Precision Ceramic Machining for the Fluid Control & Valve Industry
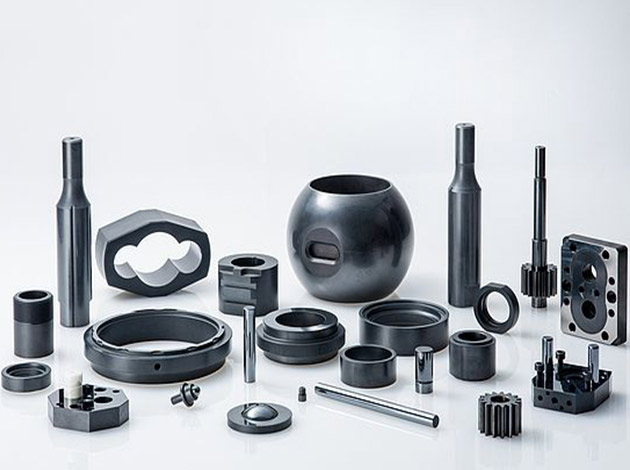
±0.001mm tolerance | Ra 0.02μm finish | Designed for corrosive and high-pressure systems
In industries where precision, sealing integrity, and chemical resistance are non-negotiable—such as chemical processing, water treatment, semiconductor fluidics, and high-pressure pumps—advanced ceramics are an ideal material for critical flow control components.
Our facility specializes in custom CNC machining of ceramic valve parts and flow components, achieving the highest dimensional and geometric tolerances needed in demanding fluid applications.
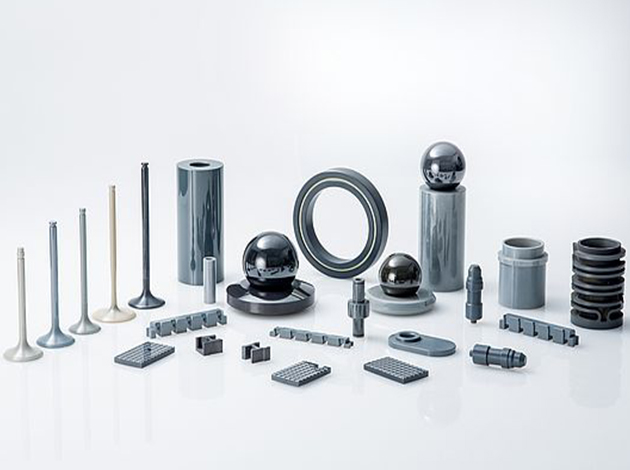
Why Ceramics for Fluid Control?
Ceramic materials like zirconia, alumina, and silicon carbide provide:
- Outstanding corrosion resistance to acids, alkalis, and solvents
- Extreme hardness for long service life in abrasive media
- Thermal and dimensional stability in high-pressure, high-temperature environments
- Low friction and chemical inertness, ideal for sealing surfaces
These properties outperform metals and plastics in many high-wear or chemically aggressive environments.
Typical Ceramic Components We Manufacture
- Ceramic valve cores / valve balls
- Precision ceramic valve seats & liners
- Ceramic plungers / pistons for metering pumps
- Flow restrictor orifices and ceramic nozzles
- High-pressure seal rings
- Non-return ceramic discs
- Fluid isolation inserts for analyzers
Used in:
✔ Chemical dosing systems
✔ Ultra-pure water systems
✔ Acid/alkaline processing lines
✔ Analytical and laboratory instruments
✔ Food-grade fluid valves
✔ Medical infusion pumps
Equipment & Tolerance Capabilities
We utilize:
- 5-axis CNC machines for complex shapes and undercuts
- Precision internal/external cylindrical grinding for sealing surfaces
- Roundness testing, flatness measurement, and laser metrology
- Superfine polishing for dynamic ceramic-to-ceramic or ceramic-to-metal seals
We routinely achieve:
- ±0.001mm dimensional tolerance
- Geometric form error ≤0.002mm (roundness, flatness, cylindricity)
- Surface finish up to Ra 0.02μm for sealing and sliding applications
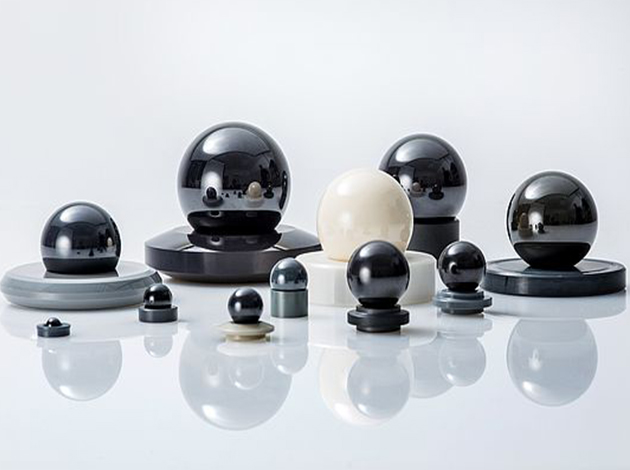
Drawing-Based Custom Manufacturing
With over 20 years of custom ceramic machining, our team works closely with clients to:
- Review 2D/3D drawings and functional specs
- Suggest material and design optimization
- Develop custom fixturing for brittle ceramics
- Ensure long-term dimensional repeatability for replacement parts or serial production
Our workflow is fully ISO9001 certified, with traceable batch controls and detailed inspection reports for each part.
Global Projects & Fluidic Systems We Support
We’ve delivered ceramic components used in:
- Precision analytical valve assemblies for lab automation
- High-pressure ceramic metering pumps in semiconductor and medical systems
- Corrosive fluid valves for petrochemical and wastewater treatment plants
- Multi-channel ceramic valve blocks in compact instrumentation systems
Our clients include OEMs and system integrators across Germany, Switzerland, the U.S., Japan, and Southeast Asia.
When Durability and Precision Matter—Ceramics Lead the Flow
Whether you need a single valve prototype or long-term OEM supply, our ceramic machining capabilities deliver sealing precision, dimensional reliability, and material integrity in the most challenging flow control environments.
Let’s build precision into every drop, every seal, and every system.