High-Precision CNC Machining for Global Clients: Customization and Expertise
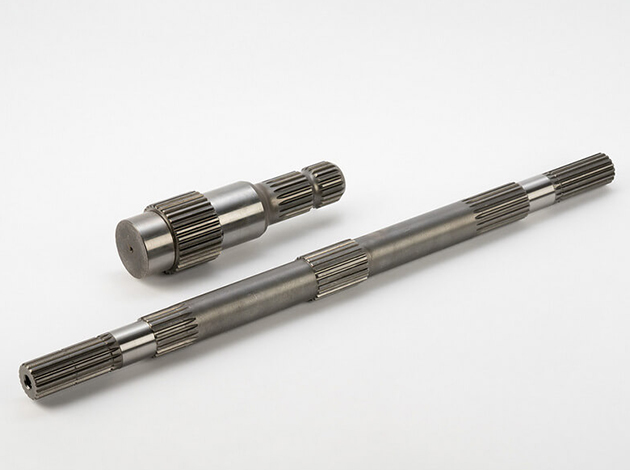
===INTRO:
In today's interconnected manufacturing landscape, high-precision CNC machining has become a critical service for global industries—from aerospace and medical devices to electronics and automotive sectors. As companies worldwide demand increasingly complex components, the need for customization, advanced techniques, and experienced craftsmanship has never been greater. Chinese CNC machining providers, such as those highlighted in the industry, now stand as vital partners for clients seeking reliable, high-quality, tailor-made solutions. This article explores how expert CNC manufacturers deliver precision, customization, and innovation across borders, ensuring clients worldwide receive components that meet the strictest standards of quality and complexity.
## High-Precision CNC Machining: Serving Global Clients with Expertise
High-precision CNC machining involves crafting components with extremely tight tolerances, often within microns, to meet exact specifications. For international clients, this means partnering with manufacturers who possess not only advanced equipment but also profound technical expertise. Such manufacturers employ state-of-the-art CNC centers capable of intricate multi-axis operations, ensuring that complex geometries are achieved with remarkable accuracy. This expertise extends beyond machinery—requiring a deep understanding of process optimization, material behavior, and quality control to consistently deliver parts that meet rigorous international standards.
Serving global clients introduces unique challenges, including variations in design expectations, material sourcing, and logistical considerations. Experienced Chinese CNC machining providers have adapted by developing extensive quality management systems, adhering to international certifications, and fostering cross-cultural communication. These efforts enable them to reliably translate detailed blueprints into tangible, high-quality components, regardless of geographic origin. The result is a seamless experience where clients’ ideas become precise, manufacturable realities, regardless of complexity or volume.

Moreover, high-precision CNC machining is essential in industries where failure is not an option. Medical implants, aerospace components, and high-performance electronics demand tolerances within microns. For these demanding applications, expertise isn’t just a bonus—it’s a necessity. By leveraging decades of experience and continuous technological upgrades, Chinese manufacturers now offer services that match or surpass global competitors, solidifying their role as trusted partners across continents.
The capacity for rapid prototyping, small-batch production, and mass manufacturing is built upon years of experience. Skilled technicians and engineers work collaboratively to troubleshoot potential issues early in the process, reducing time-to-market and ensuring reliability. Their comprehensive understanding of machining nuances ensures that even the most complex features—such as micro-holes, deep cavities, or intricate threading—are executed flawlessly.
In addition, responsive customer support and transparent communication are hallmarks of reputable Chinese CNC providers. These qualities help bridge cultural and language barriers, fostering trust among international clients. As a result, clients can confidently entrust their most challenging components to manufacturers capable of consistently achieving high precision and quality, regardless of geographical distance.
Finally, ongoing research and development play a crucial role. Chinese CNC manufacturers invest heavily in new tooling, software, and process innovations, staying ahead of industry trends. This continuous improvement cycle enables them to meet evolving client needs, particularly when high-precision requirements push the limits of current technology. The synergy of experience, technological prowess, and customer-centric service makes them invaluable partners for global industries.
## Customization by Design: Tailoring CNC Solutions to Client Needs
Customization is the cornerstone of high-precision CNC machining. Each client’s requirements are unique, whether dictated by functional demands, design intricacies, or material specifications. Leading Chinese CNC providers excel in translating complex blueprints into manufacturable parts through tailored solutions that respect every detail. This begins with comprehensive consultations, where engineers review drawings, discuss material options, and identify potential manufacturing challenges.
From there, the process involves meticulous planning—selecting suitable tooling, determining optimal machining parameters, and devising strategies to achieve tight tolerances. Custom fixtures and jigs are often designed to hold complex geometries securely, ensuring precision during multi-step processes. Advanced simulation software models machining sequences, helping to preempt issues such as tool deflection or thermal distortion, thereby reducing trial-and-error cycles.
Moreover, customization goes beyond just meeting design specifications; it encompasses considerations like surface treatment, coating, and finishing processes. Whether a client needs a specific surface roughness, corrosion resistance, or aesthetic appeal, Chinese CNC manufacturers accommodate these requirements within their workflows. This flexibility ensures that each component aligns perfectly with its intended application.
Material selection is also integral to customization. Different projects demand different raw materials—metals, alloys, or even composites. Experienced manufacturers advise clients on the best material choices based on mechanical properties, machinability, and environmental factors. Their understanding of diverse raw materials allows for optimized machining strategies, reducing waste and improving efficiency.
Communication plays a vital role in successful customization. Reputable Chinese CNC firms maintain clear dialogue with clients throughout the process—sharing progress updates, providing technical recommendations, and adjusting plans as needed. This collaborative approach ensures that the final product precisely matches the envisioned design, even when modifications are required mid-process.
Finally, the ability to handle small-batch or one-off production runs makes customization truly effective. Clients benefit from rapid prototyping and iterative testing, refining designs before mass production. This agile approach minimizes risks, reduces costs, and accelerates time-to-market, embodying the true spirit of tailored high-precision manufacturing.
## Tackling Complex Parts: Advanced CNC Techniques for Difficult Components
Manufacturing complex parts with high precision is a defining challenge in CNC machining. Such components often feature intricate geometries, micro-features, or tight internal spaces that demand sophisticated techniques. Chinese CNC manufacturers employ a suite of advanced methods—multi-axis machining, high-speed milling, and precise drilling—to efficiently produce these demanding components.
Multi-axis machining centers—such as 5-axis or even 7-axis machines—allow for continuous tool movement along multiple axes. This capability enables the machining of complex surfaces without repositioning the part, reducing setup times and increasing accuracy. For example, aerospace turbine blades with curved surfaces or medical implants with internal channels are fabricated with high precision using these advanced systems.
High-speed milling techniques are also vital for complex parts, especially when dealing with hard materials. These methods reduce cutting forces and thermal distortion, resulting in cleaner surfaces and tighter tolerances. Employing specialized tooling and coolant systems, Chinese CNC providers optimize cutting parameters to achieve smooth finishes even on the most challenging geometries.
For micro-scale features, micro-milling and laser ablation are employed. These methods facilitate the production of tiny holes, slots, and intricate textures, essential in electronics and medical devices. Additionally, wire EDM (Electrical Discharge Machining) complements CNC milling for achieving precise internal cuts in hard metals, ensuring complex internal features are accurately realized.
Managing difficult components also involves careful fixture design and clamping strategies to prevent deformation. Custom fixtures are crafted to hold parts securely during machining, especially for fragile or irregular shapes. This stability is crucial for maintaining tight tolerances and surface finishes.
Software integration plays an essential role in tackling complex parts. CAD/CAM systems enable programmers to simulate machining processes beforehand, identifying potential collisions and optimizing tool paths. This predictive approach minimizes errors, saves material, and shortens production cycles.
Finally, skilled operators are indispensable. Experienced technicians interpret complex designs, select suitable tools, and monitor machining parameters in real-time. Their expertise ensures that even the most intricate parts are produced flawlessly, demonstrating that advanced CNC techniques combined with seasoned craftsmanship are key to overcoming manufacturing hurdles.
## Material Mastery: Selecting & Working with Diverse Raw Materials
A fundamental aspect of high-precision CNC machining is material mastery. Different projects require specific raw materials—metals, alloys, or composites—that influence machinability, durability, and performance. Chinese CNC manufacturers boast extensive expertise in working with a broad spectrum of materials, ensuring optimal results tailored to client needs.
Metals like aluminum, stainless steel, titanium, and copper are common in high-precision parts. Aluminum offers excellent machinability and light weight, suitable for aerospace and electronics. Stainless steel provides corrosion resistance and strength, ideal for medical devices and machinery components. Titanium is prized for its strength-to-weight ratio and biocompatibility, often used in aerospace and implants.
Alloys such as Inconel or brass are also frequently processed. Inconel, known for high-temperature resistance, requires specialized tooling and cutting strategies due to its toughness. Brass, meanwhile, is easy to machine and often used in fittings and decorative components. Knowledge of these materials allows manufacturers to select appropriate cutting tools, speeds, and feeds, maximizing efficiency while minimizing tool wear.
Composite materials pose their own set of challenges. Materials like carbon fiber-reinforced plastics are lightweight and strong but require different cutting techniques to avoid delamination or fiber pull-out. Chinese CNC providers adapt by employing diamond-coated tools and optimized parameters to ensure quality.
Surface treatments and coatings are integral to material application. Anodizing, plating, or powder coating can enhance corrosion resistance, aesthetic appeal, or wear resistance. Manufacturers often integrate these processes into their workflows, ensuring finished parts meet all performance criteria.
Material procurement and quality control are also essential. Reputable Chinese CNC firms source high-grade raw materials from trusted suppliers, verifying certifications and material properties before processing. This attention to detail guarantees that the final components perform reliably in their designated environments.
Finally, continuous R&D efforts help manufacturers stay abreast of emerging materials, expanding their capabilities. Whether working with exotic alloys, advanced composites, or novel materials, their expertise ensures that every raw material is transformed into a precision-crafted component, meeting the highest standards of quality and durability.
## Proven Experience: Why Expertise Matters in High-Precision Machining
Experience is the backbone of high-precision CNC machining. The complexity of the parts, the diversity of materials, and the stringent quality requirements demand a deep well of practical knowledge. Chinese manufacturers with decades of proven expertise can navigate these challenges with confidence, delivering consistent, top-tier results.
Seasoned manufacturers understand the nuances of different machining processes. They recognize how material properties affect cutting tools, thermal expansion, and tolerances, adjusting parameters accordingly. Their experience allows for proactive troubleshooting—detecting potential issues before they impact quality or lead to costly rework.
Handling high-difficulty parts, such as micro-components or aerospace-grade components, requires meticulous planning and execution. Veteran technicians develop tailored strategies—specialized fixtures, custom tooling, or unique machining sequences—that optimize accuracy and efficiency. Their familiarity with complex geometries ensures that even intricate features are completed to exact specifications.
Moreover, experienced providers are adept at quality assurance. They implement rigorous inspection protocols, employing coordinate measuring machines (CMM), optical comparators, and laser scanners. Their capacity to identify deviations at early stages minimizes scrap and rework, saving time and resources.
In addition, their knowledge of international standards—such as ISO, ASTM, or AS9100—ensures compliance with client and industry requirements. This adherence not only guarantees quality but also facilitates seamless integration into global supply chains.
Customer testimonials and case studies often highlight the importance of experience. Many clients entrust complex projects to manufacturers with a track record of success, knowing that their reputation depends on precision and reliability. This proven expertise builds trust, fostering long-term collaborations across industries and borders.
Finally, continuous learning and innovation define experienced manufacturers. They stay updated with technological advancements, new materials, and industry best practices, ensuring they remain at the forefront of high-precision CNC machining. Their depth of expertise translates into tangible benefits for clients worldwide.
## Overcoming Global Challenges: Case Studies of Complex CNC Projects
Global clients often face unique manufacturing challenges—tight deadlines, complex geometries, or difficult materials—that require innovative solutions. Chinese CNC manufacturers have demonstrated their capability through numerous case studies, transforming daunting projects into success stories.
One notable example involved manufacturing aerospace turbine blades with micro-tolerance levels and internal cooling channels. Overcoming the difficulty of machining internal cavities in super-hard alloys, the Chinese team employed 5-axis high-speed milling combined with wire EDM. Extensive fixture design and process simulation ensured precise alignment, resulting in blades that met all aerospace standards within tight delivery schedules.
Another case focused on producing medical implants from titanium alloys with ultra-fine surface finishes. The challenge was to maintain high accuracy while preventing surface contamination. Utilizing specialized micro-milling tools, controlled environment processing, and post-machining surface treatments, the manufacturer delivered parts that adhered to stringent biocompatibility and safety standards.
A different project involved the production of complex electronic enclosures with micro-holes and intricate textures. By integrating laser micromachining and advanced CAD/CAM software, they achieved the desired features with high consistency. Their ability to combine multiple advanced techniques exemplifies flexible problem-solving in complex manufacturing contexts.
Handling large volume production of high-precision components also illustrates overcoming logistical and quality assurance hurdles. The Chinese CNC provider established a robust quality management system and streamlined workflows, enabling consistent output across batches while maintaining strict tolerances—a crucial advantage for global clients with tight schedules.
Case studies like these underline the importance of experience, technological adaptability, and problem-solving skills. They demonstrate how Chinese CNC manufacturers turn complex, high-stakes projects into success stories, reinforcing their reputation as reliable partners for clients worldwide.
## Precision Beyond Borders: Ensuring Quality for International Clients
Delivering high-precision components across borders involves more than just advanced machinery—it requires unwavering commitment to quality assurance. Chinese CNC manufacturers have adopted comprehensive measures to ensure that international clients receive parts that consistently meet or exceed their expectations.
International standards such as ISO 9001, ISO/TS 16949, and AS9100 certification underpin quality management systems that govern every stage of production. These frameworks emphasize process control, documentation, and continuous improvement, providing clients with confidence in the reliability of the manufactured parts.
Meticulous inspection procedures are integral. Coordinate Measuring Machines (CMM), optical inspection, and 3D scanning verify dimensions, surface finishes, and tolerances. Real-time monitoring during machining detects deviations early, reducing scrap and rework, and ensuring first-time quality.
Traceability is also crucial. Detailed records of raw materials, process parameters, and inspection results enable manufacturers to trace any issue back to its source swiftly. This transparency reassures international clients of the integrity and accountability embedded within the manufacturing process.
Furthermore, surface treatments and finishing processes—such as anodizing, electroplating, or polishing—are performed under controlled environments to guarantee consistency. This consistency ensures that components not only meet dimensional requirements but also perform reliably in their end-use environments.
Effective communication channels, including multilingual support and digital documentation, facilitate clarity and responsiveness. Clients receive regular updates, inspection reports, and certification documentation, fostering trust and collaboration.
In an increasingly globalized marketplace, the ability to deliver precise, reliable components across borders distinguishes top-tier CNC providers. Their dedication to quality beyond local borders underscores their role as dependable partners in complex international supply chains.
## Innovative Processes: Enhancing Accuracy in High-End CNC Machining
Innovation drives the evolution of high-precision CNC machining. Chinese manufacturers actively incorporate new technologies and methodologies to push the boundaries of accuracy and efficiency. From advanced software to cutting-edge hardware, these innovations enable the production of increasingly complex and demanding components.
One such development is the adoption of adaptive machining software, which dynamically adjusts tool paths based on real-time feedback. This minimizes errors caused by tool wear or material inconsistencies, maintaining tight tolerances throughout the production cycle. Similarly, the integration of Industry 4.0 principles—such as IoT sensors and automation—facilitates smarter, more connected machining environments.
High-precision spindle technology is another key area. Ultra-stable spindles with low vibration and high rotational accuracy reduce surface imperfections and dimensional deviations. Coupled with precision cooling systems, they enable stable operations even during extended machining of hard materials.
Laser measurement and in-process inspection tools allow for immediate quality checks without halting production. These systems detect minute deviations early, allowing for real-time corrections and significantly reducing scrap rates.
Additive manufacturing techniques complement traditional CNC processes, enabling the production of complex internal features that are difficult to achieve through subtractive methods alone. Hybrid machines combine milling and additive capabilities, expanding design possibilities and enhancing accuracy.
Furthermore, the use of AI-driven process optimization software predicts the best machining parameters based on material properties and design features. This proactive approach results in better surface finishes, longer tool life, and tighter tolerances.
Ultimately, the relentless pursuit of innovation in CNC machining not only improves precision but also enhances efficiency, reduces costs, and accelerates delivery—benefits that resonate deeply with international clients seeking cutting-edge manufacturing solutions.
## From Blueprint to Reality: The Customization Process Explained
Transforming detailed blueprints into high-precision parts is a meticulous process. Chinese CNC manufacturers excel in guiding clients through each step, ensuring their visions are accurately realized. The journey begins with comprehensive design review, where engineers analyze drawings for manufacturability and identify potential challenges.
Next, material selection is discussed, considering factors like strength, weight, corrosion resistance, and machinability. Clients often rely on expert advice to choose the most suitable raw materials, which the manufacturer sources from trusted suppliers with verified quality.
Once materials are secured, tooling and fixture design commence. Custom fixtures are engineered to hold complex geometries securely, enabling precise machining. This stage may involve creating prototypes or test runs to validate fixture effectiveness.
The actual machining process is meticulously planned using advanced CAD/CAM software. Tool paths are optimized for accuracy and efficiency, with simulations identifying potential collisions or errors beforehand. During production, in-process inspections monitor critical dimensions to ensure adherence to specifications.
Post-machining, parts undergo finishing processes—such as polishing, coating, or heat treatment—to meet surface quality and functional requirements. Final inspections, including CMM checks, verify that every dimension falls within specified tolerances.
Throughout this journey, clear communication and documentation keep clients informed and involved. Revisions or adjustments can be made at early stages, reducing costly rework. The result is a high-precision component that faithfully embodies the original design, delivered on time and to exact standards.
This comprehensive process exemplifies how skilled Chinese CNC providers combine technology, expertise, and customer collaboration to turn detailed blueprints into tangible, functional parts across the globe.
## High-Difficulty Parts: Managing Tolerance and Surface Finish Requirements
Manufacturing high-difficulty parts demands rigorous control over tolerances and surface finishes. Such components—used in aerospace, medical, or electronic applications—must perform reliably under demanding conditions. Chinese CNC manufacturers have developed specialized techniques and quality systems to meet these exacting standards.
Tight tolerances—often within microns—are achieved through precision machine tools, stable fixtures, and meticulous process control. Operators monitor machining parameters continuously, adjusting as needed to prevent deviations. Calibration of equipment and regular maintenance ensure machines operate at peak accuracy.
Surface finish quality is equally critical. Techniques such as high-speed milling, fine-grain tooling, and controlled cooling minimize surface roughness. Post-machining processes like polishing, electro-polishing, or coating further enhance surface quality, improving corrosion resistance and aesthetic appeal.
To manage these high standards consistently, manufacturers employ statistical process control (SPC) and rigorous inspection routines. CMM measurements verify that each part meets specified tolerances, with deviations analyzed for root causes and corrective actions implemented promptly.
Implementing cleanroom environments or controlled atmospheres is essential when working with sensitive components, such as medical implants or optical parts. This safeguards against contamination that could compromise performance.
Finally, ongoing staff training and technological upgrades ensure that the manufacturing team stays proficient in handling complex, high-precision tasks. Their expertise, combined with advanced equipment and meticulous quality control, guarantees that high-difficulty parts meet the most stringent requirements.
## Material Considerations: Working with Metals, Alloys, and Composites
The choice of material is fundamental to the success of high-precision CNC machining projects. Chinese manufacturers leverage extensive knowledge to work with an array of metals, alloys, and composites, tailoring their processes to each material’s unique properties.
Metals like aluminum are favored for their excellent machinability, lightweight characteristics, and cost-effectiveness. Stainless steel offers corrosion resistance and strength, suitable for medical and industrial applications. Titanium, with its high strength-to-weight ratio and biocompatibility, is commonly used in aerospace and implants, requiring specialized tooling and machining protocols.
Alloys such as Inconel or Kovar are employed in high-temperature or specialized electronic applications. These materials pose challenges due to their toughness and thermal properties, demanding high-energy cutting tools and controlled machining conditions.
Composite materials, including carbon fiber-reinforced plastics, require different handling techniques. Their anisotropic nature can cause delamination or fiber pull-out if not machined properly. Diamond-coated tools and optimized cutting parameters are used to ensure precision and surface quality.
Surface treatments—like anodizing, plating, or coating—are also selected based on material compatibility and application requirements. These processes enhance properties such as wear resistance, aesthetic appeal, or biocompatibility.
Managing material stock, verifying certifications, and ensuring traceability are integral parts of quality assurance. Reputable Chinese CNC providers source materials from trusted suppliers and perform thorough inspections before processing.
Their ongoing R&D efforts include exploring new materials and composite formulations, expanding their capabilities to meet emerging technological demands. This material mastery ensures that each component is manufactured to specification, optimized for performance, durability, and reliability.
## Global Standards & Quality Control: Ensuring Reliability & Precision
Adhering to international quality standards is essential for Chinese CNC manufacturers serving a global clientele. They implement comprehensive quality control systems aligned with standards such as ISO 9001, ISO/TS 16949, or industry-specific certifications like AS9100 for aerospace.
Quality assurance begins with raw material verification, ensuring traceability and compliance. During machining, in-process inspections monitor key dimensions and surface qualities, utilizing advanced measurement tools to detect deviations early.
Post-process, parts undergo thorough inspection—including CMM measurement, surface roughness testing, and non-destructive testing when necessary—to confirm they meet strict specifications. Data from these inspections are documented meticulously, providing traceability and accountability.
Manufacturers also establish calibration schedules for equipment, conduct regular audits, and employ statistical process control (SPC) techniques to maintain consistency across batches. This proactive approach minimizes variability and defects, ensuring reliable delivery.
Training personnel on quality standards, proper handling techniques, and inspection procedures fosters a culture of excellence. Clear documentation, certifications, and audit trails reassure clients of the integrity and reliability of the manufacturing process.
Finally, continuous improvement initiatives—such as feedback analysis, root cause investigations, and process optimization—help manufacturers stay ahead of evolving quality expectations. Their commitment to reliability and precision ensures that clients worldwide receive components that perform flawlessly in critical applications, forging long-term partnerships built on trust.
---
### OUTRO:
High-precision CNC machining has evolved into a sophisticated art and science—driven by technological innovation, extensive experience, and a relentless pursuit of perfection. Chinese manufacturers, leveraging their deep expertise and global standards, now serve as trusted partners for clients worldwide, delivering customized, complex, and high-quality components across diverse industries. By mastering material properties, advanced techniques, and strict quality controls, they turn intricate blueprints into tangible realities, overcoming any manufacturing challenge along the way. For enterprises seeking reliable, high-precision solutions beyond borders, these manufacturers exemplify excellence in craftsmanship, innovation, and service—setting the benchmark for the future of global manufacturing.