Expert CNC Machining for Precision Parts: Overcoming Global Challenges
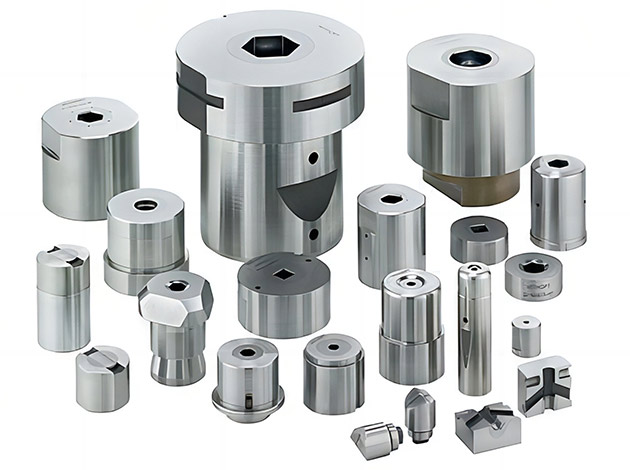
In the rapidly evolving landscape of manufacturing, the demand for high-precision, custom-engineered components has skyrocketed, driven by industries such as aerospace, medical devices, automotive, and electronics. At the heart of this technological shift lies expert CNC machining—a sophisticated process capable of transforming complex designs into tangible, precision-engineered parts. As global supply chains become more interconnected and demanding, manufacturers face an array of challenges, from intricate material properties to tight tolerances. Overcoming these obstacles requires not only cutting-edge machinery but also decades of specialized experience, meticulous process planning, and innovative problem-solving. This article explores the critical role of expert CNC machining in delivering high-precision parts worldwide, emphasizing how seasoned craftsmanship addresses the most daunting manufacturing challenges and paves the way for technological advancement.
The Importance of Custom CNC Machining for High-Precision Parts
Custom CNC machining is indispensable when it comes to producing high-precision parts tailored to specific application needs. Unlike mass production methods, CNC allows for intricate designs and tight tolerances that are often impossible with traditional manufacturing processes. Precision engineering demands exact specifications, with dimensions measured in micrometers, and surface finishes that meet strict functional and aesthetic criteria. This level of detail requires not only advanced machining tools but also an in-depth understanding of material behavior, thermal effects, and cutting dynamics. Custom CNC machining offers flexibility to adapt to unique project requirements, whether it is complex geometries, miniature components, or parts with multiple features. Such adaptability is vital in industries where performance, safety, and reliability are non-negotiable. Moreover, this approach reduces waste and shortens lead times, making it a cost-effective solution for high-value applications. The ability to produce bespoke components consistently with minimal deviations is what truly sets expert CNC machining apart in the realm of high-precision manufacturing.
Overcoming Challenging Materials Through Expert CNC Techniques
Manufacturing high-precision parts often involves working with challenging materials that pose significant technical hurdles. Materials such as titanium, Inconel, ceramics, and hardened steels are favored in demanding industries for their strength, corrosion resistance, and weight properties. However, these materials are notoriously difficult to machine due to their hardness, thermal conductivity, and tendency to work-harden or crack under stress. Overcoming these challenges requires a deep understanding of material science combined with specialized CNC techniques. Experts utilize advanced cutting tools, appropriate coolant applications, and optimized machining parameters to prevent issues like tool wear, deformation, or micro-cracks. For instance, slow feed rates and high-precision fixtures help ensure stability during machining of brittle ceramics or tough alloys. Innovative strategies such as cryogenic machining or laser-assisted cutting further enhance process capabilities. Skilled machinists also tailor tool paths and employ multi-axis machining to access complex geometries without compromising material integrity. Mastery over these techniques ensures that even the most difficult materials are transformed into precise, functional components that meet stringent industry standards.
Key Factors in Achieving Accuracy in Complex Machining Projects
Achieving exceptional accuracy in complex CNC machining projects hinges on several key factors. First and foremost is meticulous planning—understanding the design intent, selecting appropriate materials, and choosing the right tooling are fundamental steps. Proper fixture design and fixturing stability are equally critical, as even minor vibrations can lead to dimensional inaccuracies. Advanced CAD/CAM software helps simulate machining processes, identify potential issues, and optimize tool paths before actual production begins. Precision measurement and quality control are integral throughout the process, with tools like coordinate measuring machines (CMM) providing real-time feedback to ensure parts meet all specifications. Additionally, environmental control—maintaining stable temperature and humidity—reduces material expansion or contraction, which could otherwise affect accuracy. Skilled operators monitor machining parameters continuously, adjusting feeds, speeds, and coolant flow as needed. Implementing rigorous inspection protocols at various stages catches deviations early, minimizing rework. In high-precision projects, success is often determined by attention to these interconnected factors, underlining the importance of experienced craftsmanship.
Common Global Challenges in CNC Machining and How to Address Them
Global CNC machining operations face several shared challenges that can compromise quality, efficiency, and delivery timelines. Supply chain disruptions and material shortages pose significant hurdles, often necessitating the sourcing of alternative materials or adjusting machining strategies. Fluctuating exchange rates and international logistics issues also impact costs and lead times. Technical challenges such as machining exotic or hardened materials require specialized skills and equipment, which not all facilities can provide. Maintaining consistent quality across different production sites demands standardized processes, detailed documentation, and cross-site training. Environmental factors, such as temperature fluctuations and humidity, can cause dimensional variances, especially in high-precision parts. To address these issues, expert manufacturers adopt a proactive approach—building strategic supplier relationships, investing in staff training, and implementing advanced automation and quality control systems. Emphasizing communication, flexibility, and continuous process improvement helps mitigate risks and ensures reliable delivery of complex parts worldwide.
Case Studies: Solving Difficulties in Precision Part Manufacturing
Several real-world examples highlight how seasoned CNC machining experts have successfully overcome complex manufacturing challenges. One case involved producing aerospace components from titanium alloys, known for their toughness and machinability issues. By employing cryogenic machining techniques and custom tool coatings, the manufacturer achieved tight tolerances with reduced tool wear. Another case focused on machining ceramic components for medical devices, where micro-cracks threatened part integrity. Experts utilized ultra-precision grinding combined with controlled environmental conditions to ensure quality. A different project involved intricate gear components made from hardened steel, requiring multi-axis machining and specialized fixturing to prevent deformation. These cases demonstrate the importance of innovative process adaptation, advanced tooling, and rigorous quality control. They also underscore the significance of accumulated experience in troubleshooting and optimizing processes for difficult materials and designs. Such success stories serve as benchmarks for the industry, inspiring confidence in expert CNC machining’s ability to handle the most demanding projects.

Die casting
Why Experience Matters in Navigating High-Precision CNC Production
Experience is arguably the most critical factor in high-precision CNC machining. Seasoned professionals bring a nuanced understanding of material behaviors, machine capabilities, and process limitations that only comes with years of hands-on work. Their expertise allows them to anticipate potential problems, such as tool deflection, thermal expansion, or surface finish issues, before they occur. Experienced machinists can fine-tune cutting parameters in real-time to adapt to unexpected variations, minimizing scrap and rework. They also possess an intuitive grasp of complex geometries and multi-axis machining strategies necessary for intricate parts. Moreover, seasoned manufacturers have developed comprehensive quality assurance protocols and problem-solving frameworks, ensuring consistency across batches. Their insight extends to selecting suitable materials and coatings, designing effective fixturing, and optimizing cycle times—all vital for cost-effective, high-precision production. Ultimately, the depth of knowledge and skill accumulated over years elevates CNC machining from mere automation to a craft capable of meeting the highest standards of accuracy and reliability.