High-Precision CNC Machining for Cold Heading and Fastener Components
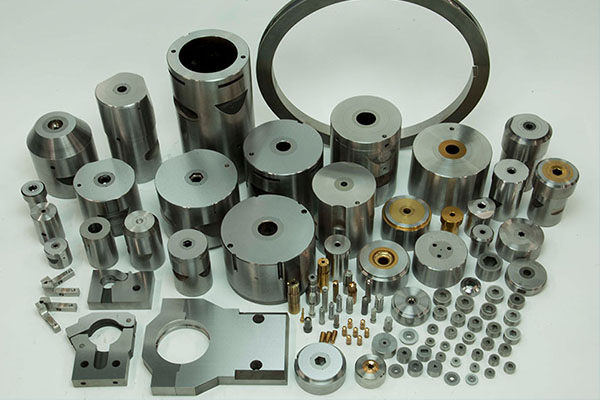
In today’s fast-paced manufacturing landscape, the demand for high-precision components has surged across various sectors, especially in cold heading and fastener production. These components are vital for ensuring the structural integrity, durability, and reliability of countless products—from automotive and aerospace to construction and electronics. Achieving the tight tolerances and intricate geometries required for such applications necessitates advanced CNC machining capabilities. This article explores the growing need for precision in cold heading and fastener components, the challenges faced, the materials utilized, and the cutting-edge CNC solutions that empower manufacturers to deliver excellence. Whether you’re sourcing custom fasteners or specialized cold-formed parts, understanding these aspects is key to selecting the right machining partner for your project. Let’s dive into the world of high-precision CNC machining tailored for cold heading and fastener components.===
The Growing Demand for Precision Components in Cold Heading and Fasteners
The modern manufacturing landscape demands components that meet exacting specifications with consistency and reliability. Cold heading and fastener components are integral parts of countless assemblies, from tiny electronic connectors to massive structural bolts. As industries such as automotive, aerospace, infrastructure, and electronics push for higher performance and safety standards, the need for precision manufacturing has intensified.
Customers now require fasteners with extremely tight tolerances—often within thousandths of a millimeter—to ensure proper fit, function, and longevity. Precision components also minimize assembly time and reduce the risk of failure, saving costs and enhancing product quality. Advances in design complexity, driven by innovations in engineering, have further increased the demand for CNC machining processes capable of producing intricate shapes and micro-scale features.
Furthermore, regulatory standards and certification processes have become more stringent, necessitating consistent quality control and traceability. CNC machining, with its ability to deliver high accuracy and repeatability, has become the backbone of modern cold heading and fastener manufacturing. As global supply chains evolve, the ability to produce high-precision parts efficiently and at scale remains a key competitive advantage.
In addition, the growth of automation and Industry 4.0 concepts has pushed for smarter manufacturing solutions. CNC machines equipped with real-time monitoring, adaptive controls, and advanced inspection systems ensure that each component adheres strictly to design specifications. This technological integration not only meets customer demands but also drives innovation in product design and material utilization.
The increasing adoption of lightweight materials and high-performance alloys further complicates manufacturing processes. These materials often require specialized machining techniques and tool technology to achieve desired standards. As a result, manufacturers investing in high-precision CNC machining are better positioned to respond to market trends and customer needs.
In summary, the rising demand for precision components in cold heading and fastener industries reflects a broader shift towards high-quality, reliable, and cost-effective manufacturing solutions that meet stringent industry standards. CNC machining plays a pivotal role in fulfilling these requirements, enabling the production of complex, high-tolerance parts at scale.
Key Challenges in High-Precision CNC Machining for Fastener Parts
Despite the clear advantages, high-precision CNC machining of fastener components presents several significant challenges that manufacturers must overcome. Understanding these obstacles is crucial for implementing effective solutions and maintaining competitive edge.
One primary challenge is achieving and maintaining extremely tight tolerances. Fastener components often require dimensions within ±0.01 mm or better, demanding meticulous machine calibration, stable machining environments, and precise tool control. Variations due to thermal expansion, tool wear, or machine vibrations can compromise accuracy, necessitating advanced control systems and frequent calibration.
Material selection adds another layer of complexity. Many fastener parts are made from high-strength alloys such as stainless steel, titanium, or alloy steels, which are difficult to machine due to their hardness and toughness. These materials can cause accelerated tool wear, increased cutting forces, and potential deformation, requiring specialized tooling and optimized cutting parameters.
Surface finish quality also presents a challenge. Many applications demand smooth, burr-free surfaces to ensure proper assembly and corrosion resistance. Achieving this consistency often requires fine-tuned machining processes, multiple passes, or secondary finishing, all of which can impact productivity.
Additionally, complex geometries and micro-features pose design and manufacturing hurdles. CNC machines need to be capable of executing intricate cuts with high accuracy, including threading, knurling, or undercuts. This may involve the use of multi-axis machines, specialized tooling, or customized fixturing.
Process stability and repeatability are vital for large-scale production. Variations in material batches, environmental conditions, or machine performance can lead to discrepancies between batches. Implementing rigorous quality control measures, such as in-line inspection and statistical process control (SPC), becomes essential.
Furthermore, manufacturing efficiency must be balanced with precision. High-precision machining can be time-consuming and costly, especially when working with complex or hard materials. Striking the right balance involves optimizing tool paths, feed rates, and machining sequences.
The integration of automation and robotics can help address some of these challenges by reducing human error and increasing consistency. However, this requires significant initial investment and expertise.
Finally, compliance with industry standards such as ISO, ASME, or ANSI requires comprehensive documentation, traceability, and quality management systems. Ensuring that each component meets these standards adds another layer of complexity but is essential for customer confidence and certification.
Overcoming these challenges demands a combination of advanced machine technology, skilled personnel, optimized processes, and rigorous quality control. Manufacturers who master these aspects can deliver high-precision cold heading and fastener components that meet even the most demanding specifications.
Essential Materials for Cold Heading and Fastener Component Manufacturing
The choice of material is fundamental to the success of cold heading and fastener component manufacturing. Different materials offer various advantages in strength, corrosion resistance, machinability, and cost. Understanding their characteristics helps in selecting the most appropriate material for specific applications.
Carbon Steel is widely used for fasteners due to its excellent strength-to-cost ratio. It is easily machinable and can be heat-treated to improve hardness and durability. However, it is susceptible to corrosion if not properly coated or treated. Common grades include 1018 and 1045.
Stainless Steel offers superior corrosion resistance, making it ideal for applications exposed to moisture or chemicals. Grades such as 304 and 316 are popular choices. Although more challenging to machine due to their hardness and tendency to work-harden, advanced CNC techniques and specialized tooling enable high-precision processing.
Titanium Alloys are prized for their exceptional strength-to-weight ratio and corrosion resistance. They are commonly used in aerospace, medical, and high-performance automotive fasteners. Titanium’s toughness and low thermal conductivity require carefully controlled machining parameters to prevent tool wear and deformation.
Alloy Steels like 4140 or 4340 combine strength, toughness, and wear resistance. They are often used for high-stress fasteners in structural or machinery applications. Their machinability can be improved through heat treatment, but they demand robust tooling and precise process control.
Brass and Copper are favored for electrical and decorative fasteners due to their excellent electrical conductivity and aesthetic appeal. They are relatively easy to machine and are resistant to corrosion but lack the strength of steel or titanium.
Nickel Alloys such as Inconel are used in extreme environments where high temperature and corrosion resistance are required. These materials are challenging to machine and often require specialized tools and cutting fluids to achieve high precision.
High-Performance Polymers like PEEK or PTFE are increasingly used for specialized fasteners in electronics or chemical industries. They offer excellent chemical resistance and low friction but have limited load-bearing capacity.
Material selection influences not only the machining process but also the final performance of the component. Factors like thermal expansion, surface finish, and mechanical properties must be aligned with the application requirements.
In high-precision CNC machining, it is essential to choose materials that balance machinability with functionality. Proper selection ensures efficient manufacturing, minimal tool wear, and optimal component performance, especially in critical applications like aerospace or medical devices.
By leveraging advanced tooling, optimized cutting parameters, and precise process control, manufacturers can successfully machine even the most challenging materials to tight tolerances, ensuring each component meets rigorous industry standards.
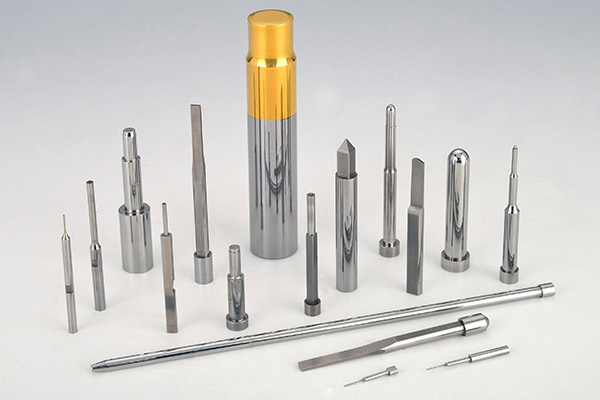
Customized machining of high-precision parts in the field of cold heading and fasteners
Our Advanced CNC Machining Capabilities: Tolerance, Equipment, and Inspection
At the core of delivering high-precision cold heading and fastener components is our advanced CNC machining capability. We utilize state-of-the-art equipment and rigorous quality control processes to ensure each part meets the most demanding specifications.
Our machining centers are equipped with multi-axis CNC machines, including 3,4, and 5-axis configurations, enabling complex geometries and micro-features to be produced with exceptional accuracy. These machines incorporate high-speed spindles, precision ball screws, and linear guides to minimize vibrations and maximize positional accuracy.
Tolerance control is a priority; we routinely achieve dimensional accuracies within ±0.005 mm for critical features. Our precision tools, combined with real-time machine feedback systems, maintain process stability and reduce variability. Adaptive machining strategies allow for on-the-fly adjustments, compensating for tool wear or material inconsistencies.
We employ a comprehensive suite of inspection and measurement equipment, including coordinate measuring machines (CMM), optical comparators, and surface profilometers. These tools verify dimensions, surface finishes, and microstructures to ensure compliance with customer specifications and industry standards.
Our process development team optimizes cutting parameters such as feed rates, spindle speeds, and coolant application to balance productivity with precision. We also utilize specialized tooling and fixturing designed for each component to guarantee stability and repeatability during machining.
Material handling is streamlined with automated loading and unloading systems, reducing human error and contamination risks. This automation accelerates production cycles while maintaining strict quality standards.
To ensure traceability, each batch of components is documented with detailed inspection reports, including measurement data, material certificates, and process logs. Our quality management system aligns with ISO 9001 standards, reinforcing our commitment to consistent excellence.
Furthermore, we continually invest in staff training and process upgrades. Our engineers and technicians stay abreast of the latest advancements in CNC technology, enabling us to tackle the most challenging projects with confidence.
By combining cutting-edge equipment, meticulous process control, and rigorous inspection protocols, we provide high-precision CNC machining services that meet the stringent demands of cold heading and fastener industries. Our capabilities ensure you receive parts that perform reliably under the most rigorous conditions.
Common Components and Their Applications in Modern Industries
High-precision CNC machining for cold heading and fastener components encompasses a wide array of parts, each serving critical functions across numerous industries. Understanding these common components and their typical applications highlights the importance of precision in ensuring safety, performance, and longevity.
Bolts and Screws are perhaps the most ubiquitous fasteners, used extensively in automotive, construction, and machinery assembly. Precision-machined threads and accurate dimensions are vital for load-bearing capacity and secure fastening. High-tolerance screws also find applications in electronics and aerospace, where miniaturization is key.
Nuts and Washers complement bolts and screws, providing secure fastening solutions. Their manufacturing demands tight tolerance control to ensure proper fit and torque transfer. Specialty washers, such as lock washers or insulators, cater to specific functional needs.
Anchors and Rivets are critical in structural applications. Precision machining ensures proper expansion, load distribution, and corrosion resistance. They are used in bridges, aircraft, and electronic enclosures.
Cold-formed Pins and Dowel Pins serve as alignment and fastening components in machinery and assemblies. Their high precision ensures accurate positioning and smooth operation in engines, gearboxes, and precision instruments.
Threaded Inserts are used to repair stripped threads or add strong attachment points in softer materials. CNC machining ensures precise dimensions for reliable performance.
Specialized Fasteners such as eye bolts, turnbuckles, and toggle clamps are essential in mechanical linkages, rigging, and adjustable systems. High-precision manufacturing guarantees their strength and functionality.
In aerospace, components such as fastener rings, high-strength rivets, and micro-fasteners are manufactured with extreme precision to meet safety standards. These parts often require certification and traceability.
In electronics, miniaturized fasteners and components are crucial for compact device assembly. Precision CNC machining allows for the production of tiny, complex parts with consistent quality.
Medical applications also benefit from high-precision fasteners, including implants and surgical instrument components, where tolerances and surface quality are critical for safety and effectiveness.
In the automotive industry, high-strength fasteners contribute to crashworthiness, vibration damping, and assembly efficiency. Their precise manufacturing directly impacts vehicle safety and performance.
Overall, the broad spectrum of components produced through high-precision CNC machining underscores the industry’s reliance on accuracy, material integrity, and quality control. These components form the backbone of modern machinery, transportation, electronics, and infrastructure, emphasizing the importance of advanced manufacturing capabilities.
Successful Projects Demonstrating Our CNC Machining Expertise
Our experience in high-precision CNC machining for cold heading and fastener components is reflected in a portfolio of successful projects across various industries. These case studies highlight our technical expertise, commitment to quality, and ability to meet challenging specifications.
One notable project involved the production of aerospace-grade titanium fasteners. The client required components with tolerances within ±0.005 mm and surface finishes adhering to aerospace standards. We employed 5-axis CNC centers with custom-fixturing and specialized cutting tools. Rigorous inspection using CMM ensured each batch met the strict industry criteria. The project was completed on schedule, contributing to the client’s certification process and product reliability.
Another example is a large-scale automotive fastener supplier seeking to optimize their manufacturing process for high-volume stainless steel bolts. Our team developed a tailored CNC machining solution integrating automation and inline inspection. The result was a significant reduction in cycle time and defect rates, with consistent parts within ±0.01 mm tolerances. This success enhanced the client’s competitiveness and product quality.
In the electronics sector, we manufactured miniaturized threaded inserts for high-density circuit boards. The challenge was achieving micro-scale precision in complex geometries. Using high-precision 4-axis machines and advanced tooling, we delivered inserts with perfect thread accuracy, ensuring seamless integration into electronic devices.
A medical device manufacturer required customized surgical instrument components made from corrosion-resistant alloys. Our team utilized synchronized multi-axis machining and strict quality control protocols to produce parts with exceptional surface finishes and micro-accuracy. Compliance with medical standards and certifications was achieved, supporting the client’s regulatory approval.
Furthermore, we collaborated with a construction hardware company to produce high-strength anchors and bolts for infrastructure projects. The components, machined from alloy steels, demonstrated excellent mechanical properties, dimensional stability, and corrosion resistance, ensuring safety and longevity in demanding environments.
Each project exemplifies our ability to adapt advanced CNC technology, optimize processes, and uphold high standards of quality and precision. These successes not only demonstrate our technical competency but also underscore our dedication to customer satisfaction and long-term partnerships.
If you are seeking a reliable partner for your cold heading and fastener component manufacturing needs, contact us today. We are ready to deliver custom solutions that meet your specifications and exceed expectations.