert CNC machining providers focus not only on cutting-edge equipment but also on process optimization and quality control. They have developed robust protocols to ensure every component meets or exceeds international standards. This commitment to excellence has established China as a reliable hub for high-precision manufacturing, capable of tackling the most demanding projects globally.
Furthermore, these companies prioritize transparent communication, enabling overseas clients to participate actively in the development process. By combining technological prowess with customer-centric service, Chinese CNC manufacturers have positioned themselves as trusted partners for high-precision manufacturing across borders.
In addition, the ability to customize solutions based on detailed technical drawings ensures that clients’ specific needs are met with utmost accuracy. This flexible approach minimizes revisions, shortens lead times, and ensures the final product aligns perfectly with application requirements.
Overall, expert CNC machining for international customers is about delivering precision, consistency, and innovation—key factors that drive success in today’s competitive global market.
---
## Custom CNC Solutions Based on Detailed Technical Drawings
One of the most critical aspects of high-precision CNC machining is the ability to translate detailed technical drawings into exact physical parts. Chinese CNC manufacturers excel in interpreting complex specifications, including tight tolerances and intricate geometries. They utilize advanced CAD/CAM software to plan and simulate machining processes before actual production, reducing errors and optimizing efficiency.
Manufacturers work closely with clients to review drawings for manufacturability, suggesting modifications if necessary to facilitate smoother machining without compromising design intent. This collaborative approach ensures that every aspect of the component—from surface finish to dimensional accuracy—is addressed from the onset.
The process begins with a comprehensive understanding of the material properties and application context, guiding the selection of appropriate machining parameters and tooling. Skilled engineers then program CNC machines to execute the design with precision, maintaining dimensional tolerances often within a few microns.
Additionally, Chinese CNC companies often offer prototyping services based on digital models, enabling clients to verify fit and function early in the development cycle. This iterative process minimizes costly revisions and guarantees that the final component aligns with the original intent.
Custom solutions are especially vital when dealing with complex geometries such as internal channels, tapered surfaces, or micro-features. Advanced five-axis machining capabilities allow for multi-directional toolpaths, ensuring precision and surface quality.
By leveraging their experience and technological resources, Chinese CNC manufacturers can produce highly customized parts that meet the most demanding specifications, providing overseas clients with confidence in the reliability and accuracy of their components.
This focus on detailed, precise, and adaptable machining processes underscores the importance of customization in high-precision manufacturing, making Chinese CNC specialists a preferred choice worldwide.
---
## Tackling Complex and High-Difficulty Machining Projects Overseas
High-precision projects often involve complex geometries and challenging materials that require advanced machining strategies. Chinese CNC manufacturers have built a reputation for handling such high-difficulty projects with expertise and efficiency.
One common challenge is machining difficult-to-cut materials like titanium, Inconel, or specialized ceramics, which demand specialized tooling, coolant systems, and cutting parameters. Experienced manufacturers optimize these variables to achieve the desired surface finish and dimensional accuracy without damaging the material.
Another challenge is manufacturing miniature or micro-components where even the slightest deviation can cause functional issues. Ultra-precision five-axis machining allows for intricate internal features and tight tolerances, ensuring high quality in small-scale parts.
Complex aerospace or medical components with multi-level geometries and demanding tolerances require sophisticated fixturing and vibration control systems. Chinese CNC providers often develop custom fixtures and employ vibration dampening technologies to maintain stability throughout the machining process.
Furthermore, handling large or heavy parts presents logistical and technical hurdles. Skilled operators and automated workholding systems facilitate safe, precise machining of sizable components, maintaining accuracy across the entire part.
The expertise in problem-solving and process innovation allows Chinese CNC companies to overcome these hurdles efficiently, even when working remotely for overseas clients. They leverage cutting-edge equipment, continuous process monitoring, and real-time adjustments to meet tight deadlines and quality standards.
Successfully delivering complex projects internationally has reinforced China’s position as a leader in high-difficulty CNC machining, making it a reliable partner for challenging engineering requirements worldwide.
---
## Material Selection and Application for Precision CNC Parts
Selecting the right material is fundamental to achieving high accuracy and durability in CNC machined parts. Chinese manufacturers emphasize material understanding, considering factors like machinability, strength, corrosion resistance, and thermal stability.
Common materials include aluminum alloys for lightweight components, stainless steels for corrosion resistance, titanium for aerospace applications, and specialized ceramics for high-temperature environments. Each material necessitates specific tooling, cutting speeds, and coolant strategies to optimize machining.
Manufacturers often collaborate with clients to determine the best material based on the application, performance requirements, and cost considerations. They provide guidance on material sourcing and quality assurance, ensuring traceability and compliance with international standards.
In high-precision projects, material properties directly influence tolerances and surface finishes. For example, softer metals like aluminum are easier to machine but might require additional post-processing for fine finishes. Harder materials such as Inconel demand specialized tools and slower cutting speeds but provide superior performance in extreme environments.
Processing exotic or composite materials introduces additional challenges, including chip removal and thermal management. Chinese CNC firms develop tailored solutions for these materials, such as optimized cutting paths and specialized coolant delivery systems.
The correct material choice can significantly extend the lifespan of the component and improve performance, particularly in critical applications like medical implants or aerospace parts where failure is not an option.
By combining material science with advanced machining techniques, Chinese CNC manufacturers ensure that every part fulfills strict specifications and functions reliably in demanding operational conditions.
This comprehensive approach to material selection and application underscores the importance of expertise in delivering high-precision components that stand the test of time.
---
## The Role of Extensive Experience in Achieving Precision Standards
Experience is the cornerstone of high-precision CNC machining. Chinese manufacturers with decades of industry involvement have cultivated a deep understanding of materials, tooling, and process optimization.
This wealth of knowledge enables them to anticipate potential issues, such as tool wear, thermal deformation, or dimensional drift, and implement proactive solutions. Experienced engineers can modify machining parameters in real-time to maintain tight tolerances and surface quality.
Furthermore, long-standing expertise fosters the development of proprietary machining techniques and workflow improvements that enhance efficiency and consistency. These innovations help minimize waste, reduce lead times, and lower costs—all critical factors for overseas clients seeking reliable supply chains.
Quality assurance is deeply rooted in experience. Seasoned manufacturers have established rigorous inspection protocols and calibration routines, ensuring each batch of components complies with international standards like ISO or AS9100.
They also possess a vast library of troubleshooting cases, allowing them to quickly identify and rectify issues during production. This problem-solving capability is crucial when dealing with complex or high-precision parts where errors can be costly and time-consuming.
Additionally, seasoned CNC providers maintain ongoing staff training programs, ensuring that their personnel stay abreast of the latest technological advancements and industry best practices.
Ultimately, their extensive experience translates into a higher success rate for high-precision projects, reducing risk and instilling confidence among international clients.
Such expertise is invaluable when delivering complex, high-tolerance components that demand consistent quality and precision over large production runs.
---
## Overcoming Common Challenges in International CNC Machining
Working with overseas clients introduces unique challenges, including language barriers, remote communication, and logistical complexities. Chinese CNC manufacturers have developed effective strategies to mitigate these issues and ensure seamless collaboration.
One prevalent challenge is ensuring clear understanding of detailed technical drawings and specifications. To address this, many companies employ multilingual staff, professional translation services, and detailed documentation practices. They also utilize visualization tools like 3D models to clarify complex geometries.
Time zone differences can delay communication and decision-making. To counter this, manufacturers often set up dedicated project management teams that coordinate with clients across time zones, providing regular updates and quick responses.
Logistics and shipping international parts involve customs procedures, quality checks, and transportation risks. Experienced companies work with reliable logistics partners and prepare comprehensive documentation to streamline customs clearance and minimize delays.
Maintaining consistent quality across overseas shipments is another concern. Implementing strict quality control protocols and utilizing advanced inspection technologies like coordinate measuring machines (CMM) helps ensure each batch meets high standards before dispatch.
Additionally, cultural differences may influence project expectations. Building strong relationships through transparent communication and mutual understanding fosters trust and long-term cooperation.
The use of digital collaboration platforms enables real-time sharing of data, drawings, and inspection reports, further enhancing transparency.
Overcoming these challenges requires a combination of technological solutions, process discipline, and cultural sensitivity—elements that Chinese CNC manufacturers are continuously refining to serve international clients effectively.
---
## Case Studies: Solving Global Difficulties in CNC Manufacturing
Real-world examples highlight the problem-solving capabilities of Chinese CNC manufacturers when faced with global machining challenges. One case involved a medical device company in Europe requiring micro-scale, high-precision titanium parts.
The project demanded tolerances within ±2 microns, intricate internal channels, and a flawless surface finish. The Chinese manufacturer employed ultra-precision five-axis machining and developed custom fixturing to secure the tiny components.
Despite challenges related to titanium’s hardness and machining difficulty, they optimized cutting parameters and used specialized coolant systems, successfully delivering parts on time and within specifications.
In another case, a aerospace client from North America needed large structural components with complex geometries. The challenge was maintaining accuracy over large dimensions while managing material warping.
The solution involved employing vibration damping fixtures and real-time process monitoring. The manufacturer also collaborated closely with the client’s engineering team to refine design tolerances, ensuring fit and performance.
A third example involved a high-temperature ceramic component for the electronics industry, demanding micro-milling and micro-hole drilling.
Through advanced micro-machining techniques and meticulous quality inspections, the Chinese company achieved the required precision and surface quality—something difficult for many overseas suppliers.
These case studies demonstrate the adaptability, technical expertise, and commitment to quality that Chinese CNC manufacturers bring to global high-precision projects.
Overcoming diverse challenges across industries highlights the importance of experience, innovation, and collaboration in achieving international machining excellence.
---
## Advanced Techniques for Precision and Tolerance Control
Achieving and maintaining demanding tolerances requires the integration of advanced machining techniques and control systems. Chinese CNC companies utilize state-of-the-art equipment such as five-axis machining centers, high-speed spindles, and precision measurement systems.
Real-time process monitoring tools enable operators to detect deviations instantaneously, allowing immediate adjustments to cutting speeds, feed rates, or coolant flow. This proactive approach minimizes errors and enhances consistency.
Adaptive machining strategies involve using software algorithms that compensate for thermal expansion, tool wear, and other dynamic factors influencing precision. These adjustments help sustain tight tolerances throughout production runs.
Laser scanning and contact measurement devices—like coordinate measuring machines (CMM)—are employed for in-process inspections, verifying component dimensions during manufacturing rather than only at the end.
The use of high-precision tooling, such as carbide or diamond-coated tools, ensures smooth cuts and minimal surface roughness, critical for high-precision applications.
Nano-technology and surface finishing techniques, including electro-polishing and vapor honing, are applied to achieve superior surface quality and micro-roughness control.
Automation and robotics further improve tolerance control by reducing human error, especially during repetitive tasks or handling fragile components.
Developing proprietary software and control systems tailored to specific machining requirements allows Chinese manufacturers to push the boundaries of precision.
These advanced techniques, combined with skilled operators and quality assurance measures, underpin the ability to produce parts with consistent high-tolerance specifications for the most demanding international clients.
---
## Quality Assurance and Inspection for Overseas High-Precision Orders
Quality assurance in high-precision CNC manufacturing is a multi-layered process that guarantees every component meets strict international standards. Chinese CNC companies invest heavily in inspection equipment and quality management systems.
In-process inspections are carried out using advanced coordinate measuring machines (CMM), laser scanners, and optical comparators to detect deviations early. These tools ensure that dimensional tolerances are maintained throughout production.
Post-process inspections include surface finish evaluations, microstructure analysis, and non-destructive testing such as ultrasonic or X-ray inspections when necessary.
Traceability is vital, especially for aerospace and medical parts. Manufacturers maintain detailed records of raw materials, processing parameters, and inspection results, enabling full traceability from raw material to finished product.
Calibration of equipment is regularly performed to prevent measurement drift, ensuring ongoing accuracy. Staff training and adherence to ISO 9001 or AS9100 standards further reinforce quality management.
Automated data collection and reporting facilitate transparent communication with international clients, providing confidence that quality standards are consistently met.
Final inspection reports, including detailed metrology data and photos, are shared with clients before shipment, allowing for approval and documentation.
Preventive quality measures, such as root cause analysis of any deviations and continuous process improvements, help sustain high standards over long-term collaborations.
A comprehensive quality assurance approach is essential for building trust with overseas clients, ensuring their high-precision components are delivered reliably and defect-free.
---
## Collaboration with International Clients: Communication and Flexibility
Effective communication is the backbone of successful international CNC projects. Chinese manufacturers prioritize understanding client expectations and maintaining open channels for dialogue.
Utilizing digital tools such as video conferencing, shared project management platforms, and real-time data sharing ensures that clients stay informed throughout the production process.
Flexibility in design modifications, process adjustments, and lead time management allows manufacturers to adapt quickly to changing project needs or unforeseen challenges.
Proactive communication helps clarify technical details, resolve ambiguities, and prevent costly misunderstandings. This is particularly important when dealing with intricate designs or high-tolerance requirements.
Many Chinese CNC companies employ multilingual teams capable of communicating seamlessly with overseas clients, reducing language barriers and enhancing collaboration.
Regular progress updates, inspection reports, and feedback sessions foster trust and transparency, reinforcing a partnership mindset rather than a transactional relationship.
Customization of services, including expedited production, special packaging, or specific shipping arrangements, demonstrates responsiveness to client needs.
Furthermore, after-sales support and ongoing technical consultation are vital for long-term cooperation, especially for complex or critical components.
Building a collaborative relationship based on mutual understanding, flexibility, and proactive communication ultimately leads to higher customer satisfaction and repeat business.
---
## Innovations in CNC Technology for Complex Component Production
Keeping pace with technological advancements, Chinese CNC manufacturers continually incorporate innovative solutions to produce complex and high-precision components.
Emerging technologies like additive manufacturing integration with CNC machining enable hybrid processes, creating more intricate geometries and reducing material waste.
Artificial intelligence (AI) and machine learning algorithms optimize machining parameters dynamically, improving accuracy and prolonging tool life.
Adaptive control systems respond to real-time sensor data, adjusting cutting conditions for consistent precision, even with variable materials or complex features.
High-speed machining centers allow for faster production without compromising quality, enabling rapid prototyping and short lead times.
Laser-based processes, such as laser welding, engraving, and micro-machining, expand the capabilities for intricate micro features and surface modifications.
Automation and robotics streamline workflows, increase repeatability, and reduce human error, especially in high-volume or delicate applications.
Development of smart fixtures and clamping systems enhances stability during complex machining operations, ensuring tolerances are maintained.
Research into new tooling materials and coatings extends tool life and improves performance in challenging materials.
These innovations empower Chinese CNC manufacturers to tackle the most sophisticated, high-precision projects demanded by global markets.
---
## Building Trust Through Consistent Quality and Expertise
Trust is essential in international manufacturing collaborations. Chinese CNC companies build this trust through consistent delivery of high-quality parts, technical expertise, and excellent service.
Reliability in meeting deadlines, adherence to specifications, and transparent communication foster confidence among overseas clients.
Long-term relationships are nurtured by demonstrating continuous improvement, investing in new technology, and maintaining rigorous quality standards.
Case studies and client testimonials further reinforce credibility, showcasing successful past projects and problem-solving capabilities.
Offering comprehensive after-sales support, including technical assistance and replacement services, assures clients of ongoing partnership.
Proactive risk management—anticipating potential issues and addressing them before impact—strengthens trust and minimizes disruptions.
Participation in international standards and certifications signals compliance and commitment to quality, reassuring clients of their product’s reliability.
Cultural understanding and personalized service help tailor solutions to meet specific client needs, fostering loyalty and long-term collaboration.
Ultimately, consistent quality, technical mastery, and proactive engagement are the building blocks of trust that enable Chinese CNC manufacturers to thrive globally.
Such dedication to excellence ensures clients receive not just components, but confidence in their supply chain and manufacturing partner.
---
## OUTRO:
Chinese CNC machining companies, equipped with advanced technology, extensive experience, and a customer-centric approach, are transforming international high-precision manufacturing. Their ability to customize solutions, tackle complex projects, and uphold stringent quality standards makes them invaluable partners for overseas clients. As the industry continues to innovate, these manufacturers are poised to set new benchmarks in precision, reliability, and global collaboration—building a future where high-precision manufacturing knows no borders.