Precision CNC Machining for Custom Parts: Expert Solutions and Materials
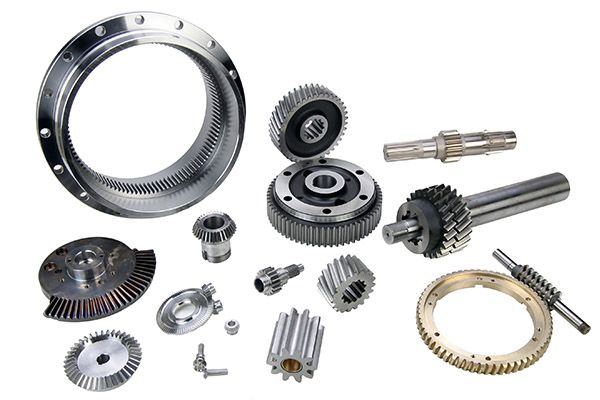
In today’s highly competitive and technology-driven industries, the demand for precision-engineered, custom parts continues to escalate. Whether in aerospace, medical devices, automotive, electronics, or industrial machinery, manufacturers rely heavily on CNC machining—an advanced manufacturing process that delivers high accuracy, efficiency, and repeatability. As component complexity and performance standards increase, the need for expert CNC machining solutions that can produce tailored parts according to precise specifications has never been more critical. In this landscape, selecting a trusted partner capable of delivering consistent quality and intricate geometries is essential for achieving success and maintaining a competitive edge.
The Growing Demand for Precision CNC Machined Custom Parts in Modern Industries
The modern manufacturing world is witnessing an exponential rise in the need for precision CNC machined custom parts. Industries such as aerospace require components that meet stringent tolerances to ensure safety and performance, while medical device manufacturers demand complex parts with tight specifications for reliability and biocompatibility. Automotive manufacturers seek lightweight yet durable components for electric and traditional vehicles, and electronics firms need miniaturized, high-performance parts for gadgets and communication devices.
This surge is driven by technological advancements that allow for more complex designs, miniaturization, and higher quality standards. As industries push the boundaries of innovation, the role of CNC machining becomes indispensable, offering unparalleled precision and flexibility. Custom parts produced through CNC machining enable rapid prototyping, small batch production, and high-volume manufacturing—each vital for staying ahead in a competitive landscape.
Furthermore, the ability to customize parts based on detailed technical drawings offers manufacturers the versatility to innovate without compromising on quality. This flexibility translates into faster development cycles, reduced lead times, and cost-effective solutions for complex prototypes and end-use components. As a result, the demand for expert CNC machining providers who can interpret detailed drawings and deliver precise, reliable parts continues to grow across multiple sectors.
The global shift toward personalized and tailored products further amplifies this demand. Consumers and industries alike are seeking products that fit specific needs, which necessitates precision machining that can adapt quickly to custom specifications. In this context, CNC machining’s ability to produce unique parts with tight tolerances and complex geometries makes it the manufacturing method of choice for modern, innovative companies.
In addition, the increasing adoption of automation and Industry 4.0 technologies in manufacturing processes is enhancing the capabilities of CNC machining. Smart CNC systems equipped with advanced software and robotics enable more efficient, precise, and consistent production of custom parts, supporting the trend toward mass customization without sacrificing quality.
This evolving landscape underscores the importance of partnering with CNC machining experts who understand the nuances of various materials, machining techniques, and quality control measures. Such expertise ensures that custom parts not only meet design specifications but also perform reliably under operational stresses. As industries continue to demand higher precision and complex geometries, the role of specialized CNC machining providers will only become more vital.
Overcoming Manufacturing Challenges with Expert CNC Machining Solutions
Despite the many advantages of CNC machining, producing custom parts with tight tolerances and intricate features involves navigating several manufacturing challenges. One common issue is achieving high precision consistently, especially when working with complex geometries or miniature components. Variations in tool wear, material properties, or machine calibration can impact the final dimensions and surface finish, risking non-conformance to specifications.
To address this, expert CNC machining providers utilize sophisticated equipment and advanced machining strategies. For example, multi-axis CNC centers allow for complex part orientation and minimized setup changes, ensuring better accuracy and surface quality. They also implement real-time monitoring systems that track cutting forces, vibrations, and temperatures, enabling proactive adjustments to maintain tight tolerances throughout production runs.
Material selection itself can pose challenges, especially when working with hard, flexible, or temperature-sensitive materials. machinists with extensive experience know how to optimize cutting parameters, select appropriate tooling, and apply specialized techniques such as high-speed machining or cryogenic cutting to manage these issues effectively. This expertise reduces tool wear, extends machine life, and ensures consistent quality.
Another significant challenge is the need for rapid turnaround times without sacrificing precision. Expert CNC shops streamline workflows through automation, digital integration, and efficient project management. They implement rigorous quality control protocols, including coordinate measuring machines (CMM) inspections and visual inspections, to verify dimensions and surface finishes meet tight tolerances before delivery.
Design complexity also introduces difficulties in fixture design and chip evacuation, which are crucial for maintaining accuracy. Skilled machinists can develop customized fixtures and employ optimized cutting paths to prevent deformation or inaccuracies. This holistic approach to problem-solving helps overcome manufacturing hurdles and ensures the successful production of highly complex custom parts.
Moreover, continuous staff training and investment in the latest CNC technology are essential for maintaining a competitive edge. Industry-leading CNC machining providers stay updated on advancements like additive manufacturing integration, high-speed cutting, and adaptive control systems, enabling them to tackle even the most demanding projects efficiently.
By leveraging these expert solutions, manufacturers can confidently produce precision-engineered, custom parts that meet rigorous standards while minimizing waste, reducing costs, and accelerating time-to-market. These capabilities highlight the importance of partnering with experienced CNC machining specialists who understand how to navigate and solve manufacturing challenges effectively.
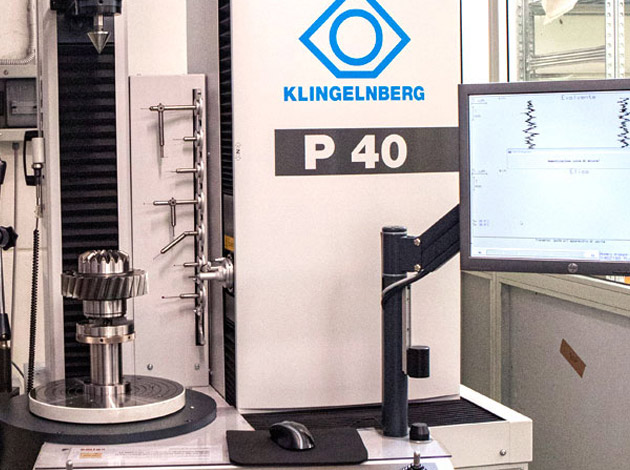
Key Materials Used in Precision CNC Machining and Their Unique Properties
The performance, durability, and functionality of CNC machined parts largely depend on the materials chosen for production. Different materials offer unique properties that make them suitable for specific applications, environments, and performance requirements. As custom parts vary widely across industries, understanding material characteristics is fundamental for achieving optimal results in CNC machining.
Aluminum is one of the most popular materials due to its excellent machinability, lightweight nature, and good corrosion resistance. Its versatility makes it ideal for aerospace, automotive, and consumer electronics. Aluminum alloys like 6061 and 7075 are commonly used for structural components that demand high strength-to-weight ratios. Their ability to produce smooth surface finishes and tight tolerances further enhances their appeal in precision machining.
Stainless steel offers exceptional corrosion resistance, strength, and hygienic properties. It is widely used in medical devices, food processing equipment, and marine applications. Types such as 316 and 17-4 PH are known for their toughness and ability to withstand harsh environments. Despite being more challenging to machine due to their hardness, advanced CNC techniques and tooling enable precise fabrication of complex stainless steel parts.
Brass and copper are valued for their excellent electrical conductivity and thermal properties, making them essential in electrical connectors, heat sinks, and valve components. Brass is also appreciated for its ease of machining, good corrosion resistance, and aesthetic appeal. These materials are ideal for intricate, precision parts where electrical or thermal performance is critical.
Titanium stands out for its high strength-to-weight ratio, biocompatibility, and temperature resistance. It is extensively used in aerospace, medical implants, and high-performance sporting equipment. Machining titanium demands specialized tools and techniques due to its toughness and tendency to gall, but the resulting parts are highly durable and lightweight.
Engineering plastics such as PEEK, Delrin (acetal), and PVC are increasingly used in CNC machining for their low weight, chemical resistance, and electrical insulation properties. They are suitable for applications where metal parts would be too heavy or reactive. These plastics can be precisely machined to tight tolerances, enabling complex, lightweight components in electronics and medical devices.
Selecting the right material involves understanding the specific application demands, environmental conditions, and desired mechanical properties. Expert CNC machining providers often collaborate with clients to recommend the most suitable materials, considering factors like machinability, cost, and end-use performance. They also have in-depth knowledge of how different materials respond to various machining techniques, ensuring optimal quality and efficiency.
The availability of advanced composite materials, ceramics, and specialty alloys continues to expand the possibilities for custom parts. Each material’s unique properties—such as hardness, thermal stability, electrical conductivity, and corrosion resistance—must be carefully considered during the design and manufacturing process. This comprehensive understanding enables CNC machining experts to produce high-quality, reliable components for even the most demanding applications.
Showcasing Our CNC Machining Capabilities: Tolerances, Equipment, and Quality Control
A key factor in producing high-precision custom parts is the capability of the CNC machining provider. Industry-leading shops boast state-of-the-art equipment, rigorous quality control protocols, and skilled personnel dedicated to exceeding client expectations. These factors collectively ensure that every part produced meets the strictest standards for accuracy, surface finish, and functionality.
Our machining centers are equipped with multi-axis CNC mills and lathes, capable of handling complex geometries, tight tolerances, and diverse materials. The high-speed spindles, advanced tooling systems, and multi-axis capabilities allow for intricate machining operations with minimal setup changes, reducing cycle times and improving precision. These machines can achieve tolerances as tight as ±0.0002 inches or better, suitable for aerospace, medical, and high-performance engineering applications.
Precision in CNC machining is supported by comprehensive CAD/CAM integration, enabling the translation of detailed drawings into optimized tool paths. This digital workflow ensures consistency and repeatability across production batches. Our engineers leverage simulation software to detect potential issues before machining begins, reducing errors and material waste.
Quality control is embedded throughout our production process. We utilize coordinate measuring machines (CMMs) for dimensional verification, ensuring that every part conforms to specified tolerances. Surface finish inspections and visual assessments are conducted regularly, and data is documented for traceability and compliance with industry standards. Our adherence to ISO 9001 or similar certifications demonstrates our commitment to quality management.
To maintain consistency, we implement rigorous process controls, including machine calibration, tool wear monitoring, and environmental controls within machining facilities. Our team continually trains on the latest techniques and industry standards, ensuring that each project benefits from cutting-edge practices.
Furthermore, our ability to offer rapid prototyping, small batch runs, and high-volume production makes us versatile partners for custom CNC machining needs. Whether you require a single prototype or thousands of identical parts, our capabilities ensure precision, reliability, and efficient turnaround times.
Ultimately, our advanced equipment, experienced staff, and strict quality assurance processes enable us to deliver custom parts that precisely match your drawings and specifications. Partnering with a CNC machining provider with such comprehensive capabilities guarantees the success of your project and satisfaction with the final product.
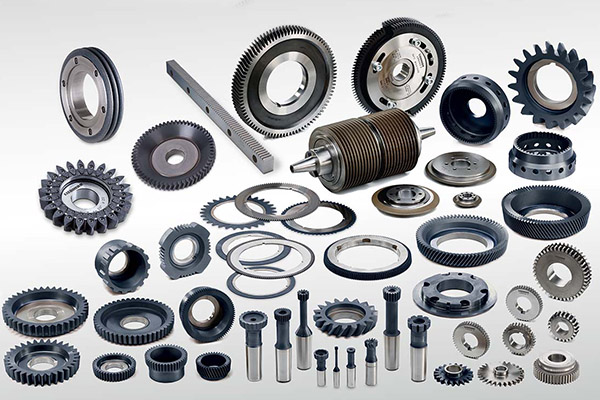
Common Custom Parts Produced by CNC Machining and Their Industrial Applications
CNC machining’s flexibility makes it suitable for manufacturing a wide array of custom parts across various industries. Some of the most common components include brackets, housings, connectors, shafts, and precision gears—each tailored to specific technical requirements.
In the aerospace industry, CNC machining produces critical structural components, engine parts, and aerodynamic surfaces where precise tolerances are mandatory for safety and performance. These parts often require the use of lightweight materials like aluminum and titanium, machined to exact specifications to withstand extreme conditions.
Medical applications benefit from CNC-machined implants, surgical instruments, and diagnostic device components. These parts demand high biocompatibility, dimensional accuracy, and surface finishes that facilitate sterilization and biocompatibility standards. Plastics like PEEK and medical-grade stainless steel are common choices for such parts.
Automotive manufacturers rely on CNC machined parts such as engine components, transmission parts, and custom brackets. These parts are designed for high durability, heat resistance, and weight reduction, supporting innovations like electric vehicles and high-performance engines. Precise machining ensures optimal fit and function while reducing assembly times.
Electronics and communication industries use CNC machined enclosures, heat sinks, and connectors that require intricate details and tight tolerances. Miniaturization trends demand components that can be produced with high precision to ensure proper fit and electrical performance, often utilizing aluminum, copper, or plastics.
Industrial machinery incorporates CNC machined gears, shafts, bearings, and housings that must operate reliably under heavy loads and harsh environments. Complex geometries and precise dimensions are necessary to ensure smooth operation and longevity of equipment.
Custom tooling and jigs for manufacturing processes, including molds and fixtures, are also produced via CNC machining. These tools enhance production efficiency, accuracy, and repeatability across various manufacturing workflows.
Overall, the versatility of CNC machining enables the production of highly specific, complex, and reliable custom parts tailored for diverse industrial applications. Partnering with experienced CNC experts ensures that your unique design requirements are met with precision and quality, helping to propel your projects forward efficiently.
Partner with Our CNC Machining Experts for Your Custom Part Needs—Get a Quote Today
When it comes to producing precision CNC machined parts based on your detailed drawings, choosing the right partner makes all the difference. Our team of dedicated CNC machining experts offers comprehensive solutions, from initial design consultation to final quality inspection. We understand the importance of accuracy, material selection, and timely delivery, ensuring your project’s success.
Our advanced manufacturing facilities are equipped with the latest multi-axis CNC machines capable of handling complex geometries and tight tolerances. We utilize cutting-edge CAD/CAM software to translate your drawings into optimized machining strategies, maximizing efficiency and precision. Our engineers are experienced in working with a wide variety of materials, including metals, plastics, and composites, tailored to your application requirements.
Quality assurance is at the core of our operations. Through rigorous inspection procedures, including CMM measurements and surface analysis, we ensure each part meets or exceeds specified tolerances. Our commitment to continuous improvement and lean manufacturing principles helps us deliver high-quality results consistently.
We also offer flexible service options suitable for prototypes, small batches, or large-volume production. Our streamlined workflow and dedicated customer support team aim to provide quick turnaround times, competitive pricing, and clear communication throughout the project lifecycle.
Partnering with us means gaining a reliable, experienced CNC machining provider who understands the importance of precision, durability, and cost-effectiveness. Whether you are designing a new product or need to produce complex components to tight specifications, we are here to turn your drawings into reality.
Requesting a quote is simple—just share your technical drawings and specifications, and our experts will evaluate your project to provide a tailored solution. Let us help you achieve your manufacturing goals with expert CNC machining services designed for your success.
Contact us today to discuss your custom part needs and discover how our precision CNC machining capabilities can bring your ideas to life with unmatched quality and efficiency.
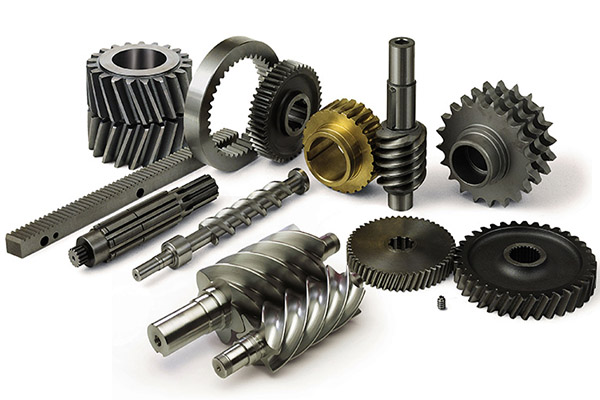