Precision CNC Machining for High-Precision Mechanical Parts
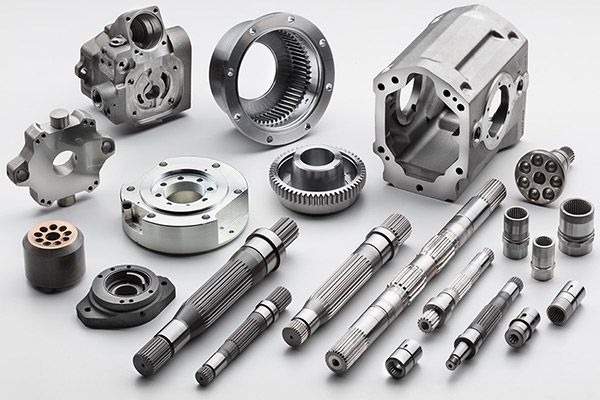
# Precision CNC Machining for High-Precision Mechanical Parts
In today’s fast-evolving manufacturing landscape, the demand for high-precision mechanical components has surged across various industries. From aerospace and automotive to medical devices and robotics, the need for parts that meet stringent tolerances and exhibit exceptional durability is more critical than ever. Precision CNC machining stands at the forefront of delivering these intricate components with unparalleled accuracy, enabling manufacturers to push the boundaries of innovation and reliability. This article explores the vital role of precision CNC machining in producing high-precision mechanical parts, highlighting the challenges, solutions, materials, capabilities, and real-world applications that define industry excellence.
===
## The Growing Demand for High-Precision Mechanical Parts in Industry
The modern industrial world heavily relies on components that must perform flawlessly under demanding conditions. Industries like aerospace require parts that operate reliably at high speeds and extreme temperatures, while automotive applications demand parts with tight tolerances for safety and efficiency. Similarly, medical equipment depends on micro-sized, highly precise parts for accurate diagnostics and treatment. As such, the need for high-precision mechanical parts has become a cornerstone of manufacturing, emphasizing the importance of advanced machining processes like CNC machining. These components are not only essential for ensuring product performance but also for enhancing overall system longevity and safety.
Moreover, the rise of automation and digitalization has increased the complexity of machine components, necessitating precision manufacturing techniques capable of delivering consistent quality at scale. The integration of high-precision CNC machining into production lines has enabled companies to reduce lead times, minimize material waste, and improve overall product quality. In industries where even the tiniest deviation can lead to costly failures, precision CNC machining has become an indispensable tool for achieving excellence and competitiveness.
The demand is also driven by the need for customized solutions. As industries move toward more personalized and specialized products, the ability to produce small batches of highly intricate parts with exact specifications is crucial. CNC machining, with its programmability and flexibility, allows manufacturers to adapt quickly to design changes and produce high-precision parts efficiently, meeting the evolving needs of modern industry.
In essence, high-precision mechanical parts are key enablers of technological advancement. They facilitate the development of innovative products and systems, from high-performance engines to delicate medical implants. As such, the industry’s reliance on CNC machining as a core fabrication process continues to grow, supporting a future where precision, durability, and customization are paramount.
## Overcoming Challenges in Precision CNC Machining: Techniques & Solutions
Achieving high precision in CNC machining presents a series of technical challenges that require sophisticated solutions. One of the primary issues is maintaining tight tolerances, often within microns, while avoiding tool wear and deformation. To address this, manufacturers employ high-quality cutting tools made from carbide or superalloys, which offer superior hardness and wear resistance. Regular tool calibration and replacement are essential to sustain consistent accuracy over production cycles.
Thermal expansion is another challenge, as the heat generated during machining can cause material distortion. Advanced cooling techniques, such as high-pressure coolant systems and misting, are implemented to manage temperature and minimize dimensional inaccuracies. Additionally, selecting materials with low thermal expansion coefficients further enhances process stability.
Vibration and chatter during machining can compromise surface quality and dimensional accuracy. To mitigate these issues, engineers optimize cutting speeds, feeds, and tool paths. The use of vibration-damping fixtures and precision machine beds also contributes to stability during operation. Modern CNC machines are equipped with active vibration control systems that automatically adjust parameters in real-time.
Achieving complex geometries with high precision often requires multi-axis machining capabilities. Five-axis CNC centers enable simultaneous movements, allowing access to intricate features and reducing the need for multiple setups. This not only improves accuracy but also shortens production time.
Quality control is critical in high-precision parts manufacturing. Non-contact measurement tools like laser scanners, coordinate measuring machines (CMM), and optical comparators are integrated into the process for in-process inspection. This ensures adherence to tight tolerances and helps identify issues early, reducing scrap and rework.
Automation and intelligent machining software have revolutionized precision manufacturing by enabling adaptive machining strategies. These systems can predict tool wear, optimize cutting parameters, and adjust operations dynamically, ensuring consistent quality even in complex projects.
Furthermore, investing in highly rigid machines and quality tooling minimizes deflections during machining. This structural integrity is fundamental when working with high-strength materials or producing parts with demanding tolerances.
Overall, overcoming the challenges of precision CNC machining involves a combination of advanced technology, meticulous process control, and continuous inspection. These solutions ensure that high-precision mechanical parts meet industry standards and customer expectations consistently.
## Key Materials Used in High-Precision CNC Machining Applications
The choice of material plays a vital role in the performance and manufacturability of precision components. Different materials offer unique advantages depending on the application, environmental conditions, and desired properties.
### Steel Alloys
High-strength steels, such as 17-4 PH stainless steel and tool steels like D2 and A2, are popular for their excellent mechanical properties and corrosion resistance. These materials are often used in transmission systems and high-performance engine components, where strength and durability are paramount.
### Aluminum Alloys
Lightweight and easy to machine, aluminum alloys like 6061 and 7075 are frequently selected for applications requiring high strength-to-weight ratios. Their thermal conductivity and corrosion resistance make them suitable for aerospace and precision instrumentation.
### Titanium
Known for its exceptional strength, low density, and corrosion resistance, titanium is favored in aerospace, medical implants, and high-end automotive parts. While more challenging to machine, advanced CNC techniques and specialized tooling facilitate its precise fabrication.
### Copper and Brass
These materials are valued for their excellent electrical and thermal conductivity, making them ideal for electronic connectors, heat sinks, and precision electrical components. Their machinability and surface finish qualities are also advantageous.
### Plastics and Composites
Engineering plastics such as PEEK, Delrin (acetal), and PTFE offer chemical resistance, low friction, and electrical insulation. These are often used in medical devices, precision fittings, and non-structural components requiring tight tolerances.
### Specialized Alloys
Materials like Inconel and Monel are used in extreme environments due to their high temperature and corrosion resistance. They are common in aerospace and chemical processing industries, demanding precise machining to withstand harsh conditions.
Selecting the appropriate material depends heavily on the application’s functional requirements, machinability, cost, and environmental considerations. Combining material properties with advanced CNC techniques ensures the production of high-quality, high-precision parts that perform reliably over time.
## Showcasing Our Advanced Capabilities in Tolerance and Quality Control
In the realm of high-precision CNC machining, achieving and verifying tight tolerances is fundamental. Our facility is equipped with state-of-the-art machinery capable of machining parts with tolerances as tight as ±2 microns. This precision is essential for applications like transmission system components and engine high-precision parts, where even slight deviations can lead to system failure.
We utilize a comprehensive suite of quality control tools, including 3D laser scanners, coordinate measuring machines (CMM), and optical comparators, to perform in-process and final inspections. These non-contact measurement systems enable us to detect even minute deviations, ensuring every part meets the exact specifications.
Our CNC centers feature multi-axis capabilities, allowing complex geometries and intricate features to be machined with exceptional accuracy and surface finish. These machines are integrated with advanced control software that allows for real-time adjustments, enhancing process stability and repeatability.
Our quality management system adheres to international standards such as ISO 9001, guaranteeing consistent manufacturing excellence. Regular calibration and maintenance of equipment further ensure measurement accuracy and process reliability.
Furthermore, we employ statistical process control (SPC) techniques to monitor production quality continuously. Data analysis helps us identify potential issues early, enabling proactive adjustments that prevent defects before they occur.
Training and expertise play a critical role in maintaining our high standards. Our engineers and technicians undergo ongoing education in precision machining best practices, ensuring they are up-to-date with the latest technologies and methods.
Our commitment to transparency and quality allows us to provide detailed inspection reports and certifications for every batch of parts. This rigorous quality control process assures our clients of the reliability and precision of their high-precision components.
Ultimately, our advanced capabilities in tolerance control and quality assurance set us apart in delivering CNC machined parts that meet the most demanding industry standards, supporting the success of our clients’ projects.
## Common Precision Machined Parts and Their Critical Applications
Precision CNC machining enables the production of a wide variety of mechanical components, each critical to their respective industries. Some of the most common high-precision parts include:
### Transmission System Components
Gears, shafts, and couplings are machined to exact tolerances to ensure smooth power transfer and minimal vibration. These parts are vital in automotive transmissions, industrial machinery, and robotics.
### Engine and Motor Parts
High-precision pistons, valves, and camshafts are manufactured to optimize performance and efficiency. Tolerance accuracy is crucial to prevent wear, leakage, and mechanical failure.
### Medical Devices
Micro-sized components like surgical instruments, implants, and dental fixtures require ultra-fine tolerances for safe and reliable operation. Materials such as titanium, stainless steel, and specialized plastics are common in these applications.
### Aerospace Components
Landing gear parts, engine brackets, and structural elements are machined for maximum strength and lightweight characteristics. These parts are subjected to rigorous testing and certification processes.
### Electronics and Semiconductor Parts
Connectors, heat sinks, and micro-electromechanical systems (MEMS) benefit from high-precision CNC machining to achieve tight fits and optimal electrical or thermal performance.
### Custom Industrial Equipment
Precision machined housings, brackets, and fixtures are tailored to specific machinery, ensuring proper fit, function, and durability in complex industrial setups.
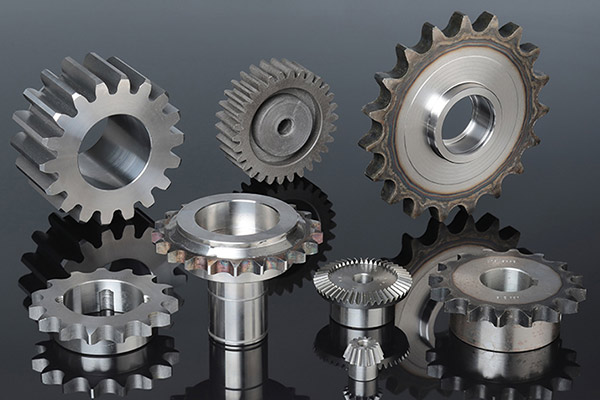
Customized machining of high-precision components for drivelines and engines
### Optical and Scientific Instruments
Lenses, mounts, and calibration devices demand micron-level accuracy for precise measurements and observations in research and development.
Each of these parts plays a critical role in their respective systems, emphasizing the importance of high-precision manufacturing to ensure safety, reliability, and performance. Our expertise in producing these components helps clients achieve their operational goals with confidence.
## Successful Projects Demonstrating Excellence in CNC Machining for Industry
Throughout our years of operation, we have delivered numerous high-precision CNC machined components for diverse industry applications. For instance, we partnered with an automotive transmission manufacturer to produce a series of high-precision gears and shafts. These parts required tolerances within ±5 microns, and our team successfully met these specifications, contributing to improved gear efficiency and longevity.
In the aerospace sector, we supplied custom titanium brackets for a commercial aircraft. The components demanded complex geometries and strict adherence to safety standards. Our advanced five-axis CNC centers, combined with rigorous inspection, ensured the parts passed all quality audits and performed flawlessly in flight tests.
A notable medical device project involved manufacturing micro-scale surgical instruments from stainless steel and PEEK plastics. The intricate features and tight tolerances were achieved through our precision machining and meticulous quality control processes, enabling the client to meet FDA safety requirements.
We also collaborated with a renewable energy company to produce precision components for wind turbine gearboxes. The parts had to withstand harsh environmental conditions and mechanical stresses, which we achieved through careful material selection and precision fabrication.
In each case, the combination of cutting-edge equipment, skilled craftsmanship, and stringent quality assurance resulted in components that exceeded client expectations. These projects exemplify our capability to handle complex, high-precision CNC machining tasks and deliver reliable, industry-grade parts.
Our portfolio reflects a commitment to excellence and innovation, reinforcing our position as a trusted partner in high-precision mechanical parts manufacturing. We continue to invest in technology and talent to support our clients’ success across all sectors.
---
## Ready to Elevate Your High-Precision Manufacturing?
Contact us today to discuss your CNC machining requirements for transmission system and engine high-precision parts. Our team is committed to delivering customized solutions with superior tolerance, quality, and reliability. Let us help turn your innovative designs into reality with precision craftsmanship you can trust.