Expert CNC Machining Services for Precision and Complex Parts
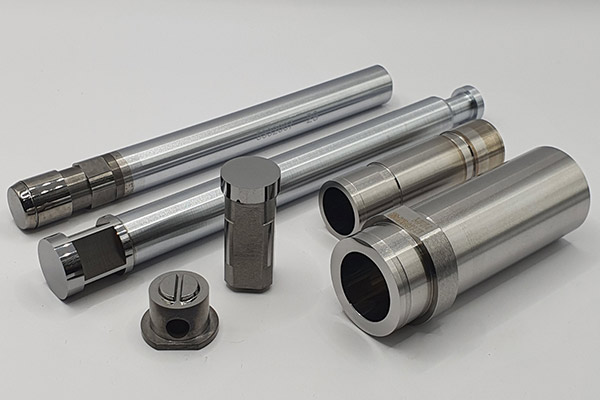
# Unlocking Precision: Expert CNC Machining for Complex Part Manufacturing
In today’s manufacturing landscape, the demand for highly precise and complex parts has skyrocketed across various industries—from aerospace and medical devices to automotive and electronics. CNC (Computer Numerical Control) machining stands at the forefront of delivering these intricate components with unmatched accuracy. With advancements in technology, expert CNC machining services have become essential for transforming detailed designs into real-world parts that meet stringent quality standards. Companies equipped with experienced operators and sophisticated machinery can handle challenging projects, ensuring clients receive reliable, high-quality outputs. This article explores how expert CNC machining services push boundaries in precision, material utilization, and complex part production, especially within the context of Chinese manufacturing excellence catering to global needs.
===
## Unlocking Precision: Expert CNC Machining for Complex Part Manufacturing
CNC machining has revolutionized the way complex parts are manufactured, offering unparalleled precision and repeatability. Expert service providers leverage advanced CNC equipment, capable of executing detailed and intricate designs with micron-level accuracy. The key to unlocking this potential lies in the mastery of programming, tooling, and process optimization. Skilled technicians understand the nuances of each material and design requirement, ensuring every cut and drill aligns perfectly with the blueprint. For high-precision industries, even the minutest deviation can compromise function; therefore, specialists employ rigorous calibration and quality control measures. The ability to handle complex geometries—such as internal channels, fine threads, or intricate contours—sets industry leaders apart. These services enable manufacturers to produce highly sophisticated parts that are impossible to create through traditional methods, ensuring innovation and performance are never compromised.
Furthermore, expert CNC machining providers often incorporate multi-axis machining capabilities, such as 5-axis or even 7-axis operations, facilitating multi-faceted cuts in a single setup. This reduces manufacturing time while enhancing the complexity of possible geometries. Their focus on precision extends to surface finish quality, tolerances, and dimensional stability, critical for applications demanding exacting standards. The integration of advanced CAD/CAM software further ensures that complex designs are accurately translated into CNC programs, minimizing errors. Overall, expert CNC machining transforms complex digital designs into tangible, high-precision components with consistency and efficiency.
In industries like aerospace, medical, and electronics, where safety and functionality are paramount, the importance of expert CNC services cannot be overstated. The ability to consistently produce high-precision, complex parts helps manufacturers meet critical certifications and quality regulations. These experts continually refine their processes, adopt new technologies, and train personnel to stay ahead in a competitive global market. Their commitment to excellence ensures that complex, high-value components are produced with the utmost reliability, supporting innovations that push technological boundaries forward.
The integration of automation and quality monitoring tools like CNC probes and real-time feedback systems further elevates the standards of precision. These advancements allow for immediate detection of deviations during machining, reducing waste and rework. As a result, manufacturers can assure clients that each component meets specified tolerances and specifications, a vital aspect for high-stakes applications. Ultimately, expert CNC machining services stand as a pillar of modern manufacturing, enabling the creation of complex parts that drive progress across multiple sectors.
Beyond precision, these services also emphasize scalability and flexibility. Whether producing prototypes, small batches, or large-volume runs, skilled CNC partners adapt seamlessly to project demands. This flexibility is crucial for industries where innovation cycles are rapid and design modifications frequent. By leveraging their deep expertise, Chinese CNC machining companies—like those exemplified by leading manufacturers—offer tailored solutions that align perfectly with diverse customer needs, ensuring excellence from concept to completion.
## Customized CNC Solutions Tailored to Your Specific Design Requirements
Every engineering project is unique, requiring bespoke manufacturing solutions that reflect specific design parameters and operational goals. Customized CNC machining services excel in transforming detailed CAD drawings into functional parts tailored to client specifications. These providers work closely with engineers and designers to understand the intricacies of each project, offering insights into manufacturability and potential improvements. They focus on achieving optimal material utilization, minimizing waste, and ensuring structural integrity, especially when working with challenging materials like titanium, stainless steel, or composites.
Customization extends beyond just dimensions; it encompasses surface finishes, tolerances, and functional features such as threading, drilling, or engraving. For instance, high-precision aerospace components may require complex internal channels with tight tolerances, demanding expert knowledge in tooling and process planning. Medical implants, on the other hand, might need biocompatible materials and ultra-fine surface finishes to ensure compatibility and longevity. Chinese CNC machining manufacturers are adept at accommodating these diverse needs, providing comprehensive solutions from initial concept to final inspection.
In addition to technical expertise, these companies often offer flexible production runs, allowing clients to iterate designs quickly without significant cost penalties. This agility supports rapid prototyping, testing, and refinement—crucial steps in industries like automotive racing or consumer electronics. Their ability to customize tooling, fixturing, and machining parameters ensures each part is crafted with precision and efficiency.
Moreover, many Chinese CNC machining services are equipped with advanced inspection and measurement tools, such as coordinate measuring machines (CMMs), to verify that parts meet bespoke specifications accurately. This commitment to quality and customization ensures that clients receive parts that not only fit their design intent but also perform reliably in demanding environments. Such tailored solutions foster innovation, reduce time-to-market, and help brands achieve competitive advantages globally.
The strategic use of high-grade materials, combined with customized machining processes, allows these manufacturers to produce parts that meet the most stringent standards. Whether it involves intricate aerospace components or specialized medical devices, high levels of customization are fundamental to delivering functional and durable parts. Ultimately, tailored CNC solutions empower industries to innovate confidently, knowing their precise specifications will be realized flawlessly.
## High-Precision CNC Machining for Challenging and Intricate Components
Producing challenging and intricate components pushes the boundaries of traditional manufacturing, demanding exceptional skill and advanced technology. High-precision CNC machining excels in creating complex geometries such as micro-holes, internal cavities, or delicate features that are often impossible with manual methods. These components are essential in sectors like aerospace, where lightweight yet strong parts are critical, or in medical devices requiring micro-scale precision.
One of the key advantages of high-precision CNC machining is its ability to maintain tight tolerances—often within microns—across complex shapes and surfaces. This level of accuracy ensures functional integrity, especially when parts need to fit together seamlessly in assemblies. For example, turbine blades with intricate cooling channels or dental implants with precise surface textures are manufactured with exacting standards. Skilled operators leverage specialized tooling, multi-axis machines, and precise control systems to achieve these demanding specifications.
Intricate components also include delicate features such as thin walls, fine threads, or complex internal structures. High-precision CNC machining companies utilize micro-machining techniques, which involve small tools and slow feed rates, to craft these features without damaging the material. Such processes require not only sophisticated equipment but also substantial experience in handling different materials and geometries.
Furthermore, the importance of comprehensive process planning cannot be overstated when machining challenging components. Experienced technicians analyze design files to optimize tool paths, cutting strategies, and cooling methods. This ensures high-quality outcomes while minimizing tool wear and preventing deformation or defects. Advanced simulation software often assists in predicting potential issues before actual machining begins.
In industries like aerospace and medical, the ability to reliably produce intricate, high-precision parts directly impacts safety and performance. These sectors demand rigorous testing and validation, often requiring repeatability across batches. Expert CNC service providers excel in this realm by maintaining strict process controls and calibration standards, ensuring each piece meets the highest quality benchmarks.
In summary, high-precision CNC machining transforms complex, delicate designs into robust, functional components. The combination of sophisticated machinery, skilled craftsmanship, and meticulous process control allows manufacturers to meet the most challenging specifications—paving the way for technological innovation and superior product performance.
## Advanced Material Utilization in CNC Machining for Diverse Industries
The versatility of CNC machining truly shines through its ability to work with a wide array of materials, from metals and plastics to composites and ceramics. This material diversity enables its application across various industries, each with specific performance and durability requirements. High-precision CNC service providers leverage their expertise to optimize the machining process for each material type, ensuring quality, efficiency, and functional integrity.
Metals like aluminum, stainless steel, titanium, and tool steels are among the most common in high-precision applications. Titanium, in particular, is prized for its strength-to-weight ratio and corrosion resistance, making it ideal for aerospace and medical devices. Machining such materials requires specialized tooling and cutting parameters due to their toughness and heat sensitivity. Experienced Chinese CNC manufacturers understand these nuances, enabling them to produce complex titanium components reliably.
In addition, advanced plastics—including PEEK, PTFE, and high-performance composites—are increasingly used for their lightweight and electrical properties. These materials are often employed in electronics, biomedical implants, and automotive parts. Their machining demands precise control to prevent melting or deformation, which expert CNC providers accommodate through optimized speeds, feeds, and coolant strategies.
Ceramics and composites, known for their heat resistance and durability, also find applications in high-tech industries. Machining brittle materials like ceramics requires delicate handling and specialized tools to prevent cracking or chipping. Experienced operators are adept at selecting appropriate techniques and fixtures to maintain material integrity during manufacturing.
The ability to work with such diverse materials expands the potential for innovation, allowing manufacturers to tailor solutions for weight reduction, chemical resistance, or biocompatibility. This flexibility ensures that CNC machining remains a vital manufacturing process across sectors ranging from aerospace and defense to healthcare and consumer electronics.
Moreover, the integration of modern CAD/CAM and simulation software assists in predicting how different materials will respond during machining, enabling adjustments that optimize tool life and surface finish quality. This proactive approach reduces costs and accelerates production timelines. The strategic use of advanced materials in CNC machining underscores its role as a versatile and reliable manufacturing methodology for the most demanding applications.
## The Importance of Experience in Handling Complex, High-Precision Parts
Handling complex, high-precision parts is a skill honed through years of dedicated experience. Knowledgeable operators understand not just the technical aspects but also the subtle nuances that influence quality, such as tool wear, material behavior, and environmental factors. This experience becomes especially critical when working with difficult geometries, tight tolerances, and expensive materials.
Experienced CNC machinists can interpret complicated drawings and identify potential manufacturing challenges early in the process. They can suggest design modifications or alternative approaches to ensure manufacturability without compromising performance. This proactive problem-solving is vital for avoiding costly rework or scrap, especially when dealing with high-value components.
Furthermore, seasoned professionals excel in selecting the right tooling, cutting parameters, and fixturing methods tailored to each project. They have a deep understanding of how different materials respond under various conditions, enabling them to optimize efficiency and surface finish. This mastery reduces machining time and extends tool life, translating into cost savings and improved lead times.
In complex projects, consistency is key. Experienced operators maintain rigorous quality control through routine measurements and real-time adjustments, ensuring each part adheres to exact specifications. They are also adept at troubleshooting issues such as vibrations, deflections, or thermal expansions that can affect precision.
Training and continuous learning are integral to maintaining this expertise, especially as new materials and advanced machine tools emerge. Leading Chinese CNC manufacturers invest heavily in workforce development, ensuring their staff stays at the forefront of technological advancements. This accumulated experience becomes a strategic asset, differentiating top-tier service providers in the global market.
Ultimately, the mastery of handling complex, high-precision parts is what enables manufacturers to consistently deliver products that meet or exceed expectations. It fosters innovation, enhances reliability, and builds long-term trust with clients across demanding industries.
## Overcoming Global CNC Machining Challenges with Innovative Techniques
The global manufacturing landscape is fraught with challenges—geographical distance, material complexities, and increasing quality standards—that require innovative solutions. Leading CNC machining companies employ advanced techniques to surmount these hurdles, ensuring clients receive precision parts on time and within budget.
One such approach is the integration of automation and smart manufacturing systems. Automated tool changers, robotic loading/unloading, and real-time monitoring enable continuous operation with minimal human intervention. This not only increases efficiency but also reduces errors, especially in high-precision tasks.
Innovative process strategies like high-speed machining, adaptive control, and minimal residual stress techniques help overcome material and geometrical complexities. High-speed machining, for example, shortens production times while maintaining surface quality, which is essential when working with delicate features. Adaptive control systems dynamically adjust cutting parameters to optimize performance and prevent defects.
Additive manufacturing and hybrid processes are increasingly incorporated into CNC workflows to produce complex internal features or to assemble multi-material components. Combining subtractive and additive techniques allows for more intricate designs and material combinations that traditional CNC alone cannot achieve.
Furthermore, companies invest in state-of-the-art simulation software to preemptively identify potential manufacturing issues, optimizing tool paths and machining parameters virtually before physical production. This proactive approach minimizes trial-and-error and accelerates project timelines.
In response to global supply chain disruptions, many Chinese CNC manufacturers have expanded their capacity, diversified their material sources, and adopted just-in-time production strategies. These measures ensure resilience and consistent quality, even under challenging circumstances.
Collaboration and communication tools also play a vital role. Cloud-based project management and digital twin technologies facilitate transparency and real-time updates, enabling clients worldwide to monitor progress and make informed decisions.
By embracing innovation—whether through cutting-edge machinery, process optimization, or digital transformation—CNC service providers continually push past global manufacturing barriers. Their agility and ingenuity guarantee that complex, high-precision parts reach worldwide markets seamlessly.
## Case Studies: Successfully Tackling Industry-Classic Difficult Machining Tasks
Real-world case studies exemplify the capabilities of expert CNC machining services in overcoming industry-specific challenges. For example, a leading aerospace client required titanium turbine blades with internal cooling channels featuring complex geometries and tight tolerances. The Chinese manufacturer employed multi-axis CNC machines, micro-drilling techniques, and extensive process validation to deliver flawless parts. The project highlighted the importance of experience and advanced tooling in handling difficult materials and geometries.
In another instance, a medical device company needed micro-precision components made from PEEK plastic with intricate surface textures. The CNC provider utilized specialized micro-milling tools, precise temperature controls, and rigorous inspection protocols to ensure compliance with biocompatibility standards while achieving the desired surface finish. This case demonstrated mastery in working with delicate, biocompatible materials.
A different example involved an automotive high-performance brake component with complex internal channels designed for heat dissipation. The challenge was to manufacture these channels without compromising strength or dimensional accuracy. The solution involved custom fixtures, high-speed machining, and real-time measurement feedback systems, resulting in high-quality parts delivered within tight deadlines.
These case studies reflect the strategic combination of technological expertise and industry experience. They confirm that expert CNC machining providers can reliably produce parts with challenging specifications, often exceeding client expectations. Their ability to solve classic problems—such as micro-machining, tough materials, or complex internal features—is vital for progress and innovation in high-tech industries.
Each success story underscores the importance of continuous process improvement, skilled workforce, and technological investment. They also serve as proof points for potential clients considering CNC partners for their most demanding projects. Ultimately, these cases reinforce the idea that with proper expertise and equipment, even the most complex machining challenges can be conquered.
## Ensuring Quality and Accuracy in High-Precision CNC Manufacturing Processes
Quality assurance is the backbone of high-precision CNC machining. Every stage—from design validation to final inspection—must adhere to strict standards to guarantee that parts meet exacting tolerances and specifications. Leading CNC service providers implement comprehensive quality management systems, including ISO certifications, to uphold these standards consistently.
Advanced measurement tools such as coordinate measuring machines (CMMs), optical comparators, and laser scanners are employed to verify dimensions, surface finishes, and geometric tolerances. These tools provide real-time feedback and detailed reports, enabling operators to make immediate adjustments if deviations are detected. Rigorous calibration routines ensure that machines maintain their accuracy over time, preventing drift that could compromise quality.
In addition to automated inspections, human expertise plays a vital role. Skilled technicians visually examine critical features, especially those that require nuanced judgment, such as surface textures or micro-features. Combining automated and manual inspection ensures comprehensive quality control.
Process control methodologies such as Statistical Process Control (SPC) are used to monitor consistency across batches. Data collected from inspections feed into continuous improvement initiatives, helping identify sources of variability and implement corrective actions. This systematic approach minimizes defects and waste, leading to cost savings and higher client satisfaction.
Material traceability is another crucial factor, especially in regulated industries like aerospace and medical. Every batch of raw material is documented, and parts are identified through serial numbers or barcodes, ensuring full traceability for audits or recalls.
Furthermore, digital documentation and certifications accompany each order, providing transparency and confidence to clients worldwide. Many Chinese CNC machining companies also adopt industry standards such as AS9100, ISO 13485, or ISO 9001, aligning with international quality expectations.
In conclusion, rigorous quality management, state-of-the-art inspection tools, and experienced personnel combine to ensure that high-precision CNC parts meet the highest standards of accuracy. This unwavering commitment to quality is essential for critical applications where failure is not an option.
## How Custom CNC Machining Supports High-Performance and Specialized Applications
Custom CNC machining is indispensable for high-performance applications requiring tailored solutions that standard manufacturing methods cannot provide. Whether it's aerospace components that demand lightweight, durable materials or medical implants with precise biocompatible surfaces, custom machining fulfills these specialized needs.
The flexibility of CNC technology allows for the production of complex geometries, micro-features, and multi-material assemblies. Custom fixturing and tooling are designed to accommodate unique part shapes, enabling the production of highly specialized components. This capability supports innovation in product design, functionality, and weight reduction—crucial factors in aerospace, automotive, and sports equipment.
In high-performance sectors, parts often operate under extreme conditions—high temperatures, mechanical stresses, or corrosive environments. Custom CNC solutions enable the use of advanced materials like titanium alloys, composites, and ceramics, which are machined with precision to ensure performance and longevity. The ability to work with such materials broadens the scope for innovative engineering solutions.
Moreover, custom CNC processes can incorporate features like micro-structuring or surface treatments—such as coatings or texturing—to enhance properties like friction, wear resistance, or fluid dynamics. These enhancements are vital for specialized applications like turbine blades or biomedical devices.
The ability to produce prototypes rapidly accelerates development cycles, allowing designers to test and refine their ideas efficiently. Small batch production or one-off custom parts become feasible, supporting a wide range of research, development, and production activities.
Ultimately, custom CNC machining empowers industries to push technological boundaries by providing tailored, precise, and reliable components that meet their unique performance criteria. This adaptability ensures that high-performance applications are not limited by manufacturing constraints, fostering continuous innovation.
## The Role of Skilled Operators and Modern Equipment in Complex Part Production
The production of complex parts relies heavily on the synergy between skilled operators and state-of-the-art equipment. Modern CNC machines—equipped with multi-axis capabilities, advanced controls, and automation systems—are essential, but their full potential is unlocked through the expertise of experienced personnel.
Skilled operators interpret complex design specifications, select appropriate tooling, and fine-tune machine parameters to optimize machining processes. Their practical knowledge helps prevent issues such as tool breakage, inaccuracies, or surface imperfections, especially when working with high-value materials or micro-features.
Modern equipment, such as 5-axis machining centers, high-speed spindles, and precision measurement systems, enable the production of intricate geometries with high accuracy. These advanced machines often incorporate automation features, enabling continuous operation and reducing human error. Their precision control systems monitor machining conditions and make real-time adjustments, ensuring consistent quality.
Training and continuous education are vital. Operators must stay abreast of technological advancements, new materials, and best practices. Many leading Chinese CNC manufacturers invest heavily in workforce development, recognizing that mastery over complex manufacturing processes requires a combination of technical skill and experience.
Maintenance and calibration of equipment also play critical roles. Well-maintained machines deliver consistent results, while regular calibrations ensure that tolerances are maintained over time. This reliability is essential when manufacturing parts with tight specifications.
In summary, the combination of modern machinery and highly skilled operators is fundamental to achieving the high standards demanded by complex part production. This partnership guarantees precision, efficiency, and quality—cornerstones of successful high-tech manufacturing.
## Benefits of Choosing a Chinese CNC Machining Manufacturer for International Projects
Chinese CNC machining manufacturers have gained recognition globally for their advanced capabilities, competitive pricing, and comprehensive service offerings. For international clients, partnering with a Chinese provider offers numerous strategic advantages, especially in demanding high-precision, complex part production.
One primary benefit is cost competitiveness. China’s manufacturing ecosystem allows for high-volume production with lower labor and material costs, translating into significant savings without compromising quality. This affordability makes it feasible for companies worldwide to produce high-value parts at scale.
In addition, China boasts a vast ecosystem of modern CNC facilities equipped with multi-axis machines, advanced inspection tools, and automation systems. Many manufacturers adhere to international standards like ISO 9001, ensuring quality and consistency. Their capacity to handle complex, custom-designed parts aligns well with the needs of high-tech industries.
The ability to customize production processes, rapid prototyping, and flexible batch sizes provides clients with agility. Whether they require one-off prototypes or large production runs, Chinese CNC companies can adapt quickly and deliver within tight timeframes.
Furthermore, many Chinese manufacturers are experienced in working with international clients, offering multilingual communication, transparent project management, and comprehensive after-sales support. Their expertise in handling sensitive projects ensures confidentiality and compliance with industry standards.
Lastly, strategic geographic positioning and investment in logistics infrastructure enable efficient shipping worldwide. Clients benefit from timely delivery and reduced lead times, critical for maintaining competitive advantages.
Partnering with a reliable Chinese CNC machining manufacturer thus combines technical excellence with economic benefits, supporting the successful execution of complex, high-precision projects across borders.
## Future Trends in CNC Machining: Innovations for Complex and Precise Part Production
The future of CNC machining is poised for continued innovation, driven by technological advancements and evolving industry demands. Trends such as Industry 4.0, artificial intelligence, and additive manufacturing are shaping the way complex and precise parts are produced.
Smart manufacturing, enabled by IoT sensors and real-time data analytics, will allow for predictive maintenance and process optimization. This results in higher precision, reduced downtime, and improved yield. For example, machine learning algorithms can analyze machining data to suggest optimal parameters or foresee tool wear before it impacts quality.
Additive manufacturing integration with CNC machining is opening new possibilities for complex geometries and multi-material components. Hybrid processes that combine subtractive and additive techniques enable manufacturing of parts with internal channels, intricate structures, or embedded features previously impossible to produce.
Advances in robotics and automation will further enhance efficiency and repeatability. Fully automated production cells with minimal human intervention will handle complex tasks, ensuring consistent high quality even in high-volume scenarios.
Materials science will also evolve, with the development of new composites and alloys tailored for specific high-performance applications. CNC systems will adapt to these materials, requiring sophisticated tooling and process adjustments.
Digital twins and virtual simulation will become standard practice, allowing engineers to model and optimize manufacturing workflows before actual production. This reduces errors, shortens development cycles, and ensures compliance with stringent standards.
Overall, innovation in CNC machining promises to push the boundaries of complexity and precision, supporting industries that demand cutting-edge components and enabling new levels of performance and miniaturization.
---
##
As manufacturing technology continues to evolve, the role of expert CNC machining services becomes ever more critical. From handling complex geometries and high-precision tolerances to working with diverse materials and innovative solutions, these services underpin the progress of high-tech industries worldwide. Chinese manufacturers, with their vast capacity, advanced equipment, and experienced workforce, are well-positioned to meet the growing global demand for sophisticated, custom-engineered parts. Embracing future trends like automation, AI, and hybrid manufacturing will only enhance their capabilities further. Ultimately, investing in expert CNC machining ensures that innovative designs are realized with accuracy, quality, and efficiency—driving forward technological advancements across the globe.