High-Precision CNC Machining Solutions for Optical Component Manufacturing
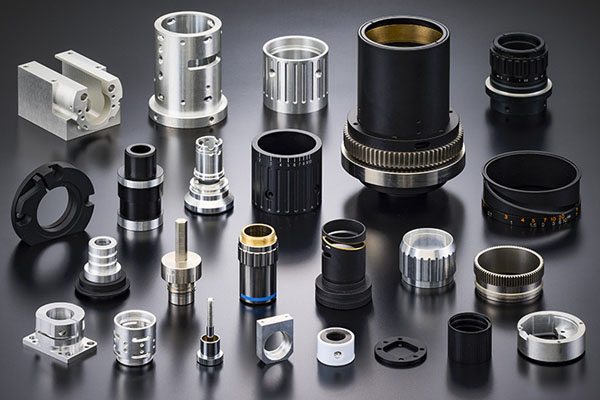
===INTRO:===
In the rapidly evolving world of precision engineering, the demand for high-precision optical components has surged dramatically across various industries. From telecommunications and aerospace to medical devices and consumer electronics, the core of these innovations relies heavily on components that require meticulous manufacturing processes. As the backbone of these high-performance systems, optical parts demand exceptional accuracy, surface finish quality, and reliability. CNC machining has emerged as a pivotal technology in meeting these stringent requirements, offering the capability to produce complex, ultra-precise optical components with consistent quality and efficiency. This article explores the significance of high-precision CNC machining solutions tailored specifically for optical component manufacturing, highlighting the challenges, materials, capabilities, and successful case studies that demonstrate our expertise in this specialized field.
The Growing Demand for High-Precision Optical Components in Manufacturing
The exponential growth of optical technology applications has notably increased the need for highly precise, intricately crafted components. Optical systems, whether used in laser devices, imaging instruments, or fiber optic communication networks, require parts with exacting tolerances—often within micrometers or even nanometers. As technology advances, so do customer expectations for better performance, miniaturization, and durability of optical components. This trend drives manufacturers to adopt more sophisticated manufacturing methods, with CNC machining standing out due to its remarkable precision and repeatability.
In sectors like aerospace and defense, optical components such as lenses, prisms, and mirrors are critical for system accuracy and safety, necessitating manufacturing processes that can handle complex geometries without compromising quality. Similarly, medical imaging devices depend on optical parts with flawless surface finishes to ensure clear imaging. The consumer electronics industry, with its demand for compact and lightweight devices, also relies heavily on CNC-machined optical components to maintain high standards while reducing size and weight.
Furthermore, the pursuit of innovative optical solutions, such as integrated photonics and miniaturized sensors, pushes the boundaries of traditional manufacturing. High-precision CNC machining provides the flexibility to produce custom, small-batch, and complex parts with tight tolerances, making it an indispensable tool in the modern optical manufacturing landscape. As the market continues its upward trajectory, investments in advanced CNC solutions are becoming essential for companies aiming to stay competitive and deliver cutting-edge optical products.
Overcoming Key Challenges in CNC Machining of Optical Parts
Manufacturing optical components via CNC machining involves several unique challenges that require careful planning and advanced solutions. One primary obstacle is achieving the ultra-smooth surface finish required for optical performance. Surface roughness can significantly affect the optical clarity and efficiency, making it crucial to control parameters such as tool selection, cutting speed, and cooling methods.
Another challenge is maintaining exact tolerances during the machining process. Even minute deviations can result in optical aberrations or misalignments, which compromise the functionality of the final product. To address this, high-precision CNC machines equipped with multi-axis controls and real-time feedback systems are employed. These systems enable meticulous control over tool paths and dimensions, ensuring consistent quality across production batches.
Materials used in optical components, such as fused silica, BK7 glass, and sapphire, are often hard and brittle, demanding specialized tooling and machining strategies to prevent cracking or chipping. Correct selection of cutting tools, along with optimized feed rates and cooling strategies, helps mitigate stress and deformation.
Contamination and particle generation during machining can also be problematic, as even microscopic debris can impair optical clarity. Implementing cleanroom environments and precision coolant systems reduces contamination risks. Additionally, advanced inspection methods like interferometry and atomic force microscopy are employed to verify the surface quality and dimensional accuracy of the machined parts.
Thermal management is another critical factor since heat generated during machining can cause material expansion, leading to dimensional inaccuracies. Employing precise temperature controls and low-thermal-expansion fixtures helps maintain stability throughout the process.
Ultimately, overcoming these challenges necessitates a combination of state-of-the-art machinery, skilled operators, and rigorous quality control protocols. By integrating these solutions, manufacturers can produce optical components that meet the highest standards of performance and reliability.
Essential Materials Used in Optical Component CNC Machining
The selection of materials is fundamental in optical component manufacturing, as each material brings unique properties that influence machining strategy, performance, and application suitability. Here, we highlight some of the most common materials used in high-precision CNC machining for optical parts.
Fused Silica: Known for its excellent transparency, chemical stability, and low thermal expansion, fused silica is widely used in high-power laser optics and precision lenses. Its hardness and brittleness require careful tool selection and optimized machining parameters to prevent cracking.
Borosilicate Glass (e.g., BK7): Featuring good optical clarity, ease of fabrication, and thermal stability, BK7 glass is often used in imaging and measurement devices. Its moderate hardness makes it more manageable in CNC processes compared to fused silica.
Sapphire: Valued for its exceptional hardness, scratch resistance, and optical transparency in the visible and infrared spectrum, sapphire is ideal for high-durability windows and laser components. Machining sapphire demands diamond tools and ultra-precise control to avoid surface damage.
Calcium Fluoride (CaF₂): With excellent transmission in the ultraviolet and infrared ranges, calcium fluoride is utilized in specialized optical applications. Its softness relative to other materials necessitates gentle machining to prevent deformation.
Optical Crystals (e.g., LiNbO₃, KTP): These materials exhibit nonlinear optical properties, essential in laser modulation and frequency doubling. Their complex shapes and sensitive nature call for tailored CNC strategies.
Metallic Materials: While less common for pure optical functions, metals such as aluminum and copper are used for mounts, housings, and reflective surfaces. Their machinability is generally more straightforward, but surface finish quality remains critical.
Each material’s unique characteristics influence the choice of cutting tools, cooling methods, and machining parameters. Understanding these properties enables manufacturers to optimize processes, maximize yield, and ensure the functional integrity of the final optical components.
Showcasing Our CNC Machining Capabilities for Optical Applications
Our facility boasts cutting-edge CNC machining equipment tailored specifically to the demands of optical component manufacturing. We operate multi-axis CNC machines equipped with ultra-precision spindles capable of achieving tolerances within ±2 micrometers, ensuring that every component meets strict industry standards.
Precision control is central to our machining process. Our machines are integrated with real-time feedback systems, such as laser measurement and interferometric sensors, to continuously monitor dimensional accuracy during production. This allows us to detect and correct deviations instantly, maintaining consistency across batches.
Surface finish quality is a top priority. We utilize fine-grain diamond tools and employ polishing techniques in conjunction with CNC milling and grinding to achieve nanometer-level surface roughness. This combination ensures optical clarity and minimizes light scattering or distortion.
Temperature stability is maintained in our cleanroom environment, preventing thermal expansion from affecting part dimensions during machining. Additionally, we use specialized coolant and filtration systems to reduce particle contamination and improve surface quality.
Our team is experienced in handling a wide range of optical materials, from fragile fused silica to robust sapphire, employing tailored strategies for each. We also offer comprehensive inspection services, including interferometric testing, coordinate measuring, and surface profilometry, to verify that every component conforms to specifications.
Ultimately, our capabilities enable us to deliver high-precision CNC machined optical components that meet diverse industry standards, from aerospace to biomedical applications. Our commitment to quality, innovation, and customer satisfaction positions us as a trusted partner in optical component manufacturing.
Common Optical Components Manufactured Through CNC Precision Machining
CNC machining is instrumental in producing a broad spectrum of optical components, many of which are vital in advanced technological applications. Here are some of the most common optical parts manufactured through high-precision CNC processes:
Lenses: Custom-shaped lenses, including plano-convex, plano-concave, and complex aspheric designs, are machined with high accuracy to ensure precise focusing, imaging, or beam shaping.
Prisms: Used in beam steering and polarization control, prisms require exact angles and smooth surfaces. CNC machining allows for complex geometries that are challenging to produce with traditional methods.
Mirrors: Precision mirrors, especially those with curved surfaces, are fabricated with tight tolerances to ensure proper reflectivity and surface smoothness, critical in laser systems and telescopes.
Optical Windows and Covers: These components protect sensitive optical elements while allowing light transmission. They must be flat, scratch-free, and free from distortions.
Fiber Optic Components: Connectors, ferrules, and collimators are machined to tight tolerances to ensure optimal light transmission and minimal signal loss.
Waveguides and Integrated Photonics: Miniaturized optical pathways require precise fabrication of complex geometries to facilitate photonic integration and signal control.
Diffusers and Beam Expanders: These components modify light properties and are machined to exact specifications for uniform illumination and beam shaping.
The ability to produce such a diverse range of components highlights the versatility of CNC machining in optical manufacturing. This technology allows for rapid prototyping, small-batch production, and complex geometrical designs, fulfilling the evolving needs of the optical industry.
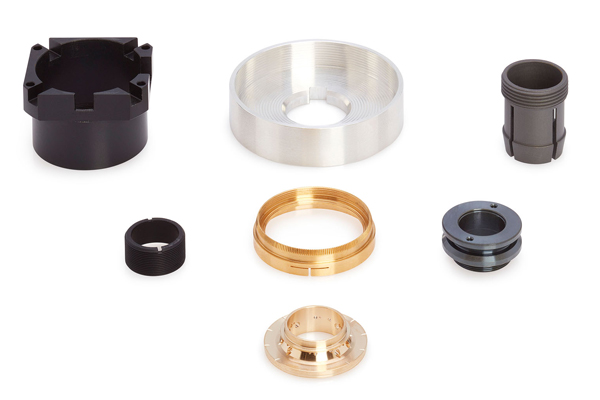
Customized processing of high-precision parts in the optical field
Successful Projects and Customer Testimonials in Optical CNC Machining
Our portfolio features numerous successful projects where high-precision CNC machining has delivered exceptional results for clients across various sectors. For example, we supplied custom fused silica lenses for a leading laser manufacturer, achieving surface roughness below 1 nanometer and tolerances within ±1 micrometer. The client reported improved laser beam quality and system stability as a direct result of our precise manufacturing.
In another project, we produced sapphire windows for aerospace optical sensors, requiring complex curved surfaces with immaculate surface finishes. Our team utilized diamond milling and polishing techniques to meet the demanding specifications, leading to enhanced sensor durability and performance.
A renowned medical device company commissioned us to manufacture optical prisms for imaging systems. Our precision machining ensured that the prisms maintained angular accuracy within arc seconds, enabling clearer diagnostics and better patient outcomes.
Customer testimonials consistently highlight our attention to detail, responsiveness, and ability to meet tight deadlines. Clients appreciate our transparent communication and comprehensive quality control, which provide confidence in every batch of parts produced.
Many of our clients have also benefited from our seamless collaboration in developing custom solutions, adapting processes to meet their specific material and design requirements. These successes underscore our commitment to excellence and our capability to support innovative optical projects at every stage.
Partnering with us means leveraging advanced CNC machining solutions dedicated to pushing the boundaries of optical component manufacturing. Contact us today to discuss your project needs and discover how we can turn your optical visions into reality with high-precision, reliable CNC solutions.
===OUTRO:===
High-precision CNC machining stands at the forefront of optical component manufacturing, enabling the production of complex, ultra-smooth, and precisely dimensioned parts essential for cutting-edge optical systems. By overcoming manufacturing challenges through advanced equipment, meticulous processes, and material expertise, we deliver components that meet the highest industry standards. Whether designing lenses, prisms, mirrors, or specialized optical modules, our capabilities and experience ensure your projects are executed with unmatched accuracy and quality. Partner with us to bring your optical innovations to life—reach out today for tailored CNC machining solutions that elevate your optical products to new heights.