High-Precision CNC Machining for Global Clients: Customization and Expertise
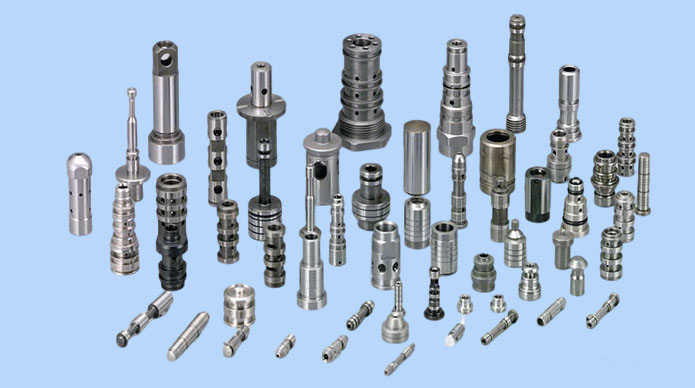
===INTRO:
In today’s highly competitive global manufacturing landscape, high-precision CNC machining has become a cornerstone for industries demanding exceptional accuracy and customization. From aerospace to medical devices, clients around the world rely on advanced CNC solutions to meet their stringent specifications. Chinese CNC machining manufacturers have emerged as reliable partners, offering tailored services that emphasize craftsmanship, material expertise, and innovative problem-solving. This article explores the core principles of high-precision CNC machining for international clients, highlighting customization, technical mastery, and case studies that demonstrate how complexities are effectively addressed. Whether dealing with complex geometries or challenging materials, these experts deliver results that meet and often exceed expectations. Let’s delve into how global clients benefit from China’s CNC manufacturing capabilities rooted in experience, precision, and innovation.===
## High-Precision CNC Machining: Meeting Global Client Demands
High-precision CNC machining is essential in producing components with tight tolerances, intricate details, and superior surface finishes. For international clients, the demand is not just for quality but also for consistency across large production runs. Chinese CNC manufacturers have responded by investing heavily in state-of-the-art equipment, including multi-axis machines capable of complex operations. These facilities are equipped to handle parts with tolerances within microns, guaranteeing repeatability and reliability.
Furthermore, strict quality control protocols are integral to meeting global standards such as ISO and ASTM. These manufacturers employ advanced inspection tools like coordinate measuring machines (CMM) and laser scanners to verify each component’s dimensional accuracy. Additionally, their proximity to raw material suppliers ensures a steady supply chain, minimizing delays.
The ability to swiftly adapt to new designs or modifications is a key asset. Clients can submit digital models—such as CAD files—and receive prototypes or mass-produced parts with minimal turnaround time. This flexibility is crucial for industries like aerospace, where design iterations are frequent. Overall, high-precision CNC machining from China effectively bridges the gap between innovative engineering and reliable manufacturing for global markets.
Moreover, the scalability of these services allows clients to start with small batches for testing before scaling up to mass production, ensuring risk mitigation. The integration of automation and smart manufacturing systems further enhances precision and efficiency, making Chinese CNC machining a trusted partner worldwide.
Finally, the comprehensive service ecosystem—ranging from design consultation to post-processing—ensures that clients' specifications are fully realized. This holistic approach guarantees that each component aligns exactly with project requirements, reinforcing confidence in Chinese manufacturing capabilities.
In essence, high-precision CNC machining now delivers more than just parts; it provides peace of mind for global clients seeking consistent, high-quality, and customized solutions. The combination of advanced technology, rigorous quality assurance, and customer-centric flexibility embodies the future of precision manufacturing.
## Custom CNC Solutions Tailored to Unique Customer Specifications
Every product design carries its unique requirements, making customization a vital aspect of modern CNC machining. Chinese manufacturers excel in translating complex customer specifications into tangible, precise components. They work closely with clients from the initial concept stage through to final delivery, ensuring every detail is meticulously executed.
Utilizing sophisticated CAD/CAM software, engineers analyze and optimize designs for manufacturability. They identify potential issues early, such as tool accessibility or material constraints, and suggest modifications without compromising functionality. This collaborative approach results in cost-effective and efficient machining processes tailored to the client's project.
Custom fixtures and jigs are often developed to support complex geometries, ensuring stability and accuracy during production. Additionally, flexible tooling systems allow for quick adjustments when design changes occur, reducing lead times. For high-precision, low-volume runs, these custom setups eliminate common issues like misalignment or vibration, which can compromise quality.
Material selection is also a key part of customization. Clients may require specific alloys, composites, or exotic materials that demand specialized machining techniques. Chinese manufacturers leverage their experience to select appropriate cutting tools and parameters, maximizing material performance and lifespan.
Quality control procedures are customized according to the project’s critical requirements. For instance, aerospace parts may require multi-stage inspections, while medical components necessitate strict biocompatibility standards. This attention to detail ensures that each part meets the original specifications precisely.
Customization extends beyond the machining process itself, encompassing surface treatments, coatings, and finishing techniques. Whether polishing, anodizing, or coating, these processes are integrated seamlessly into the overall project plan.
By offering comprehensive, tailored solutions, Chinese CNC manufacturers enable clients to achieve their unique product visions. This high level of personalization and technical adaptation is what sets them apart in a competitive global market.
In summary, bespoke CNC machining services empower clients to transform complex ideas into high-precision, manufacturable components. The ability to adapt processes and materials to specific needs underscores the strength of Chinese manufacturing in serving diverse industries worldwide.
## Expertise in High-Complexity Parts for Advanced Industries
Handling high-complexity components is a true test of a CNC machine shop’s expertise. Industries such as aerospace, defense, medical, and semiconductor manufacturing demand parts with intricate geometries, micro-features, and extremely tight tolerances. Chinese manufacturers have cultivated a deep knowledge base and technical skill set to meet these rigorous standards.
Advanced CNC machines with multi-axis capabilities enable the production of complex shapes that would be impossible with traditional methods. These include tapered holes, curved surfaces, internal cavities, and fine features that require precise toolpath programming. Skilled programmers and engineers develop optimized strategies to achieve these geometries efficiently.
Expertise in micro-machining is particularly crucial for industries like medical devices and electronics, where tiny, detailed features are commonplace. Chinese manufacturers utilize high-precision spindles, laser measurement, and advanced cutting tools to produce components with micron-level accuracy. Such precision ensures functionality and safety in critical applications.
Manufacturers also possess extensive experience in difficult-to-machine materials such as titanium, Inconel, ceramics, and composites. These materials often demand specialized cutting techniques, coolant applications, and tool materials. The ability to machine these challenging substances confidently opens opportunities for high-end, performance-critical parts.
Safety and compliance are integral when manufacturing components for aerospace or medical use. Chinese experts are familiar with international standards and perform rigorous inspections, including non-destructive testing, to verify structural integrity and dimensional accuracy.
Training and continuous skill development are core to maintaining expertise. Many Chinese CNC shops invest in ongoing education, certifications, and technology upgrades, ensuring their teams stay ahead of industry demands. This commitment translates into higher quality outputs for complex projects.
Case studies showcase their capability: producing turbine blades with complex aerodynamics, micro-holes for medical implants, or precision connectors for semiconductors. These successes demonstrate their mastery over high-precision, high-complexity manufacturing.
In essence, their ability to produce complex parts reliably and consistently makes Chinese CNC manufacturers indispensable partners for advanced industries seeking innovation and excellence.
## Material Selection and Utilization in Precision CNC Manufacturing
Material choice significantly influences the performance, durability, and machinability of precision components. Chinese CNC manufacturers possess extensive expertise in selecting and working with a wide range of materials tailored to client specifications and application environments.
For aerospace and defense, high-performance alloys such as titanium, Inconel, and stainless steels are common due to their strength-to-weight ratios and corrosion resistance. Machining these materials requires specialized tools and cooling techniques, which experienced Chinese manufacturers have mastered over years of practice.
Medical devices often involve biocompatible materials like surgical stainless steel, titanium, or plastics like PEEK. These materials demand strict adherence to cleanliness and surface quality standards. Precision machining ensures smooth finishes critical for biocompatibility and functionality.
Electronics and semiconductor industries utilize materials such as ceramics, quartz, and specialty plastics. Machining these substrates involves controlling thermal expansion and preventing micro-cracking, skills that Chinese experts have developed through extensive technical know-how.
Exotic materials, like hardened alloys or composite fibers, are increasingly used for lightweight yet durable parts. Their unique properties pose challenges, but customized tooling and process parameters enable successful machining without compromising material integrity.
Recycling and sustainability considerations are also integrated into material management. Chinese manufacturers optimize cutting parameters to minimize waste and extend tool life, which is essential when working with costly or rare materials.
Material handling protocols are strictly followed to prevent contamination, especially for sensitive applications like medical implants or aerospace components. Cleanroom environments and sealed transport systems maintain quality integrity throughout the process.
In addition, surface treatments—such as anodizing, coating, or polishing—are tailored to material specifications, enhancing corrosion resistance, wear properties, or aesthetic appeal.
By harnessing deep material expertise, Chinese CNC shops deliver components that meet or exceed industry standards for performance and reliability. Their ability to work with diverse and advanced materials enhances their appeal as global manufacturing partners.
## Overcoming Challenging Machining Tasks with Proven Techniques
High-precision machining often involves tackling difficult tasks such as machining hard-to-cut materials, achieving perfect surface finishes, or manufacturing parts with complex internal geometries. Chinese manufacturers employ proven techniques to address these challenges effectively.
One such technique is high-pressure coolant delivery, which aids in efficient chip removal and reduces heat buildup during machining of tough alloys like titanium or Inconel. This prevents tool wear and ensures dimensional stability.
Utilizing coated cutting tools, such as TiAlN or diamond-coated bits, extends tool life and improves surface finish, especially when working with abrasive materials. These coatings reduce friction and thermal transfer, allowing for more aggressive machining parameters.
Adaptive feed and speed strategies are implemented to optimize cutting conditions dynamically. This minimizes tool deflection, vibrations, and potential inaccuracies, even on challenging geometries.
Advanced fixturing and clamping systems are designed to securely hold complex parts, preventing movement during machining. Custom jigs and fixtures are often developed in-house to accommodate unique shapes and ensure stability.
For internal features or micro-machining, ultrasonic-assisted machining or laser ablation techniques are employed. These methods can achieve fine details without damaging surrounding material, opening new possibilities for intricate designs.
Finite element analysis (FEA) simulation helps predict tool behavior, stress points, and deformation before actual machining, allowing engineers to refine processes and prevent costly errors.
Post-machining processes such as precision grinding, polishing, and surface treatments are integrated to rectify any imperfections and achieve desired surface qualities.
The combination of these proven techniques enables Chinese CNC manufacturers to consistently produce high-quality parts even under demanding circumstances, reinforcing their reputation for excellence.
Overall, their mastery of overcoming machining challenges translates into higher success rates, reduced lead times, and superior product quality for international clients facing complex manufacturing tasks.
## Case Studies: Solving Global Classic CNC Machining Problems
Real-world cases illustrate how Chinese CNC manufacturers resolve typical and complex machining dilemmas faced by global clients. These examples highlight their technical proficiency, problem-solving capabilities, and quality standards.
One notable case involved manufacturing aerospace turbine blades with complex aerodynamics and tight tolerances. By employing multi-axis machining, customized fixturing, and advanced inspection, the manufacturer achieved precision within microns, ensuring optimal performance and safety.
In another project, a medical device firm required micro-scale components with intricate internal channels. Through ultrasonic-assisted micro-machining and meticulous process control, the Chinese team delivered parts with flawless internal geometries and excellent surface finishes, meeting all biocompatibility standards.
A challenging case involved machining Inconel parts for the oil and gas industry, where high hardness and thermal stability pose difficulties. The manufacturer optimized cutting parameters, employed high-pressure coolant, and used coated tools, resulting in high-quality components delivered on tight schedules.
For electronics sector clients, a project involved precision ceramic components with micro-holes. The solution utilized laser micro-machining combined with post-process polishing, achieving the required specifications without inducing micro-cracks.
In the defense industry, complex armor system parts with high-dimensional accuracy and surface integrity were produced by integrating FEA simulations, precision fixturing, and multi-stage inspections. The outcome was components that met military standards for durability and precision.
These case studies exemplify a problem-solving mindset rooted in technical expertise and innovative approaches. They demonstrate how Chinese CNC manufacturers adapt to diverse challenges across industries and applications.
Such successful projects inspire confidence among international clients, reinforcing the reputation of Chinese high-precision CNC machining as a reliable and capable partner for solving complex manufacturing problems.
## The Importance of Skilled Experience in High-Precision Manufacturing
Experience remains the cornerstone of excellence in high-precision CNC machining. Skilled operators, programmers, and engineers bring invaluable insights that cannot be replaced solely by automation or software.
Veteran craftsmen understand the nuances of different materials, cutting tools, and machine behaviors. Their intuition guides process adjustments for optimal results, especially in tricky tasks like micro-machining or working with exotic materials.
Experienced programming teams develop efficient toolpaths that minimize cycle times while maximizing accuracy. They anticipate potential issues such as tool deflection, vibration, or thermal effects, preventing costly errors before production begins.
Continuous training and exposure to cutting-edge technologies keep the workforce sharp and adaptable. Chinese manufacturers invest in certifications, workshops, and industry collaborations, ensuring their staff remains at the forefront of precision manufacturing.
Knowledge transfer across teams fosters a culture of quality and innovation. Senior experts mentor junior operators, passing down best practices and practical skills that are vital for tackling high-complexity parts.
Quality assurance is deeply rooted in experience. Seasoned inspectors recognize subtle deviations, micro-cracks, or surface imperfections that automated systems might overlook. Their judgment ensures only parts meeting stringent standards reach clients.
Moreover, experience allows manufacturers to develop proprietary techniques and customized solutions tailored to specific challenges encountered in high-precision production.
Client trust is reinforced when they see that their projects are handled by professionals who possess a deep understanding of the intricacies involved. This confidence is crucial for long-term partnerships, especially in industries where failure is not an option.
In conclusion, expertise grounded in years of hands-on experience elevates Chinese CNC manufacturing from good to exceptional, creating a competitive edge in the global high-precision market.
## Customization Processes: From Design to Final Product Delivery
The journey from initial concept to finished component involves multiple stages, each emphasizing precision and client satisfaction. Chinese CNC manufacturers adopt a systematic approach to ensure seamless customization at every step.
Starting with detailed communication, clients submit digital design files, which are analyzed by experienced engineers. They assess manufacturability, suggest improvements, and confirm material suitability, aligning expectations from the outset.
Design optimization incorporates considerations such as tool accessibility, machining sequences, and cost efficiency. This collaborative process ensures that the final design is both functional and feasible for high-precision production.
Prototyping follows, allowing clients to review samples and provide feedback. Rapid prototyping using CNC or additive manufacturing techniques accelerates testing and validation, enabling quick iterations.
Once the design is finalized, detailed process planning begins. Engineers select appropriate tools, cutting parameters, and fixturing solutions tailored to the part’s complexities and material properties.
Production is carried out in controlled environments, with continuous monitoring and in-process inspections to detect deviations early. Advanced measurement systems verify dimensions against tolerances, ensuring adherence to specifications.
Post-processing steps such as surface finishing, coating, or assembly are integrated into the workflow, finalizing the component’s functionality and aesthetics. Each step is meticulously documented for quality traceability.
The final inspection involves comprehensive testing, including CMM measurements, visual checks, and non-destructive testing if required. Documentation and certification accompany each batch, providing transparency and confidence.
Delivery logistics are also carefully managed, with packaging and customs compliance tailored to international standards. Manufacturers often offer just-in-time delivery options to meet clients’ supply chain needs.
Throughout this process, open communication and a customer-centric mindset ensure that expectations are met or exceeded. Customized solutions are not just about manufacturing parts but about building long-term trust and satisfaction with clients worldwide.
## Ensuring Quality and Accuracy in Complex CNC Components
Maintaining high quality and accuracy in complex CNC parts is a top priority for Chinese manufacturers serving global clients. This involves rigorous multi-stage inspection and quality assurance systems integrated into every process phase.
Initial quality checks include verifying raw materials and tooling before machining begins. Material certificates and incoming inspections prevent issues downstream. During production, in-process measurements detect deviations early, reducing scrap and rework.
Advanced inspection equipment such as coordinate measuring machines (CMM), optical comparators, and laser scanners are employed to validate complex geometries and tight tolerances. Data collected triggers immediate process adjustments if necessary.
Surface integrity is critical, especially for aerospace or medical components. Non-destructive testing methods, including ultrasonic or dye penetrant inspections, ensure internal and surface quality meet industry standards.
Traceability systems track each component’s manufacturing history, from raw material to final inspection. This accountability demonstrates compliance with international certifications like AS9100 or ISO 13485.
Additionally, continuous improvement practices, such as Six Sigma and lean manufacturing, optimize processes, reduce variability, and enhance overall quality. Employee training emphasizes attention to detail and adherence to strict protocols.
Client-specific quality requirements are incorporated into quality control plans, which are reviewed and approved before production. Customized inspection reports and certifications provide transparency and confidence.
Finally, after delivery, some manufacturers offer post-sales support and warranty services, ensuring the ongoing performance of high-precision parts in critical applications.
Through these comprehensive measures, Chinese CNC manufacturers guarantee that complex components are produced with unparalleled accuracy, reliability, and consistency, satisfying the most demanding international standards.
## Collaborating with International Clients for Optimal Results
Effective collaboration with global clients is vital for achieving precision manufacturing excellence. Chinese CNC manufacturers prioritize transparent communication, cultural understanding, and flexibility to align with client expectations.
Initially, detailed consultations clarify project scope, material preferences, tolerances, and delivery timelines. Digital tools facilitate real-time communication, allowing clients to review progress and provide feedback promptly.
Language barriers are mitigated through multilingual staff and comprehensive documentation, ensuring clarity and mutual understanding. Regular updates and virtual meetings maintain alignment throughout the production cycle.
Adapting to different time zones and working hours, manufacturers often implement flexible scheduling to accommodate client needs. This responsiveness shortens lead times and enhances customer satisfaction.
Quality standards and certifications are meticulously observed to meet diverse international requirements. Customized inspection reports and certifications are provided, demonstrating compliance and fostering trust.
Shared project management platforms enable transparent tracking of production status, inspection results, and logistics. This openness encourages collaborative problem-solving and continuous improvement.
Involving clients in prototype testing or design reviews allows for early detection of potential issues, saving time and costs in the long run. This cooperative approach results in parts that precisely match the intended application.
Post-delivery support, including technical assistance, spare parts, and maintenance advice, further strengthens client relationships. Chinese manufacturers often view these collaborations as long-term partnerships, not just transactional deals.
By emphasizing open communication, cultural sensitivity, and quality assurance, Chinese CNC manufacturers build lasting trust with international clients, delivering optimal results tailored to diverse industries worldwide.
## Innovative Approaches to Difficult Material Machining Challenges
Tackling difficult materials like titanium, ceramics, or composites requires innovative solutions. Chinese CNC manufacturers leverage cutting-edge technologies and creative techniques to overcome these challenges efficiently.
One approach involves the use of advanced cooling systems, such as high-pressure coolant or cryogenic cooling, to manage heat generated during machining. This prolongs tool life and maintains dimensional stability.
Specialized cutting tools with coatings like diamond or ceramic enhance wear resistance when machining abrasive materials. Custom tool geometries are designed to optimize chip removal and surface finish.
Ultrasonic-assisted machining combines high-frequency vibrations with traditional cutting, reducing cutting forces and improving surface quality on brittle or hard materials like ceramics and glass.
Additive manufacturing techniques are sometimes integrated with CNC machining, enabling the creation of complex internal features that are difficult to machine conventionally. This hybrid approach expands design possibilities.
Finite element analysis and simulation tools help predict machining behavior, allowing engineers to develop bespoke process parameters tailored to material-specific challenges and avoid issues like micro-cracking or deformation.
Collaboration with material suppliers provides insights into the optimal machining conditions for new or exotic materials, ensuring process stability and part integrity.
Post-processing techniques such as grinding, polishing, or chemical etching compensate for surface imperfections and enhance performance, especially for applications demanding high precision and surface quality.
These innovative approaches exemplify the ingenuity Chinese manufacturers apply to solve the toughest material machining problems, continually pushing the boundaries of what’s achievable in high-precision manufacturing.
## Building Trust Through Precision, Customization, and Expertise
Establishing trust with international clients hinges on consistently delivering high-quality, customized, and expertly manufactured parts. Chinese CNC manufacturers recognize that transparency, reliability, and technical excellence are fundamental to long-term relationships.
Precision is demonstrated through adherence to strict tolerances, thorough inspections, and certification compliance. Clients can rely on the consistent quality of parts, even for highly complex or demanding applications.
Customization capabilities allow clients to realize unique design visions, with the manufacturer acting as a collaborative partner rather than just a supplier. Flexibility in process adjustments and material selection reinforces this partnership.
Expertise accumulated over years of experience ensures that complex projects are handled with confidence and skill. Knowledge transfer and ongoing training further solidify their position as competent and innovative manufacturers.
Open communication channels, timely response, and proactive problem-solving foster a sense of partnership and mutual respect. Clients value transparency about production progress and quality control measures.
Investing in advanced technology, skilled personnel, and quality systems signals a genuine commitment to excellence. This investment builds credibility and reassures clients of the manufacturer’s capabilities.
Successful case studies, certifications, and client testimonials serve as proof points of reliability. Long-term collaborations are nurtured through consistent delivery and attentive customer service.
Ultimately, the combination of precision, customization, and experienced craftsmanship forms the foundation for trust that spans borders and industries. Chinese CNC manufacturers are increasingly recognized worldwide for their dedication to excellence in high-precision manufacturing.