High-Precision CNC Machining for Large-Scale Industrial Equipment Components
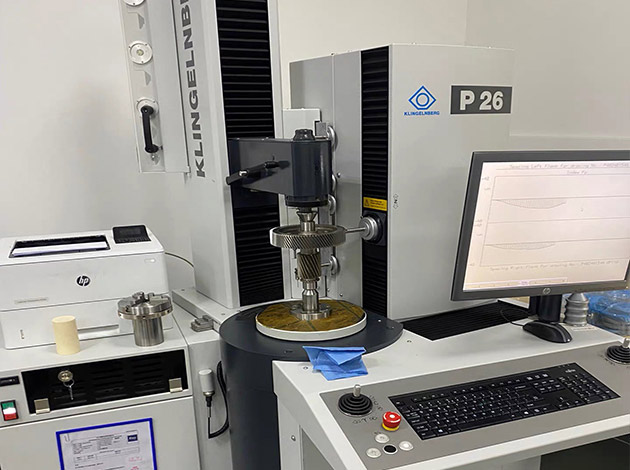
Precision Demands in the Heavy Industrial Equipment Sector
The heavy machinery and equipment industry—ranging from large turbines and compressors to rolling mills and mining machinery—relies heavily on high-precision, high-complexity CNC machining to manufacture critical components. As machines continue to grow in size and sophistication, the demand for tighter tolerances, more durable materials, and increasingly complex geometries has pushed CNC manufacturing capabilities to new limits.
In this environment, equipment manufacturers and system integrators require a machining partner capable of handling large-sized parts, highly complex geometries, and stringent dimensional tolerances, while also maintaining consistent quality across batches. Precision is not just a requirement—it’s a necessity to ensure optimal machine performance, reduce maintenance downtime, and extend equipment lifespan.
Machining Challenges and How We Solve Them
Machining large and intricate parts for heavy equipment presents multiple challenges:
- Thermal deformation during cutting, particularly in thick sections or long shafts;
- Maintaining tolerance control over large dimensions, often up to several meters;
- Ensuring surface integrity and resistance to corrosion, fatigue, or friction;
- Complicated setup and fixturing, especially for asymmetrical or oversized components;
- Material difficulties, such as hardened steels, stainless steels, or exotic alloys.
To overcome these issues, we utilize a combination of engineering expertise, advanced CNC machine tools, and quality assurance systems. Our process includes:
- Thermal compensation and multi-point clamping to reduce distortion;
- Multi-axis simultaneous machining (up to 5-axis) for accurate geometry in fewer setups;
- Toolpath simulation and collision detection before actual machining;
- Real-time monitoring and adaptive feed control to optimize machining conditions;
- Precision inspection equipment, including CMM and roundness testers, to validate tolerances down to ±0.001 mm.
Commonly Used Materials and Their Advantages
Heavy equipment components must endure extreme mechanical and environmental stresses. We frequently work with:
- Alloy Steel (e.g., 42CrMo, 20CrNiMo): Offers excellent strength and toughness, ideal for shafts, gears, and bushings.
- Stainless Steel (e.g., 304, 316, 17-4PH): Provides corrosion resistance and is suitable for harsh chemical environments.
- Cast Iron & Ductile Iron: Common in housing structures and heavy load-bearing parts for vibration damping.
- Titanium Alloys (e.g., Ti-6Al-4V): Lightweight and corrosion-resistant, used in energy and aerospace-related heavy machinery.
- Aluminum Alloys (e.g., 6061-T6, 7075-T6): Good for reducing overall component weight without sacrificing structural integrity.
- Copper Alloys: Often used in electrical equipment or components requiring thermal conductivity.
All materials are carefully sourced and certified, and we offer full traceability throughout the machining process.
Advanced Machining Capabilities and Equipment
We specialize in high-precision CNC machining for large, high-complexity parts, with the following capabilities:
- Machining Tolerances: Down to ±0.001 mm for critical features; geometric tolerances (flatness, roundness, concentricity) as tight as 0.002 mm.
- Max Part Size: Up to 2000 mm (diameter) and 3000 mm (length), depending on the configuration.
- Surface Finish: Achievable Ra ≤ 0.02 μm using grinding, honing, and polishing processes.
- Multi-Axis Machining: 4-axis and 5-axis simultaneous machining for complex contours and compound angles.
- High-Speed Milling and Turning: Suitable for high-hardness materials and high-volume production.
Inspection & Quality Assurance:
- Zeiss CMM Systems: For high-precision 3D measurements.
- Roundness and Cylindricity Analyzers: For critical rotational components.
- Digital Profile Projectors and Non-contact Measuring Systems: For complex profiles.
- 100% Dimensional Reports available on request.
Every part is subjected to a rigorous inspection process before delivery, ensuring it meets customer specifications in both performance and finish.
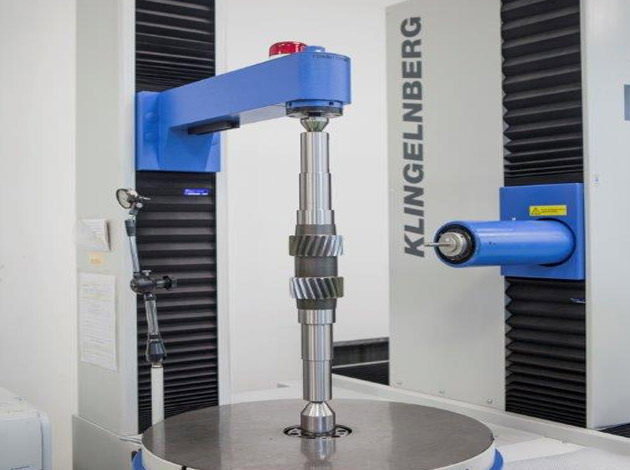
Typical Components and Industrial Applications
We provide CNC machining services for a wide variety of components used in:
- Turbomachinery: Precision rotor shafts, impellers, and volutes.
- Rolling Mills: Drive shafts, backup rolls, bearing housings.
- Compressors and Pumps: Cylinder blocks, bearing sleeves, and valve bodies.
- Construction and Mining Equipment: Gearboxes, hydraulic blocks, couplings.
- Power Transmission Systems: Keyed shafts, clutch housings, brake drums.
- Heavy-Duty Elevators and Cranes: Wheel hubs, support brackets, lifting mechanisms.
Each part is custom machined according to your drawing or 3D model, with optional reverse engineering services available for legacy components.
Project Showcase: Custom Rotor Shaft for Power Generation Equipment
One notable project involved the production of a rotor shaft over 1800 mm long, made from 42CrMo quenched and tempered alloy steel, requiring concentricity tolerance within 0.003 mm across the entire length. The part was used in a large power generation turbine and required:
- Mazak turning center for roughing;
- Mikron high-speed CNC for profile milling;
- Studer cylindrical grinder for final finish;
- Tokyo Seimitsu roundness testing to ensure conformity;
- Zeiss CMM for comprehensive dimensional reporting.
The successful delivery and performance of this part earned us long-term cooperation with a key global energy equipment supplier.
Ready to Support Your CNC Machining Needs
Whether you need a high-precision, high-complexity large CNC machining manufacturer for new product development or a reliable partner for long-term component production, we’re equipped to deliver unmatched precision, consistency, and service.
Contact us today to discuss your drawings, materials, and tolerances. Our engineers are ready to offer tailored machining solutions that meet your industry’s toughest demands.
👉 Get a Quote Today – Precision Without Compromise.
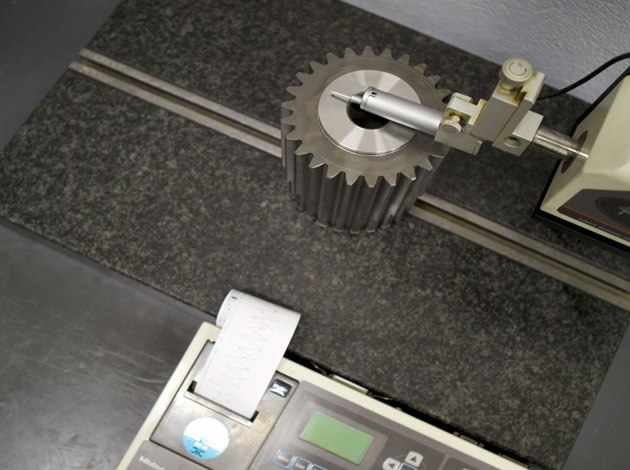