Expert CNC Machining for Precision High-Complexity Parts Worldwide
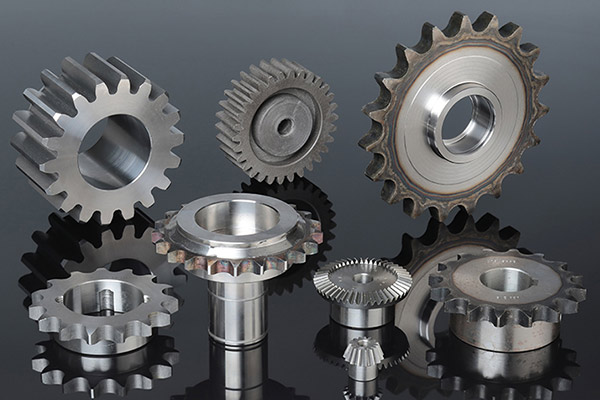
# Unlocking Precision: Expert CNC Machining for Complex Parts Worldwide
In today’s fast-paced global manufacturing landscape, the demand for highly precise and complex components is soaring across various industries—from aerospace and medical devices to automotive and industrial machinery. At the heart of this precision revolution lies CNC (Computer Numerical Control) machining, a technology that enables manufacturers to produce intricate parts with unparalleled accuracy. However, achieving these high levels of precision, especially on complex geometries and difficult materials, requires more than just advanced machinery; it demands expertise, experience, and innovative solutions. This article explores the critical role of expert CNC machining in delivering high-complexity parts worldwide, emphasizing the importance of custom solutions, material mastery, and technological advancements. We will delve into how global manufacturers overcome challenges, maintain quality, and foster trusted partnerships to meet the most demanding specifications.
===
## Unlocking Precision: Expert CNC Machining for Complex Parts Worldwide
1. CNC machining has revolutionized manufacturing by allowing for the production of highly detailed and precise components that were once difficult or impossible to achieve manually.
2. With the ability to work on a wide array of materials—including metals, plastics, and composites—CNC processes can be tailored to meet specific application requirements.
3. Complex parts often feature intricate geometries, tight tolerances, and specialized surface finishes, necessitating advanced programming and machine capabilities.
4. Expert operators and programmers play a crucial role in optimizing tool paths, reducing cycle times, and ensuring that every detail aligns with design intent.
5. Global demand calls for manufacturers capable of delivering on-time, high-quality components regardless of geographical barriers, emphasizing the importance of scalable and flexible CNC solutions.
6. Precision is not just about dimensional accuracy but also about consistency across large production runs, which requires rigorous process control.
7. High-Complexity CNC machining often involves multi-axis setups, requiring in-depth knowledge of machine kinematics and advanced fixturing techniques.
8. Manufacturers invest heavily in training and skill development to ensure their teams can handle the most challenging machining tasks efficiently.
9. The ability to adapt to new design innovations and material developments is essential for staying competitive in the high-precision market.
10. Ultimately, expert CNC machining transforms complex, high-precision designs into tangible, functional products that meet the stringent standards of global industries.
## Custom CNC Solutions for High-Precision, High-Complexity Components
1. Off-the-shelf solutions rarely suffice when manufacturing high-complexity parts, making custom CNC programming crucial for success.
2. Custom solutions begin with detailed design analysis, ensuring manufacturability and identifying potential challenges early in the process.
3. Tailored fixturing and tooling setups enable the machining of complex geometries with maximum stability and minimal deformation.
4. Advanced CAD/CAM software allows for precise simulation of machining processes, reducing errors and optimizing tool paths before production begins.
5. Custom programming also involves selecting the right cutting parameters, speeds, and feeds to handle difficult materials and intricate designs.
6. High-precision components often require multi-step processes, which are carefully sequenced to prevent material stress and ensure quality.
7. Integrating automation and robotics into CNC workflows enhances consistency, especially for small batch or prototype projects.
8. Collaboration between engineers and machinists ensures the final product adheres to strict specifications and tolerances.
9. Flexibility in manufacturing processes enables the production of diverse and complex parts without compromising quality or efficiency.
10. These custom CNC solutions are vital for industries where precision and complexity directly influence performance and safety.
## Advanced Material Utilization in CNC Machining for Diverse Industries
1. The selection of materials is fundamental to achieving desired mechanical properties and longevity in high-precision parts.
2. Metals such as titanium, inconel, stainless steel, and aluminum are frequently used due to their strength-to-weight ratios and corrosion resistance.
3. Engineering plastics like PEEK, PTFE, and UHMW are also popular for applications requiring chemical resistance and electrical insulation.
4. Difficult materials—such as superalloys—pose machining challenges due to their hardness and tendency for thermal expansion, demanding specialized tools and techniques.
5. Manufacturers with experience in advanced materials can develop process strategies that minimize tool wear and optimize cutting performance.
6. Material properties significantly influence tool selection, coolant use, and machining speeds, impacting overall quality and productivity.
7. Cross-industry applications—medical implants, aerospace components, and high-performance automotive parts—benefit from precise material processing.
8. Understanding material behaviors under machining stresses allows for better control over surface finish and dimensional accuracy.
9. Proper material handling and storage are also critical to preventing contamination and ensuring consistency.
10. The capacity to work with a broad spectrum of materials makes expert CNC machining a versatile solution for complex, high-value components worldwide.
## The Importance of Experienced CNC Machinists in Complex Part Manufacturing
1. While machinery and software are vital, the expertise of skilled machinists often determines the success of high-precision projects.
2. Experienced operators possess a deep understanding of machine dynamics, tool wear, and material responses, enabling them to troubleshoot real-time issues.
3. Their knowledge allows for fine-tuning machining parameters, particularly when working with challenging geometries and tough materials.
4. Precision manufacturing demands meticulous attention to detail, which seasoned machinists deliver through rigorous quality checks and adjustments.
5. They are adept at reading complex drawings and translating digital models into accurate physical parts.
6. Skilled personnel also play a role in process improvement, reducing waste and increasing efficiency over time.
7. Continuous training and exposure to new tools and techniques ensure machinists stay ahead in this highly technical field.
8. In high-stakes industries like aerospace and medical, their expertise directly correlates with product safety and performance.
9. Collaboration between engineers and experienced machinists creates a synergy that elevates the quality of complex components.
10. Investing in experienced talent is essential for achieving and maintaining the highest standards of precision in CNC machining.
## Overcoming Global Challenges in High-Precision CNC Machining Processes
1. Geographical barriers, time zone differences, and varying standards pose challenges for international CNC projects.
2. Ensuring consistent quality across different facilities requires strict process standardization and documentation.
3. Supply chain disruptions can delay critical materials or components, demanding proactive planning and inventory management.
4. Working with diverse materials and complex geometries necessitates adaptable machining strategies to meet tight tolerances.
5. Language and cultural differences can impact communication, emphasizing the need for clear technical documentation and collaboration tools.
6. Different countries have varying regulations and certification standards, requiring compliance management and quality assurance.
7. The integration of digital technologies enables remote monitoring and control of machining operations worldwide.
8. Developing strong, transparent partnerships helps to align expectations and foster continuous improvement.
9. Overcoming machine downtime and maintenance challenges involves predictive maintenance systems and technical support networks.
10. Despite these obstacles, innovative practices and a global mindset enable manufacturers to deliver high-precision parts reliably worldwide.
## Case Studies: Tackling Difficult Machining Tasks Across the Globe
1. One aerospace client required the production of an intricate titanium component with micron-level tolerances, demanding multi-axis machining and specialized cooling.
2. A medical device manufacturer in Europe needed complex plastic parts with ultra-smooth finishes, achieved through precision control of cutting parameters and polishing techniques.
3. An automotive company in North America faced challenges machining hardened steel parts with tiny internal channels, solved through advanced tooling and high-pressure coolant systems.
4. A defense contractor in Asia required high-precision CNC components from exotic alloys, utilizing custom fixtures and rigorous process validation.
5. A renewable energy project involved manufacturing large, complex wind turbine parts with demanding surface finishes, achieved via multi-stage machining and inspection.
6. An electronics industry client needed small batch prototypes with tight tolerances in advanced composites, relying on rapid prototyping and iterative testing.
7. Across these cases, the common denominator was the application of deep machining expertise, innovative tooling solutions, and adaptive process control.
8. Overcoming material-specific challenges often involved custom tool design and innovative fixturing strategies.
9. In each case, continuous communication and quality checks ensured the final parts met stringent international standards.
10. These global examples underscore the importance of expertise, tailored solutions, and innovative thinking in high-precision CNC machining.
## Designing for Manufacturability: How Custom CNC Machining Meets Unique Requirements
1. Design for manufacturability (DFM) is crucial in enabling efficient, cost-effective production of complex parts.
2. Early collaboration between designers and machinists helps identify potential issues related to tooling, tolerances, and material selection.
3. Simplifying complex geometries when possible reduces machining time and tooling complexity without compromising functionality.
4. Incorporating appropriate features, such as easy-to-access surfaces and standard hole sizes, streamlines the manufacturing process.
5. Tolerances are balanced with design intent to avoid unnecessary costs while maintaining performance standards.
6. Using CAD/CAM simulations allows for virtual testing of manufacturability, minimizing errors before actual production.
7. Designing with custom fixtures and modular tooling enables flexible handling of diverse and complex parts.
8. Material choice can influence design features; selecting machinable materials simplifies manufacturing without sacrificing quality.
9. Aspects like surface finish and residual stresses are considered early to prevent post-machining issues.
10. Ultimately, integrated design and manufacturing approaches ensure that high-precision requirements are met efficiently and reliably across various industries.
## Precision Tolerances and Quality Control in High-Complexity CNC Parts
1. Achieving tight tolerances requires meticulous calibration of CNC machines and regular maintenance.
2. Quality control processes include in-process inspections, using coordinate measuring machines (CMM), laser scanners, and other metrology tools.
3. Statistical process control (SPC) helps monitor and improve process consistency over production runs.
4. Advanced programming techniques, such as adaptive machining, optimize tool paths for maximum precision.
5. Material properties and environmental factors like temperature fluctuations are closely managed to prevent dimensional deviations.
6. Clear documentation and traceability are vital for meeting international standards like ISO, ASME, or industry-specific certifications.
7. Non-destructive testing methods verify the integrity of complex internal features or delicate surfaces.
8. Repeated measurement and feedback loops enable continuous improvement and early detection of issues.
9. Skilled QC inspectors interpret data to address variances proactively and implement corrective actions.
10. The culmination of these efforts ensures that high-complexity CNC parts consistently meet the strictest accuracy and quality requirements.

CNC
## CNC Machining for Prototype Development and Small Batch Production
1. Rapid prototyping allows for quick validation of design concepts before mass production, saving time and costs.
2. Small batch runs enable manufacturers to test manufacturing processes, identify potential flaws, and refine designs.
3. CNC machining offers high flexibility for producing prototypes with complex geometries and tight tolerances.
4. Custom fixturing and quick-change setups facilitate efficient transitions between different parts and iterations.
5. Advanced software allows for simulation and virtual testing, reducing the need for multiple physical prototypes.
6. This approach supports iterative development cycles, especially critical in innovative industries like aerospace and medical devices.
7. Cost-effective small batch production helps clients evaluate functionality, aesthetics, and assembly before full-scale manufacturing.
8. High-precision CNC machining ensures that prototypes accurately reflect final production parts, minimizing surprises during mass manufacturing.
9. Collaboration between design teams and machinists ensures prototypes meet expectations and inform future improvements.
10. Ultimately, CNC machining for prototypes and small batches accelerates product development and reduces time-to-market globally.
## Innovations in CNC Technology Enhancing Complexity and Accuracy
1. Multi-axis machining centers extend capabilities beyond traditional three-axis systems, allowing for complex geometries and reducing setups.
2. High-speed spindles and advanced tooling enable faster, more precise cuts on challenging materials.
3. The integration of automation and robotics increases repeatability, reduces errors, and enhances production efficiency.
4. Real-time data collection and IoT connectivity facilitate predictive maintenance and process optimization.
5. Advanced software solutions, including AI-driven tool path generation, improve accuracy and surface finish quality.
6. Laser and waterjet finishing techniques complement CNC processes, achieving superior surface finishes and intricate details.
7. Hybrid manufacturing combining additive and subtractive processes opens new possibilities for complex, high-value parts.
8. Machine learning algorithms help optimize cutting parameters dynamically, especially for difficult materials.
9. Virtual reality and augmented reality tools assist in design validation, process planning, and operator training.
10. These technological advances continually push the boundaries of what is achievable in high-precision, high-complexity CNC machining worldwide.
## Ensuring Consistency and Reliability in International CNC Machining Projects
1. Standardized procedures and certifications ensure consistent quality across multiple manufacturing sites globally.
2. Robust communication channels facilitate clear, timely exchange of designs, specifications, and feedback.
3. Uniform quality control protocols and frequent audits maintain high standards regardless of location.
4. Implementing digital tracking systems allows for real-time monitoring of production status and quality metrics.
5. Training programs ensure that all personnel adhere to best practices and industry standards.
6. Supply chain management is optimized to prevent delays and ensure material quality and availability.
7. Cross-border collaborations often leverage shared digital platforms for seamless project management and documentation.
8. Continuous improvement initiatives help identify and rectify process inefficiencies or inconsistencies.
9. Building long-term relationships with reliable suppliers and partners fortifies project stability and trust.
10. Ultimately, a comprehensive approach combining technology, quality assurance, and skilled personnel guarantees reliable, high-precision results worldwide.
## Building Trusted Partnerships for Global High-Precision Manufacturing Needs
1. Collaborations rooted in transparency and mutual understanding foster long-term trust between clients and manufacturers.
2. Clear communication of project goals, tolerances, and expectations minimizes misunderstandings.
3. Providing comprehensive technical support and consultation ensures designs are optimized for manufacturability.
4. Sharing feedback and continuous improvement efforts strengthen relationships and drive quality enhancements.
5. Flexibility in accommodating evolving project requirements demonstrates commitment and reliability.
6. Investing in advanced technologies and skilled personnel reflects a manufacturer’s dedication to excellence.
7. Certifications and compliance with international standards reassure clients of consistent quality.
8. Building a global network of trusted suppliers and logistics partners ensures timely delivery of high-precision parts.
9. Emphasizing confidentiality and intellectual property protection encourages innovation-sharing and collaboration.
10. Ultimately, trusted partnerships form the foundation for successful high-precision manufacturing solutions that meet complex international demands.
In an era where innovation and precision define competitive advantage, expert CNC machining stands as a cornerstone of modern manufacturing. From tackling complex geometries and high-performance materials to ensuring unwavering quality standards across borders, the role of experienced professionals and advanced technology cannot be overstated. By embracing custom solutions, continuous innovation, and strategic collaborations, manufacturers worldwide can unlock new potentials in high-precision, high-complexity parts—delivering excellence on a global scale. The future of manufacturing belongs to those who master the art of precision, turning intricate designs into tangible reality, regardless of the geographical or technical challenges involved.