Precision CNC Machining for High-Precision Mechanical Components
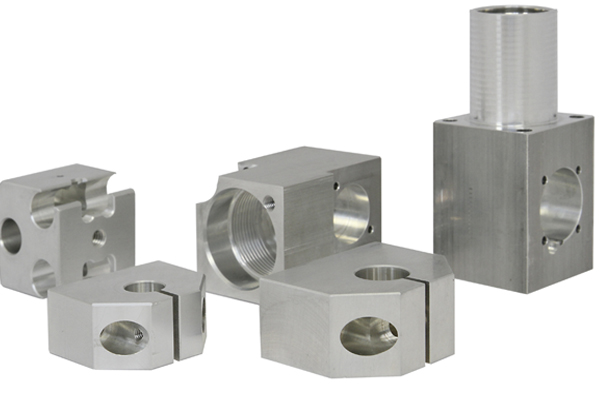
# Precision CNC Machining for High-Precision Mechanical Components
---
##
In today's fast-evolving industrial landscape, the demand for high-precision mechanical components has surged dramatically. Whether in aerospace, automotive, medical devices, or automation equipment, the performance and reliability of machinery heavily depend on the quality and precision of the parts used. CNC machining, especially advanced precision CNC techniques, has emerged as a critical enabler for manufacturing these complex, high-precision components. This article explores the growing need for such parts, the challenges faced in manufacturing them, the materials involved, our capabilities, and real-world success stories that highlight the importance of precision CNC machining in engineering applications.
---
## Understanding the Growing Demand for High-Precision Mechanical Components
The global manufacturing industry is increasingly driven by the demand for miniaturization, enhanced performance, and durability. High-precision mechanical components are essential in sectors like aerospace, where tolerances often need to be within micrometers to ensure safety and efficiency, or in medical devices that require flawless, reliable parts for patient safety. As automation and robotics become ubiquitous in manufacturing and other industrial sectors, the need for consistent, high-quality components with intricate geometries has become paramount.
Industries such as engineering machinery and automation demand components that can withstand extreme conditions while maintaining tight tolerances. Moreover, the trend towards smart, interconnected systems necessitates components that are not only precise but also manufactured with high repeatability. This growing complexity has elevated the role of precision CNC machining as the go-to solution for producing high-precision parts at scale.
Furthermore, the push for innovation in design—like lightweight yet strong parts—relies heavily on advanced machining techniques. As a result, the industry’s reliance on cutting-edge CNC technology continues to grow, driven by the need for high accuracy, complex geometries, and superior surface finishes. This demand also extends to the customization of parts, enabling tailored solutions for specialized applications.
The ability to produce complex, high-precision parts efficiently reduces time-to-market and supports rapid prototyping, which is crucial for innovative product development. As industries evolve, so does the sophistication of the components they require, making precision CNC machining an indispensable part of modern manufacturing.
Lastly, environmental considerations and cost efficiency are influencing manufacturing choices. High-precision CNC machining minimizes material waste due to its accuracy, reduces the need for secondary processing, and ensures parts meet stringent specifications in the first pass. This combination of high quality, efficiency, and customization underscores the rapid growth of high-precision mechanical components in the global industrial ecosystem.
---
## Overcoming Challenges in Precision CNC Machining Processes
Manufacturing high-precision mechanical parts is not without its challenges. One of the primary difficulties lies in maintaining ultra-tight tolerances consistently across complex geometries. Variations in material properties, tool wear, and machine stability can impact the final accuracy of components, requiring advanced control systems and strict process monitoring.
Material selection itself presents challenges. Many high-performance materials—such as titanium alloys, Inconel, or ceramic composites—are difficult to machine due to their hardness, strength, or thermal properties. These materials demand specialized cutting tools, optimized machining parameters, and sometimes even cryogenic or other advanced cooling techniques to prevent deformation or tool failure.
Another obstacle is achieving the desired surface finish. High-precision parts often require smooth, defect-free surfaces that meet strict specifications, especially when used in sensitive applications like medical implants or aerospace components. This necessitates meticulous process planning, including polishing and surface treatment steps, which can be time-consuming and costly.
Thermal control during machining is also critical. High-precision machining generates heat, which can cause material expansion and affect dimensional stability. Implementing advanced cooling and lubrication solutions helps mitigate these effects, but it adds complexity to the process.
Automation and real-time monitoring have become essential to address these challenges. Integrating CNC systems with precision measurement tools allows for immediate adjustments, reducing errors and ensuring consistent quality. Techniques like in-process gauging, laser scanning, and coordinate measurement machines (CMM) are now standard to verify tolerances during manufacturing.
Furthermore, training and expertise are vital. Operators need specialized knowledge of machine capabilities, material behavior, and quality standards to troubleshoot issues swiftly. Investing in skilled personnel and continuous process optimization ensures production of high-precision parts that meet or exceed client expectations.
Lastly, establishing rigorous quality control protocols is crucial. Regular calibration of equipment, comprehensive inspections, and adherence to industry standards (such as ISO 9001) help maintain the highest quality levels. Overcoming these challenges through technological innovation and expertise ensures the successful production of complex, high-precision mechanical components.
---
## Key Materials Used in High-Precision CNC Machining Applications
The choice of materials plays a pivotal role in the performance, durability, and machinability of high-precision components. Different applications demand specific material properties, from strength and thermal stability to corrosion resistance and lightweight characteristics. Here, we explore some of the most common materials utilized in precision CNC machining.
**Stainless Steel:** Known for its excellent corrosion resistance and mechanical strength, stainless steel is widely used in medical devices, food processing equipment, and aerospace components. Its machinability varies depending on the grade, with 17-4 PH and 316L being popular choices for high-precision parts due to their balance of strength and ease of machining.
**Titanium Alloys:** With remarkable strength-to-weight ratios and resistance to corrosion and high temperatures, titanium alloys like Ti-6Al-4V are common in aerospace, medical implants, and marine applications. However, their high strength and low thermal conductivity make machining challenging, requiring specialized tools and techniques.
**Inconel and Superalloys:** These nickel-based superalloys excel in extreme environments—such as high temperatures and corrosive conditions—making them ideal for aerospace engines and power generation equipment. Their hardness and tendency to work-harden necessitate advanced machining strategies and coolant use.
**Aluminum Alloys:** Popular for their lightweight nature, aluminum alloys like 6061 and 7075 are easy to machine and suitable for automotive, aerospace, and automation parts. They allow rapid production of high-precision components with excellent surface finishes.
**Ceramics and Composites:** For applications demanding exceptional wear resistance, thermal stability, and chemical inertness, materials like alumina, zirconia, and carbon fiber composites are used. Machining these materials requires diamond-coated tools and ultra-precise control due to their brittleness and hardness.
**Plastic Materials:** Engineering plastics such as PEEK, PTFE, and Delrin are also employed in high-precision parts where electrical insulation, chemical resistance, or weight reduction are priorities. Their ease of machining makes them suitable for prototypes and specific functional components.
Each material presents unique challenges and benefits, influencing tooling choices, cutting parameters, and post-processing requirements. Selecting the appropriate material is critical to achieving the desired mechanical performance, longevity, and manufacturing efficiency in high-precision applications.
---
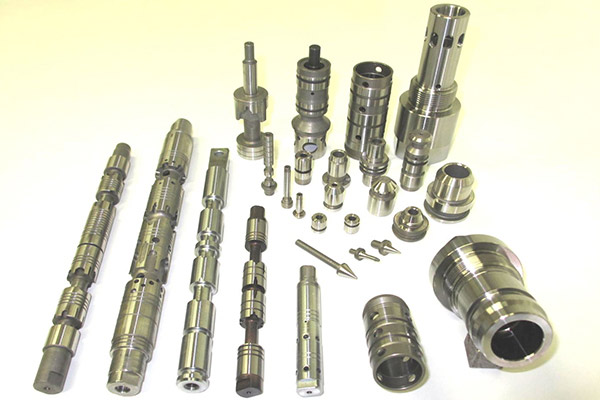
Customized machining of high-precision parts for construction machinery and automation
## Showcasing Our CNC Machining Capabilities and Quality Standards
Our CNC machining facility is equipped with state-of-the-art machinery designed to produce high-precision components with exceptional accuracy and surface quality. From multi-axis CNC milling centers to high-speed precision lathes, our equipment enables us to handle complex geometries and tight tolerances—often within ±2 micrometers.
We prioritize process control and consistency. Our advanced CNC systems incorporate real-time feedback, adaptive control algorithms, and high-resolution encoders to ensure each part meets stringent specifications. These capabilities allow us to produce intricate components with complex features that are often impossible with traditional manufacturing methods.
Our quality assurance protocols are rigorous. We employ coordinate measuring machines (CMM), laser scanners, and surface profilometers to verify dimensions and surface finishes during and after production. Every batch undergoes comprehensive inspection, ensuring compliance with industry standards such as ISO 9001 and AS9100 for aerospace quality management.
Precision surface finishing is a key aspect of our service. We offer multiple post-processing options, including polishing, electro-polishing, anodizing, and coating, to achieve the desired surface quality and corrosion resistance. These processes enhance functional performance and aesthetic appeal.
Material traceability and documentation are integral to our operations. We maintain detailed records of raw material certificates, process parameters, inspection reports, and calibration data, providing transparency and confidence for our clients.
Our team of experienced engineers and technicians collaborates closely with clients to optimize designs for manufacturability, cost-efficiency, and performance. We also invest in continuous training and technological upgrades to stay at the forefront of precision CNC machining.
By leveraging cutting-edge technology, stringent quality controls, and a customer-centric approach, we ensure that every high-precision mechanical component we produce consistently exceeds expectations, supporting critical applications across various industries.
---
## Common Mechanical Parts Manufactured with Precision CNC Techniques
Precision CNC machining enables the manufacturing of a broad spectrum of mechanical components critical to many industries. Common parts include shafts, gears, brackets, housings, connectors, and custom-engineered components that require tight tolerances and intricate features.
**Shafts and Spindles:** Used extensively in automation, robotics, and engine assemblies, these components demand high dimensional accuracy and smooth surface finishes to ensure optimal performance and minimal wear over their lifespan.
**Gears and Couplings:** Precision machining allows the creation of complex gear profiles and couplings with exact tooth geometry, essential for transmitting torque efficiently and reliably in machinery, automotive systems, and aerospace applications.
**Mechanical Housings and Enclosures:** Custom housings protect sensitive electronics or mechanical parts. CNC machining enables precise internal and external features, including threaded holes, cooling channels, and complex contours, all achieved with high repeatability.
**Valves and Fittings:** In fluid control systems, high-precision valves and fittings require close tolerances to prevent leaks and ensure smooth operation, often made from stainless steel or brass using CNC techniques.
**Medical Devices and Implants:** Components like surgical instruments, dental implants, or prosthetic parts require utmost precision to fit and function correctly, often manufactured from biocompatible materials like titanium or medical-grade plastics.
**Electrical Connectors and Enclosures:** Precision CNC machining allows the production of tiny, complex electrical connectors capable of withstanding harsh environments and ensuring reliable connections in aerospace, defense, and automation.
**Prototyping and Custom Parts:** Rapid prototyping of new designs or small-batch production of custom components benefits from CNC machining’s flexibility to produce complex geometries with high accuracy, reducing development time.
These parts not only serve functional roles but also contribute significantly to the overall reliability, longevity, and efficiency of the machinery or devices in which they are integrated. Precision CNC machining continues to be a cornerstone technology in manufacturing these critical components.
---
## Real-World Client Success Stories in High-Precision Machining
Our commitment to quality and precision has enabled us to develop successful collaborations with clients across various industries. One notable project involved manufacturing high-precision aerospace brackets made from titanium alloy. These components required tolerances within ±2 micrometers and complex geometries. Through advanced multi-axis CNC milling combined with meticulous inspection, we delivered parts that met strict aerospace standards, leading to improved aircraft safety and performance.
In the medical sector, we produced custom dental implant components from medical-grade titanium. The parts demanded flawless surface finishes and precise dimensions to ensure proper fit and function. Our team employed specialized tooling and surface treatment processes, resulting in implants that significantly reduced surgical time and improved patient outcomes.
For an automation equipment manufacturer, we fabricated critical high-tolerance shafts made from stainless steel. The parts had to withstand high rotational speeds and loads. Our precision machining and heat treatment processes ensured durability and minimal runout, enabling smoother operation and longer service life of the automated systems.
A leading engineering machinery company entrusted us with producing complex hydraulic valve housings. These parts featured intricate internal channels and tight tolerances. Our advanced CNC techniques, coupled with in-process measurement, allowed us to optimize the manufacturing process, reducing lead times and ensuring flawless performance in demanding environments.
Small-batch prototypes for a robotics startup were also successfully developed using our rapid CNC machining services. The ability to quickly iterate designs with high accuracy accelerated their product development cycle, ultimately helping them bring innovative robotic solutions to market faster.
These success stories exemplify our expertise in tackling complex manufacturing challenges, delivering high-precision components that meet or exceed industry standards. Our proven track record demonstrates our capability to support clients’ innovation and operational excellence through reliable, high-quality CNC machining services.
---
## High-precision CNC machining stands at the forefront of modern manufacturing, enabling the production of complex, reliable, and high-performance mechanical components across diverse industries. With advanced technology, rigorous quality standards, and expert craftsmanship, we are dedicated to delivering solutions tailored to your specific needs. Whether you're working on aerospace, medical devices, automation, or engineering machinery, our precision CNC machining services can help turn your innovative designs into reality. Contact us today to discuss your project and experience the difference that high-precision machining can make for your business.