Expert CNC Machining Services for High-Precision Global Clients
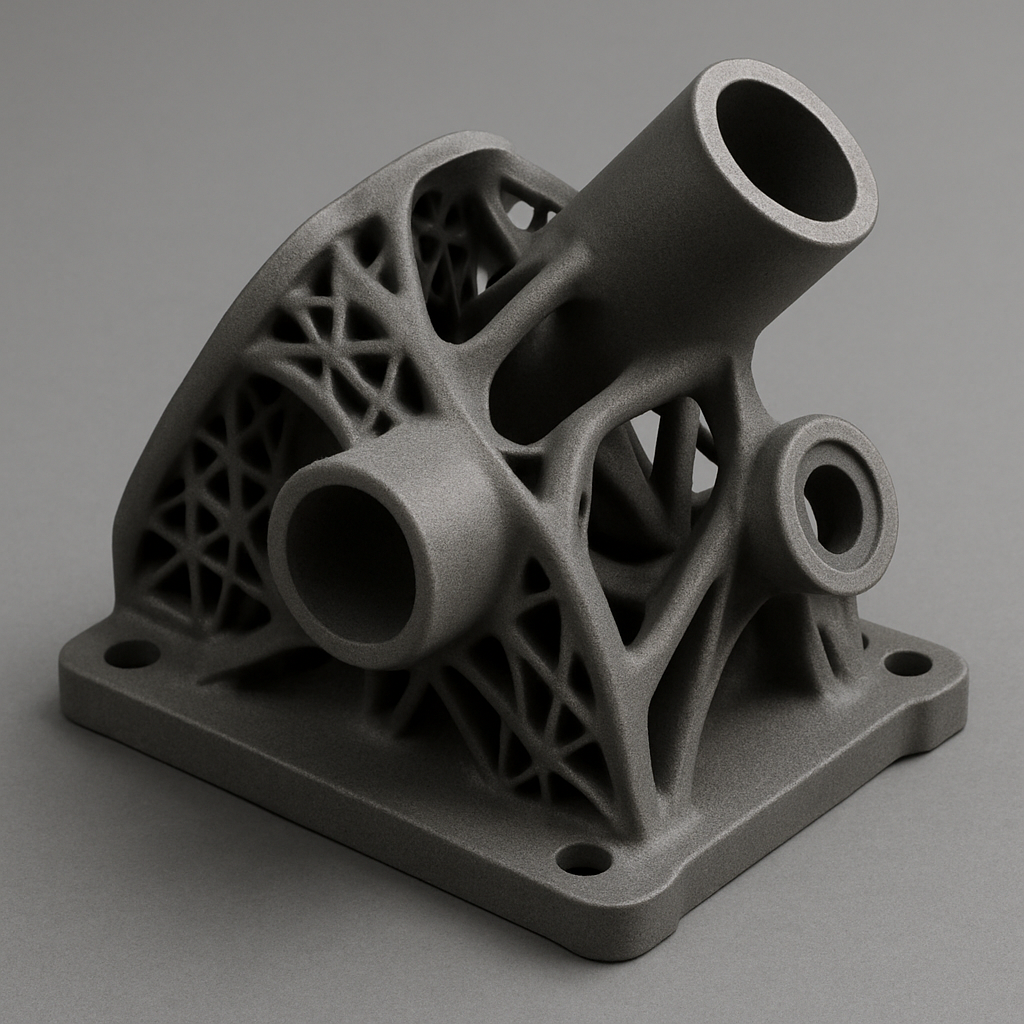
In an interconnected world where precision and quality are non-negotiable, expert CNC machining services have become the backbone of high-tech manufacturing for international clients. Specializing in custom, high-precision components, top-tier CNC machining providers serve a diverse range of industries—from aerospace and medical devices to defense and high-performance electronics. These services are distinguished by their ability to interpret intricate technical drawings, tackle complex geometries, and work with a variety of advanced materials, ensuring that each project meets stringent international standards. The global demand for dependable, accurate, and innovative CNC solutions continues to grow, pushing service providers to elevate their processes and technological capabilities. This article explores the critical elements of expert CNC machining services that cater to high-precision needs worldwide, emphasizing custom solutions, material mastery, experience, and future trends.
Introduction to Expert CNC Machining for Global High-Precision Needs
High-precision CNC machining is a cornerstone of modern manufacturing, especially for clients operating on an international scale. These clients demand not only accuracy but also consistency and reliability in every batch of parts produced. Expert CNC machining providers excel in translating complex technical drawings into physical components with tight tolerances, often as precise as a few microns. Such precision is vital for industries like aerospace, where even minor deviations can lead to critical failures.
CNC machining for global clients involves managing diverse requirements—varying standards, different materials, and complex geometries—necessitating a sophisticated level of expertise. These service providers invest heavily in state-of-the-art machinery, advanced software, and skilled personnel to ensure every project’s success. Excellent communication is crucial, as detailed specifications must be accurately interpreted and executed across different languages and time zones.
Furthermore, these companies typically adopt stringent quality control measures, including in-process inspections and final testing, to guarantee the highest standards. They also adapt their processes to accommodate various international regulatory standards, ensuring that components are compliant with client-specific and regional requirements. The ability to deliver high-precision components consistently, regardless of project complexity or material challenges, distinguishes leading CNC machining services.
Importantly, their reputation depends on their capacity for reliable delivery, quick turnaround times, and cost-effective solutions—all while maintaining impeccable quality. As industries evolve, so do the capabilities of these expert providers, adopting innovations like automation, digitization, and advanced tooling to meet ever-increasing demands.
Ultimately, high-precision CNC machining services empower global industries by providing the foundational components that enable cutting-edge technologies and innovations. They serve as strategic partners, supporting the growth and success of international enterprises through precision craftsmanship and technical excellence.
Custom CNC Machining Solutions Based on Detailed Technical Drawings
One of the hallmarks of expert CNC machining services is their ability to deliver fully customized solutions based on detailed technical drawings provided by clients. These drawings serve as the blueprint for precision manufacturing, containing critical information about dimensions, tolerances, surface finishes, and material specifications.
Precision machining providers interpret these intricate drawings with a high degree of expertise, ensuring every detail is captured accurately. This process involves translating complex 2D or 3D CAD files into machine instructions that guide the CNC equipment. Skilled operators and engineers collaborate closely with clients to clarify ambiguities and optimize machinability.
Customization often extends beyond simple dimensions. It includes selecting appropriate tooling, adjusting machining parameters, and designing fixtures that support complex geometries. For high-precision applications, even minor adjustments can significantly improve accuracy and surface quality. The result is a tailored manufacturing process that maximizes efficiency and precision.
In many cases, clients require prototype production or small batch runs before mass manufacturing. Expert providers are adept at adjusting their processes to accommodate these needs without sacrificing quality. They employ advanced simulation software to predict potential issues, minimizing waste and reducing lead times.
Furthermore, these solutions consider factors like material behavior, thermal expansion, and fixture stability, which are crucial for maintaining tolerances during machining. This comprehensive approach ensures that each component aligns perfectly with the original design intentions.
Ultimately, custom CNC machining solutions are vital for clients with specialized needs, where off-the-shelf parts are insufficient. The ability to faithfully reproduce complex designs with high precision is what sets industry leaders apart and fosters long-term trust with international clients.
Tackling Complex and High-Difficulty Machining Challenges Worldwide
High-precision manufacturing often involves tackling some of the most complex machining challenges across the globe. These include intricate geometries, extremely tight tolerances, difficult-to-machine materials, and multi-axis machining requirements. Expert CNC providers develop specialized strategies to address these hurdles effectively.
For example, machining aerospace components with complex internal channels and thin walls requires advanced multi-axis CNC machines and precise control of cutting parameters. Such parts often demand minimal warping and high surface finish quality, which in turn necessitate sophisticated tooling and process optimization.
Similarly, medical devices with micro-scale features or complex internal cavities pose unique challenges that demand ultra-precise, contamination-free operations. The use of high-precision micro-milling and laser-assisted machining processes helps overcome these difficulties, ensuring high accuracy and surface integrity.
High-difficulty parts made from titanium, Inconel, or other hard-to-cut materials require innovative approaches like cryogenic machining or plasma-assisted processes. These methods reduce tool wear and improve dimensional stability during manufacturing.
Another example is the production of precision molds and dies with complex contours and micro-textures, which demands meticulous planning and execution. Advanced CAD/CAM software combined with real-time monitoring ensures that tolerances are maintained throughout the process.
Expert CNC service providers also leverage feedback-driven adjustments, adaptive machining algorithms, and high-speed automation to tackle these complex challenges efficiently. They often share case studies of successful projects involving difficult-to-machine materials, demonstrating their problem-solving capabilities and technical expertise.
In essence, their ability to navigate and resolve high-difficulty machining challenges globally not only enhances product quality but also accelerates project timelines, making them invaluable partners for high-stakes industries.
Advanced Material Application in Precision CNC Manufacturing Processes
The application of advanced materials in CNC machining continues to grow as industries push for higher performance and durability. Expert providers are well-versed in handling a broad spectrum of materials, from traditional alloys to cutting-edge composites and ceramics.
Titanium and its alloys are popular for aerospace and medical applications due to their strength-to-weight ratio and corrosion resistance. Machining these materials requires specialized tooling and cooling strategies because of their tendency to work-harden and generate high heat. CNC providers develop tailored solutions, such as using coated tools and low-speed high-torque operations, to optimize results.
Superalloys like Inconel are critical for high-temperature environments, such as turbine blades and engine components. Their machinability challenges are addressed through cryogenic cooling, high-pressure coolant systems, and optimized cutting parameters. These techniques extend tool life and improve surface finish, ensuring reliable performance.
Advanced composites, including carbon fiber-reinforced plastics, are increasingly used for lightweight structural parts. Machining these materials demands sharp tools, slow feed rates, and specialized fixturing to prevent delamination or fiber pull-out. CNC providers develop process protocols to maintain dimensional accuracy while minimizing waste.
Ceramics, with their extreme hardness and brittleness, require precision grinding and ultra-fine machining techniques. Laser-assisted CNC machining and hybrid processes enable the production of complex ceramic components with tight tolerances and excellent surface quality.
Understanding material behavior at a microscopic level allows high-precision CNC experts to predict potential issues and implement mitigation strategies. They also continuously research new cutting tools, coatings, and machining methods to stay ahead of material-related challenges.
Ultimately, mastery over advanced material application ensures that clients receive parts that meet or exceed performance standards, even in the most demanding environments. This capability is crucial for industries that rely on high-performance materials to push technological boundaries.
The Role of Extensive Experience in Achieving Perfect CNC Results
Experience is the backbone of reliable, high-precision CNC machining for global clients. An extensive track record enables providers to anticipate potential issues, refine their processes, and deliver impeccable results consistently. Years of hands-on expertise translate into a deep understanding of material properties, tooling nuances, and process dynamics.
Veteran CNC machinists have encountered and solved a multitude of challenges, from dimensional inaccuracies to surface defects. Their problem-solving skills are honed through years of working with diverse materials and complex geometries. This experience allows them to select the best strategies for each project, minimizing trial-and-error and reducing lead times.
Moreover, seasoned providers have developed a library of proven solutions and best practices. They understand the intricacies of tool wear, thermal expansion, vibration damping, and fixture stability—factors that can significantly affect precision. Their familiarity with these variables helps maintain tight tolerances throughout production runs.
Experience also involves familiarity with international standards and quality certifications, ensuring that parts comply with various regulatory frameworks. This is especially important when working with clients in aerospace, medical, and defense sectors, where non-compliance can be costly.
In addition, experienced CNC shops leverage advanced software simulations and in-process monitoring tools, refining their processes virtually before actual machining begins. This proactive approach reduces errors and ensures that high-precision specifications are met on the first attempt.
Ultimately, the depth of experience directly impacts the accuracy, consistency, and reliability of CNC machining outcomes. For international clients seeking high-stakes, high-precision components, partnering with experienced providers ensures peace of mind and superior product quality.
Case Studies of Global Difficult Machining Projects and Solutions
Real-world case studies highlight the capabilities and innovation of expert CNC machining providers worldwide. These examples demonstrate how complex, high-difficulty projects are successfully executed, reinforcing their technical prowess and problem-solving skills.
One notable project involved manufacturing aerospace engine components from titanium with micro-scale internal channels. The challenge was ensuring tight tolerances and surface finishes, despite the material’s tendency to work-harden. The solution included employing high-pressure coolant systems and ultra-precise five-axis machining, coupled with real-time monitoring, to achieve the desired results.
Another case involved creating medical implants with intricate micro-textures on the surface from biocompatible alloys. This required micro-milling and laser finishing techniques to meet stringent surface finish standards and avoid contamination. The provider’s extensive experience in microfabrication played a key role in success.
In the defense sector, a project involved machining Inconel turbine blades with complex cooling channels. The difficulty lay in maintaining dimensional accuracy during high-temperature processing. Cryogenic machining combined with adaptive control algorithms enabled precise, high-quality production.
A different example features the production of micro-electromechanical systems (MEMS) components from ceramics. The challenge was machining brittle materials with micro-scale features. Hybrid laser-milling processes facilitated the achievement of micro-tolerances with minimal cracking or chipping.
These case studies exemplify the importance of tailored strategies, innovative techniques, and experienced personnel in overcoming global machining challenges. They also serve as proof points of a provider’s capability to deliver complex parts reliably, reinforcing client confidence and fostering long-term partnerships.
Ensuring Quality and Precision in High-Standard CNC Services
Quality assurance is integral to high-precision CNC machining, especially when serving international clients with strict standards. Expert providers implement comprehensive quality management systems that encompass every stage of production.
First, incoming materials are rigorously inspected to verify specifications and eliminate defects. Advanced non-destructive testing methods, such as ultrasonic or X-ray inspection, are often employed for critical components. This ensures material integrity before machining begins.
During manufacturing, in-process measurement tools like coordinate measuring machines (CMM) and optical inspection systems monitor dimensional accuracy and surface quality. Any deviation triggers immediate adjustments, preventing defects from propagating. Automated feedback loops enhance process stability and consistency.
Post-machining, parts undergo detailed inspection to verify tolerances, surface finish, and geometric conformity. Digital reports and certification documents are provided to clients as proof of compliance with international standards such as ISO, ASME, or industry-specific regulations.
Traceability is also maintained throughout the process, from raw material to finished component, enabling root-cause analysis and continuous improvement. Feedback from clients is actively solicited and incorporated to refine quality procedures further.
Moreover, staff are trained in quality management principles, and audits are regularly conducted to ensure adherence to best practices. This meticulous approach ensures that every piece leaving the facility meets the highest high-precision standards, fostering trust among global clients.
In essence, quality assurance in CNC machining is not an afterthought but a core aspect of service delivery, crucial for industries where failure is not an option.

3D Printing
Overcoming Material and Tolerance Challenges in Critical Parts
Manufacturing critical parts with exacting tolerances and complex materials is fraught with challenges. Expert CNC providers develop specialized solutions to navigate these issues successfully. Material behavior, such as thermal expansion, work hardening, or brittleness, can threaten dimensional accuracy.
To mitigate these problems, process parameters are meticulously optimized based on material properties. For example, slow feed rates, reduced cutting speeds, and specialized tooling help prevent deformation or cracking in sensitive materials like ceramics or superalloys.
Achieving tight tolerances—often within a few microns—requires state-of-the-art measurement systems and process controls. Multi-sensor inspection and adaptive machining algorithms enable real-time adjustments, ensuring parts stay within specified limits.
Handling complex geometries with high precision often involves multi-axis machining, custom fixturing, and innovative tooling. These strategies distribute cutting forces evenly, reduce vibration, and support delicate features.
Material-specific challenges, such as chip removal in difficult-to-machine metals, are addressed through innovative solutions like high-pressure coolant, cryogenic cooling, or laser-assisted cutting. These techniques improve chip evacuation and reduce thermal effects that can distort parts.
Tolerance challenges in critical parts demand thorough validation and testing, including non-destructive evaluation and functional testing. This process guarantees that parts not only meet dimensional specs but also perform reliably in their intended application.
By continually refining their techniques and leveraging technological advances, expert CNC providers turn material and tolerance complexities into opportunities for delivering superior, high-precision components worldwide.
Innovative Techniques for Machining Hard-to-Process Materials
Machining hard-to-process materials requires pushing the boundaries of traditional techniques. Industry leaders adopt innovative methods to achieve the desired precision and surface quality efficiently.
Cryogenic machining, which involves cooling cutting tools with liquid nitrogen, reduces tool wear and improves dimensional stability when working with superhard materials like Inconel or titanium alloys. This technique also minimizes thermal distortion.
Laser-assisted machining pre-conditions materials by locally heating or softening them, enabling easier cutting and reduced tool stress. This approach is especially effective for ceramics and hardened steels.
Ultrasonic vibration-assisted machining introduces high-frequency vibrations into the cutting process, decreasing cutting forces and enhancing surface finish on challenging materials such as composites and superalloys.
Additive-subtractive hybrid manufacturing combines 3D printing with CNC milling, allowing for complex geometries to be built layer-by-layer and then finished with high precision. This layered approach is invaluable for intricate internal features.
Advanced tooling technology, including coated carbide and ceramic cutting tools, extends tool life and enables more aggressive cutting parameters. Customized tooling design can optimize performance for specific materials.
High-speed machining techniques, supported by powerful CNC controls, facilitate efficient material removal while maintaining tight tolerances. These methods reduce cycle times and improve productivity without compromising quality.
Implementing these innovative techniques requires specialized knowledge and investment but results in superior parts that meet the demands of aerospace, medical, and high-tech industries. They exemplify the technological evolution driving modern CNC machining capabilities.
The Importance of Collaboration and Communication in Global Projects
Effective collaboration and clear communication are essential for the success of high-precision CNC projects across borders. International clients rely on seamless information exchange to ensure their specifications are accurately interpreted and executed.
From the initial consultation through design review, quoting, production, and delivery, open channels of communication facilitate understanding and alignment. Digital tools like CAD sharing, project management platforms, and video conferencing bridge geographical gaps and streamline workflows.
Detailed technical documentation, including drawings, specifications, and inspection reports, must be consistent and accessible to all stakeholders. Precise communication minimizes misunderstandings and reduces rework or delays.
Regular updates on project status, potential issues, and process adjustments foster transparency and build trust. Feedback loops allow clients to provide input during different stages, enabling timely modifications and refinements.
Cultural awareness and language proficiency also play vital roles. CNC providers often employ multilingual teams or translators to bridge language barriers and ensure technical accuracy.
Collaborative problem-solving becomes more effective when clients and providers share a mutual understanding of project goals, constraints, and expectations. This cooperation leads to higher quality outcomes and stronger long-term partnerships.
In an era where global manufacturing is commonplace, investing in robust communication strategies is crucial for delivering high-precision CNC parts that meet international standards and client satisfaction.
Future Trends in CNC Machining for High-Precision Industries
The future of high-precision CNC machining is poised for revolutionary advancements driven by digitalization, automation, and new material science. Industry leaders anticipate smarter, more connected manufacturing ecosystems.
Artificial intelligence and machine learning will increasingly optimize machining processes, predict tool wear, and reduce waste, leading to more efficient production cycles. Real-time data analytics enable proactive adjustments and quality control.
The integration of Internet of Things (IoT) devices allows for seamless communication among machines, sensors, and software, creating a highly responsive manufacturing environment. This connectivity enhances traceability and process transparency.
Additive manufacturing combined with CNC subtractive processes will enable the production of even more complex geometries with improved material properties. Hybrid manufacturing approaches will become standard for critical parts.
Advances in material development, such as new composites or ultra-hard ceramics, will expand the range of applications handled by CNC technology. Machining techniques will evolve to accommodate these innovations.
Automation will also extend to robotic arms and automated inspection systems, reducing human error and increasing throughput. Narrowing tolerances and achieving nanometer-scale precision will become more feasible.
Sustainability considerations, including energy-efficient processes and recyclable materials, are expected to influence future CNC strategies. The industry will strive for greener manufacturing practices without compromising quality.
Overall, the convergence of digitalization, materials science, and automation promises a future where high-precision CNC machining continues to push the boundaries of what is possible, supporting the next generation of technological breakthroughs.
Why Choosing an Experienced CNC Partner Matters for International Clients
For global industries requiring high-precision components, partnering with an experienced CNC service provider is a strategic decision that can significantly influence project success. Experience translates into the ability to handle complex designs, tough materials, and tight tolerances with confidence.
An experienced provider possesses a deep understanding of international standards and certifications, ensuring that parts are compliant with regional regulations. This compliance is crucial for avoiding costly delays or rejections.
Their familiarity with diverse industries—such as aerospace, medical, and electronics—means they can anticipate and address unique challenges specific to each sector, delivering tailored solutions.
Such providers also have access to advanced equipment, proprietary processes, and a skilled workforce capable of executing high-precision work consistently. They invest in continuous training and technological upgrades to stay ahead of industry trends.
Reliability, quality, and quick turnaround times are often hallmarks of experienced CNC partners. This reliability provides peace of mind, especially for critical components where failure is not an option.
Furthermore, long-term relationships with trusted providers foster ongoing innovation, process improvements, and cost savings—benefits that are invaluable for international clients seeking competitive advantages.
In sum, choosing an experienced CNC partner isn’t just about acquiring parts; it’s about securing a collaborative relationship that ensures excellence, compliance, and success in the global marketplace.
High-precision CNC machining services for international clients are a testament to technological mastery, customized solutions, and strategic partnerships. As industries evolve and demands grow, the role of experienced providers becomes ever more vital in delivering complex, high-quality components on time and within specifications. Embracing innovations, maintaining rigorous quality standards, and fostering clear communication will continue to shape the future of high-precision manufacturing—empowering global industries to achieve new heights of excellence and innovation.